William AJ Mercier
Sr. Consultant Transportation/ Engineering & Technical Services at SeaTec Consulting Inc.- Claim this Profile
Click to upgrade to our gold package
for the full feature experience.
Topline Score
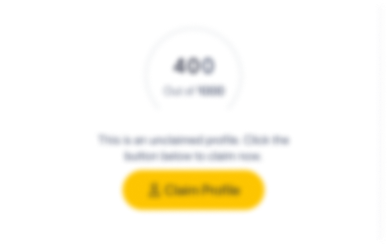
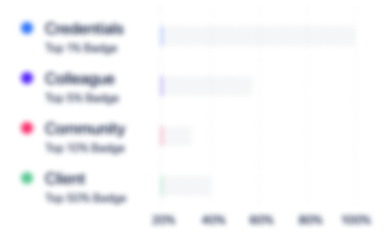
Bio

Ron Little
William has proven his visionary and leadership skills in every position he has held throughout his career progression. I have worked with him as colleagues at Delta Air Lines and as a consultant when he was director at JetBlue. His grasp of the complexity of maintenance program requirements, maintenance planning and the impact they have on cost, aircraft availability and reliability is un-paralleled. I worked closely with him on a maintenance program optimization project to train him on MSG-3, Program requirements, and the Reliability Programs optimization / analysis process. By the end of that project William was leading the discussion with the FAA office as a program SME garnering support and approval of C Check tasks well above the OEM MRBR intervals. His understanding of MSG-3 and maintenance task development earned him the seat as Chairman of the A4A Maintenance Programs Industry Group (MPIG) that is responsible for the MSG-3 process and provides input into policies set forth by international regulatory bodies such as the FAA and EASA. His current role as a senior consultant at SeaTec is just a natural progression to the next level supporting multiple clients and airlines with his vast background, knowledge and skills he brings to the table.

Keith McGuire
It was a pleasure to work alongside Bill. I always appreciated his knowledge, demeanor, leadership, and focus on team work when addressing strategy and execution. Thinking out of the box, developing relationships, ensuring compliance, meeting deadlines, strategic vision, and collaboration are just a few of his strong suits. Bill is a fantastic executive and I am honored to have worked with him.

Ron Little
William has proven his visionary and leadership skills in every position he has held throughout his career progression. I have worked with him as colleagues at Delta Air Lines and as a consultant when he was director at JetBlue. His grasp of the complexity of maintenance program requirements, maintenance planning and the impact they have on cost, aircraft availability and reliability is un-paralleled. I worked closely with him on a maintenance program optimization project to train him on MSG-3, Program requirements, and the Reliability Programs optimization / analysis process. By the end of that project William was leading the discussion with the FAA office as a program SME garnering support and approval of C Check tasks well above the OEM MRBR intervals. His understanding of MSG-3 and maintenance task development earned him the seat as Chairman of the A4A Maintenance Programs Industry Group (MPIG) that is responsible for the MSG-3 process and provides input into policies set forth by international regulatory bodies such as the FAA and EASA. His current role as a senior consultant at SeaTec is just a natural progression to the next level supporting multiple clients and airlines with his vast background, knowledge and skills he brings to the table.

Keith McGuire
It was a pleasure to work alongside Bill. I always appreciated his knowledge, demeanor, leadership, and focus on team work when addressing strategy and execution. Thinking out of the box, developing relationships, ensuring compliance, meeting deadlines, strategic vision, and collaboration are just a few of his strong suits. Bill is a fantastic executive and I am honored to have worked with him.

Ron Little
William has proven his visionary and leadership skills in every position he has held throughout his career progression. I have worked with him as colleagues at Delta Air Lines and as a consultant when he was director at JetBlue. His grasp of the complexity of maintenance program requirements, maintenance planning and the impact they have on cost, aircraft availability and reliability is un-paralleled. I worked closely with him on a maintenance program optimization project to train him on MSG-3, Program requirements, and the Reliability Programs optimization / analysis process. By the end of that project William was leading the discussion with the FAA office as a program SME garnering support and approval of C Check tasks well above the OEM MRBR intervals. His understanding of MSG-3 and maintenance task development earned him the seat as Chairman of the A4A Maintenance Programs Industry Group (MPIG) that is responsible for the MSG-3 process and provides input into policies set forth by international regulatory bodies such as the FAA and EASA. His current role as a senior consultant at SeaTec is just a natural progression to the next level supporting multiple clients and airlines with his vast background, knowledge and skills he brings to the table.

Keith McGuire
It was a pleasure to work alongside Bill. I always appreciated his knowledge, demeanor, leadership, and focus on team work when addressing strategy and execution. Thinking out of the box, developing relationships, ensuring compliance, meeting deadlines, strategic vision, and collaboration are just a few of his strong suits. Bill is a fantastic executive and I am honored to have worked with him.

Ron Little
William has proven his visionary and leadership skills in every position he has held throughout his career progression. I have worked with him as colleagues at Delta Air Lines and as a consultant when he was director at JetBlue. His grasp of the complexity of maintenance program requirements, maintenance planning and the impact they have on cost, aircraft availability and reliability is un-paralleled. I worked closely with him on a maintenance program optimization project to train him on MSG-3, Program requirements, and the Reliability Programs optimization / analysis process. By the end of that project William was leading the discussion with the FAA office as a program SME garnering support and approval of C Check tasks well above the OEM MRBR intervals. His understanding of MSG-3 and maintenance task development earned him the seat as Chairman of the A4A Maintenance Programs Industry Group (MPIG) that is responsible for the MSG-3 process and provides input into policies set forth by international regulatory bodies such as the FAA and EASA. His current role as a senior consultant at SeaTec is just a natural progression to the next level supporting multiple clients and airlines with his vast background, knowledge and skills he brings to the table.

Keith McGuire
It was a pleasure to work alongside Bill. I always appreciated his knowledge, demeanor, leadership, and focus on team work when addressing strategy and execution. Thinking out of the box, developing relationships, ensuring compliance, meeting deadlines, strategic vision, and collaboration are just a few of his strong suits. Bill is a fantastic executive and I am honored to have worked with him.

Credentials
-
Digital Transformation in Supply Chains
LinkedInDec, 2022- Nov, 2024 -
Engineering Drawings for Manufacturing
LinkedInDec, 2022- Nov, 2024 -
Agile Foundations
LinkedInOct, 2022- Nov, 2024 -
Decision-Making Strategies
LinkedInOct, 2022- Nov, 2024 -
Leading Productive Meetings
LinkedInOct, 2022- Nov, 2024 -
Learning Design Research
LinkedInOct, 2022- Nov, 2024 -
Project Management Skills for Leaders
LinkedInOct, 2022- Nov, 2024 -
Six Sigma: White Belt
LinkedInOct, 2022- Nov, 2024 -
Agile Project Leadership
LinkedInSep, 2022- Nov, 2024 -
Coaching and Developing Employees
LinkedInSep, 2022- Nov, 2024 -
How to Use LinkedIn Learning
LinkedInSep, 2022- Nov, 2024 -
Leading When You're Not in Charge
LinkedInSep, 2022- Nov, 2024 -
Organizational Learning and Development
LinkedInSep, 2022- Nov, 2024 -
Lean Six Sigma Master Black Belt
Villanova UniversityMar, 2019- Nov, 2024
Experience
-
SeaTec Consulting Inc.
-
United States
-
Airlines and Aviation
-
100 - 200 Employee
-
Sr. Consultant Transportation/ Engineering & Technical Services
-
May 2022 - Present
-
-
-
JetBlue
-
United States
-
Airlines and Aviation
-
700 & Above Employee
-
Director of Maintenance Planning & Programs: Technical Operations
-
Jul 2018 - Apr 2022
Direct and coordinate maintenance planning department maintaining focus on safety, compliance, reliability, and continuous improvement. Launch and optimize maintenance programs. Analyze program data. Supervise 85 direct reports and supply chain groups. Develop competent team structure to support division goals. Steer change management. Improve processes and workflows. ● Yielded better results for airline following evaluation and focused on improvement opportunities within maintenance footprint and programs; reexamined all maintenance stations within JetBlue, set up operations, and divided specific maintenance activities at various locations, improving cost and delivery of critical materials. o Increased operational effectiveness and improved TechOps scalability; grew available seat miles (ASMs) and reduced resources required to support cost per available seat mile (CASM). ● Delivered overall vision and implementation of internal base maintenance operation, multimillion-dollar business venture creating more capacity, expertise, and options for heavier maintenance requirements within airline. o Managed launch of Maintenance Operations Control Center within system operations center and streamlined planning and programs department based on work demand. Show less
-
-
-
United Airlines
-
United States
-
Airlines and Aviation
-
700 & Above Employee
-
Manager: Base Maintenance Planning & Operations
-
2015 - 2018
Provided tactical oversight of maintenance plan and led development and execution of $750M+ in base maintenance events with focus on safety, compliance, and reliability. Oversaw budget and 12 direct reports. Coached and mentored staff on Lean Six Sigma, project management, and theory of constraints. Created and evaluated KPIs and aggressive targets. ● Recovered millions of dollars annually by facilitating process improvement initiatives and strategies, transforming overall culture and thought process from reactive to proactive, generating robust cost savings, efficiencies, and aircraft reliability, and identifying and offering real solutions. ● Ensured safety, quality, and stability in base maintenance visits and strategic hangar plan due to redesign and implementation of fresh policies and processes utilizing theory of constraints methodologies as well as efforts to designate new KPIs and aggressive targets. Show less
-
-
-
Delta Air Lines
-
United States
-
Airlines and Aviation
-
700 & Above Employee
-
Senior Project Manager
-
2013 - 2015
Managed internal strategic heavy maintenance plan. Directed all phases of capital projects. Supervised 2 direct reports and delivered guidance to base maintenance team. Developed and analyzed KPIs. Created, assessed, and deployed various statistical models and software solutions to evaluate data and trends and coordinate data-driven decisions and solutions. ● Assisted in securing multimillion-dollar contracts with Virgin Atlantic and Hawaiian Airlines, driving several millions of dollars in revenue for Delta Air Lines; generated 50% to 66% in cost savings for Hawaiian; performed heavy maintenance and established win-win plan for both parties.● Surpassed financial and operational objectives within department, encompassing throughput, labor, and material utilization by establishing and leading aggressive targets.o Drove 50% growth in Delta MRO Airframe Services’ hangar capacity, increased portfolio by several million, and secured 2 additional long-term clients. Show less
-
-
Maintenance Tracking and Configuration Control, Propulsion Division
-
Nov 2011 - Apr 2013
Implemented and led significant continuous improvements. Worked in engine maintenance shop with tight turn times for large clients. Conducted critical analysis of engine delivery, executed adjustments, and enhanced overall process. Completed evaluation of data from shop orders and nonroutine cards; established and maintained baseline work standards for recurring maintenance tasks, financial planning analysis, and airworthy compliance and safety standards. Helped achieve industry-leading turnaround times by enhancing alignment between back shops, paperwork and maintenance. Show less
-
-
-
Republic Airways
-
United States
-
Airlines and Aviation
-
700 & Above Employee
-
Heavy Maintenance Coordinator: Heavy Maintenance Operations
-
Jan 2008 - Oct 2011
Worked in daily operations of 4 heavy maintenance bays and supply chains for 4 airlines (CHQ, S5, RP, and F9). Led process improvements and efficiencies during expansion of base. Negotiated component purchase and leases. Participated Kaizen workflow improvement projects. Participated in launch of new Enterprise Resource Program (RAMCO). Assisted in crew member training. ● Helped Recover close to $1 millions of dollars in FY11 by reducing utilization of existing inventory during heavy maintenance visits; helped base achieved all financial and operational objectives while upholding strong proactive safety culture. Show less
-
-
-
The Ohio State University Airport
-
United States
-
Airlines and Aviation
-
1 - 100 Employee
-
Repair Shop Business Associate/ Repairman, Aircraft Maintenance Department
-
2005 - 2008
Established robust maintenance plan for OSU flight school fleet and repair shop. Restructured and advanced repair shop filing system, creating more user-friendly system and increasing accuracy and swiftness of information Established robust maintenance plan for OSU flight school fleet and repair shop. Restructured and advanced repair shop filing system, creating more user-friendly system and increasing accuracy and swiftness of information
-
-
Education
-
The Ohio State University
Aviation Mgt/ Economics -
Villanova University
Lean Six σ Master Black Belt, Project Management and Professional Studies
Community
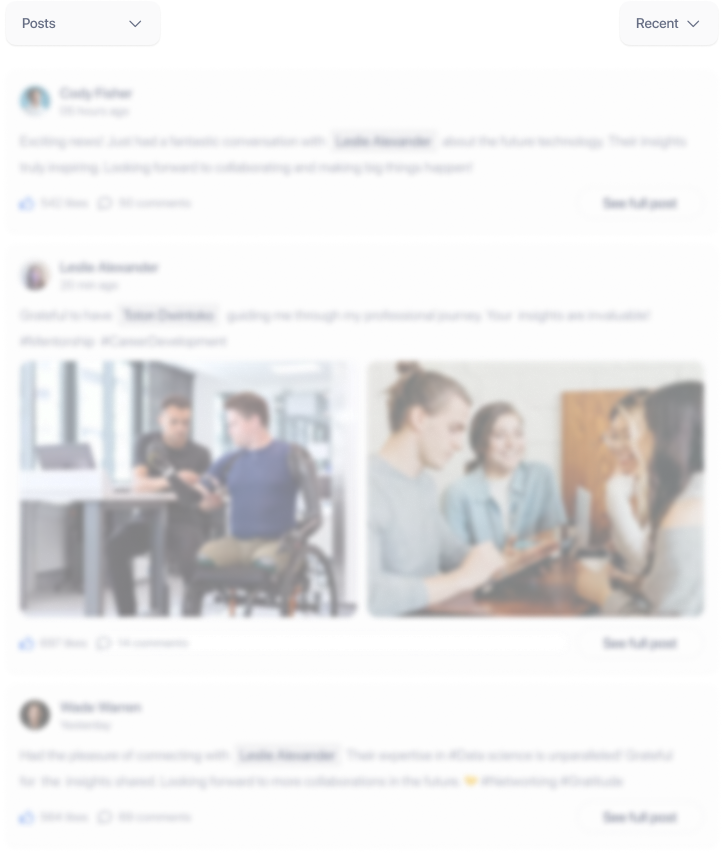