William Bailey
Compliance and Quality Manager at Brickell Men's Products- Claim this Profile
Click to upgrade to our gold package
for the full feature experience.
Topline Score
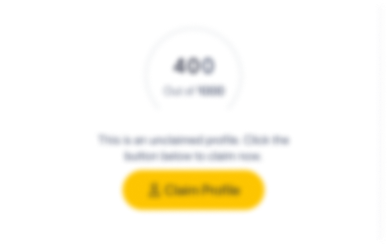
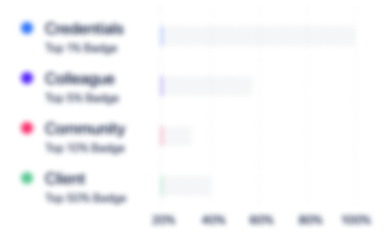
Bio


Experience
-
Brickell Men's Products
-
United States
-
Wellness and Fitness Services
-
1 - 100 Employee
-
Compliance and Quality Manager
-
Sep 2021 - Present
-
-
-
United States Post Office
-
Scarborough
-
Postal Support Employee
-
Nov 2019 - May 2022
-
-
-
-
Maintenance and Sanitation Manager
-
May 2016 - Nov 2019
-
-
Process Manager
-
May 2014 - May 2016
Managing all aspects of production in assigned area. Scheduling personnel, materials and equipment. Working with the other process manager, operations manager and other departments to optimize throughput, yield, quality, safety and food safety.
-
-
Quality Assurance Administrator
-
Jun 2011 - May 2014
Scheduled quality control technicians work. Assured that all paperwork was FDA and BRC compliant. Worked with the president, quality manager and plant manager to review and design processes and documentation to comply to all regulatory and third party audits. Responsible for equipment used to verify Critical Control Points (CCP) from the Hazard Analysis Critical Control Point (HACCP) plan including calibration of thermometers, scales and stop watches. Acted as document control coordinator.
-
-
-
University of Southern Maine
-
United States
-
Higher Education
-
700 & Above Employee
-
Student (Industrial Technology)
-
Jan 2010 - Jun 2011
-
-
-
AdvancePierre Foods
-
United States
-
Food Production
-
400 - 500 Employee
-
Business Systems Analyst
-
May 2006 - Jan 2010
-
-
Business System Analyst/ EDI Coordinator
-
Jan 2006 - Dec 2009
EDI Coordinator responsibilities (added 2008):Support and expand EDI system utilizing File Transfer Protocol (FTP), Applicability Statement 2 (AS2) and Value Added Network (VAN) communications, EDI document translation through Seeburger, and the interface with SAP modules, Integrated Asset Management(MP2), Database (Lotus Notes), and Manufacturing Execution System (MES). Monitor and resolve all data communication errors related to Seeburger. Reduced EDI VAN charges by 45% between January and August of 2009. Show less
-
-
Manufacturing Improvement Team Supervisor
-
Jan 2003 - Jan 2006
Managed a diverse team that encompassed clerks up to process analysts. The team was tasked with identifying, leading and measuring process improvement projects for manufacturing initiatives. Guided team in information system utilization, analysis and data integrity which included 1st tier help desk issues (hardware, software and data) and training.
-
-
Business Unit Project Lead
-
Jan 2001 - Jan 2003
Led projects collaborating with many departments to accomplish company goals using the DMAIC methodology. Acted as process owner on teams implementing the MES and Kronos systems at Barber Foods. Developed processes and trained all operations management, supervisors and operators on system process.
-
-
Production Supervisor
-
Jan 1994 - Jan 2001
Supervised a variety of groups throughout the manufacturing facility:Production Line Supervisor - Managed safety, throughput, staying within budget, reviewing schedules for efficiency, identifying and executing projects on a line of approximately 80 people.Meat Room Assistant Lead - Led and trained a team of 10 - 15 technicians/operators tasked with providing 100% of the supply of meat to up to 4 production lines. Collaborated with Plant Foreman to set priorities.Crew Lead - Directed a crew of 30 - 40 including conflict resolution, time and attendance, discipline, performance evaluations and job assignments. Prep Area Lead - Led a small crew of 4 - 6 technicians responsible for all stuffing production. Show less
-
-
Meat Room Technician
-
Jan 1991 - Jan 1994
-
-
Education
-
University of Southern Maine
BA in Industrial Technology, Industial Management -
Southern Maine Community College
Building Construction, College/University Preparatory and Advanced High School/Secondary Diploma Program
Community
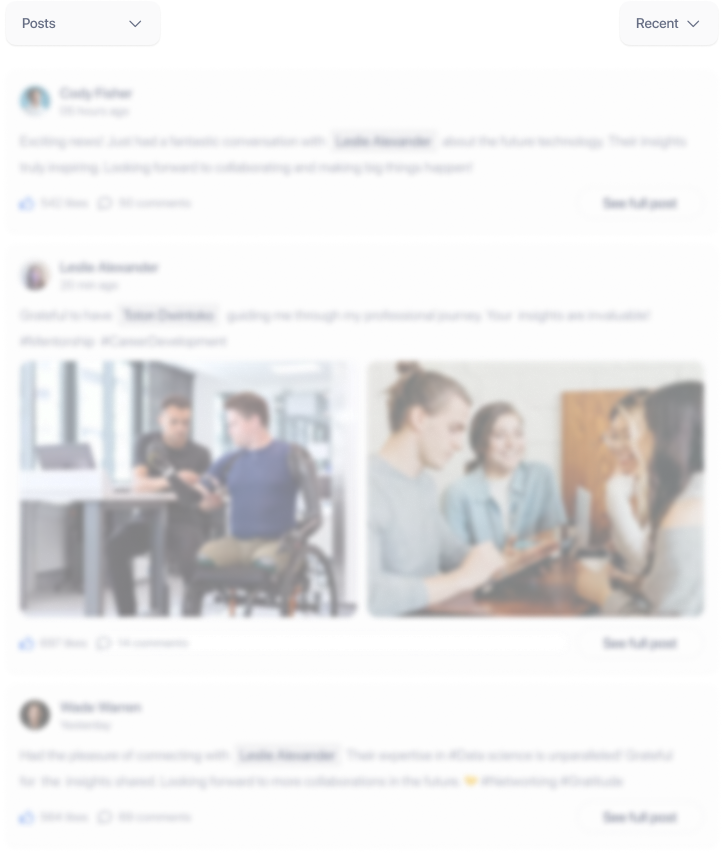