W.Trapper Kurpe
Reliability PM Program Manager at Port Authority of Allegheny County- Claim this Profile
Click to upgrade to our gold package
for the full feature experience.
Topline Score
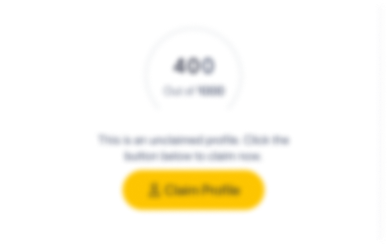
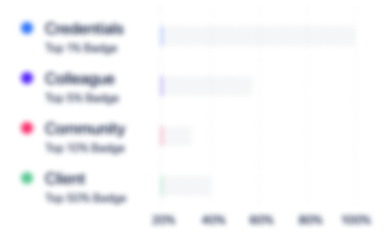
Bio


Credentials
-
Level 1 Infrared Thermography
Infraspection InstituteMar, 2009- Nov, 2024
Experience
-
Port Authority of Allegheny County
-
United States
-
Transportation/Trucking/Railroad
-
400 - 500 Employee
-
Reliability PM Program Manager
-
Dec 2016 - Present
• Recognizes and identify the need for the development of new Preventive and Predictive maintenance procedures. • Help implement and oversee new asset management through the Trapeze EAM and Fiix work order systems. • Coordinate the transfer of date from the old work order system to EAM Trapeze system. • Audit Preventive maintenance processes. • Work with Authority and vendor personnel to identify any operational related issues dealing with the EAM system. • Document and maintain asset historical records and prepare statistical and ad-hoc reports. • Provided end user training in the use of the EAM system functionality. • Help lead in the development of new maintenances or operational procedures. • Work with state oversight to insures maintenances process is being performed according to the new mandate (State Of Good Repair).
-
-
-
Rexnord Corporation
-
United States
-
Industrial Machinery Manufacturing
-
100 - 200 Employee
-
Maintenance/ Reliability Manager
-
Jan 2016 - Jan 2017
• Worked closely with environmental and safety to help resolve issues and insure a safe work place • Developed a TPM Program and implemented Preventative and Predictive maintenance. • Establish and setup a new work order systems using Maintenance connect CMMS platform. • Helped develop and lead Kaizens events monthly. • Established machine monitoring to help better utilize a small maintenance work force. • Performed 3P meeting with management and help lead lean manufacturing of the facilities. • Analyze facility and equipment date to ensure proper planning. • The writing of (RCFA) Root cause failure analysis for down equipment when repairs are outside of normal Maintenances or large impact to operations. • Source and negotiate quotes from vendor and outsourced contractors. • Oversee all Maintenances actives, equipment moves and projects for multiple locations.
-
-
-
ATI
-
United States
-
Aviation and Aerospace Component Manufacturing
-
700 & Above Employee
-
Maintenance Manager
-
May 2010 - Jan 2016
• Oversee the Operation and Maintenance of the facilities water treatment plant. • Analyze Mill equipment date to ensure proper planning through the use of Maximo IBM maintenance management software • Plane and set yearly maintenances work for large projects and outages. • Plan, Organize and provide supervision and oversight to maintenance tech’s and turn supervisors. • Source and negotiate quotes from vendor and outsourced contractors. • Inspect and monitor all maintenance actions performed by maintenance employees or outsourced contractors to verify completion of work within expected guidelines. • Direct and manage internal machine retrofit and electrical systems upgrade. • Developed and implemented preventative maintenance programs. • Train maintenance employees in preventative and Predictive maintenance and good housekeeping procedures 6S. • Oversee transportation department maintenance and operations. • Conduct daily safety and maintenance meeting and review near misses.
-
-
-
SKF Group
-
Sweden
-
Industrial Machinery Manufacturing
-
700 & Above Employee
-
Vibration/Reliability Tech
-
Jun 2008 - May 2010
• Install of Vibration monitoring equipment • Mechanical testing of rotating equipment by the us of Vibration, Thermograph, Ultrasound testing technologies. • Participate in the final check-out of new installations and repairs of equipment. • Participate in the writing of (RCFA) - Root cause failure analysis and (FMEA) – Failure modes and effects analysis along with (FTA) – fault tree analysis. • Install of Vibration monitoring equipment • Mechanical testing of rotating equipment by the us of Vibration, Thermograph, Ultrasound testing technologies. • Participate in the final check-out of new installations and repairs of equipment. • Participate in the writing of (RCFA) - Root cause failure analysis and (FMEA) – Failure modes and effects analysis along with (FTA) – fault tree analysis.
-
-
-
Glenshaw Glass
-
Greater Pittsburgh Area
-
Electrical/Mechanical Tech
-
Apr 2005 - Jun 2008
• Maintaining of electrical and mechanical systems. • Maintaining of automated controls and PLC programming. • Repair and troubleshooting of motors, pumps, compressors, conveyor systems and HVAC equipment. • Installation of new machinery and retrofits of existing equipment. • Preventive and predictive check of equipment to ensure proper operation of the equipment. • Maintaining of electrical and mechanical systems. • Maintaining of automated controls and PLC programming. • Repair and troubleshooting of motors, pumps, compressors, conveyor systems and HVAC equipment. • Installation of new machinery and retrofits of existing equipment. • Preventive and predictive check of equipment to ensure proper operation of the equipment.
-
-
Education
-
Triangle Tech
Associate’s Degree, electrical Maintenance
Community
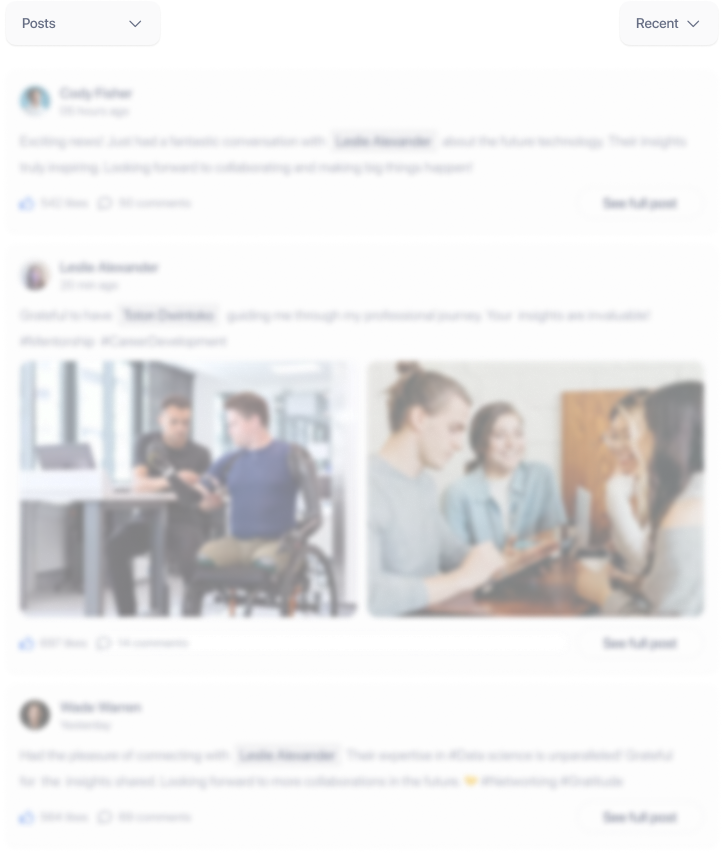