Wendy Walsh
Customer Support Specialist at Explorer Software Group- Claim this Profile
Click to upgrade to our gold package
for the full feature experience.
-
English -
Topline Score
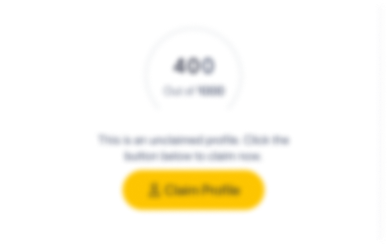
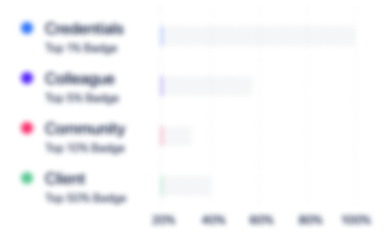
Bio


Credentials
-
Bits and Bytes of Computer Networking
CourseraJan, 2023- Nov, 2024 -
Technical Support Fundamentals
CourseraJan, 2023- Nov, 2024 -
Learning Data Analytics: 1 Foundations
LinkedInDec, 2022- Nov, 2024
Experience
-
Explorer Software Group
-
Canada
-
Software Development
-
1 - 100 Employee
-
Customer Support Specialist
-
Feb 2023 - Present
Construction Accounting Support Specialist Construction Accounting Support Specialist
-
-
-
Emcon Services Inc.
-
Canada
-
Construction
-
100 - 200 Employee
-
Lead Payroll Administrator
-
Dec 2018 - Feb 2023
Training new staff to process payroll & Set up work orders for payroll & billing. Billing AT work orders. Processing bi-weekly & special run payroll from timesheets for both Union (Collective Agreement) and non union employees, verifying hours with foreman. Balancing and verifying payroll is correct. Issuing Paystubs & Direct Deposit. Vacation tracking, Employee wage/position changes, setting up employee's and direct deposit details. Issuing ROE's Training new Payroll Admin and answering any payroll entry questions. Answering any payroll questions from Employee's.
-
-
-
County of Two Hills
-
Two Hills Alberta
-
County Clerk
-
Aug 2017 - Dec 2018
Front Desk, Answering Phones, Dispatching Graders & Gravel Trucks. Taking Gravel Orders. Preparing maps for Grader operators for Bus Routes & Construction Area's. First Call paperwork for construction. Front Desk, Answering Phones, Dispatching Graders & Gravel Trucks. Taking Gravel Orders. Preparing maps for Grader operators for Bus Routes & Construction Area's. First Call paperwork for construction.
-
-
-
Equans BeLux
-
Belgium
-
Mechanical Or Industrial Engineering
-
700 & Above Employee
-
Materials Coordinator
-
Oct 2015 - Aug 2016
- Determine material requirements for mod yard install and identify Ship loose material for project, upload to Cofely materials management system. - Requesting project material in Jovix from client's marshalling yard. - Setting up master document packages for mod yard crews. - Set up tool crib - Receiving material with tablet as well as on the server. - Issuing material for construction. - Preparing Agenda & Chairing Materials meetings, and taking minutes and distributing - Attending Progress / Materials and Construction meetings to ensure remain on schedule and report on any delays. - Set up warehouse locations for storage and tracking of material. - Developing and maintaining good working relationships with subcontractors to coordinate material receiving and issuing material to subcontractors. - Verifying and Tracking of OS&D's providing pictures etc for file. - Developing and maintaining good working relationship with Client to resolve material issues and OSD's. - Ensuring smooth functioning of warehouse, verifying loads coming in and out of yard. - Tracking material received at marshaling yard for completed mod material. -Advising construction on material status, and which mods up coming may have material issues. - Obtaining detail drawings from Client, getting quotes, obtaining approvals & requisitioning material for purchase. -Arranging pick up of empty material skids. -Coordinating loads leaving site, creating shipments and arranging transport. - Developing and maintaining good working relationship with other mod yards on project to coordinate shipping and delivery of materials delivered to wrong sites, borrowing materials to complete urgent requirements that material delivery has a long eta for delivery. -Associating RFID tags and creating shipments in Jovix for completed mods and ship loose items.
-
-
-
Tecnicas Reunidas
-
Spain
-
Engineering Services
-
700 & Above Employee
-
Materials Coordinator (Warehouse Assistant)
-
May 2015 - Sep 2015
- Performing inventory stocks check. - Providing Information on materials received for planner, attending weekly materials/planning meeting . - Coordinating with contractor on shipments coming to yard. - Uploading and Receiving materials in Marian System, update and tracking of all material in spreadsheets. - Vetting and updating contractors MTO (all diciplines) for accuracy for upload and receiving to Jovix, and Vetting of all materials to be received at contractors yard for accuracy and full Mod requirements . - Trouble shooting material shorts, coordinating with marshalling yard for full shipments getting materials required expidited. - Communicates product shortages required to fill orders to the Expiditer. - Verifying and Tracking of OS&D's providing pictures etc for file. - Researches and troubleshoots unpickable orders. - Provides ASN (Advanced Shipping Notice) and MIR's Material Issue Reports to Contractor. - Makes recommendations to the Marshalling yard and Warehouse Manager to maintain adequate stock throughout. - Ensuring smooth functioning of warehouse, verifying Loads coming in and out of Contractors yard. - Working with Contractor's workface planning and our engineering team to resolve discrepancies in MTO's and material being recieved.
-
-
-
KBR, Inc.
-
United States
-
IT Services and IT Consulting
-
700 & Above Employee
-
Materials Coordinator
-
Dec 2013 - May 2015
• Identify materials requirements MTO from ISO's and uploading into materials management system, determining if materials are field install or shiploose material. • Upload Awards of Client supplied material to receive. • Maintains and monitors the Material Management system & updating BOM revisions. • Maintains and promotes safety policies and procedures. • Maintains familiarity and knowledge prime contracts and ensure compliance with contractual requirements. • Maintains familiarity with the Client's AML to insure that material is procured from approved Vendors. • Processes, reviews, records, and issues Requests for Quotation, Purchase Orders and Change Orders in the material management system. • Maintains communication with Client/Vendors to accomplish on-time shipment of materials and equipment to meet project schedule requirements, as required. • Assists Technical Document Control in obtaining Vendor Data, develop and maintain MTR tracking system as needed. • Coordinates transportation requirements with the Logistics group. • Ensures OS&D’s handled in timely manner with vendor and or Client. • Responsible for field expediting and field purchasing orders. • Directs the Warehouse Supervisor, responsible for planning, controlling and managing the warehouse group to ensure that the correct quality and quantity of materials and equipment are properly received, stored, preserved, issued, and/or shipped. • Coordinate the identification and Shipping of Client supplied material shipments to site. • Working with Foreman/Project Managers to rectify shorts on material issued, advising if components are not being installed, initiating RFI's for materials not identified on ISO that are required for installation. • Identifying and follow-up on any Material RFI's and Site Query's , adjusting BOM in material management system. Identifying new materials for Extra Work Orders (EWO) and processing Request for Quotes and Purchases of materials.
-
-
-
ShawCor CSI Services
-
Edmonton, Canada Area
-
Contract Project Purchaser - Kinder Morgan Site
-
May 2013 - Dec 2013
• Issued PO’s for purchasing materials in IFS. Prepared quotes for sourcing. Communicate with vendor for pricing, ordering and resolving backorders. Scanning Purchase order Requests into IFS. • Receiving and verifying packing slip to order, entering received material into IFS. Scanning and attaching Packing slip into order on IFS. • On site contact for deliveries and consumable tracking and ordering. • Inventory tracking twice monthly. • Issued PO’s for purchasing materials in IFS. Prepared quotes for sourcing. Communicate with vendor for pricing, ordering and resolving backorders. Scanning Purchase order Requests into IFS. • Receiving and verifying packing slip to order, entering received material into IFS. Scanning and attaching Packing slip into order on IFS. • On site contact for deliveries and consumable tracking and ordering. • Inventory tracking twice monthly.
-
-
-
Pillar Resource Services
-
Edmonton, Alberta
-
Shipper/Receiver/Tool Crib
-
Jun 2012 - Mar 2013
• Issued PO’s for purchasing materials, safety equipment/consumables. Prepared quotes for sourcing. Verifying Receiving report to PO for any shortages or backorders and communicated with vendor to resolve shortages. • Prepared BOL’s (Bill of Lading) and any documentation required for outgoing shipments. • Developed and maintained an MTR tracking system for QC department. • On site IT contact for troubleshooting server & photocopier. • Received Materials coming to site, verify amounts, material grade and parts match the shipping documents. • Accurately sorted pull lists from ISO’s for specific jobs and released to fabrication. • Organization of warehouse. • Tool Crib attendant, issued tools to employees and identified outstanding tools on a weekly basis. Filled out damage reports for any tool damage, and arranged for repair, monitoring of consumables for reordering. • Provided training & support to new employees and junior workers.
-
-
-
Bradken Canada
-
Edmonton, Canada Area
-
Materials Coordinator
-
Dec 2011 - Jun 2012
• Received material, insuring the dimensions and amount are correct as per blueprints and Job. • Coordinated with Machine shop and subcontractors to facilitate shipments of materials to and from shops in a timely manor. • Tracked progress of fabrication in Vantage. • Attended production meetings to report any delays in materials, and ascertain machine shop schedules and delays. • Issuing materials to job from inventory in Vantage and closing out all completed stock jobs • Received material, insuring the dimensions and amount are correct as per blueprints and Job. • Coordinated with Machine shop and subcontractors to facilitate shipments of materials to and from shops in a timely manor. • Tracked progress of fabrication in Vantage. • Attended production meetings to report any delays in materials, and ascertain machine shop schedules and delays. • Issuing materials to job from inventory in Vantage and closing out all completed stock jobs
-
-
-
Pillar Resource Services
-
Edmonton
-
Contract Billing/Time Keeper Cenovus Mod Yard
-
Dec 2010 - Dec 2011
• Accurate entry of time sensitive billing hours into database for payroll and client billing. • Daily billing client for man hours and equipment hours per job. • Attach new employees to the computerized pay system and update any changes into database. • Monitoring of Company paid training and agreements. • Completing the daily muster, volunteered to be muster warden. • Monitoring of all safety certifications and renewal dates, helping out with and hosting orientation & safety meetings as required. • Completing and tracking RFI’s. • Tracking of time and costs for approved RFI’s • Bi-weekly reporting of time and cost per job to client. • Bi-weekly meeting minutes updates. • Working in Microsoft Project (entry level). • On site IT contact for troubleshooting server & photocopier as well as install software for printers. • Provided training & support to new employees and junior workers.
-
-
-
URS Flint (now part of URS Corporation)
-
Oil and Gas
-
700 & Above Employee
-
Pipefitter/Time Keeper/JR Planning
-
Jun 2007 - Oct 2008
• Accurately entered employee timesheets (3 shops) into excel spreadsheet for payroll reporting. • Provided training & support to new administrators. • Identified oversights in the green hand program and offered support to the safety department and foreman to improve the efficiency of the program. • Entered Weld and Fitter completed dates into database. • Coordinate drawing packages and materials for production & release for fabrication. • Reported to Project Managers and Superintendant any delays, and status of spools being fabricated and attended production meetings. • Receiving materials for jobs from warehouse and verifying all materials were received. • Spool checking for accurate measurement and orientation. • Forklift operator
-
-
Education
-
National Payroll Institute
Working toward PCP, Payroll Certification -
Northern Alberta Institute of Technology
1st & 2nd Year, Pipefitter -
HarryAinley Composite High School - Edmonton
High School Diploma
Community
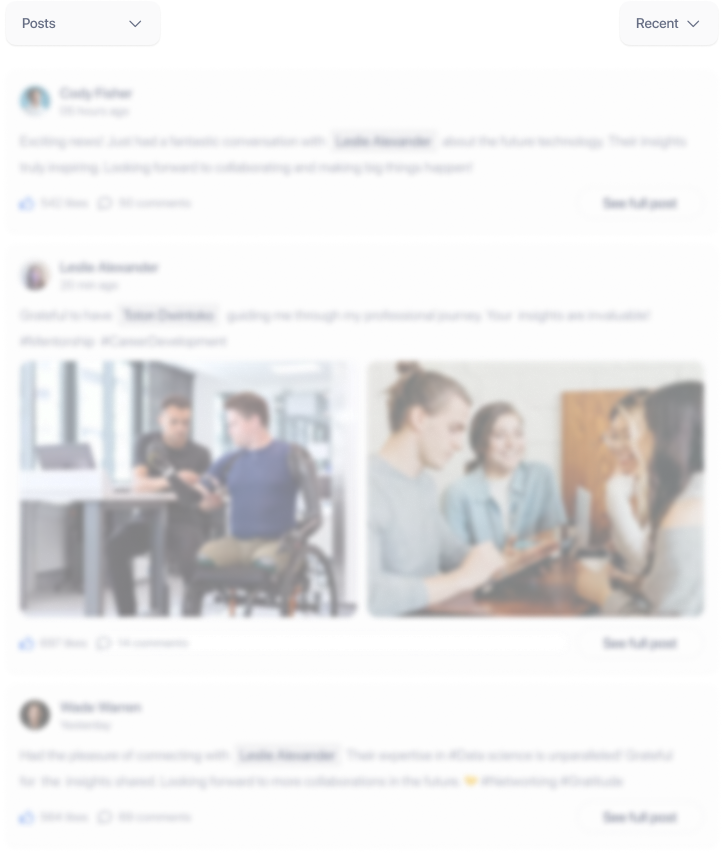