Wayne Weaver
Senior Manager Supply Chain at Cook MyoSite- Claim this Profile
Click to upgrade to our gold package
for the full feature experience.
Topline Score
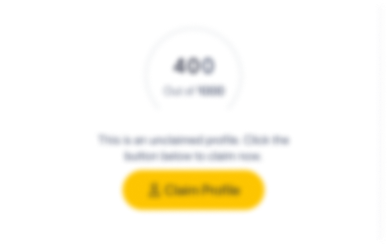
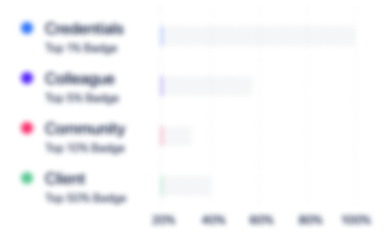
Bio


Credentials
-
Certified Supply Chain Professional (CSCP)
APICSOct, 2021- Oct, 2024
Experience
-
Cook MyoSite
-
United States
-
Biotechnology Research
-
100 - 200 Employee
-
Senior Manager Supply Chain
-
Nov 2021 - Present
-
-
-
Viatris
-
United States
-
Pharmaceutical Manufacturing
-
700 & Above Employee
-
Senior Manager, Supply Chain Planning
-
May 2019 - Oct 2021
Management of the site procurement, Recipe (BOM) creation, and materials management personnel. Oversight of API and IPI material purchases with a carrying inventory value exceeding $100M supporting production of ~ 3 billion doses annually. Led risk mitigation efforts in 2020 converting ~ $11M of at-risk raw materials through shelf life extensions, accelerated production planning, transfers to alternate sites, vendor returns/credits, and 3rd party sales. Support of site KPIs, yield & production standards, CAPA’s, and raw material related investigations. Attention on employee wellness during pandemic in remote work environment while providing continuous guidance and tools to promote personal success. Development and oversight of material expiry and purchase budgets. Developed program to proactively identify and systematically reduce outdates throughout each phase of production yielding a 50% + decrease YOY and maintaining compliance with ANDA provisions. Developed material management tool to monitor inter-stage material line items in SAP to align with actual in-house inventories resulting with properly closing out in-excess of 7000-line items. Generated analysis of equipment utilization by resource for all Mfg operations and supported capacity planning and labor requirement efforts for the site. Supported Mfg and Finance with cost containment and improvement initiatives. Shared Mfg knowledge base with procurement team and implemented a team toolbox to link key information utilized by all. Developed a dashboard serving as a critical tracking mechanism for the $100+ M of raw materials.
-
-
-
Mylan
-
United States
-
Pharmaceutical Manufacturing
-
700 & Above Employee
-
Senior Manager Manufacturing Operations
-
Apr 2017 - May 2019
Management of site Industrial Engineering Operations teamo Support Mfg Ops with continuous improvement initiatives and CAPA solutions.o Maintain production costing standards and product yields for 500+ SKUs across 7unit operationso Support Mfg Ops with cGMP through SOP’s, Work Instructions, Kaizen events, & data analysiso Collaborate with Finance on labor and material costing for new and existing productso Report out on site metrics, perform ROI’s for Capital Expenditures Developed an inventory reporting tool to monitor next inspection and expiration dates reducing losses and/or outdating of in-process materials. Supported ops management and planning with monthly production commitments and resource utilization. Supported site initiatives on improving production room cleaning and developing new production batch documents impacting product quality and improved accuracy (Right First Time). Supported site work force contract renewal analysis to include alternate shift configurations and contingency planning in the event of a work stoppage. Assisted with the development of restructured operational Product and Process teams. Coordinated tasks and timelines for HPLC Quality lab expansion.
-
-
Industrial Engineering Manager
-
Apr 2016 - Apr 2017
Developed a scheduling tool for intermediate raw material requirements reducing WIP from a 4-week supply to ~ 2 weeks while decreasing the admin time by ~7 hours per week. Optimized 114 product BOM’s resulting in ~ savings of $115k of reduced raw materials (in Yr 1) Provided technical support to the Imprinting operation with set-up and validation of equipment settings prior to processing new products and troubleshooting of issues with processing current products. Assisted with managing the Coating Department during a leadership transition working closely with planning to generate weekly schedules and achieving monthly commitments. (~500 MM doses/month) Developed awareness tool to track batches in WIP approaching production outdates (< 10 days). Performed justification and generated CAPEXs for an additional coating and vision inspection equipment. Developed department scheduling and dashboard tools to report daily expectations and key metrics. Supported 6S identification though department audits and implementation of improvement opportunities.
-
-
Industrial Engineer
-
Jan 2014 - Apr 2016
-
-
-
Eagle Systems
-
Morgantown WV
-
Deputy Program Manager
-
Apr 2010 - Dec 2013
Technical direction and management of 37 government contract personnel who validate inventory status of medical equipment and supplies maintained by Army units in the US and abroad. Manage Customer and business metrics, CPI’s, and cost reduction actions. Implemented Quality Management System for the contract to comply with ISO 9001-2008 criteria. Manage and approve expenditures associated with the contract. Review and approve documentation of project work performed prior to submission to US Army customer. Manage location expenses, identify and implement cost reduction improvements. Currently hold a Secret security clearance.
-
-
-
Nukote
-
Connellsville PA
-
Quality Assurance Manager -
-
Oct 2008 - Apr 2010
Management of QC laboratory functions to include print testing of all laser, copier and wide format toner products for compliance to customer specifications. Directed final disposition of all toner products for shipment. Managed maintenance and calibration of all QC test equipment. Maintained inventory of testing components. Managed SPC data for all WIP toner through all manufacturing and testing stages. Conducted analysis of processes out of control and/or customer specification. Facilitated team meetings to resolve product and Customer issues, which included involvement with vendors, R&D, and the sales team. Generated certificate of analysis documents and placed testing results on our customer accessible web site. Maintained database of product problems, CAPA, continuous improvements, and ISO 9001/14001 audits. Managed inventory levels of Customer purchased raw materials and the quality assurance of Customer product through audits of incoming material and in-house packaging. Developed access queries and reports to streamline collection and analysis of quality data. Coordinated production planning calls for our major customers. Determined material requirements based on actual and forecasted orders. Identified raw material lead times and assisted with scheduling the work orders through production and packaging.
-
-
-
Cintas
-
United States
-
Facilities Services
-
700 & Above Employee
-
Manager, Plant/General
-
Sep 2002 - Nov 2007
Managed 50+ production partners and plant operations for rental and direct sale business of garments and ancillary items amounting to $145K in weekly volume. Responsible for line item budgets, product line purchasing, and management of utilities.Directed transfer of $110K in weekly garment rental volume into the plant. Coordinated layout modifications, new equipment installation and start-up. Managed facility maintenance program to include boiler, wastewater treatment, auto chemical injection, washers/dryers, steam tunnel and pressing equipment, heat reclamation, and conveyance systems.Served as POC for OSHA inspections and as a member of the safety team. Managed operations and distribution of Sanis brand product line to rental locations in 19 states each week.Directed $1.2 M start-up of Distribution center entailing plant design, equipment purchases and installation, staffing, fleet logistics, product testing, vendor selection, and customer reviews. Maintained relationships with all product vendors which include annual pricing reviews, product quality, inventory requirements, and standardized ordering.Handled closure and decommissioning of 2 business locations and consolidated distribution entailing changes to the delivery fleet, routing plans, equipment, and staffing in order to provide service to 80 Cintas rental facilities.
-
-
Six Sigma BB / Engineer
-
Sep 2004 - Jun 2007
Responsible for corporate Black Belt projects, change management, implementing process improvement opportunities, and driving Six Sigma initiatives at the group level which achieved $1.3 million in FY07.Directed Executive Steering Committees (ESC’s), conducted Six Sigma Green Belt training for 100+ partners, mentored teams, and provided support for all Green Belt projects at the group level.Developed 6σ transactional process for automatic audits of customer invoices to identify errors in billing, generating a minimum of $850K annually across the rental division of the company.Conducted quarterly production efficiency audits for 7 processing facilities. Developed process to reduce average load time per route by 5.2 minutes by customizing load sheets based upon the layout of product storage areas: ~ $865K in annual labor reductions.Implemented an automated process to increase collection of finance charge revenue on past due customer invoices: ~ $450K annual cost improvement.
-
-
Education
-
West Virginia University
Bachelor of Science (BS), Industrial Engineering
Community
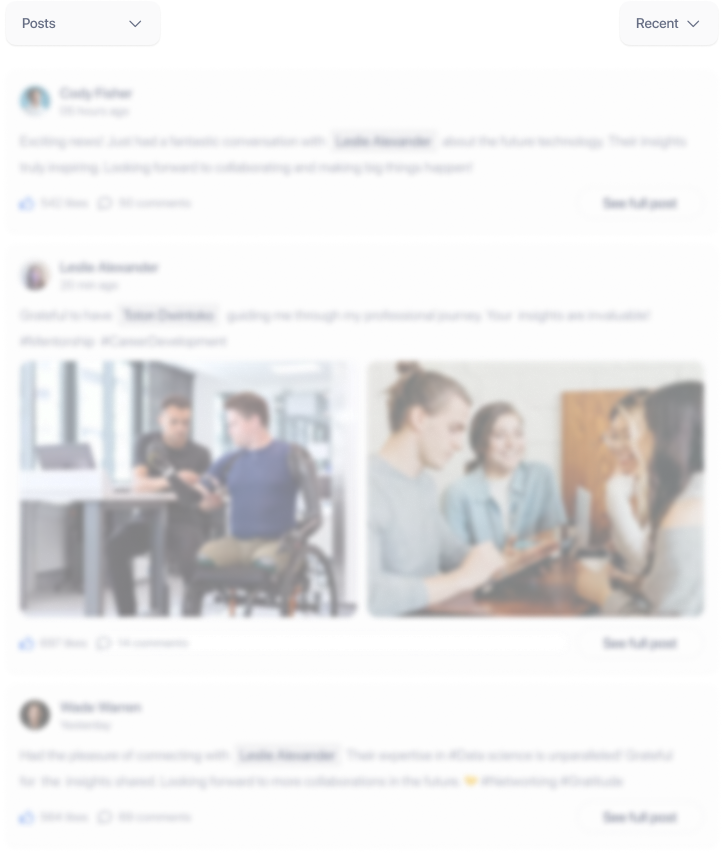