Dongki (D.K.) Won, PE
Engineer at Samuel Pressure Vessel Group- Claim this Profile
Click to upgrade to our gold package
for the full feature experience.
-
English -
-
Korean -
Topline Score
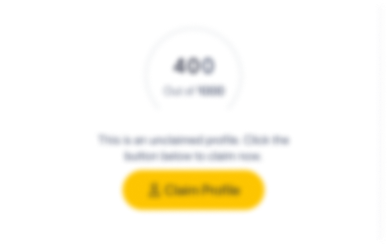
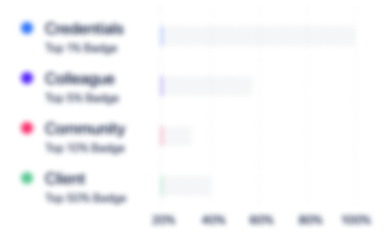
Bio


Credentials
-
Professioanl Engineer, Georgia and Texas
NCEESMay, 2022- Nov, 2024
Experience
-
Samuel Pressure Vessel Group
-
United States
-
Mining
-
1 - 100 Employee
-
Engineer
-
Oct 2021 - Present
-
-
-
Arseal
-
United States
-
Oil and Gas
-
1 - 100 Employee
-
Engineer II
-
Oct 2018 - Nov 2019
Create P&IDs and Review mechanical drawings for oil & gas pipelines as per ASME B31.4. Created BOM and tracked long lead items including various valves, equipment, pipe and fittings. • Prepare construction package including P&IDs and mechanical drawings for Epic Upton Pump Station and Terminal, located in Midland Texas in 3-month time frame, delivering product perfectly on time Create P&IDs and Review mechanical drawings for oil & gas pipelines as per ASME B31.4. Created BOM and tracked long lead items including various valves, equipment, pipe and fittings. • Prepare construction package including P&IDs and mechanical drawings for Epic Upton Pump Station and Terminal, located in Midland Texas in 3-month time frame, delivering product perfectly on time
-
-
-
Otis Elevator Co.
-
Consumer Services
-
700 & Above Employee
-
Senior Mechanical Engineer
-
Jan 2017 - Apr 2018
Senior Mechanical Engineer at Otis Elevator Co. Designed new parts for high rise elevator, provided product support, interfaced with field engineer. • Conducted finite element analysis and analytical review for the design of the rail bracket to reduce the thickness, resulting in installation and manufacturing cost reduction. Senior Mechanical Engineer at Otis Elevator Co. Designed new parts for high rise elevator, provided product support, interfaced with field engineer. • Conducted finite element analysis and analytical review for the design of the rail bracket to reduce the thickness, resulting in installation and manufacturing cost reduction.
-
-
-
American Bureau of Shipping (ABS)
-
United States
-
Maritime Transportation
-
700 & Above Employee
-
Senior Engineer
-
Dec 2008 - Sep 2016
Reviewed design and issued ABS certificate and approval letter of various drilling equipment undergoing high well bore pressure, including blow out preventer (BOP), marine riser, choke and kill manifolds, and pressure vessels. Checked drawings, bill of materials, FEA design calculation and test reports as per API 16A, 6A, 16F, 8C and ASME Boiler and Pressure Vessel Code Section VIII. • Conducted finite element analysis and verified the design of BOP body and rams, expediting process from 4 weeks to 2. • Finished review of equipment in 4-week time frame, delivering product perfectly on time. • Verified and resolved design issue of water tank and heat exchanger using engineering software compress, resulting in saving production cost. • Managed GE design project to review request of various oil well drilling equipment, verified design document packages, helping team finish review and deliver product on time. • Saved construction cost of arctic navigating vessels by conducting static and dynamic finite element analysis (FEA/FEM) with Ansys and Nastran that simulated plastic deformation of front hull structure due to ice floe impact loading. • Avoided experiment cost of liquefied natural gas (LNG) carriers by finding dynamic response of inner hull structure for impact pressure loading by liquid sloshing. Show less
-
-
-
University of Florida
-
United States
-
Higher Education
-
700 & Above Employee
-
Assistant Research
-
2003 - 2005
Performed finite element analysis to improve milling performance and increase productivity. Simulated wear with Coulomb friction model between two surfaces in artificial knee joint and pin-pivot system • Reduced the cost of manufacturing product by suppress chatter (vibration) of the milling process by inserting additional damping. • Predicted service time of artificial knee joint and pin-pivot system by conducting finite element analysis (FEA) with coulomb friction model using Ansys Performed finite element analysis to improve milling performance and increase productivity. Simulated wear with Coulomb friction model between two surfaces in artificial knee joint and pin-pivot system • Reduced the cost of manufacturing product by suppress chatter (vibration) of the milling process by inserting additional damping. • Predicted service time of artificial knee joint and pin-pivot system by conducting finite element analysis (FEA) with coulomb friction model using Ansys
-
-
Education
-
Texas A&M University
Masters of Engineering (ME), Civil Engineering -
University of Florida
Masters of Science (MS), Mechanical & Aerospace Engineering
Community
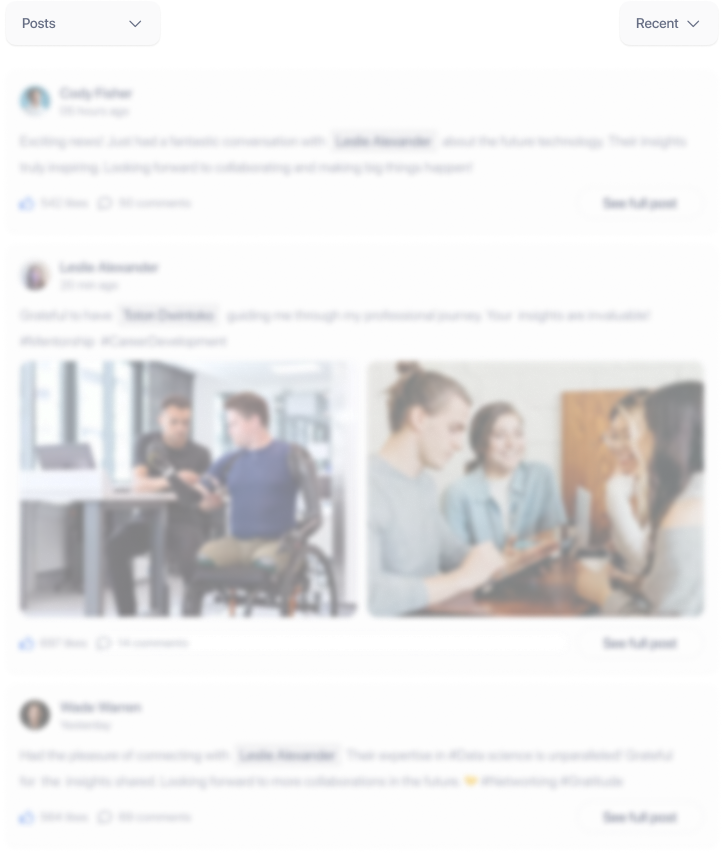