Yoann Guyon
Demand and Supply Manager at The Better Health Company (TBHC)- Claim this Profile
Click to upgrade to our gold package
for the full feature experience.
-
Anglais Professional working proficiency
-
Espagnol Limited working proficiency
-
Portugais Elementary proficiency
-
Chinois Elementary proficiency
Topline Score
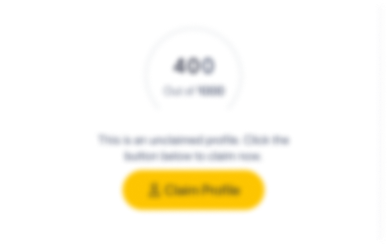
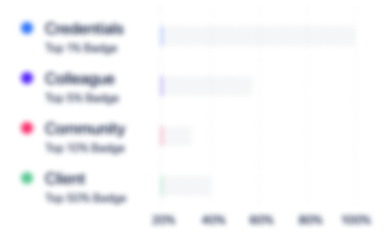
Bio


Experience
-
The Better Health Company (TBHC)
-
Health, Wellness & Fitness
-
1 - 100 Employee
-
Demand and Supply Manager
-
Sep 2022 - Present
Demand Forecasting:· Manage the monthly forecasting process at aggregate and detail level across GOAU and GONZ and NZHM contract, business units – Both Volume and Revenue· Prepare content and chair the monthly Demand Review as part of the overall Go Healthy S&OP process· Co-ordinate with Business Managers to ensure the forecasting process is finalized to meet the timelines and content for S&OPDemand Management· Ensure that supply and demand are balanced and where demand needs reshaping work with the relevant business divisions to increase/decrease demand and have these reflected in the forecasts· Manage and monitor NPD introduction to market, including forecasts and measurement of initial introduction successDemand Analysis:· Review and analyze forecast results in relation to business direction and provide business and sales managers with observations of forecast directions/insights. Demand analysis relates to both volume and revenue· Establish and maintain forecast performance measurement and evaluation· Identify product and/or market trends pertinent to forecast execution, including any market and category insight activitiesDemand Control: · Identify root causes of serial issues in process and/or operational performance, and develop any corrective actions required.· Ensure data integrity and quality by reviewing data, identifying unusual occurrences and exceptions, seeking explanations and assisting in developing corrections to prevent reoccurrences. Show less
-
-
Planning Manager - New Zealand Health Manufacturing
-
Dec 2021 - Aug 2022
Management of the Planning department with 5 direct reports, responsible of bringing the team together to ensure the plant is running smoothly.In charge of the manufacturing plan of 15 production machines and 7 packing lines, maximizing their production rate and minimizing the down times.Chair person of the S&OP meeting, analyzing short, mid and long term demand forecasts against production capacity. Reporting to the general management production capacity issues that will prevent us from achieving our customer satisfaction targets. Show less
-
-
Supply Chain Planner/Analyst - New Zealand Health Manufacturing
-
Sep 2020 - Dec 2021
New Zealand Health Manufacturing Limited (NZHM) was Founded in 2014 in order to meet a growing demand for New Zealand made dietary supplements. NZHM supplies complementary products across New Zealand, Australia and Asia.NZHM is part of The Better Health Company with GO Healthy NZ, GO Healthy AU and Egmont Honey.As a Supply Chain Planner / Analyst, I am demand forecasting for GO Healthy NZ business over 350 products and managing the sales orders for The Better Health Company group. Therefore, I am focusing on the end to end management of sales orders and maintaining data accuracy within the system (Netsuite).I am managing the full manufacturing plan to meet our customers' expectations in collaboration with Sales, QA and Production team leaders (50+ work orders a week to manufacture 10 million Hard Shell capsules, 15 to 20 million Soft Gel capsules and 1 to 2 million tablets a week)I am setting our monthly production targets and tracking our production achievements on a daily and a weekly basis. Strongly focused on problem solving, I also escalate any production capacity issue to the management team.Member of the S&OP team, I maintain ETA visibility to GO Healthy New Zealand and GO Healthy Australia, ensure DIFOT is achieved and raise any delay that may affect sales or promotional activities. Show less
-
-
Sales Analyst - GO Healthy NZ
-
Nov 2019 - Aug 2020
The main objective for GO Healthy: To reboost people with passion in order for them to be the best and to give the best of themselves.GO Healthy is the #1 brand selling complement pills in New Zealand.As a sales analyst, my role is to :- Analyse sales data in order to assist the Sales Director and his Team- Organize promotions with every customers (mainly pharmacies)- Coordinate promotions with the Design Team- KPI calculation and tracking- Create every report and data analysis (using Netsuite) to highlight issues and to bring solutions in a continuous improvement approach Show less
-
-
-
Toolog
-
France
-
Warehousing and Storage
-
1 - 100 Employee
-
Supply Chain Specialist
-
Feb 2017 - May 2019
Member of the Industrial Department (Team of three people), I worked with the Chief Executive, the Operations Manager and the QHSE manager in order to improve operational efficiencies at the warehouse. I was in charge of : • Supply and Demand Analysis for Consumables Management o Robust demand forecasts to order the exact quantity needed (3 to 12 months forecasts) to ensure deliveries to the final customer o Data Analysis using SQL and Excel VBA o Study and selection of new consumables or suppliers to optimize the triptych Cost-Quality-Time o Negotiation of prices with all suppliers • Continuous Improvement Project Manager o Building of a 4 levels mezzanine (12000m2) for shoes and clothes in order to increase the global storage capacity by 600 000 items (1.5 year project set up with MECALUX, Engie AXIMA and BEL D’ELEC) o Implementation of an automatic conveyor and two Qimarox lifts to convey boxes in and out each level of the mezzanine (1 year project set up with MECALUX and BK SYSTEMES) o Implementation of a conveyor and machines to recycle board wastes (6 months project set up with PAPREC) o Major changes of conveyors and machines in the Shipping Area to increase the parcels flux (9 months project set up with ACTEMIUM / VINCI ENERGY and BPLUS EQUIPMENT) • Functional Management of the maintenance department (1 Or 2 people, 3 days a week) • Industrial standard operating procedures and staff training • Staff training in Excel (25 people) and VBA (3 people) Show less
-
-
-
SPARTOO.COM
-
France
-
Internet Publishing
-
1 - 100 Employee
-
Demand Planner Manager
-
Oct 2014 - Jan 2017
Trinomial team work (Demand Planner, Buyer and Buyer Assistant) to manage over 80 famous international brands of shoes (e.g. Nike, Adidas, Asics...) • Robust demand analysis for the buyer to forecast future purchases (12 months forecasts) for next seasons • Stock optimisation and deliveries management • Day to day products replenishment for 80 brands and 10 000 models (succeeded in the objective of availability rate > 80%) • Monitoring an annual budget for products replenishment • Collaboration and negotiation with suppliers for each sales periods • Tools development in order to improve the company’s performances (sales projections, product life analysis...). Statistics made with Microsoft Excel • Tool development for purchases in the sales department : 20% more effective • Staff Training in VBA (100 people) Show less
-
-
-
STMicroelectronics
-
Switzerland
-
Semiconductor Manufacturing
-
700 & Above Employee
-
Internship Master's Degree : Optimization of the flow of goods
-
Feb 2014 - Jul 2014
Tests and deployment of a tool to manage product flows and optimise production times. - Data gathering using SQL requests - Data analysis using Excel and VBA - Tool creation with Excel VBA - Deployment of the tool - change management Tests and deployment of a tool to manage product flows and optimise production times. - Data gathering using SQL requests - Data analysis using Excel and VBA - Tool creation with Excel VBA - Deployment of the tool - change management
-
-
-
Becton Dickinson
-
Hospitals and Health Care
-
1 - 100 Employee
-
Assistant Engineer
-
Jun 2013 - Sep 2013
In a team of two people, I was in charge of the creation of a software to manage the planning and costs of the Engineering Service : - Conception and development of a tool using Excel VBA - Change management of all Engineering Service staff In a team of two people, I was in charge of the creation of a software to manage the planning and costs of the Engineering Service : - Conception and development of a tool using Excel VBA - Change management of all Engineering Service staff
-
-
-
Freemens
-
France
-
Renewables & Environment
-
1 - 100 Employee
-
Deployment Strategy Adviser
-
Apr 2013 - May 2013
Field study in a trinomial team for the deployment of a new company. Field study in a trinomial team for the deployment of a new company.
-
-
-
Schneider Electric
-
Appliances, Electrical, and Electronics Manufacturing
-
1 - 100 Employee
-
Assistant Engineer : Continuous Improvement Project Leader
-
Apr 2012 - Aug 2012
I was in charge of the development of a tool to manage every flow of goods in the shipping department: - Identification of all flows of goods - Tool development with Excel - Change Management for 5 people I was in charge of the development of a tool to manage every flow of goods in the shipping department: - Identification of all flows of goods - Tool development with Excel - Change Management for 5 people
-
-
Education
-
Grenoble Institute of Technology
Master Degree Industrial Engineering, Industrial Engineering -
Jacques Decour
Prepare for the highly competitive nationwide exams, Math and Physics
Community
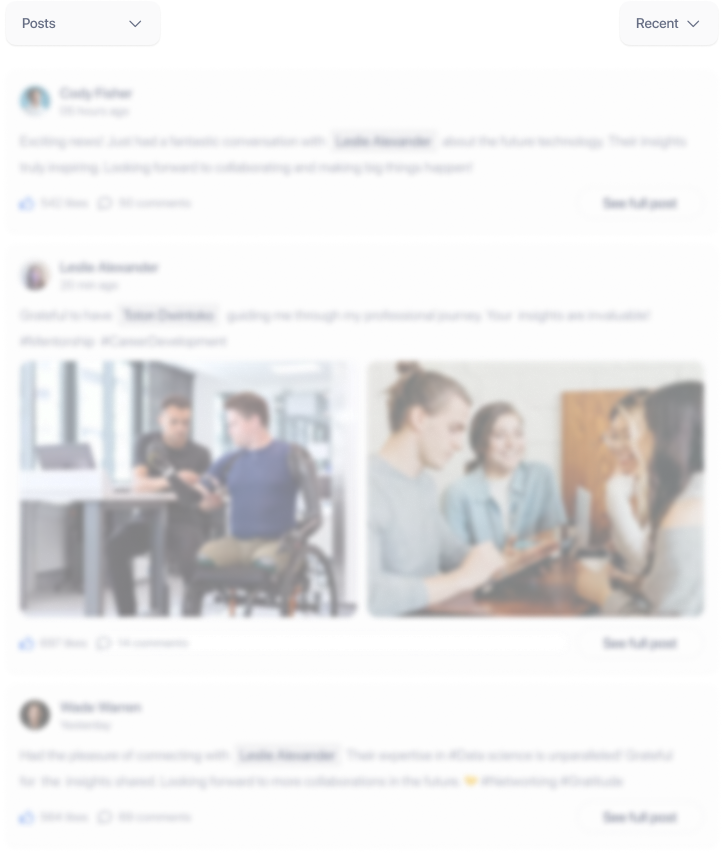