Zachary Diable
Senior Supply Chain Consultant at TriVista- Claim this Profile
Click to upgrade to our gold package
for the full feature experience.
Topline Score
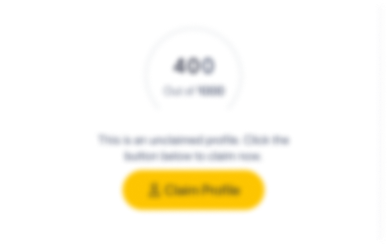
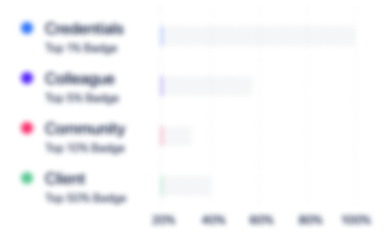
Bio


Credentials
-
Lean Six Sigma Black Belt (ICBB)
Villanova UniversityOct, 2022- Nov, 2024 -
Lean Six Sigma Green Belt
GE Transportation, a Wabtec companyMay, 2018- Nov, 2024
Experience
-
TriVista
-
United States
-
Business Consulting and Services
-
1 - 100 Employee
-
Senior Supply Chain Consultant
-
Jul 2022 - Present
• Execution of more than 20 M&A transactions, continuous improvement, and supply chain optimization projects for Private Equity clients and their portfolio companies ranging from $20M to $4B revenue• Led a multi-phase global supply chain transformation, relieving dependency on long-term contract manufacturer located in SE Asia. Established a North American supply base to alleviate geopolitical risk and supply chain disruption, while generating >$1.5M in cost reduction• Developed a consolidation strategy through a network optimization engagement that generated ~$14M/year in annual savings and further enabled business growth• Created reorder point model for client struggling with material availability, generating 80% reduction in stockouts and decrease of $300k in inventory Show less
-
-
Supply Chain Consultant
-
Jun 2021 - Jul 2022
-
-
-
GE Transportation, a Wabtec company
-
United States
-
Truck Transportation
-
700 & Above Employee
-
Lead Production Specialist
-
Nov 2020 - Jun 2021
• Coached team members in Pipe Shop and Cable Tray build areas of Texas Locomotive final assembly plant. • Developed standard work and area layout for insourcing of Cable Trays.• Implemented Standard Work and SOP’s to optimize one-piece flow through Pipe Shop elimination of batch building.
-
-
Materials Planning and Execution Specialist
-
May 2019 - Nov 2020
• Managed ~$2M inventory for Light Fabrications, Pipe Shop, and Harness Repair areas within Locomotive Manufacturing Plant.• Engaged cross functionally with Engineering, Quality, and Configuration Control to ensure correct material demand driven through Bill of Material accuracy.• Owned kitting for six product lines and improved line-side material presentation for bulk ordered items.• Interacted with international and domestic procurement and sourcing teams to ensure purchase order deliveries would support production schedule.• Implemented Material Handler standard work and procedures to improve material presentation as well as production efficiency. Show less
-
-
Operations Management Leadership Program
-
May 2017 - May 2019
Third Rotation – Console/CA1 PTA/Supervisor – Erie, PA (B12) • Led 16 hourly employees to meet customer commitments by ensuring appropriate schedule attainment and labor utilization. • Implemented continuous improvement projects to increase Console Area TOP (time on product) by 15% during rotation • Improved material availability at Point of use by ensuring 100% kit accuracy within first 5 units of the build. • Implemented 5S standards and ensured sustainment via a 5S scorecard graded on weekly basis.Second Rotation – Manufacturing Engineer (ME) – Grove City, PA (GRR) • Supported as ME for Pumps, Pins, Crowns, Laydown, and Assembly Hall by creating and documenting standard work procedures, implementing fixtures and tooling, and driving 5S standards plantwide.• Increased throughputs by an average of 44% in the laydown area through new pallet designs, tooling, and standard work.• Decreased GRR STO inventory by 40% and improved material control by implementing LEAN principals and operational improvements within the stockroom.First Rotation – Fulfillment Buyer – Grove City, PA (GRV) • Improved Material on Time Delivery from 76% to 84% by working cross functionally with suppliers, commodity, quality, engineering, and production to resolve complex problems.• CAS Blanket PO Project - Eliminated $5.7B of supplier inventory risk by ensuring blanket PO volume was reflective of forecasted demand. • Managed Fabrication fulfillment buy across a $9M spend, 20 suppliers, and 4 different customers across the United States. • Improved Supplier on Time to Promise from 71% to 78% by limiting non-value add PO changes. Show less
-
-
-
GE Transportation, a Wabtec company
-
United States
-
Truck Transportation
-
700 & Above Employee
-
Industrial Engineering Intern
-
May 2016 - Aug 2016
-
-
-
Altec
-
United States
-
Machinery Manufacturing
-
700 & Above Employee
-
Manufacturing Engineer Co-op
-
Jan 2015 - Aug 2015
-
-
-
West Virginia University
-
United States
-
Higher Education
-
700 & Above Employee
-
Teaching Assistant
-
Aug 2014 - Jan 2015
-
-
Education
-
West Virginia University
Bachelors Degree, Industrial Engineering -
Penn-Trafford High School
Community
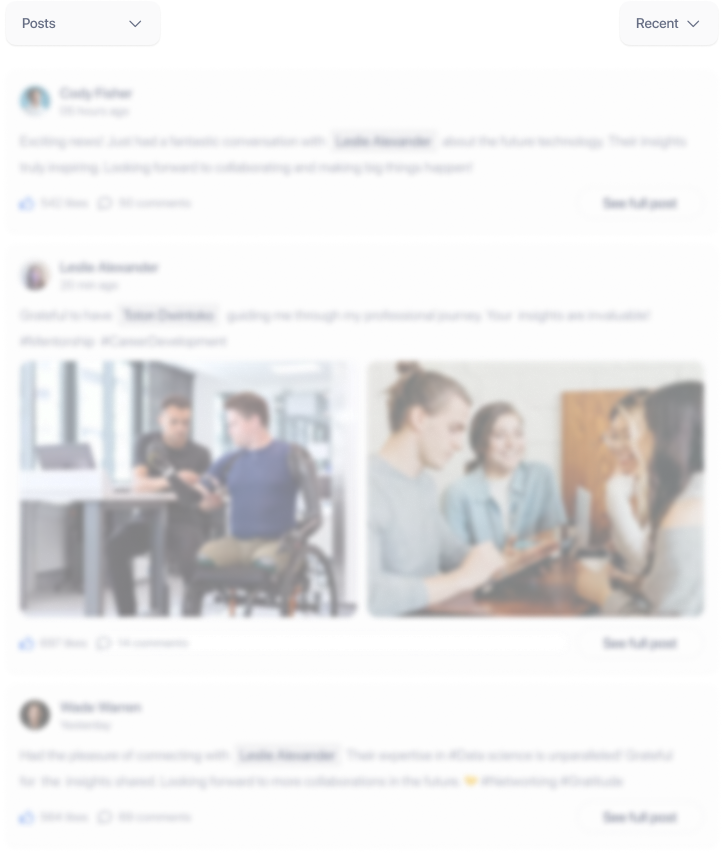