Joseph Armstrong
Process Engineer at Roehm- Claim this Profile
Click to upgrade to our gold package
for the full feature experience.
-
French Limited working proficiency
Topline Score
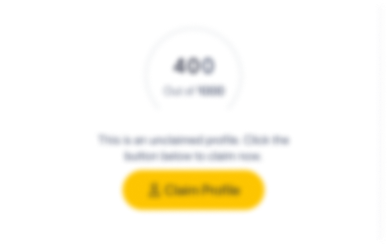
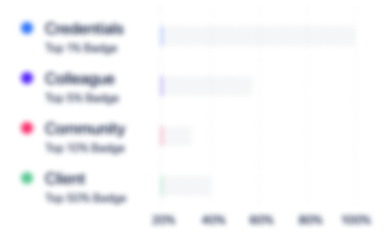
Bio


Credentials
-
SharePoint Online Essential Training: Beyond the Basics
LinkedInJul, 2022- Sep, 2024 -
Learning VBA in Excel
LinkedInFeb, 2022- Sep, 2024 -
SQL for Non-Programmers
LinkedInFeb, 2022- Sep, 2024 -
Power BI Data Visualization and Dashboard Tips, Tricks, & Techniques
LinkedInJan, 2022- Sep, 2024 -
Power BI Quick Tips
LinkedInJan, 2022- Sep, 2024 -
Power BI Top Skills
LinkedInJan, 2022- Sep, 2024 -
Leading Productive Meetings
LinkedInSep, 2021- Sep, 2024 -
Microsoft Project 2016 Essential Training
LinkedInSep, 2021- Sep, 2024 -
Project Management Foundations
LinkedInSep, 2021- Sep, 2024 -
Project Management Foundations: Small Projects
LinkedInSep, 2021- Sep, 2024 -
AutoCAD P&ID Essential Training: User
LinkedInMay, 2021- Sep, 2024 -
AutoCAD Plant 3D Essential Training: Specs & Catalogs
LinkedInMay, 2021- Sep, 2024 -
AutoCAD Plant 3D Essential Training: User
LinkedInMay, 2021- Sep, 2024 -
Dieter Rams: Principles of Good Design
LinkedInMay, 2021- Sep, 2024
Experience
-
Roehm
-
Germany
-
Chemical Manufacturing
-
500 - 600 Employee
-
Process Engineer
-
Jan 2022 - Present
-
-
-
Armstrong Carpentry
-
United States
-
Construction
-
Carpenter
-
Mar 2020 - Present
-
-
-
Reporter Magazine
-
United States
-
Newspaper Publishing
-
1 - 100 Employee
-
Staff Writer
-
Oct 2021 - Jan 2022
Wrote and published two articles on emerging Carbon Capture and Energy Storage Technologies respectively, for the Tech category. Wrote and published two articles on emerging Carbon Capture and Energy Storage Technologies respectively, for the Tech category.
-
-
-
ECT2 (Emerging Compounds Treatment Technologies, Inc.)
-
United States
-
Environmental Services
-
1 - 100 Employee
-
Design/Field Engineer Intern
-
May 2021 - Aug 2021
-
-
-
Whitcraft Group
-
United States
-
Aviation & Aerospace
-
100 - 200 Employee
-
Design Engineer Intern
-
Sep 2020 - Apr 2021
• Undertook the task of designing and drafting over 70 individual true-position inspection gages in SolidEdge for complex Pratt and Whitney bracket parts (Whitcraft LLC, 2020). • Using SolidEdge, designed a unique indexing mill fixture utilizing a combination of existing clamps and springs, 3D printed parts, and steel components fabricated using conventional machine tools, which allowed for the proper single-piece-flow of titanium Rolls Royce brackets through a precise chamfer operation on a Bridgeport mill, using the motion of the programmed CNC to virtually automate the switching and ejection of parts with the push of a button (Whitcraft LLC, 2020). • Supported the brackets Single-Bend production line as primary design engineer, supporting the Brackets division as a whole by designing and drafting inspection gages and fixtures, writing work orders and process sheets, and updating Engineering Masters to reflect process changes (Whitcraft LLC, 2020). • Was approached regarding safety concerns over the basket in a wash tank forcing operators to reach over it, exposing themselves to the fumes of the solvent cleaner, and smaller parts falling through gaps in the basket’s mesh; designed steel hooks in SolidEdge so that the basket could be hung in a more user-friendly placement, and wrote a laser program to cut a finer mesh out of sheet metal, resolving the complaint in a matter of hours (Whitcraft LLC, 2020). • Worked on a cross-functional taskforce in a flow line for a Honeywell duct where the operator was being exposed to excessive noise. Helped eliminate the use of loud belt sanders and pneumatic deburring tools by redesigning the part in SolidEdge and working with the six-axis laser programmer to cut welding-bevels during the laser operation, negating the need for the operator to do so (Whitcraft LLC, 2020).
-
-
-
HillHouse Assisted Living
-
United States
-
Hospitals and Health Care
-
1 - 100 Employee
-
Maintenance Worker
-
Jun 2015 - Feb 2021
Basic maintenance; painting, carpentry, and landscaping. Worked part time through high school and my college career. Basic maintenance; painting, carpentry, and landscaping. Worked part time through high school and my college career.
-
-
-
PPC Broadband, Inc. - A Belden Brand
-
United States
-
Telecommunications
-
300 - 400 Employee
-
Design Engineer Intern
-
Jan 2019 - Jun 2019
• Designed a mechanically-complex ratcheting tool in SolidWorks, including motion studies, which I later prototyped and achieved proof-of-concept for, and for which the company filed an Intellectual Property claim (PPC Broadband, 2019). • Redesigned coaxial drop connector components in SolidWorks, specifically the nut and compression ring, to save an estimated 30% production cost (PPC Broadband, 2019). • Spearheaded a product qualification process for a customer in Australia, researching test standards, recommending suitable environmental test procedures to the customer and executing them on the product (PPC Broadband, 2019). • Worked with a team to identify product failure modes of the company’s flagship product, helping with research and testing including fatigue analysis on flashing and plating types and subsequent corrosion buildup, and reporting weekly findings to the group (PPC Broadband, 2019).
-
-
-
-
Continuous Improvement Intern
-
May 2018 - Aug 2018
Joseph Armstrong worked at Whitcraft Eastford’s moonshine shop during his 2018 coop period, working for the division Lean Leader at the time, Timothy Williams. Eastford specializes in formed sheet metal, welded assembly and machine aircraft components manufactured in one piece flow lines. During his time in the moonshine shop Joe supported strategic goals at the Eastford division to improve manufacturing processes, methods and quality. Joe learned and utilized Kaizen tools such as: • time studies in support of creating and designing operator standard work. • Documented material and people flow and provided custom and unique processes improvements Joe also designed and assembled right-sized shop solutions using a combination of Creform and mechanical components. Joe created the first material handling Creform cart that incorporated Karakuri technologies. Joe utilized the Kaizen concepts of trystorming, which consists of hand sketches and mock ups to the point where he had refined the technology to a functional product. Joe developed a material handling device for a machined bearing housing (~80 lbs). This material handling device was specifically designed to facilitate 1 pc flow; however, when material went outside the flow line (coatings) the material handling devices were cluttering the flow line. Joe put to use Karakuri concepts and built collapsible carts that can be stowed away taking up 50% less space. This technology is still being utilized on the Genba 2 years later and has accelerated the shop forward. Joe supported 1S workshops on a weekly/monthly basis to eliminate sleeping tooling and material as well as resolving safety concerns on the Genba essentially freeing up space. This was in support of our Just in time manufacturing journey. Joe helped implement and revise new flow lines such as the Mutli-weld bracket line and modified the existing flow lines such as the manifolds and ducts assembly.
-
-
Education
-
Rochester Institute of Technology
Bachelor of Science - BS, Mechanical Engineering Technology
Community
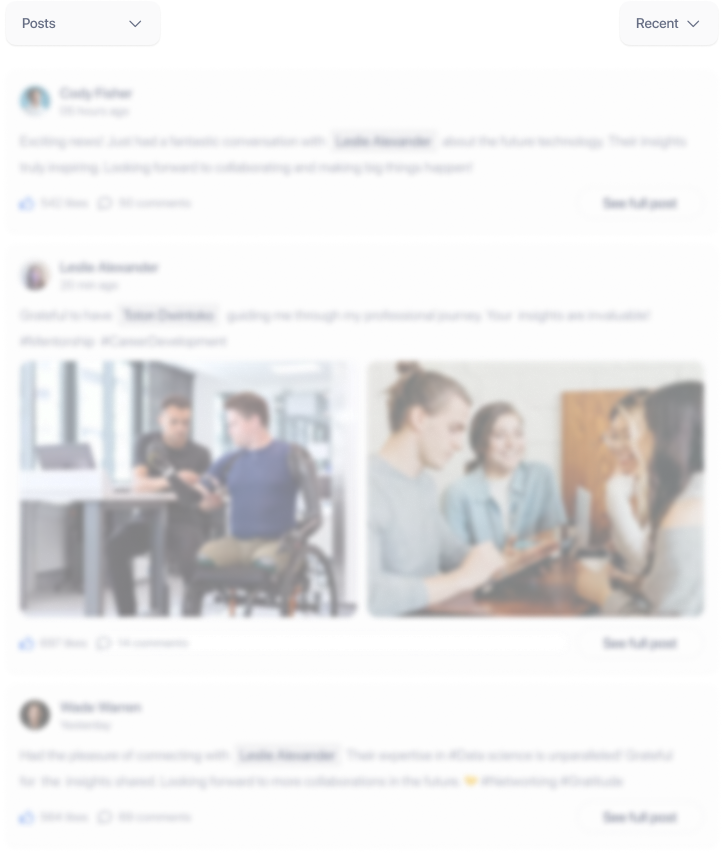