
Woody Brown
President / Engineer at TavaTek LLC- Claim this Profile
Click to upgrade to our gold package
for the full feature experience.
Topline Score
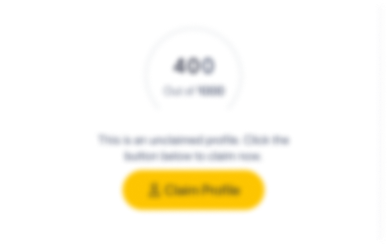
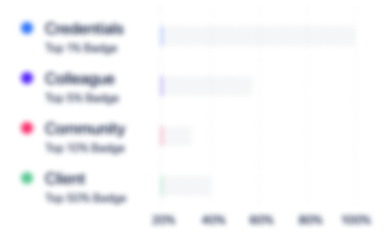
Bio
0
/5.0 / Based on 0 ratingsFilter reviews by:
Experience
-
TavaTek LLC
-
United States
-
Industrial Machinery Manufacturing
-
1 - 100 Employee
-
President / Engineer
-
Aug 2018 - Present
Business development for startup business focused on offering machine-building, process development, and process improvement/lean consulting. Custom designed and built automatic machine tools for clean-room applications. Business development for startup business focused on offering machine-building, process development, and process improvement/lean consulting. Custom designed and built automatic machine tools for clean-room applications.
-
-
-
-
Business Owner
-
Jun 2018 - Present
-
-
-
-
Business Process Improvement Manager
-
Apr 2016 - Jun 2018
Developing process improvement solutions for “last mile” delivery of medical devices from distribution to the operating room; developed and tested technologies (RFID/Bluetooth) to track usage of medical instrument trays and implants for company-owned product inventory from forward stock location in and out of the hospital, and in and out of operating room and Sterile Processing Department.
-
-
Global Lean Process Improvement Manager
-
Jun 2012 - Apr 2016
Lean consultant for all Synthes production facilities around the world, teaching, coaching and managing projects. Spearheaded the ongoing support of Lean initiatives and promoted Lean methodologies in the development of new and existing production processes. Implemented ‘lean best practices’ at all 19 Synthes production facilities located around the world. Strategically facilitated work with leaders throughout the company, applying the lean philosophy for continuous improvement and waste reduction in manufacturing and business processes. Developed a custom, global Lean training program and trained 4,000 employees in six languages across 10 countries. Partnered with sales field to enhance the supply chain through to the customer’s level. Attended surgeries and worked within the hospital Sterile Processing Departments. Trained hospital SPD staff in Lean techniques and developed programs to complete the supply chain link to the OR. Developed the innovative ‘Synthes Metro Office’ “forward stock location” concept for key US metro locations (Atlanta, Baltimore, Chicago, Dallas, Los Angeles and New York). Successfully built prototype office in Philadelphia for corporate visibility, providing support to 30 sales consultants and the vision and strategic plan for Super Metro Office and ‘hub & spoke’ implementation around the US. Developed a strategic plan to deliver DePuy Synthes surgical products directly to the point-of-use in the hospital operating rooms, which was called “JIT to the OR.” Plan includes a strategy around goals, objectives, targets and costs.
-
-
-
-
Global Lean Process Improvement Manager
-
2007 - 2012
-
-
Engineering Manager
-
Jan 1996 - Dec 2006
Responsible for development, capital appropriation, execution and financial accountability of key production projects. Mentored and trained facility staff in upholding company’s manufacturing philosophies as the in-house subject matter expert for the Synthes Production System. Led and managed a group of 26 engineers, supporting the production of 30,000 SKU’s in small lot sizes from raw material to finished goods within a 2-3 day lead-time. Maintained a small single location inventory of product (< 6 weeks total) and supported overnight delivery of finished goods to 6,500 customers throughout the US. Implemented Synthes Production System in four plants in the US, six in Switzerland, one each in Germany, Mexico, Brazil and China. Developed unique quick change, small lot heading and machining process for bone screw production worldwide. Established unique relationship with custom machine manufacturer (Hasagawa, Japan) to develop and engineer small footprint custom machines, making Monument’s production facility the largest, most cost-effective single bone screw manufacturing plant in the world, producing over 12 million finished goods screws and 9 million blanks in less than 4,000 square feet for markets in Switzerland, China, Mexico and Brazil.
-
-
New Product Development Manager
-
1994 - 1996
Developed business and marketing plans for the complete product line of Cannulated Bone Screw Implants and their associated surgical instruments. Communicated those plans throughout the sales organization within the US. Recognized as the expert with the most thorough knowledge involving the production of Cannulated Bone Screws, their features and clinical benefits. Designed new percutaneous screw and wire guide as well as a new multiple angle guides for femoral neck fracture fixation with 7.3 mm Cannulated Screws. Developed new guide wire in stiffer L605 Steel material. Successfully executed the development of an entirely new product line of Titanium Cannulated Screws in five different diameters for use with 18 different surgical implant and instrument sets. These engineering advances pushed the company to gain considerable market share of Cannulated Screws and become the market leader in orthopaedic trauma products.
-
-
Production Manager
-
1991 - 1994
Analyzed worker activities with focus on creating innovative, appropriate production schedules to better meet internal management and external customer needs. Requisitioned materials, assigned responsibilities and ensured deadlines for production and new product launches were exceeded. Established work procedures and implemented measures to improve production methods.Managed 50 employees, in the Nail and Ex-Fix production department. Successfully transferred production of External Fixation products and all associated equipment from Monument, CO to Brandywine, PA with zero loss to item fill rate. Successfully developed new production cells for Universal and Tibia Nails, growing production to an annual volume of 30,000 units and 70,000 units respectively while still requiring fixed lot sizes and a strict timetable scheduling for long-term success.
-
-
Manufacturing Engineer
-
1981 - 1991
Developed new production systems and implemented new manufacturing process solutions. Communicated to senior management the production plans and rationale for the capital funding. Developed core manufacturing production cell concept and built dozens of manufacturing cells to support double-digit annual sales growth. Invented and awarded United States Patent titled: Method and Apparatus # 5,073,694 for Laser Cutting of a Hollow Metal Work Piece. Installed and troubleshot manufacturing equipment and performed necessary maintenance crucial to vital production machines. Used mechanical and technical skills to analyze and develop production processes and programmed CNC and PLC machine controllers. Designed and built custom machines / electrical, hydraulic, pneumatic control systems and wrote PLC programs. Assigned to team that developed initial and long-term Synthes manufacturing culture.
-
-
Education
-
University of Colorado Colorado Springs
Community
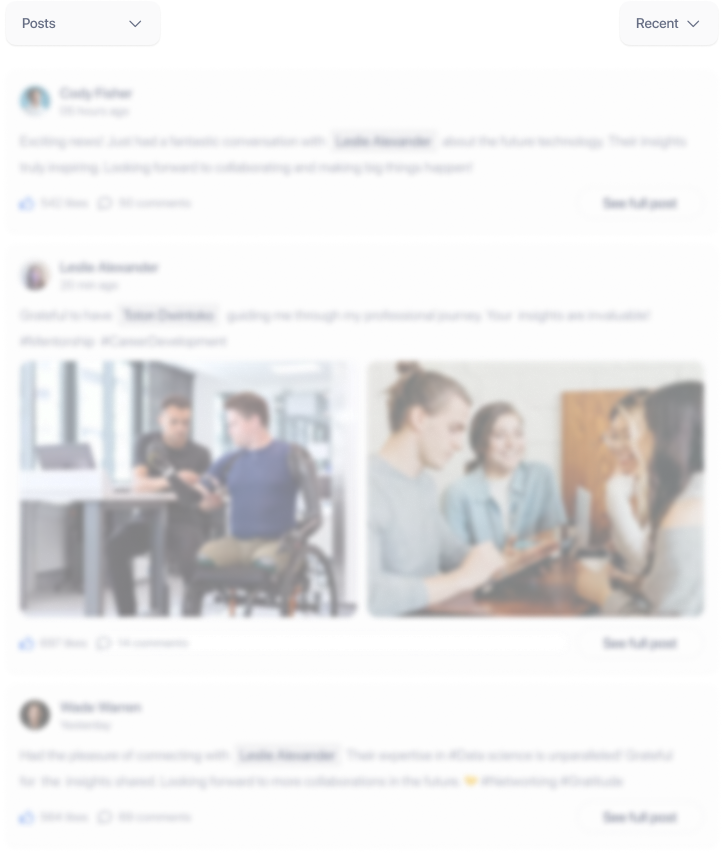