Vladimir Selgrad
Chief Executive Officer at Optimo-logistika- Claim this Profile
Click to upgrade to our gold package
for the full feature experience.
-
English Full professional proficiency
-
Bosnian Native or bilingual proficiency
-
Croatian Native or bilingual proficiency
-
Serbian Native or bilingual proficiency
Topline Score
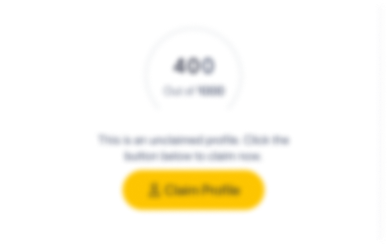
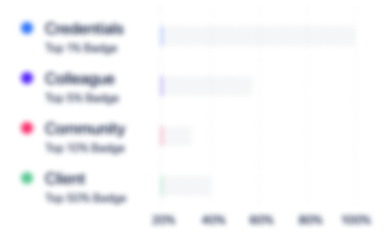
Bio

LinkedIn User
I was very lucky to join Vladimir's team and work with him in Alca trgovina. He is very professional, supportive and collaborative person, highly capable to always find solution for challenging projects and situations. He is a person that can be fully trusted. His professionalism and above all great personality contributed very much to my professional development in Alca trgovina.

LinkedIn User
I was very lucky to join Vladimir's team and work with him in Alca trgovina. He is very professional, supportive and collaborative person, highly capable to always find solution for challenging projects and situations. He is a person that can be fully trusted. His professionalism and above all great personality contributed very much to my professional development in Alca trgovina.

LinkedIn User
I was very lucky to join Vladimir's team and work with him in Alca trgovina. He is very professional, supportive and collaborative person, highly capable to always find solution for challenging projects and situations. He is a person that can be fully trusted. His professionalism and above all great personality contributed very much to my professional development in Alca trgovina.

LinkedIn User
I was very lucky to join Vladimir's team and work with him in Alca trgovina. He is very professional, supportive and collaborative person, highly capable to always find solution for challenging projects and situations. He is a person that can be fully trusted. His professionalism and above all great personality contributed very much to my professional development in Alca trgovina.

Experience
-
Optimo-logistika
-
Serbia
-
Truck Transportation
-
Chief Executive Officer
-
Mar 2019 - Present
-
-
-
-
Supply Chain Manager
-
Sep 2019 - Mar 2020
-
-
-
KIT Commerce
-
Serbia
-
Motor Vehicle Manufacturing
-
1 - 100 Employee
-
Supply Chain Manager
-
Nov 2017 - Oct 2018
Kit Commerce is leader in automotive industry of spare parts with more than 300 different brands and more than 130k SKU's. Main achievements: + Responsible for driving end-to-end supply chain performance and developing high performing team+ Cross-functional agenda+ Successful implementation of WMS Gold stock in less than 6 months.+ Setting up the sustainable system with focus on full transparency + Introduction of KPI's in supply chain as well as bonus system+ Increasing productivity in warehouse by 40% and implementing 5S standard + Reduction of stock by 100% in retail storesLeader of team consisting of 130 employees (5 direct reports).
-
-
-
Alca trgovina d.o.o.
-
Serbia
-
Consumer Goods
-
1 - 100 Employee
-
Director of Logistics
-
Aug 2016 - Nov 2017
Main achievements: + Responsible for driving end-to-end logistics performance and developing high performing team + Cross-functional improvements in customer service & customer collaboration, logistics operational excellence, S&OP, sourcing, and sell-out & peak shaving+ Introduced KPIs in each department+ Increased total logistics productivity by 34%+ Decreased OOS by 50%+ High performing team consisting of 200 employees (10 direct reports)Responsibilities: 1. Customer Service+ Managing relationships with Customers+ Maintaining and improving main performance indicators such as: PCO, PfR, OT deliveries, Average Resolution Time, Response Time by First Reply, Customer Satisfaction Score, First Contact Resolution, % of signed and stamp delivery notes, etc+ Managing Import-export activities 2. Distribution, 70% own fleet and 30% outsource+ Budgeting/transportation planning+ Closing the gap with fluctuation of truck drivers resulting in the outsource fleet reduction by 50%+ Maintaining and improving major performance indicators such as: Truck utilisation, % of ousource fleet, Fuel consuption per 100km, Transport cost, etc+ Involvement in tendering which decreases transportation costs (outsource) by 10%3. Warehouse operations in two distribution centers, two X-dock and 3 warehouses+ Safety + Restore basic conditions of WMS + Stock counting/management + Write offs+ Freshness/FEFO+ Change of warehouse layout gives us opportunity to enhance capacity by 20% and to decrease various losses
-
-
-
-
Logistics Manager
-
Nov 2013 - Mar 2016
Main achievements: • Established new logistics organizational structure • Redesigned logistics organization helped us to do revision of the current processes- process mapping done by using Kaizen/ Lean and changed management methodology, new standards set up with focus on loss reduction• Introduced daily, weekly and monthly performance indicators across the board which supported control of the processes and led to improvement in the overall business achievements• The youngest team member in blue print creation of World Class Logistics organization in Heineken worldwide. As result of it, chosen to be the leader of E2E process implementation in Serbia• Leader of team consisting of 100 employees (5 direct reports)• Responsible for people development and creation of rewarding work environment through coaching, regular 1:1 meeting, bonus system, etc. with emphasis on empowering people to be independent decision makers• Logistics cost control/planningResponsibilities:1. Supply Chain Planning and S&OP Process• Improved production/brewery performance 2. Customer Service• Managed relationship with Customers (Coca Cola, K.A., distributors)• Improved customer satisfaction by 10% through customer survey• Maintained and improved main performance indicators such as: PCO, CFR, OT deliveries • Import-export activities • Logistics Trade Terms 3. Primary Distribution• Maintaining and improving main performance indicators such as: One Way Routes, Truck utilization, Outbound transport cost, etc.• Involvement in tendering which cut down on transportation service cost• Managing relationship with 30 suppliers through performance measurement and monthly meetings4. Logistics operation in two breweries–Warehouses• 5S• Stock counting• RPM management• Safety• Write offs• Freshness/FEFO• Changed warehouse layout provided us with opportunity to enhance capacity by 30%• Experienced and knowledgeable of TPM (Kaizen/Lean) with more than 30 projects
-
-
Supply Chain Planning and S&OP Manager
-
Feb 2008 - Nov 2013
Main achievements: • Built up planning process and implemented new standards in two production locations• Leader of S&OP process implementation when TOP 3 result on audit was achieved• Improved cash flow results with reduction of stock for various materials and increased forecast accuracy by 15%.Responsibilities:• Total supply chain planning processes (demand and supply planning) in two production locations (beer breweries)• Leading Monthly S&OP processes (4 stages: Demand, Supply, Alignment and S&OP MT meeting) with X-functional collaboration• Leading Weekly S&OP meeting• Leading Material Requirement Planning (MRP) within Supply Chain in both breweries• Leading the TPM / Lean Management of Plan Pillar and SCOM member of Logistic Pillar• SAP Business Process Owner of modules: Sales & Distribution, Production Planning• SAP Key user for Material Management• Inter OpCo Sourcing activities to secure regular supply planning• Inventory Management (50 raw materials, 300 packaging materials, 40 semi finish products, 60 SKU’s + promotional materials)• Brewing plan creation• Packaging planning and scheduling • RPM planning• Shift planning and scheduling• Capacity planning creation
-
-
-
MB brewery
-
United States
-
Religious Institutions
-
Logistics Coordinator
-
Feb 2007 - Feb 2008
Main achievements: • Established route scheduling process and couched the team in five DC’s which resulted in increasing of On Time deliveries and customer satisfaction.Responsibilities:• Managing routing system and transportation planning• Planning and optimization of stocks in distribution centers• Demand planning for distribution centers• Supply planning for distribution centers• Management of own and third party fleet (100 trucks)• Management of company cars fleet (250 cars)
-
-
-
Comtrade Group
-
Serbia
-
IT Services and IT Consulting
-
200 - 300 Employee
-
Sales & Logistic Manager
-
Feb 2006 - Feb 2007
Main achievements: Improved sales in 3 shops in Novi Sad through products presentation in various companies outside of the shops.Responsibilities:- Managing team of 25 employees (3 direct reports)- Setting up sales strategy in shops enhance achieving the targets- Inventory optimisation for more than 1000 products (computer equipment, phones, LCD &Plasma TV, digital cameras, etc.)- Shift planning in three shops Main achievements: Improved sales in 3 shops in Novi Sad through products presentation in various companies outside of the shops.Responsibilities:- Managing team of 25 employees (3 direct reports)- Setting up sales strategy in shops enhance achieving the targets- Inventory optimisation for more than 1000 products (computer equipment, phones, LCD &Plasma TV, digital cameras, etc.)- Shift planning in three shops
-
-
Education
-
Faculty of Technical Sciences, Novi Sad
Road and City Traffic
Community
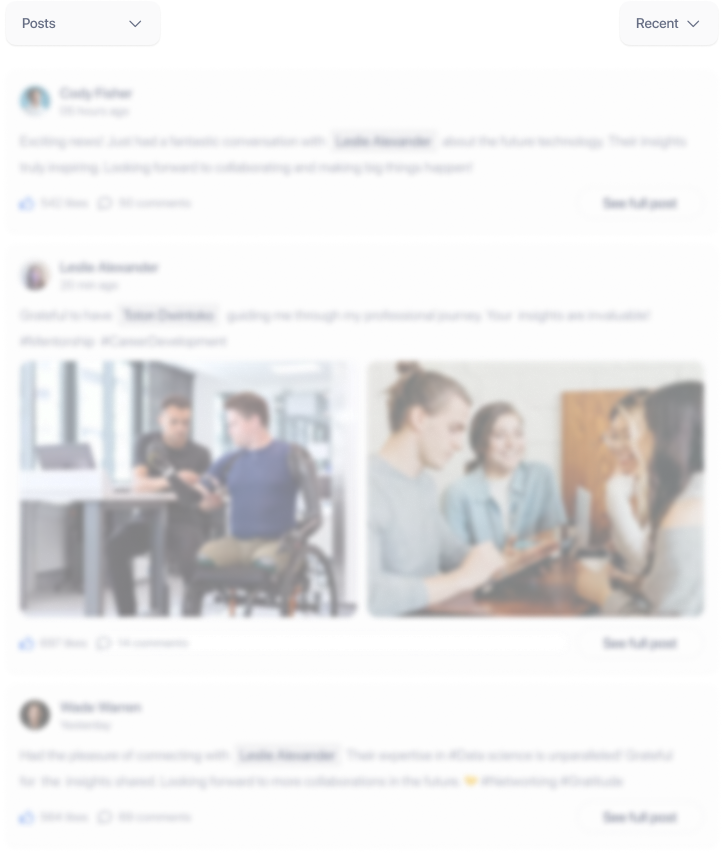