
Yakov Vinogradskiy
Lean Manager at AVM Industries- Claim this Profile
Click to upgrade to our gold package
for the full feature experience.
-
English Full professional proficiency
-
Russian Full professional proficiency
-
French Limited working proficiency
-
Romanian Limited working proficiency
Topline Score
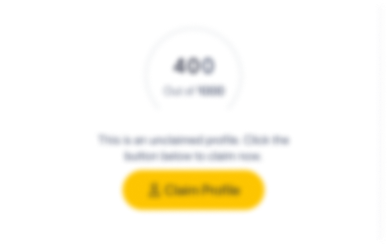
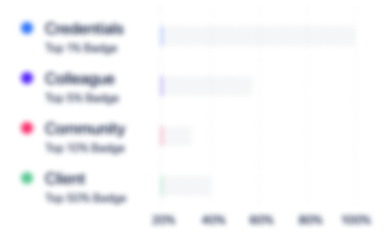
Bio


Credentials
-
Certified Lean Six Sigma Black Belt
General Electric -
Certified Scrum Master
Scrum Alliance -
TRIZ Specialist
The International TRIZ Association
Experience
-
AVM Industries
-
Automotive
-
1 - 100 Employee
-
Lean Manager
-
2015 - Present
Leading Tier1 supplier of gas springs lift supports in the automotive market, including GM, Honda & Toyota, and dampers and hydraulic motion control in Construction & Farm equipment, including John Deer & Bobcat. Responsible for leading initiatives for the organization through the complete Continuous Improvement lifecycle including: identifying opportunities, evaluating processes, translating requirements into action plans, developing and implementing solutions, training employees, monitoring new processes and providing ongoing support.• Work with site leadership in identifying CI opportunities within the manufacturing operation and suppliers based on 20 KPI assessment and evaluations.• Develop and implement 5S roll out plan throughout the plant.• Work with key stakeholders to drive process improvements that quantitatively and qualitatively improve costs, quality, distribution and service.• Reduce & eliminate material shortage issues by utilizing 8D & VSM tools that resulted in updated WI.• Manage cost improvement savings, track project progress to plan, work with project leads to assure timely completion and report out status periodically to plant and corporate leadership. • Lead cross functional teams in identifying, evaluating, and developing effective processes, procedures and solutions to meet business needs.• Improve delivery performance of Gas Springs product by developing more robust component scheduling system
-
-
-
Yokohama Tire Corporation
-
United States
-
Automotive
-
700 & Above Employee
-
Plant Quality Control Manager
-
2013 - 2015
Provided leadership to the over $100 M Tier 1 Supplier of power steering and transmission oil cooling coupling lines to Chrysler Fiat Automotive and Ford Motor Company in the area of maintaining and improving the quality systems. Duties included, but not limited to serving as the leading point of contact with customers when product or service quality omissions occur, quality management of 92 Tier II suppliers, change control, test methods & equipment, standard instructions, audits, manuals, and other normal quality systems capacities. Primary Responsibilities:• Provided hands-on management of the elements of the QMS (Quality Management System) TS/ISO 16949. These include corrective actions, supplier quality management, customer complaints, change control, audit processes, standard procedures, test methods, and process controls.• Generated scorecards and reports for all aspects of plant quality, not limited to and including external and internal CARs, SNCRs, KPI reporting, LPAs sand Change Control processes. • Acted as the lead plant representative for any meetings or interactions with customers as it relates to product or service quality• Participated on teams and lead efforts toward continuous improvement initiatives within the Plant
-
-
-
GE
-
United States
-
Industrial Machinery Manufacturing
-
700 & Above Employee
-
Certified Lean Six Sigma Black Belt
-
2008 - 2012
Accountable for implementing quality initiatives across EED by executing programs and projects for driving engineering quality in the processes from order inquiry to remittance by utilizing Lean Six Sigma. Drove and supported Lean Six Sigma quality initiative deployment throughout USA & Canada. Conducted training in Lean Six Sigma.• Significantly improved transparency, visibility and on time delivery (OTD) of 46 New Product Introduction (NPI) programs across EED by implementing Agile Lean methodology.• Reduced OTD of XL Go + video probe program by 7% by leading Agile lean NPI roll out.• Attained 18% cycle time reduction of Engineering/Manufacturing Schedule Review Process by conducting Lean Action Workout and Project.• Improved the EED Drawing quality by leading the development of End Yield Web Portal.• Achieved a 30% the bucket set cost reduction and developed 4 intellectual properties proposals by directing the 9F class Gas Turbine Stage 1 Bucket cost reduction project through the utilization of VEA, TI & TRIZ approaches. • Delivered 5 intellectual properties opportunities with estimated savings of $35K per unit by guiding TI and TRIZ workshops to reduce the cost of the GT Fuel System Enclosure.• Mentored 12 engineers to achieve Green Belt Six Sigma certification status.
-
-
-
Hendrickson
-
United States
-
Truck Transportation
-
700 & Above Employee
-
Quality Assurance Lead/Manager
-
2006 - 2007
Managed the implementation of TS 16949 Quality Management System. Led Corrective Action Requests to drive key suppliers improvements. Guided teams in key quality tools applications to drive improvement and solve problems.• Developed QMS key metrics and drove organization to continuous improvement actions: o Led the plant in dramatic Customer Satisfaction improvements from 4428 PPM to 35 PPM through implementation of 8D type cross functional workshops.o Achieved the shortest Plant Customer Concern Response Time within the division at 18 days by establishing accountabilities.o Accomplished overall Scrap Cost below target at 0.34% of Sold Goods by establishing sequential production inspections.
-
-
-
Dana Incorporated
-
United States
-
Motor Vehicle Manufacturing
-
700 & Above Employee
-
Six Sigma/Dana Production System (DPS) Manager
-
2005 - 2006
Led the Plant Lean Transformation by developing, directing and coordinating various productivity and quality improvements projects through Lean Manufacturing and Six Sigma Systems. Developed Plant wide statistical performance assessment. Reported metrics on a weekly basis to the Division Lean Group. • Established Five Value Streams within Plant to optimize production operations.• Conducted three Value Stream Mapping workshops and 18 Kaizen events.• Completed 34 productivity, quality and cost reduction Lean and Six Sigma projects.• Achieved $1.29M in estimated annualized savings in 2005 and 2006 by improving processes and product via eliminating waste and reducing non value added activities.
-
-
-
Visteon Corporation
-
United States
-
Motor Vehicle Manufacturing
-
700 & Above Employee
-
Lean Manufacturing Specialist
-
2000 - 2004
Visteon North American Aftermarket Group, Livonia, MI (2002 – 2004)Accountable for Lean Production System implementation within domestic and international manufacturing facilities of Aftermarket Hard Parts Division by providing Lean workshops, training and guiding transformation from Mass to Lean production system.• Led 3 VSM and 4 CCF Lean workshops that enabled several production facilities to make transition from Push to Pull systems.• Guided task force team of acquired plants through Lean transformation that resulted in $300K cost savings through the implementation of lean layout and single piece flow. Visteon Advanced Manufacturing /DPG, Ypsilanti, MI (2000 – 2002)Responsible for developing manufacturing and assembly processes for Fuel Cell Reformer. Devised advanced manufacturing processes for alternator varnish applications.• Reduced reformer lead-time by 82% by using Lean and Design for Manufacturing and Assembly (DFM&A) principles.• Developed six patentable concepts for Lean alternator stator and rotor varnish impregnation cells.
-
-
-
Ford Motor Company
-
United States
-
Motor Vehicle Manufacturing
-
700 & Above Employee
-
Manufacturing & Cost Reduction Engineer
-
1996 - 2000
Responsible for alternator stator varnish impregnation process. Sustained and improved production processes by defining process flow, developing Process FEMA, Control Plan and PPAP. Oversaw the turnkey ABB robots installation.• Reduced scrap by 75% by developing and implementing automated front slide varnish trickle system.• Led development of chemical cure varnish process that resulted in reduction of total cycle time by 30%.Responsible for cost reduction actions development and implementation in support of manufacturing operations within Alternator Engineering Department.• Increased throughput by 12% and decreased downtime by 14% of Rotor Varnish Impregnation bottleneck Process by developing and implementing Root Cause Analysis, Process FEMA and Work Procedures.
-
-
-
Ideation International
-
Software Development
-
1 - 100 Employee
-
TRIZ Specialist
-
1994 - 1995
Product and process improvement consulting company utilizing TRIZ (The Theory of Inventive Problem Solving) and VA/VE (Value Analysis/ Value Engineering)Devised innovative concepts of solutions based on TRIZ and VA / VE.• Ford Motor Company: Enhanced wind tunnel throughput by 3.5%.• Inland Fisher Guide: Improved functionality of headrest system and reduced NVH of window drive mechanism. Product and process improvement consulting company utilizing TRIZ (The Theory of Inventive Problem Solving) and VA/VE (Value Analysis/ Value Engineering)Devised innovative concepts of solutions based on TRIZ and VA / VE.• Ford Motor Company: Enhanced wind tunnel throughput by 3.5%.• Inland Fisher Guide: Improved functionality of headrest system and reduced NVH of window drive mechanism.
-
-
Education
-
Agricultural State University of Moldova
Master's degree, Mechanical Engineering
Community
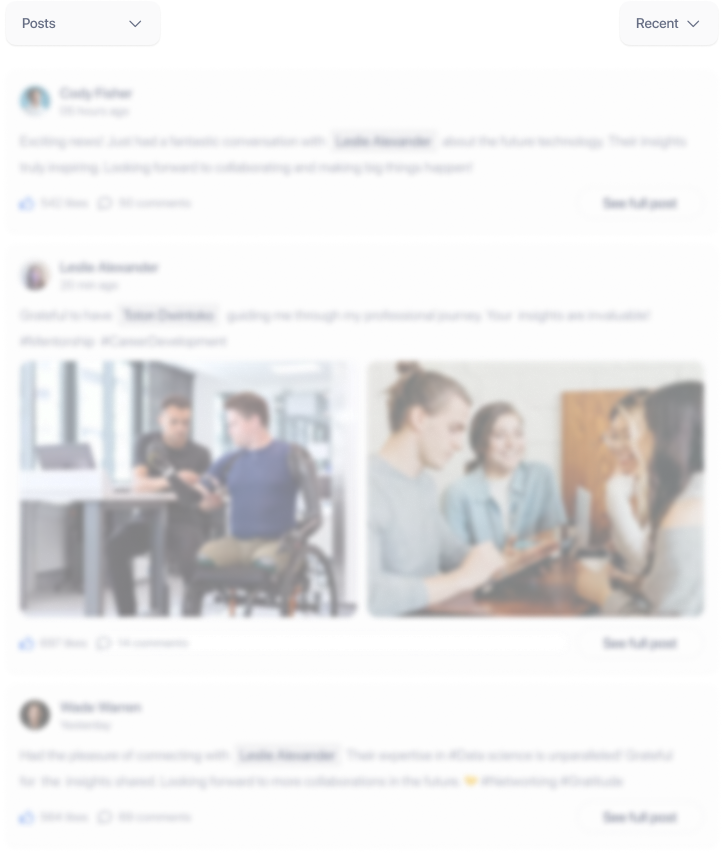