zaini mabrur
Manager Operations at PT Delta Jaya Mas- Claim this Profile
Click to upgrade to our gold package
for the full feature experience.
Topline Score
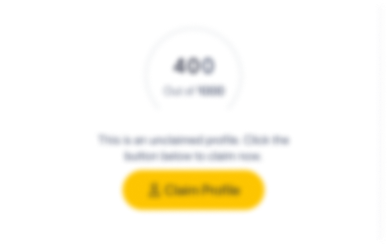
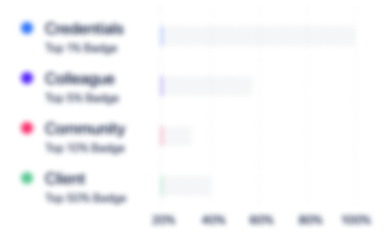
Bio


Experience
-
PT. Delta Jaya Mas
-
1 - 100 Employee
-
Manager Operations
-
Oct 2014 - Present
Report to GM Operation,6 direct report sub-ordinates,125 permanent employees and 190 out-sourcing workers Roles & Responsibilities: 1.Manage all sources of manufacturing processes and oversee all day-to-day factory operations from production and manufacturing to ensure company policies and procedures are running correctly, continuous improvement processes that maximize management, safety, quality and productivity. *Managing Organizational structures,systems and people development of effective to achieve the target Management. *Improve the operational systems,processes and policies in support of organizations mission specifically,support better management reporting,information flow and management,business process and organizational planning. *Direct and coordinate organization's financial and budget activities to fund operations,maximize investments,and increase efficiency. *Setting Effective process manufacture and Quality management system. *Delivery and development of high quality services achieved through the involvement of customers, carers and other stakeholders. *Ensure that all workings are manufactured in a correct,cost effective and timely manner in alignment with specifications and quality requirements. 2.Products & Processes Quality Assurance *Develop Quality Control Analysis,Conducting tests and inspections of products,services,or processes to evaluate quality or performance *Validates quality processes by establishing product specifications and quality attributes;measuring production,documenting evidence,determining operational and performance qualification,writing and updating quality assurance procedures. 3.Organization & People Development *Assist in employee recruitment, performance evaluation,promotion,retention and termination activities. *Organize job trainings to team members to achieve Operational goals. 4.Improve performance using World Class Manufacturing/Total Productive Management methodology *Implement TPM & TQM Show less
-
-
-
PT Santos Jaya Abadi 3 (Kapal Api Global)
-
Sidoarjo East Java
-
Production Coordinator ( Junior Manager )
-
Oct 2010 - Oct 2014
Report to Plant Manager,5 direct report sub-ordinates, 32 permanent employees and 52 out-sourcing workers Roles & Responsibilities: 1.Working together with the project managers and engineering departments in the process of Commissioning and installation of the production plant . *Supervising Production plant construction, modification and improvement. *Managing and ensure the Commissioning process plant production in accordance with the schedule. 2. Manage all resources of Production department and coordinate with other department to achieve production targets in term of volume, quality and efficiency at cost leadership, based on Key Performance Indicators. *Plan, manage and ensure the production process in accordance with the target Management. *Monitor production activities and adjust schedules for on-time delivery. *Determine equipment, material and manpower requirements for project execution. *Ensure that final product meets quality standards and customer specifications. *Recommend cost reduction initiatives while maintaining quality standards. *Investigate production issues and develop resolutions. *Ensure that final product meets quality standards and customer specifications. *Schedule equipment maintenance and inspection on regular basis. *Ensure that team follows company policies and safety standards. *Prepare ISO 22000, Halal, Occupational Safety& Health Management System (SMK3), ISO 14001 and ISO 9001 certification. 3.Improve & Maintain Productivity & Performance *Develop & improve manufacturing practices. *Develop project budget and maintain expenses within the budget *Improve Manufacturing Performance System using Overall Equipment Effectiveness (OEE). *Drive TPM implementation 4.Organization & People Development *Assist in employee recruitment, performance evaluation, promotion, retention and termination activities. *Organize job trainings to team members to achieve production goals. Show less
-
-
-
PT Mitshubshi Cable Industries
-
Surabaya Area, East Java, Indonesia
-
Production Engineer
-
Jul 2006 - Oct 2010
Report to Plant Manager ,1 direct report sub-ordinates, 8 permanent employees. Main Roles & Responsibilities: Maintaining the efficiency and effectiveness off all production related manufacturing equipment & process required to manufacture high quality product in a repeatable and cost effective manner. 1.Plan and coordinate production processes on daily basis to produce high quality products. *Coordinate and Monitor performance and implement improvements. Ensure quality of products. Manage quality and quantity of employee productivity. Manage maintenance of equipment and machinery. Provide technical support where necessary. *Develop process improvements to effectively utilize equipment and materials to maximize production. *Develop operational strategies to achieve production and financial objectives. *Develop operating instructions and equipment specifications for production activities. *Identify unsafe operations and practices and report the same to Manager immediately *Develop best practices to improve production capacity, quality and reliability. *Setting Effective process manufacture and Quality management system *Investigate problems, analyze root causes and derive resolutions. *Establish safety procedures and environmental regulations for employees. 2.Member of Product Development Team *Provide technical support for new product development *Develop new process and machine/equipment for new product 3.Implement Defect prevention trough statistical process control *Set-up and implement statistical process control *Train and guide Statistical Process control implementation 4.Organization & People Development *Assist in employee recruitment, performance evaluation, promotion, retention and termination activities. *Multi-skills / Multi-tasks implementation (% of Employee Flexibility). *Training Hours & Coverage (Hrs & Modules / Employee). *Zero Accident (# of Accidents). Show less
-
-
Education
-
Unwip Sby
Bachelor's degree, Industrial Engineering
Community
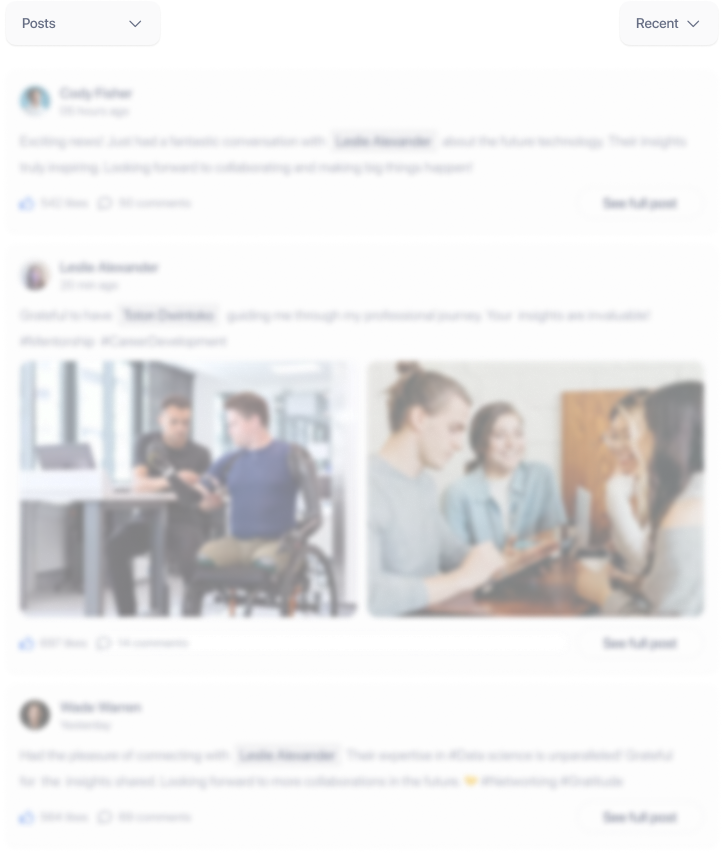