Zeina Arabi
Program Manager at Naprotek- Claim this Profile
Click to upgrade to our gold package
for the full feature experience.
Topline Score
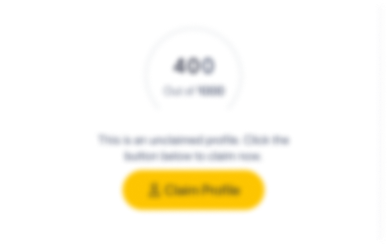
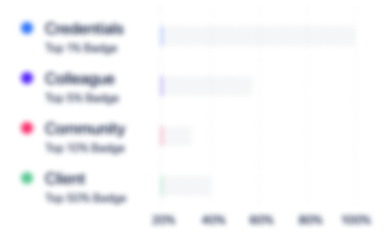
Bio

Liz Davidson
Zeina was a great addition to our Program Management Team. She received on-the-job training and also completed training and certification by IPC as EMS Program Manager. Zeina has a high energy level and is detailed in her work. Her accuracy and output are definitely strengths as well. She is professional with her customers, both external and internal, and proactive in monitoring the performance to schedule. Zeina is a model employee and a pleasure to have as part of the team. Liz Davidson

Judy Comish
Zeina is a dedicated employee and a delight to work with. She goes above and beyond to make things happen and to ensure everything is right!

Liz Davidson
Zeina was a great addition to our Program Management Team. She received on-the-job training and also completed training and certification by IPC as EMS Program Manager. Zeina has a high energy level and is detailed in her work. Her accuracy and output are definitely strengths as well. She is professional with her customers, both external and internal, and proactive in monitoring the performance to schedule. Zeina is a model employee and a pleasure to have as part of the team. Liz Davidson

Judy Comish
Zeina is a dedicated employee and a delight to work with. She goes above and beyond to make things happen and to ensure everything is right!

Liz Davidson
Zeina was a great addition to our Program Management Team. She received on-the-job training and also completed training and certification by IPC as EMS Program Manager. Zeina has a high energy level and is detailed in her work. Her accuracy and output are definitely strengths as well. She is professional with her customers, both external and internal, and proactive in monitoring the performance to schedule. Zeina is a model employee and a pleasure to have as part of the team. Liz Davidson

Judy Comish
Zeina is a dedicated employee and a delight to work with. She goes above and beyond to make things happen and to ensure everything is right!

Liz Davidson
Zeina was a great addition to our Program Management Team. She received on-the-job training and also completed training and certification by IPC as EMS Program Manager. Zeina has a high energy level and is detailed in her work. Her accuracy and output are definitely strengths as well. She is professional with her customers, both external and internal, and proactive in monitoring the performance to schedule. Zeina is a model employee and a pleasure to have as part of the team. Liz Davidson

Judy Comish
Zeina is a dedicated employee and a delight to work with. She goes above and beyond to make things happen and to ensure everything is right!

Credentials
-
EMS Program Management Certification
- -
ISO13485/AS9100/ISO9001 Internal Auditor Training
Naprotek Inc. -
Master Management Level 1 Training
Penn State University
Experience
-
Naprotek
-
United States
-
Appliances, Electrical, and Electronics Manufacturing
-
1 - 100 Employee
-
Program Manager
-
Aug 2011 - Present
Program Manager for all assigned accounts. Directly managed a variety of projects from beginning to end Interfaced between customer and Naprotek, providing quotes, order status, and replying to any and all requests to and from the customer Interacted between different departments internally such as document control, quality assurance, manufacturing, purchasing, engineering, inventory control, shipping as needed to make sure jobs are on task Coordinated kit audits on consigned… Show more Program Manager for all assigned accounts. Directly managed a variety of projects from beginning to end Interfaced between customer and Naprotek, providing quotes, order status, and replying to any and all requests to and from the customer Interacted between different departments internally such as document control, quality assurance, manufacturing, purchasing, engineering, inventory control, shipping as needed to make sure jobs are on task Coordinated kit audits on consigned assemblies and resolved discrepancies with customer and stockroom to expedite kit release to manufacturing. Coordinated material purchases for turnkey orders with the buyers and resolved any discrepancies between BOM AVL and manufacturer part numbers. Monitored material kit to kit release schedule to meet deadlines to customer Processed ECO’s as required to maintain accurate data base on turnkey assemblies. Scheduled builds with manufacturing to meet customer schedule demands. Coordinated shipping schedule with shipping department to meet customer deliveries date. Scheduled and lead contract review launch meetings. Voice of the customer. Escalated all matters to appropriate personnel to make sure I resolve and build and deliver quality product in a timely fashion. Expert in the document control department: Trained new employees on entering BOMs in Manex (data management system) creating part numbers and releasing accurate documentation and issuing internal ECOs/Deviations/BCNs among other tasks critical for delivering build to print boards
-
-
Document Control Analyst
-
Feb 2010 - Aug 2011
Assisted personnel in the creation of Engineer Change Order (ECO), Deviations (DVA) reviewed the ECO, resolved issues with initiator of the change, and entered the ECO into MANEX SYSTEM. Developed and implemented a method for routing and tracking the ECOs during the approval process. Formatted/imported customer EXCEL DOC BOM to MANEX system. Ensured all the assembly part numbers AVL (approved vendor list/spec sheets) were included. Created /entered part numbers in Manex for all prototype PCB… Show more Assisted personnel in the creation of Engineer Change Order (ECO), Deviations (DVA) reviewed the ECO, resolved issues with initiator of the change, and entered the ECO into MANEX SYSTEM. Developed and implemented a method for routing and tracking the ECOs during the approval process. Formatted/imported customer EXCEL DOC BOM to MANEX system. Ensured all the assembly part numbers AVL (approved vendor list/spec sheets) were included. Created /entered part numbers in Manex for all prototype PCB boards that are manufactured at Naprotek using BOMs provided to us by our customers. Ensured that the current revision of a controlled document such as assembly drawing/BOM and Fab is clearly defined in order to preclude the use of non applicable document and promptly removed any obsolete documents from all points of issue or use. Ensured that documentation/data that relate to the requirements of the Quality System are controlled in a manner which ensures integrity and accessibility. Developed, enhanced and revised documentation procedures, and maintained all required documents as defined applicable. Acquired knowledge in typing and printing special serialized labels for different customers following specific specs instructions such as label size/type etc. Trained employees on using the label software and wrote the corresponding procedure for specific 2D labels. Officially completed ISO 9001:2008 for internal audits due to my good organizational skills and attention to details.
-
-
-
Extreme Networks
-
United States
-
Software Development
-
700 & Above Employee
-
Engineer Change Management
-
Feb 2008 - Mar 2009
Engineer Change Management Specialist
-
-
ECM Engineer Change Management Contractor
-
Feb 2008 - Mar 2009
Managed and issued ECOs“Engineer Change Orders”, MCOs “Manufacturing Change Order”, DVAs “Deviations” using Agile to manage the changes of products through the product life cycles. Ensured that the product will meet life cycle requirements from preliminary to prototype and finally production. Assigned Part Numbers for the Shipping/System/Different Assemblies/Documents/mechanical etc. Built BOM Structure “Bill of Material” with indented BOMs using Agile and tracked the changes; such as… Show more Managed and issued ECOs“Engineer Change Orders”, MCOs “Manufacturing Change Order”, DVAs “Deviations” using Agile to manage the changes of products through the product life cycles. Ensured that the product will meet life cycle requirements from preliminary to prototype and finally production. Assigned Part Numbers for the Shipping/System/Different Assemblies/Documents/mechanical etc. Built BOM Structure “Bill of Material” with indented BOMs using Agile and tracked the changes; such as REV control, date code embedded at the S/Ns, or both Gathered all needed Docs/Spec and checked the submitted items from vendors/engineers to make sure that they match with our product BOM. Acquired some Knowledge in of EMC and safety requirement for the Product: such as UL and FCC. Acquired some knowledge of Green Initiative Requirement for the products, such as EU WEEE Directive, EU RoHS, and China RoHS; and upcoming regarding to “Energy saving” in EU, etc. Performed FAIs “First Article Inspection” on the Product (making sure it matches with our BOM). Alerted engineers on some missing parts/labels/ among other issues making the PLM process smoother.
-
-
-
-
Y3K Computers Purchasing/Procurement Manager
-
Jan 2004 - Jan 2006
Managed all purchases for the Y3K company which includes the following: Managing orders on a weekly basis Establishing excellent relationships with multiple vendors and was able to get most competitive bids Managing all shipping overseas Effectively handling returns Conducting successful negotiation with partners that resulted in a win-win agreement. Managed all purchases for the Y3K company which includes the following: Managing orders on a weekly basis Establishing excellent relationships with multiple vendors and was able to get most competitive bids Managing all shipping overseas Effectively handling returns Conducting successful negotiation with partners that resulted in a win-win agreement.
-
-
Education
-
Evergreen College
AA, Engineering -
Evergreen Valley College
Associate's degree in Engineering, Engineering
Community
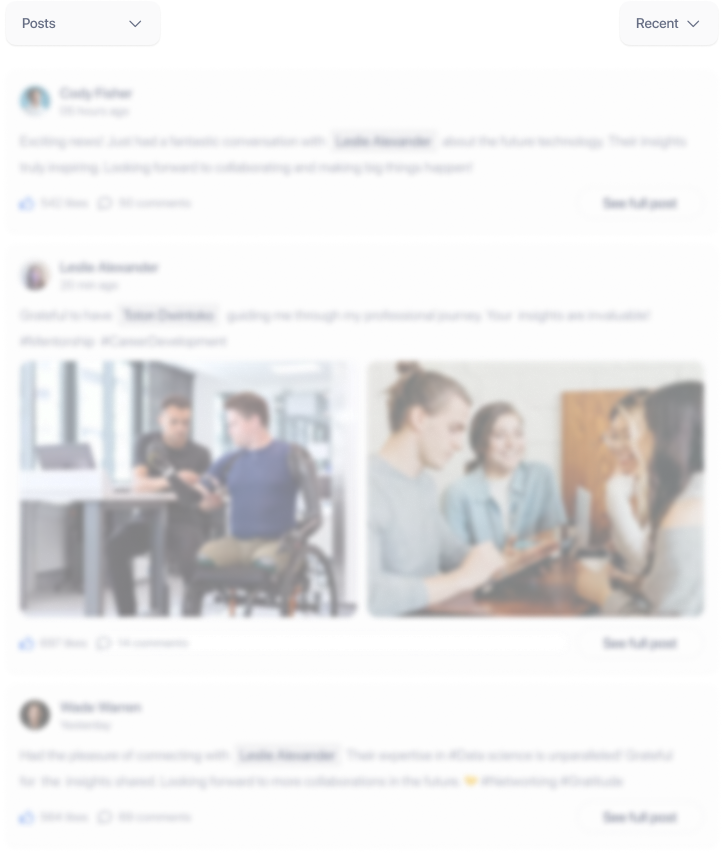