Wayne Buttery
Inventory Coordinator at CleanRiver Recycling Solutions- Claim this Profile
Click to upgrade to our gold package
for the full feature experience.
Topline Score
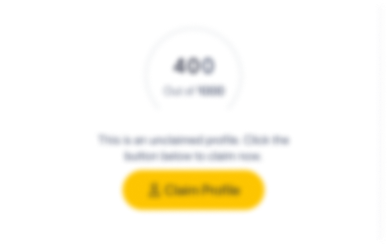
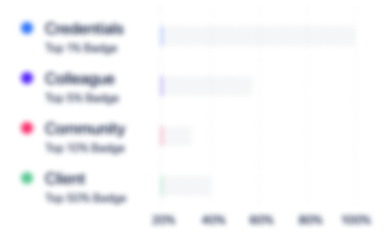
Bio

Cindy Speisman
Highly recommend Wayne. Wayne played an integral role in our healthcare business. Procuring and maintaining our demo inventory as well as supporting the sales team with on site demo equipment, often with little notice. No matter how impossible the task Wayne found a way to get it done. He also responded to urgent customer needs coordinating last minute requests. Wayne was always available. Always willing to help. Consistently went above expectations to deliver what was required. His attention to detail was critical to our inventory control. A great colleague.

James Sayegh
I have worked closely with Wayne for the past year, and highly recommended him. Wayne is an extremely diligent and hard worker, and is very process oriented. He understands his role and department better than most, and expects those he works with to share the same dedication to detail and perfection that he has. I would not hesitate to recommend Wayne, and would welcome him on the same team as me any time.

Cindy Speisman
Highly recommend Wayne. Wayne played an integral role in our healthcare business. Procuring and maintaining our demo inventory as well as supporting the sales team with on site demo equipment, often with little notice. No matter how impossible the task Wayne found a way to get it done. He also responded to urgent customer needs coordinating last minute requests. Wayne was always available. Always willing to help. Consistently went above expectations to deliver what was required. His attention to detail was critical to our inventory control. A great colleague.

James Sayegh
I have worked closely with Wayne for the past year, and highly recommended him. Wayne is an extremely diligent and hard worker, and is very process oriented. He understands his role and department better than most, and expects those he works with to share the same dedication to detail and perfection that he has. I would not hesitate to recommend Wayne, and would welcome him on the same team as me any time.

Cindy Speisman
Highly recommend Wayne. Wayne played an integral role in our healthcare business. Procuring and maintaining our demo inventory as well as supporting the sales team with on site demo equipment, often with little notice. No matter how impossible the task Wayne found a way to get it done. He also responded to urgent customer needs coordinating last minute requests. Wayne was always available. Always willing to help. Consistently went above expectations to deliver what was required. His attention to detail was critical to our inventory control. A great colleague.

James Sayegh
I have worked closely with Wayne for the past year, and highly recommended him. Wayne is an extremely diligent and hard worker, and is very process oriented. He understands his role and department better than most, and expects those he works with to share the same dedication to detail and perfection that he has. I would not hesitate to recommend Wayne, and would welcome him on the same team as me any time.

Cindy Speisman
Highly recommend Wayne. Wayne played an integral role in our healthcare business. Procuring and maintaining our demo inventory as well as supporting the sales team with on site demo equipment, often with little notice. No matter how impossible the task Wayne found a way to get it done. He also responded to urgent customer needs coordinating last minute requests. Wayne was always available. Always willing to help. Consistently went above expectations to deliver what was required. His attention to detail was critical to our inventory control. A great colleague.

James Sayegh
I have worked closely with Wayne for the past year, and highly recommended him. Wayne is an extremely diligent and hard worker, and is very process oriented. He understands his role and department better than most, and expects those he works with to share the same dedication to detail and perfection that he has. I would not hesitate to recommend Wayne, and would welcome him on the same team as me any time.

Experience
-
CleanRiver Recycling Solutions
-
Canada
-
Manufacturing
-
1 - 100 Employee
-
Inventory Coordinator
-
Feb 2023 - Present
-
-
-
Philips
-
Netherlands
-
Hospitals and Health Care
-
700 & Above Employee
-
Sales and Operations Inventory Planner
-
May 2010 - Jan 2023
-
-
-
Philips
-
Netherlands
-
Hospitals and Health Care
-
700 & Above Employee
-
Inventory & Logistics Coordinator
-
Jan 2008 - Aug 2009
•Achieved $500K of transportation savings in 2008 by reorganizing the allocation/deployment of Ultrasound demonstration systems and by building relationships with the 3PL. •Reduced 2009 warehouse charges by a projected savings of $35K through hands-on analysis and disposition of installation returns. •Identified $900K of non existing stock within SAP, worked with management and finance to remove from the general ledger and implemented a reorganization of all demonstration equipment inventories. •Directed the reassignment of approximately $800K of stock into demonstration systems to avoid the purchase of replacement inventory. •Attained Zero stock loss (total inventory of $6.6M) in the 2009 annual physical inventory through the development and implementation of various process improvements. •Initiated and completed a project on time and under budget to refurbish/replace all demonstration shipping crates with no disruption to the sales team schedule. Show less
-
-
-
Momentive
-
United States
-
Chemical Manufacturing
-
700 & Above Employee
-
Production Coordinator (Contract Position)
-
May 2007 - Jan 2008
•Utilized SAP to issue production orders, perform weekly cycle counts, and coordinate timely product releases with the Quality department. •Coordinated carrier pick ups and prepared shipping/customs paperwork for all deliveries to Canada and the U.S. •Conducted monthly Environmental Health and Safety audits and entered, tracked and verified completion of corrective action to ensure a safe work environment. •Utilized SAP to issue production orders, perform weekly cycle counts, and coordinate timely product releases with the Quality department. •Coordinated carrier pick ups and prepared shipping/customs paperwork for all deliveries to Canada and the U.S. •Conducted monthly Environmental Health and Safety audits and entered, tracked and verified completion of corrective action to ensure a safe work environment.
-
-
-
-
Inventory Control Manager
-
May 1997 - Apr 2006
•Recruited to improve the effectiveness of both the planning team and MRP systems. •Supervised the day-to-day activities of 4 direct (2 Warehouse Supervisors and 2 Inventory Planning Coordinators) and 48 indirect (8 Inventory Planners and 40 Warehouse Associates in 3 plants). •Developed and managed an operating budget exceeding $2.3M. •Reduced component inventory (30K SKUs) by $5M a 70% reduction over a 3-year period through the implementation of new management concepts such as eliminating safety stocks and minimizing fixed ordering quantities. •Developed and introduced a weekly report to track inventory on a SKU by SKU basis which facilitated “real-time” decision making and assisted to reduce high cost stock. •Prepared and led the team through the implementation of J.D. Edwards management software resulting in a smooth transition. •Participated on a cross-functional management team which successfully planned and executed the consolidation of 2 manufacturing plants to 1 plant with no disruption to delivery schedules. •Coached, trained and mentored associates to improve effectiveness and ensure compliance to all internal/external policies and procedures i.e. the use of Personal Protective Equipment (PPE) as required by the Occupational Health and Safety Act. Show less
-
-
-
-
Supervisor–Production Planning &Distribution
-
Jan 1996 - May 1997
•Supervised 1 Production Planner and 4 Warehouse Associates. •Initiated a warehouse reorganization that included the implementation of a Push Back racking system and purchase of a new reach truck. •Managed the implementation of SAP Materials Management modules, project was completed in 4 months and launched on time. This project was only the third such installation of SAP in North America. •Analyzed, generated and presented the monthly Sales and Operations Planning reports to the management team. •Planned the delivery of bulk tablets from France, Netherlands, and Germany as well as finished goods and packaging components from Canadian and American vendors. •Managed the implementation of all packaging and label artwork that was made necessary by a corporate name change and coordinated the approvals and final submission for production. Show less
-
-
-
-
Inventory Control Manager
-
Jan 1988 - Jan 1996
BAYER Inc •Created an innovative inventory management system using MAPICS software. •Merged Miles (80 SKUs) and Sterling (110 SKUs) into one integrated product group. •Worked closely with vendors to build strong relationships which reduced backorder from 20 products to zero. •Reduced inventory from 123 days coverage to 66 days against a budget allowance of 89 days resulting in the best year-end performance of all 7 Bayer divisions. •Planned the delivery of finished goods from Germany, Ireland, United States and Canada. Sterling Health •Managed all aspects of the OTC finished goods inventory and supervised the Sales Forecast Analyst. •Approved the functionality and participated as a key member of the taskforce that introduced the new PC-based SDC inventory and purchasing software. •Designed inventory management reports that helped reduced total inventory by 40% resulting in inventory turns increasing from 4.2 to 8.9 in less than one year and achieved zero back orders for a 2 week period. •Created, implemented and managed a Vendor Performance analysis process to 8 source plants in Europe and North America significantly improving communication and on time delivery. •Contributed as a member of the Priority Projects Committee that successfully launched over 60 new SKUs in a 4 year period. •Planned all OTC bridging inventories used to satisfy demand while the Sterling Drug facility was being shut down and new source plants were being set up. •Received the Achievers Award in 1991 for creative problem solving excellence. Sterling Drug •Responsible for the Master Scheduling and Production Planning of finished goods as well as the purchasing of packaging materials for OTC division’s three major brands: Aspirin, Gaviscon, and Midol. •Initiated an inventory clean up resulting in over $500,000 of dead stock being put back into production or destroyed. •Provided planning support to the $12 million Actiprofen new product launch. Show less
-
-
Education
-
Fleming College
Diploma (3 year), Business Administration / Materials Management -
Crestwood Secondary School
Diploma
Community
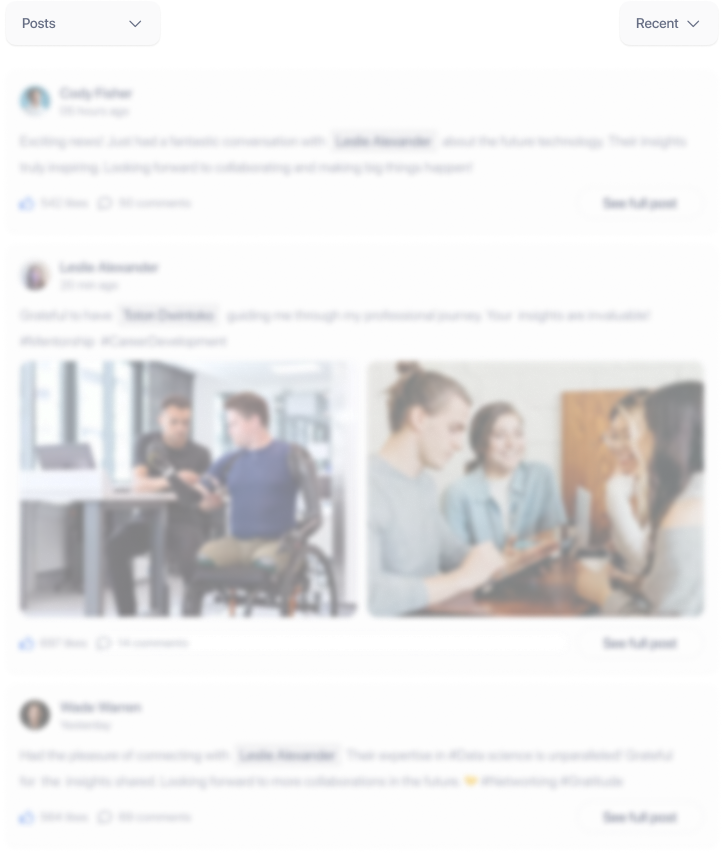