Yago F.
Chief Operations Officer at Hamble Aerostructures Ltd- Claim this Profile
Click to upgrade to our gold package
for the full feature experience.
-
Inglés Full professional proficiency
-
Francés Professional working proficiency
Topline Score
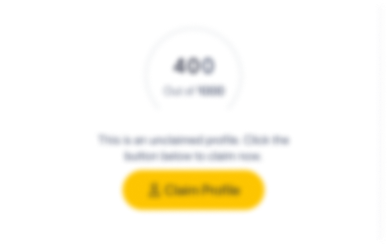
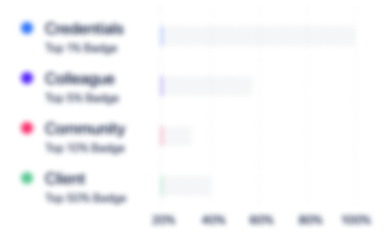
Bio


Experience
-
Hamble Aerostructures Ltd
-
United Kingdom
-
Airlines and Aviation
-
100 - 200 Employee
-
Chief Operations Officer
-
Jan 2020 - Present
in January 2020, Aernnova acquired GE Aviation's Hamble business unit , with the aim of expanding its Business in the UK , both for the Civilian and Defense Markets. Underpinned by the good trajectory at Coasa, I've then been requested by the Aernnova Board to drive the Transformation of this Company and take it to the Benchmark reference in the UK. Four years later and many Transformation Projects successfully implemented, mainly in the Organizational and Operational domaine, Hamble Aernnova Aerostructures has been Increasingly improving its performance and profitability. One of main Customers, Airbus, has recognized Hamble significant step change by awarding Aernnova in 2021 as the best Supplier in the Operational Excelence category. Show less
-
-
-
COMPONENTES AERONAUTICOS COASA SA
-
Spain
-
Business Consulting and Services
-
1 - 100 Employee
-
General Manager
-
Sep 2010 - Jan 2020
Throughout this decade, I've been striving to drive the Company orientated by some fundamental principals: 1. Create a “sharply-outlined” and recognizable Company Identity through a meaningful Vision&Mission Statement, widely communicated and published. 2. Operational Excelence, Lean Management across all Departments. 3. Company Goals shared and rolled-out through interlinked Departmental Balance Score Cards. 4. Implementation of DDMRP [ Demand Driven MRP] as Procurement methodology in order to reduce inventory and increase level of service. An outstanding 25% inventory reduction has been achieved whilst 100% Customer OTD been consistently maintained. 5. Drive behaviors by pursuing Value throughout our Operations in contra position to a cost reduction single-minded culture. Based on this Principals, Coasa has been increasingly improving its Operational KPIs ( OTD, OTQ) year after year, and achieving and maintaining double figures in Ebit versus Revenues. Other Key Drivers: • Increased efficiency, effectiveness and profitability by managing team productivity, costs and budgets. • Formed and sustained strategic relationships with clients. • Formulated business plans to maximise growth and lower costs for company. • Developed business strategies to establish short and long-term goals for company. • Delivered speeches at events and conferences to raise brand awareness. • Established professional relationships with business partners, shareholders and authorities to develop trust, rapport and reliability. Show less
-
-
-
COASA-AERNNOVA
-
Ourense, Galicia, Spain
-
Production Director
-
Jun 2006 - Sep 2010
During this period, the main focus was to strengthen the Company by enhancing the Operations. To that effect, a three years Road Map was pushed through underpinned by these two key pillars: 1. Customer Demand Management and Manufacturing Plans built under the TOC ( Theory of Constraints ) and DBR. ( Drum Buffer Rope ). 2. Push forward Production Standardization in order to drive efficiency and reduce lead times, and select the appropriate suit of Lean Manufacturing tools driven by core Process Value Stream Mapping. Other Key Drivers: • Achieved on-budget performance and production targets through effective management of teams and resources. • Assisted in various areas of manufacturing, safety, inventory control and process implementation. • Planned and coordinated position requirements, schedules and production team processes. • Completed key projects on time, on budget and with high level of accuracy. • Optimised team performance by articulating growth objectives and operating plans. • Trained, mentored and counselled employees to develop high-performing team. • Organised, prioritised and managed plant maintenance projects to keep facility safe, efficient and clean. • Enforced culture of lean manufacturing and continuous improvement while providing operational leadership. • Created workforce planning and development models to inform quarterly scheduling and processes. • Ensured profitable operations, conducting market research and reviewing production and sales costs. • Increased productivity and reduced material waste to establish coherence. Show less
-
-
-
COMPONENTES AERONAUTICOS COASA SA
-
Spain
-
Business Consulting and Services
-
1 - 100 Employee
-
Director of Quality
-
Apr 2001 - Jun 2006
COASA was founded in 2020 as the first and unique Composites Business Unit within the Gamesa Aeronautical Group in the northwest Spanish region of Galicia. As a brand new factory, everything was needed to be established from scratch, being the Quality Management System and Customer Process Qualification the fundamental milestone to enable the Business to operate In the sector. After a hard work , COASA started to deliver flight-able product in September 2001, and being certified against the EN 9100 as the first Gamesa Aeronautical´s site. Other Key Drivers: • Implemented improved policies and plans to enhance operational processes. • Controlled operational output by implementing quality procedures throughout production. • Applied Quality Assurance (QA) methodologies to measure output quality. • Conducted in-depth conclusions with customers to obtain extensive understandings of their expectations and needs. • Managed inspections, fault-finding and diagnosing malfunctions on products. Show less
-
-
-
Groupe PSA
-
France
-
Motor Vehicle Manufacturing
-
700 & Above Employee
-
Laboratory Manager
-
Nov 1995 - Apr 2001
Just a few months after completing my University degree in Engineering , I had the opportunity to join the biggest and more important Industrial Company of Galicia , Citroën Hispania. I spent several months traveling around the different french site as part of my training and preparation to take over the Laboratory, which happened one year after I first joined. I drove the team and the department through a full transformation, where up-spilling the team and expanding the knowledge was the main focus in order to set up the Laboratory as the technical reference point for the whole factory and the PSA Group. Other Key Drivers: • Coordinated and assigned routine responsibilities to subordinates to complete daily job tasks successfully. • Applied all applicable OSHA and local safety requirements to all assigned work to avoid injury and illness. • Performed all work by organisational regulations, policies and accreditation requirements. • Planned and executed continuous improvement projects within lab teams. • Kept up to date with advances in food testing to fulfill evolving test requirements. • Performed bench work to maintain proficiency and competency in technical operations. • Adapted evolving procedures, processes and techniques to meet requirements of position. • Provided safe working environment throughout lab facility for all employees to avoid employee injuries. • Delivered clear task directions and responded accordingly to employee inquiries about assigned job duties. Show less
-
-
Education
-
Universitat Ramon Llull
Master's degree, Agronomy and Crop Science -
Escuela de Negocios Caixanova
Operations and Advance Finance, Business Administration, Management and Operations -
Escuela de Negocios Caixanova
Operations Management, Business Administration, Management and Operations -
Universitat Ramon Llull
Double Grade in Industrial and Chemistry Enginnering, Engineering
Community
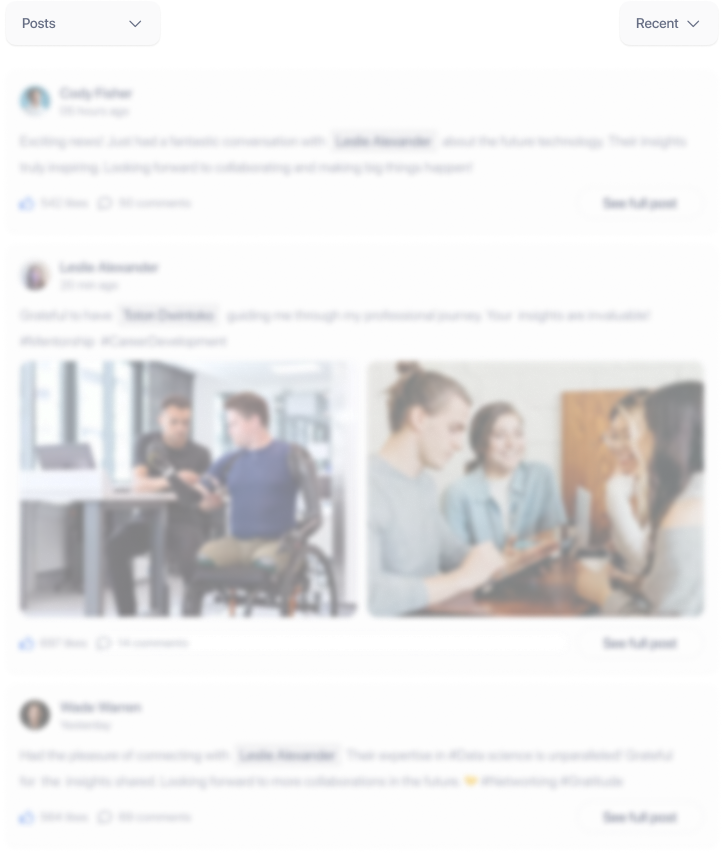