
William E. Hernandez
Improvement Scientist / Contract Consultant at NOVACES International Management Consulting Ltd Sti- Claim this Profile
Click to upgrade to our gold package
for the full feature experience.
-
Spanish -
Topline Score
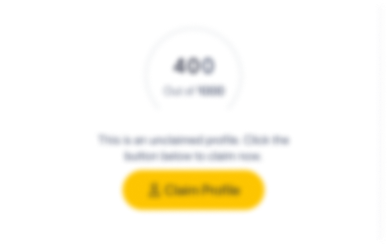
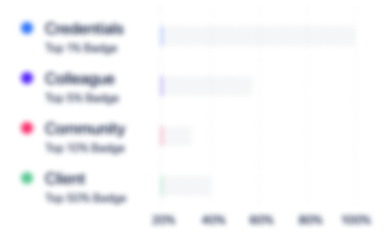
Bio

Jack Gaige
William is one of the best Master Black Belts that I have have the privledge of working with. His knowlege of LSS and CPI is exceptional. He is a versed and talented facilitator and instructor and takes pride in mentoring and coaching other belts. He sees the big picture and always works towards continuous process improvement. He is a major player on my staff.

Michael Blair CLSSBB
Over the past two years I have had the pleasure of working together on numerous projects with Will Hernandez at the Air Forces Air Combat Command in Langley Virginia. His knowledge level of Organization Change Management and Statistical Analysis is second to none. He taught me something new with each and every project. He doesn't just facilitate meetings and projects. He is truly gifted in mentoring organizations in real sustainable organizational change. On numerous occasions I have seen him get results where others have failed. If I owned a company Will Hernandez would be one of the first people I would want on my team. I would recommend Will Hernandez for any leadership role within any organization knowing that he would achieve immediate sustainable results and the organization would benefit for years to come.

Jack Gaige
William is one of the best Master Black Belts that I have have the privledge of working with. His knowlege of LSS and CPI is exceptional. He is a versed and talented facilitator and instructor and takes pride in mentoring and coaching other belts. He sees the big picture and always works towards continuous process improvement. He is a major player on my staff.

Michael Blair CLSSBB
Over the past two years I have had the pleasure of working together on numerous projects with Will Hernandez at the Air Forces Air Combat Command in Langley Virginia. His knowledge level of Organization Change Management and Statistical Analysis is second to none. He taught me something new with each and every project. He doesn't just facilitate meetings and projects. He is truly gifted in mentoring organizations in real sustainable organizational change. On numerous occasions I have seen him get results where others have failed. If I owned a company Will Hernandez would be one of the first people I would want on my team. I would recommend Will Hernandez for any leadership role within any organization knowing that he would achieve immediate sustainable results and the organization would benefit for years to come.

Jack Gaige
William is one of the best Master Black Belts that I have have the privledge of working with. His knowlege of LSS and CPI is exceptional. He is a versed and talented facilitator and instructor and takes pride in mentoring and coaching other belts. He sees the big picture and always works towards continuous process improvement. He is a major player on my staff.

Michael Blair CLSSBB
Over the past two years I have had the pleasure of working together on numerous projects with Will Hernandez at the Air Forces Air Combat Command in Langley Virginia. His knowledge level of Organization Change Management and Statistical Analysis is second to none. He taught me something new with each and every project. He doesn't just facilitate meetings and projects. He is truly gifted in mentoring organizations in real sustainable organizational change. On numerous occasions I have seen him get results where others have failed. If I owned a company Will Hernandez would be one of the first people I would want on my team. I would recommend Will Hernandez for any leadership role within any organization knowing that he would achieve immediate sustainable results and the organization would benefit for years to come.

Jack Gaige
William is one of the best Master Black Belts that I have have the privledge of working with. His knowlege of LSS and CPI is exceptional. He is a versed and talented facilitator and instructor and takes pride in mentoring and coaching other belts. He sees the big picture and always works towards continuous process improvement. He is a major player on my staff.

Michael Blair CLSSBB
Over the past two years I have had the pleasure of working together on numerous projects with Will Hernandez at the Air Forces Air Combat Command in Langley Virginia. His knowledge level of Organization Change Management and Statistical Analysis is second to none. He taught me something new with each and every project. He doesn't just facilitate meetings and projects. He is truly gifted in mentoring organizations in real sustainable organizational change. On numerous occasions I have seen him get results where others have failed. If I owned a company Will Hernandez would be one of the first people I would want on my team. I would recommend Will Hernandez for any leadership role within any organization knowing that he would achieve immediate sustainable results and the organization would benefit for years to come.

Credentials
-
Six Sigma Master Black Belt
-
Experience
-
NOVACES International Management Consulting Ltd Sti
-
Türkiye
-
Business Consulting and Services
-
1 - 100 Employee
-
Improvement Scientist / Contract Consultant
-
Oct 2017 - Present
Influencing organizational leadership to function cohesively in the execution of its mission and objectives through effective improvement methodologies Coordinated and provided process improvement training, coaching and project management and Operational Programs. Served as an advocate to identify actionable strategies to improve performance and drive key initiatives. Focused on the continual refinement of operational processes to achieve operational excellence. Influencing organizational leadership to function cohesively in the execution of its mission and objectives through effective improvement methodologies Coordinated and provided process improvement training, coaching and project management and Operational Programs. Served as an advocate to identify actionable strategies to improve performance and drive key initiatives. Focused on the continual refinement of operational processes to achieve operational excellence.
-
-
-
University of Virginia Health System
-
United States
-
Medical Practices
-
1 - 100 Employee
-
Sr. Profermance Improvement Coach
-
Aug 2015 - Oct 2017
Provided Sr. leadership (CEO, COO, CFO) guidance around Lean Transformation, Performance Improvement methodologies and approaches to include operational strategies Responsible for leading key organizational level performance improvements efforts impacting core business processes and critical patient care functions to include inpatient and clinical services Coach and mentor through project completion and performance sustainment Redesigned the Supply Chain Dept., encompassing an end-to-end flow of supplies, material information, supply demands, material storage and cost value analysis. Guide and influence system thinking in effort to drive ideal results through ideal behaviors
-
-
-
Adventist Health System
-
United States
-
Medical Practices
-
Corporate Director of Quality and Performance Improvement
-
Feb 2014 - Aug 2015
»Program Director of Lean Transformation for 45 Hospitals, Project Manager and facilitator of Lean and Six Sigma Methodologies to improve Healthcare Services and achieve noticeable results.»Technical expert in advanced statistical analysis, project management, program administration, training, project coaching and mentoring. »Identified High-leverage opportunities to apply lean six sigma techniques throughout our 44 hospital system »Mentored and facilitated hospital enterprise projects (Hospital Wide Patient Experience, ED throughput, Nurse Turnover, reduction in RN hiring process, first time quality in surgical cast cart picks, warehouse inventory flow and material replenishment)»Provided technical and business support to the overall deployment of continuous process improvement initiatives across the enterprise; aligning strategic goals and operational objectives in support of Service Excellence.
-
-
-
-
Regional Lean Six Sigma Master Black Belt / Contract Consultant
-
Sep 2012 - Feb 2014
»Navy East Regional Program Lead responsible for process improvement programs at all 18 healthcare facilities. »Driver of organizational change by developing corporate and regional high-performance work teams in effort to align priorities to organizational goals. »Work closely with Operational leadership to advance efficient and effective operational practices. »Evaluate Operational Excellence through Project Management, Project Execution and by conducting quarterly organizational performance evaluation reviews.
-
-
-
-
LSS Master Black Belt / Quality Control Engineer / Contract Consultant
-
May 2012 - Oct 2012
»Developed Six Sigma Belt Certification Programs (BB, GB and Champion) and Lean Master Instruction based on A3 thinking.»Lead Six Sigma activities, including program development, training activities, project leader development, and operational deployment»Responsible for facilitating key enterprise Kaizen Events, TOCs and JDIs on key selected supply chain issues (inventory reduction, standardization of routine consumables, real time material management and elimination of inventory contamination).
-
-
-
DSD Labs
-
United States
-
IT Services and IT Consulting
-
1 - 100 Employee
-
Sr. Business Consultant / Contract Consultant
-
Jan 2010 - Dec 2011
»Responsible for deployment, sustaining and creating an operational excellence service culture at ACC A9 HQ Commands (administrative processes, Supply Chain Material Standardization and readiness focus projects)»Provided senior level insight and senior level integration from a technical perspective, and strategic alignment of improvement projects. Customer liaison, culture transition, and interface relation for the program.»Provided program and project direction, including work plan development and execution, quality control management, timeline management, risk assessment and business case development.»Provided strategic continuous improvement deployment, facilitated the establishment of organizational goals and objectives, formulated performance metrics, and developed action plans tied to gap analysis.»Responsible for reengineering enterprise acquisitions and supply model to meet modern day combat requirements for Air Force. »Responsible for continuous improvement guidance and project management to healthcare facilities, operational readiness systems, and aircraft maintenance operations.»Mentored and trained Green Belt and Black Belts to ensure project completion, conduct EVSA, SA&D and 8 Step/A3, Value Stream Mapping, BPR, DMAIC Methodology and RIE approaches.
-
-
-
Blackwater USA
-
Security and Investigations
-
200 - 300 Employee
-
Corporate Director of QA & Process Improvement
-
Aug 2008 - Jan 2010
»Cultured and trained corporate leadership, staff and business members as to the quality management system and their supportive responsibilities. »Provided strategic planning, development, and implementation of activities in support of operations.»Obtained a company-wide organizational ISO quality management system and certification with all required policies and procedures in support of company quality objectives and regulatory compliance requirements. »Cultured and trained corporate leadership, staff and business members as to the quality management system and their supportive responsibilities. »Provided strategic planning, development, and implementation of activities in support of operations.»Obtained a company-wide organizational ISO quality management system and certification with all required policies and procedures in support of company quality objectives and regulatory compliance requirements.
-
-
-
Massimo Zanetti Beverage USA
-
United States
-
Food and Beverage Services
-
100 - 200 Employee
-
Sr. Manager of Continuous Improvement Deployment
-
Nov 2007 - Aug 2008
»Lead Lean Transformation program throughout the coffee manufacture sector previously know as Sara Lee Corp. »Developed a formal monthly S&OP management review process while identifying the key process indicators of functional areas that focused on company goals. »Lead the innovation & development team into new products while designing new processes to meet new ventures. »Reduced manufacturing cost through LEAN manufacturing principles realizing an increase in productivity, efficiency and waste elimination.
-
-
-
Northrop Grumman Systems Corporation
-
United States
-
1 - 100 Employee
-
Supply Chain Process Improvement Quality Engineer
-
Aug 1999 - Nov 2007
»Responsible for trouble shooting production performance issues with assembly operations. Worked collaboratively with operations, plant engineering and quality assurance personnel in the continuous improvement of manufacturing excellence.»Monitored and managed various service value streams to properly support business capacity while keeping overall operating costs within budget guidelines»Constantly monitored manufacturing trends and resource alignment to meet evolving demands. »Persistently developing processes improvement operational results through Configuration Management, Product Quality Assurance, Measurement and Analysis, Project Monitoring and Control, Project Planning and Development, Verification, Validation and Organizational Training.»Coached, training and mentored Yellow, Green, Champions and Black Belts through certification through Lean principles, DFSS, DOE, SPC and DMAIC methodology
-
-
-
Northrop Grumman Corporation
-
United States
-
1 - 100 Employee
-
Sr. Supplier Quality & Suppy Chain Engineer
-
Aug 1999 - Nov 2007
» Responsible for ensuring Supplier Quality Compliance and regulatory requirements.» Responsible for the Supply Chain system, process audits and associated corrective actions. » Perform Line Control assessments, and oversee quality engineering test and RMA functions» Managed new and overhaul construction material flow to meet construction deadlines. » Analyze production assignments to ensure the corporation maximizes productivity and profits.» Developing and initiating systems that allowed warehouse management to estimate average daily staging space requirements, manpower and overtime requirements and determine needs for contingency planning. » Provide supplier quality management throughout the Supply Chain commodities (Steel, pipe and fittings, electrical and complex machinery). » Develop and appropriated annual budgets for various construction programs, direct and indirect contracts.
-
-
-
US Navy
-
United States
-
Armed Forces
-
700 & Above Employee
-
Hospital Corpsman - Naval Special Operations
-
Sep 1985 - Sep 1993
Special Operations and Medical Trauma Support. Special Operations and Medical Trauma Support.
-
-
Education
-
Trident University International
(PhD) Business Administration, 1st year Candidate, Organizational Leadership -
Troy University
MBA, Master of Business Administration -
Columbia College
BS, Operations & Finance
Community
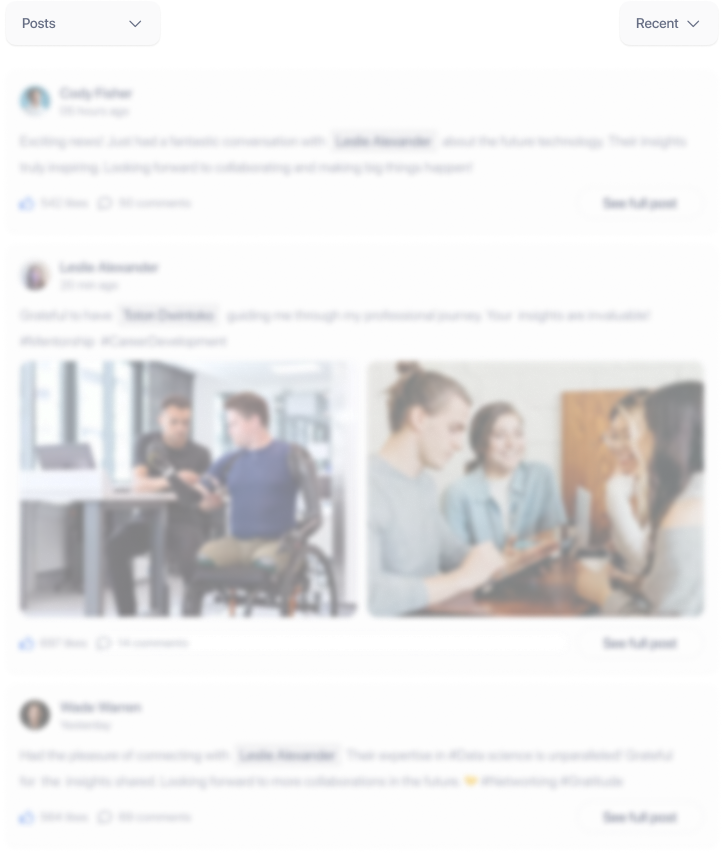