W. Edward Peterson
Manager of Quality Control and R&D; Welding Engineer at Laser Welding Solutions, LLC- Claim this Profile
Click to upgrade to our gold package
for the full feature experience.
Topline Score
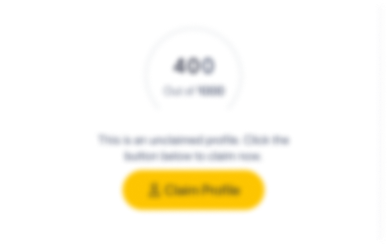
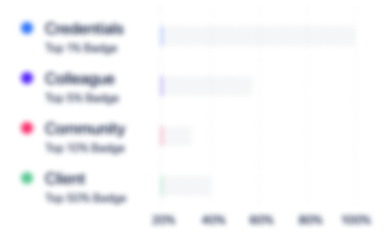
Bio


Credentials
-
Certified SolidWorks Associate
Dassault SystèmesMay, 2015- Nov, 2024 -
Certified Welding Inspector (CWI)
American Welding SocietyFeb, 2019- Nov, 2024
Experience
-
Laser Welding Solutions, LLC
-
United States
-
Oil and Gas
-
1 - 100 Employee
-
Manager of Quality Control and R&D; Welding Engineer
-
Jul 2018 - Present
WELDING ENGINEERING and R&D - Maintain qualified welders and welding procedures. - Qualify new welding procedures including specific customer approval as required. - Work with customers using laser cladding, laser welding, and GTAW welding to develop a solution meeting their unique requirement. - Provide technical review of requirements and capabilities for quoting new parts. MANAGER OF QUALITY CONTROL - Maintain Laser Welding Solutions' ISO 9001 certification and records. - Maintain approved suppliers and vendors; perform new qualifications, audits, and performance reviews. - Investigate quality non-conformances to identify the root cause(s) and prevent recurrences. - Create CARs, assign actions, and follow up as required to address internally or externally identified issues.
-
-
-
TechnipFMC
-
United Kingdom
-
Oil and Gas
-
700 & Above Employee
-
Rotational Welding Engineer
-
Aug 2016 - Jun 2018
SUPPLIER QUALITY ROTATION Worked with and developed suppliers to ensure quality products were delivered to TechnipFMC. Partnered with suppliers to identify the root causes of non-conformances and support the implementation of corrective actions. Preventative actions included process audits and APQP*. Cleared backlog of supplier documents never submitted for internal review; developed and implemented a new system to prevent the issue from reoccurring. WELD LAB R&D ROTATION Oversaw, data logged, and documented the welding of two experimental test coupons. Assisted with the daily operation of the global welding R&D lab. Projects utilized processes including machine GMAW-CMT, machine Hot-wire GTAW, manual GTAW, narrow groove GTAW, SAW, Induction Pre-heat, and Furnace PWHT. SHOP ROTATION Hands-on work in the shop assisting technicians with assembly and testing which gave me a better understanding of subsea products and the assembly process. Worked directly with NDE, pressure testing, and assembly. WELD SHOP ENGINEERING ROTATION Assisted in setting up a new internal weld shop. Involved in qualifying welding procedures to API6A, ASME Section IX, NACE MR0175, and customer requirements; lead development of localized PWHT procedures; assisted with shop work instructions and production documentation.
-
-
-
LeTourneau University
-
United States
-
Higher Education
-
500 - 600 Employee
-
Supplemental Instructor
-
Aug 2013 - May 2016
Provide weekly review sessions for students taking historically difficult courses. Have SI'ed for General Chemistry 1, General Physics 1, University Physics 1, and University Physics 2. Provide weekly review sessions for students taking historically difficult courses. Have SI'ed for General Chemistry 1, General Physics 1, University Physics 1, and University Physics 2.
-
-
-
FMC Technologies
-
Oil and Gas
-
700 & Above Employee
-
Welding Engineering Intern
-
Jun 2015 - Aug 2015
Welding Engineering Intern in Western Region Materials and Weld Engineering. Involved in development of PQRs and WPSs; reviewed WPSs for compliance with ASME Section IX and NACE MR0175/ISO15614; created testing instruction for qualification of new forging. Welding Engineering Intern in Western Region Materials and Weld Engineering. Involved in development of PQRs and WPSs; reviewed WPSs for compliance with ASME Section IX and NACE MR0175/ISO15614; created testing instruction for qualification of new forging.
-
-
-
FMC Technologies
-
Oil and Gas
-
700 & Above Employee
-
Welding Engineering Intern
-
May 2014 - Aug 2014
Welding Engineering Intern in Global Materials and Welding. Gap analysis on current versus final draft of new ISO 15615-1; Gap analysis on internal specifications; Documentation of welds for new PQRs; Assisted with mini DOE on forgings. Welding Engineering Intern in Global Materials and Welding. Gap analysis on current versus final draft of new ISO 15615-1; Gap analysis on internal specifications; Documentation of welds for new PQRs; Assisted with mini DOE on forgings.
-
-
Education
-
LeTourneau University
Bachelor of Science in Engineering, Materials Joining Concentration (Welding Engineering) -
Homeschooled
High School Diploma
Community
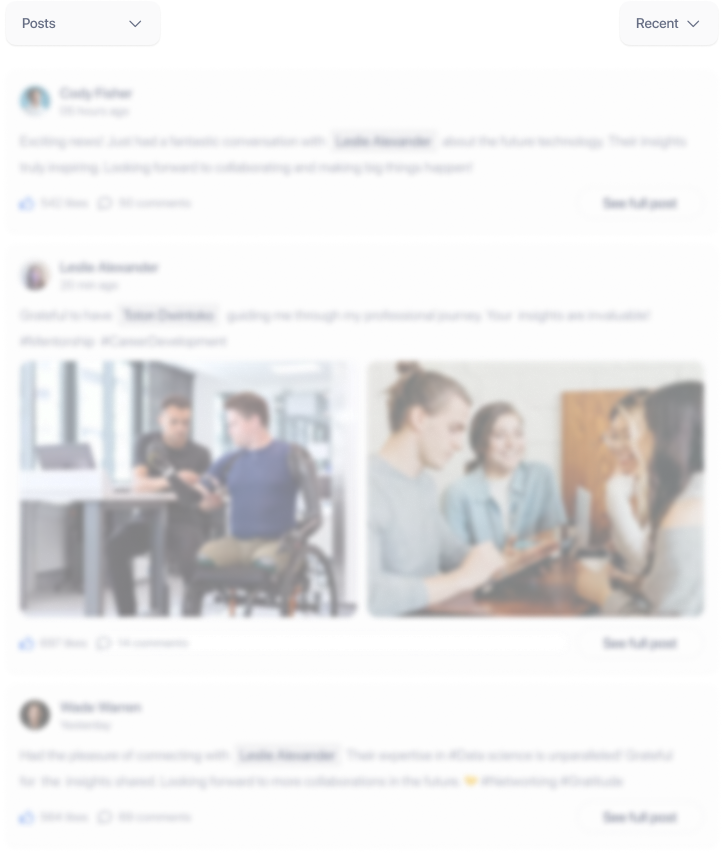