Willy Weinmann
Vice President Quality Assurance at Haydon Corporation- Claim this Profile
Click to upgrade to our gold package
for the full feature experience.
Topline Score
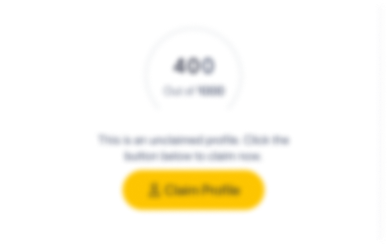
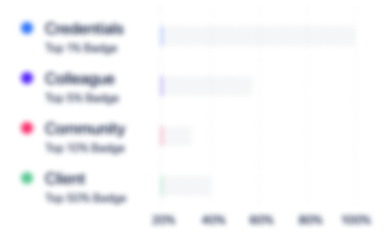
Bio

Khai Luong
What Willy has done to Alpine Biomed was undeniable proof that QA/RA should not necessarily be a burden to the business. With a thorough understanding of the business requirements and needs, Willy’s very effective skills and pragmatic nature have made quality an added-value to operations, with tremendous benefits to the organization. Under Willy's tenure, quality became the fiber of the company culture and values, and compliance evolved from being an obligation of every department into a pride of everyone.

Mark Ehlert
Willy was a wonderful, detail oriented manager that always had a good feel for the pulse of the organization and the issues he faced in his role at Hospira. He worked closely with Operations and R&D, always in a collaborative effort and quite often, provided answers to those difficult questions before his colleagues. A good friend and valued colleague!

Khai Luong
What Willy has done to Alpine Biomed was undeniable proof that QA/RA should not necessarily be a burden to the business. With a thorough understanding of the business requirements and needs, Willy’s very effective skills and pragmatic nature have made quality an added-value to operations, with tremendous benefits to the organization. Under Willy's tenure, quality became the fiber of the company culture and values, and compliance evolved from being an obligation of every department into a pride of everyone.

Mark Ehlert
Willy was a wonderful, detail oriented manager that always had a good feel for the pulse of the organization and the issues he faced in his role at Hospira. He worked closely with Operations and R&D, always in a collaborative effort and quite often, provided answers to those difficult questions before his colleagues. A good friend and valued colleague!

Khai Luong
What Willy has done to Alpine Biomed was undeniable proof that QA/RA should not necessarily be a burden to the business. With a thorough understanding of the business requirements and needs, Willy’s very effective skills and pragmatic nature have made quality an added-value to operations, with tremendous benefits to the organization. Under Willy's tenure, quality became the fiber of the company culture and values, and compliance evolved from being an obligation of every department into a pride of everyone.

Mark Ehlert
Willy was a wonderful, detail oriented manager that always had a good feel for the pulse of the organization and the issues he faced in his role at Hospira. He worked closely with Operations and R&D, always in a collaborative effort and quite often, provided answers to those difficult questions before his colleagues. A good friend and valued colleague!

Khai Luong
What Willy has done to Alpine Biomed was undeniable proof that QA/RA should not necessarily be a burden to the business. With a thorough understanding of the business requirements and needs, Willy’s very effective skills and pragmatic nature have made quality an added-value to operations, with tremendous benefits to the organization. Under Willy's tenure, quality became the fiber of the company culture and values, and compliance evolved from being an obligation of every department into a pride of everyone.

Mark Ehlert
Willy was a wonderful, detail oriented manager that always had a good feel for the pulse of the organization and the issues he faced in his role at Hospira. He worked closely with Operations and R&D, always in a collaborative effort and quite often, provided answers to those difficult questions before his colleagues. A good friend and valued colleague!

Credentials
-
7 Habits of Highly Effective People
Stephen Covey -
Front Line Leadership Facilitator
Zenger Miller -
Journeyman Machinist
International Association of Machinist and Aerospace Workers -
Quest Team Skills Facilitator
Zenger Miller -
Senior Leadership Program
Abbott Laboratories
Experience
-
Haydon Corporation
-
United States
-
Manufacturing
-
1 - 100 Employee
-
Vice President Quality Assurance
-
Sep 2022 - Present
At Haydon, we deliver the highest-quality metal framing, roof top support and baseboard systems with the power and reach of a national leader and the flexible, personalized approach of a local supplier. Over more than half a century, Haydon has grown to become a national leader in our industry, and we know what it takes for each project to succeed. At Haydon, we deliver the highest-quality metal framing, roof top support and baseboard systems with the power and reach of a national leader and the flexible, personalized approach of a local supplier. Over more than half a century, Haydon has grown to become a national leader in our industry, and we know what it takes for each project to succeed.
-
-
-
Applied Science, Inc.
-
Medical Equipment Manufacturing
-
1 - 100 Employee
-
Vice President Quality - Medical Device
-
Aug 2020 - Sep 2022
As a member of the Senior Executive Staff responsible for maintaining our corporate quality management system to ensure all activities promote customer satisfaction, meet regulatory requirements and positively impact the financial performance of ASI. Champion continuous improvement efforts and defect reduction initiatives to maintain an effective Quality Management System (QMS) and a high-quality product. As a member of the Senior Executive Staff responsible for maintaining our corporate quality management system to ensure all activities promote customer satisfaction, meet regulatory requirements and positively impact the financial performance of ASI. Champion continuous improvement efforts and defect reduction initiatives to maintain an effective Quality Management System (QMS) and a high-quality product.
-
-
-
IDEX Corporation
-
United States
-
Machinery Manufacturing
-
700 & Above Employee
-
Vice President Quality Assurance / Regulatory Affairs
-
Feb 2014 - Dec 2019
Spearheaded overall quality assurance and regulatory affairs responsibility of seven sites in USA. Developed, implemented, and established dashboard to monitor multi-site quality systems to assure compliance with ISO standards and medical device customer requirements. Initiated action to prevent non-conformities. Identified and documented quality problems and verified solutions to product problems. Participated actively in customer and notified body inspections including responding to observations, securing agreement of corrective actions, and overseeing implementation of corrective actions. Advised senior management on appropriate resolution of issues posing risk to company. - Developed strategic sourcing team resulting in $4,500,000 savings. - Reduced product complaint rates by 79% (from 4891 to 1006 DPPM) through implementation of a robust CAPA process. - Led reduction of Cost of Poor Quality (CoPQ) 31% from 2.6% to 1.8% returning $2,800,000 to bottom line. - Overhauled product development process with key focus on design transfer process to confirm products readiness for launch and market adoption. - Achieved ISO9001; 2015 for seven sites while reducing registrars from 4 to 1. Show less
-
-
-
Baxter International Inc.
-
United States
-
Medical Equipment Manufacturing
-
700 & Above Employee
-
Director Of Quality Assurance - Medical Device
-
Aug 2012 - Feb 2014
Accomplished objectives in developing a Quality Systems Improvement Plan (QSIP) for a newly acquired IV infusion pump business. Led a team of 10 in integration of quality systems with Baxter Medical Products. Acted as primary interface for regulatory inspections, including FDA and ISO. - Aligned with quality initiatives by serving as the sites quality management representative and ensuring accountability for all activities related to quality assurance function. - Successfully addressed and closed outstanding 483s and ISO 13485 non-conformances. Subsequent ISO recertification audit resulted in no non-conformances. - Upheld quality assurance (QA) standards in key areas using strategic planning, continuous improvement, lessons learned, supplier quality, process control, and audits. Show less
-
-
-
-
VIce President Quality Assurance / Regulatory Affairs- Medical Device
-
2008 - 2012
Developed and executed the Quality Assurance and Regulatory Affairs strategy and led all Quality Assurance and Regulatory Affairs due diligence activities in support of the overall business plan to build the company into a global specialty diagnostic device leader in the gastroenterology and neurology clinical markets leading to the strategic sale of Alpine Biomed’s Neurodiagnostic business to Natus Medical and the Gastrodiagnostic business to Given Imaging Ltd . Both transactions positioned the businesses as global leaders in their respective industries. QUALITY ASSURANCE - Developed and implemented a global corporate Quality Management System (QMS) resulting in the successful certification of the QMS to ISO13485;2003,Canadian Medical Device Regulation (CMDCAS) and compliance to 21CFR Part 820 Quality System Regulations for our facilities in the U.S., Canada, Denmark and Vietnam. - Developed and implemented standardized corporate quality reports and KPI’s to measure product quality and quality system effectiveness at each facility. - Developed and implemented an integrated global CAPA, Complaint Handling and Risk Management process resulting in a world class post market surveillance program. REGULATORY AFFAIRS - Established and implemented strategy to consolidate multiple manufacturing sites into a single “Notified Body” capable of providing global support. This initiative afforded the business an efficient means of optimizing product manufacturing capability. - Served as primary regulatory interface with FDA, Canadian Medical Device Bureau, EU and other country Ministries of Health. - Maintained CE Technical Files in compliance with the Medical Device Directive (MDD). - Maintained Design History Files (DHF) in compliance with 21CFR820 to support 510k submissions. - Completed 14 international submissions including China, Brazil, Canada, Colombia, Japan and Mexico in three years. Show less
-
-
-
Abbott
-
United States
-
Hospitals and Health Care
-
700 & Above Employee
-
Director Global Quality Assurance - Medical Device
-
1988 - 2008
Promoted through increasingly responsible positions in the Quality Assurance. Planned and directed activities connected with development, application and maintenance of quality standards for manufacturing processes of medical devices. Transformed the Electro-Mechanical Quality Assurance unit from a reactive functionally centric organization to a proactive Business unit. Director of two manufacturing sites, one third party manufacturer, five functional managers and approximately 75 exempt and non-exempt employees. Worked diligently to establish strategic plan, policies and procedures, to streamline production processes, reduce costs, and ensure quality products. Scope of responsibility included: Quality Assurance - Reduced overhead costs through a “Quality at the Source” initiative by 39% or the equivalent of $3.65M. - Improved product quality 22% by utilizing and reducing customer complaints. - Utilized Lean Sigma techniques to integrate quality assurance testing into the manufacturing process. - Championed development and implementation of inspection and acceptance procedures to address critical productivity, efficiency and quality issues. Global Service Center Appointed as the Quality Assurance project leader for planning, launching and management of nine Global Service Centers including Taiwan, Australia, Spain, Ireland, Chili, Columbia, Brazil and Canada. Maintained a stellar compliance record with FDA and Notified Body by consistently ensuring compliance within the QSRs (21CFR Part 820 Quality System Regulations) and ISO13485. Functioned as inspection administrator for all external and internal audits; interface with agencies such as FDA, Ministries of Health, Notified Body. Show less
-
-
-
Johnson & Johnson
-
United States
-
Hospitals and Health Care
-
700 & Above Employee
-
Quality Assurance Engineer - Medical Device
-
1983 - 1988
Supplier Quality Engineer – 9/87 to 6/88 Responsible for contracting electro/mechanical assemblies associated with two existing product lines. Quality Engineer - 5/86 to 9/87 Identified and recommended solutions for process related problems through analysis of data collected, resulting in increased yields during manufacturing process. Responsible for supplier surveys and qualifications as well as monitoring supplier performance. Provided technical support for supplier related process problems. Served as the Quality Assurance representative with the responsibility of transitioning product from Research & Development to Production. Quality Assurance Supervisor - 11/85 to 5/86 Managed staff of eight technicians; responsible for the quality of medical infusion devices, IV administration sets and sterilization. Quality Assurance representative on new product and process development task forces. Quality Assurance representative on Material Review Board and Change Control Board. Responsible for departmental budgets and monthly reports for submission to division manager. Responsible for all regulatory activities as required by FDA, to include FDA inspections. Incoming Quality Assurance Supervisor - 5/84 to 11/85 Responsible for development and implementation of manufacturing process control and Quality Assurance systems in compliance with state and federal medical device manufacturing regulations. Additional responsibilities included implementation of acceptance standards for incoming material such as printed circuit boards, printed circuit assemblies, industry standard components, injection molded parts, etc. Senior Precision Mechanical Inspector - 6/83 to 5/84 Responsible for incoming inspection of injection molded, casted and machined parts. Performed complex first article inspections working from blueprints. Show less
-
-
Education
-
IAM&AW
Journeyman Machinist, Computer Numerically Controlled (CNC) Machinist Technology/CNC Machinist
Community
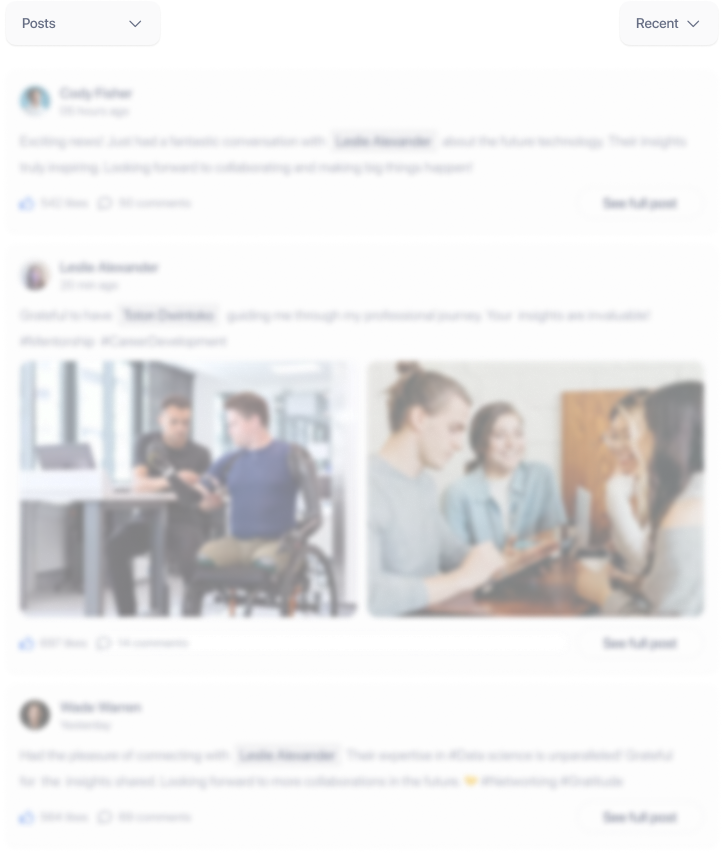