Vishaal Gopal
Program Manager at ChemFORWARD- Claim this Profile
Click to upgrade to our gold package
for the full feature experience.
Topline Score
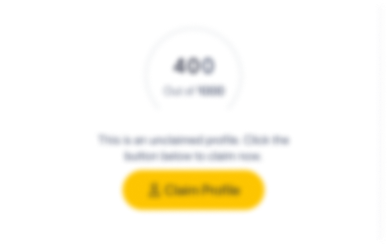
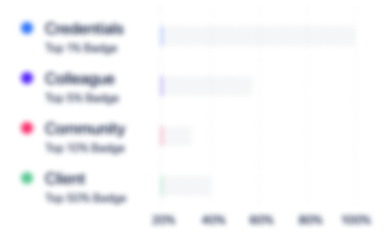
Bio


Experience
-
ChemFORWARD
-
United States
-
Non-profit Organizations
-
1 - 100 Employee
-
Program Manager
-
Aug 2023 - Present
Nashville Metropolitan Area ● Operationalize the Electronics Safer Chemistry Collaborative for scale and growth ● Manage key business initiatives, programs, client projects, and stakeholder engagement with members including Apple, Google, Intel, HP, Amazon, Microsoft, Seagate, Sonos, and more ● Champion the coordination of resources and processes to ensure that projects and initiatives are delivered on time and within budget ● Utilize project management tools and processes to plan, organize, allocate… Show more ● Operationalize the Electronics Safer Chemistry Collaborative for scale and growth ● Manage key business initiatives, programs, client projects, and stakeholder engagement with members including Apple, Google, Intel, HP, Amazon, Microsoft, Seagate, Sonos, and more ● Champion the coordination of resources and processes to ensure that projects and initiatives are delivered on time and within budget ● Utilize project management tools and processes to plan, organize, allocate resources, establish timelines, monitor metrics, report on progress, and solve challenges as they arise. ● Coordinate internal resources and third parties/vendors for execution, management, and growth ● Developing project scopes and objectives, performing risk management, creating and maintaining appropriate project documentation and reporting to achieve program growth and sustainability ● Engaging stakeholders including OEM’s, chemical suppliers, and relevant industry associations. ● Driving weekly, monthly, and quarterly meetings with key stakeholder groups while growing engagement through strategic outreach ● Champion efficiency and scalability by establishing project management processes and tools to track, communicate progress, and ensure projects are delivered on time, within scope, and within budget ● Build relationships with team members and external stakeholders, troubleshoot blockers and ensure that when challenges arise they are addresed in a timely manner by partnering with relevant stakeholders ● Using appropriate verification techniques to manage changes in project scope, schedule, and costs ● Drive operational efficiency and establish metrics for project performance using appropriate systems, tools and techniques ● Lead development of new processes and tools that will be recognized as key factors in growth, scalability, and ultimate success Show less
-
-
-
Amazon
-
Bangladesh
-
Advertising Services
-
1 - 100 Employee
-
Program Manager - Threat Intelligence
-
Dec 2022 - Aug 2023
Nashville Metropolitan Area Amazon External Threat Intelligence team plays a key role in the interpretation, transformation, and dissemination of intelligence crucial to the protection of Amazon customers and partners from fraudulent actors. External Threat Intelligence team provides Amazon teams with information about the threat landscape and targeting fraud actors. The team uses information derived from all intelligence disciplines to determine changes in actor activity, capabilities, intent, and resources. -… Show more Amazon External Threat Intelligence team plays a key role in the interpretation, transformation, and dissemination of intelligence crucial to the protection of Amazon customers and partners from fraudulent actors. External Threat Intelligence team provides Amazon teams with information about the threat landscape and targeting fraud actors. The team uses information derived from all intelligence disciplines to determine changes in actor activity, capabilities, intent, and resources. - Partner with internal teams to dive deep and assess risks, identify root causes and create plans to engage Amazon stakeholders to mitigate and close vulnerabilities - Own regular program reviews with stakeholders to assess ongoing performance against key milestones and program goals - Cross functional team collaboration with operations leaders, risk managers, product managers, threat intelligence analysts, software developers, data and security engineers - Define appropriate milestones and mechanisms to measure the progress for programs and share structured recurring updates to executive leaders across the company - Monitor and respond to stakeholder feedback, escalate and drive clarity on program objectives - Own components of strategic initiatives and collaborate with Sr. Program Managers to execute programs to drive long term detection and mitigation of risks - Responsible for meticulous documentation, communicating project updates to executive leadership and stakeholders on regular cadence - Contribute narrative inputs to business and leadership reviews of ongoing programs
-
-
Program Manager - NASC Performance
-
Aug 2021 - Dec 2022
Nashville, Tennessee, United States I was a part of the NASC (North America Sort Centers) Performance team NASC Performance team is the heart of Amazon WW (World Wide) Operations. The Performance team comprises of a set of network subject matter experts who leverage data and anecdotes from CE (Customer Experience) defects to continually raise the bar on delivery services at Amazon. - Develop an operational and technical roadmap based on data deep dives and anecdotes to mitigate customer experience risk for the Sort… Show more I was a part of the NASC (North America Sort Centers) Performance team NASC Performance team is the heart of Amazon WW (World Wide) Operations. The Performance team comprises of a set of network subject matter experts who leverage data and anecdotes from CE (Customer Experience) defects to continually raise the bar on delivery services at Amazon. - Develop an operational and technical roadmap based on data deep dives and anecdotes to mitigate customer experience risk for the Sort Center network - Work directly with operations leaders and partner teams such as process engineering, software developers, data analytics, quality assurance and logistics planners to craft and deliver scalable solutions to identified operational issues - Own communication for the region, accelerating progress by driving crisp and timely decisions, clearing blockers (e.g., path to green), escalating as appropriate - Influence design and development of processes in sort centers - Collaborate with program managers and business leaders to communicate and impact critical business initiatives - Develop, implement, and govern key performance indicators (KPI) reporting for the region’s health, providing visibility to the milestones and performance across all projects and using the data to drive business decisions - Explore opportunities to improve program quality and operational excellence - Partner with other program managers to secure resources, scope efforts, set project priorities, milestones and drive delivery
-
-
-
Boeing
-
United States
-
Aviation and Aerospace Component Manufacturing
-
1 - 100 Employee
-
Procurement Agent - Boeing Defense, Space & Security (BDS)
-
Apr 2020 - Jul 2021
El Segundo, California, United States I was a part of the Boeing Defense, Space & Security (BDS) Supply Chain organization • Leads proposal analyses, supplier negotiation process, develops contract management plans and negotiation strategies for new business acquisition to fulfill customer/program strategic requirements • Negotiates and contracts for products, services and technologies • Negotiates all elements of the contract including pricing, contract terms and conditions • Creates/modifies buy authorization;… Show more I was a part of the Boeing Defense, Space & Security (BDS) Supply Chain organization • Leads proposal analyses, supplier negotiation process, develops contract management plans and negotiation strategies for new business acquisition to fulfill customer/program strategic requirements • Negotiates and contracts for products, services and technologies • Negotiates all elements of the contract including pricing, contract terms and conditions • Creates/modifies buy authorization; Prepares, executes negotiated contractual documents and binding agreements • Prepares, executes negotiated documents and manages contract terminations/renewals in compliance with Federal Acquisition Regulations (FAR) & Defense Federal Acquisition Regulations (DFAR) through end to end contract management • Manages and leads development of cross functional solutions to address issues, deploy improved processes, systems and tools • Communicates and provides updates in project and program reviews; Engages stakeholders to integrate program, customer, product and in-service strategies into source selection, negotiation and contracting strategies • Optimizes execution of the supply chain balancing inventory, supply orders and schedule demand • Manages supplier/subcontractor performance and relationship to ensure delivery, quality, financial stability and in-service performance; Leading supplier performance teams to develop strategic supplier solutions across programs and commodities • Facilitates and ensures compliance with company procedures and regulatory requirements • Manages supplier import/export regulatory requirements and compliance (EAR and ITAR) • Leads suppliers and stakeholders in the development of risk, issue and opportunities management plans; Communicates across functions/programs to manage risks, issues and performance to plan • Initiates/executes supplier improvement activities and provides results for integration into contracting strategies
-
-
Procurement Agent - Boeing Global Services (BGS) / Manufacturing, Supply Chain & Operations (MSC&O)
-
Oct 2017 - Apr 2020
Seal Beach, California, United States Project Management / Major Subcontracts Management: - Developing & supporting procurement solutions to best fulfil customer requirements - Evaluating supplier capabilities & capacities - Negotiating & executing supplier contracts by working with internal and external stakeholders - Managing supplier delivery, quality, cost, and performance - Optimizing the execution of the supply chain - Managing supplier performance through collaborative relationships -… Show more Project Management / Major Subcontracts Management: - Developing & supporting procurement solutions to best fulfil customer requirements - Evaluating supplier capabilities & capacities - Negotiating & executing supplier contracts by working with internal and external stakeholders - Managing supplier delivery, quality, cost, and performance - Optimizing the execution of the supply chain - Managing supplier performance through collaborative relationships - Identifying & mitigating supply chain risks - Pursuing & developing continuous improvement opportunities - Coordinate with engineering stakeholders to facilitate design for manufacturing (DFM) feedback from the supply base to enhance first time quality, improve product build lead time and costs Supply Chain Strategies/ Contracts, Risk & Compliance Management: - Engage in Value Add/Value Engineering Mapping & Execution - Actively partner with Enterprise stakeholders on development and implementation of Supply Chain strategies - Collaborating with cross-functional teams to fulfill business objectives - Improve and document Process Flows - Implementation of Lean Improvements across the value chain - Communicate, track and manage project objectives and activities - Extract and analyze data, Key Performance Indicators and Metrics from multiple data sources and ERP systems to streamline the Supply Chain - Review Procurement systems & prepare reports to evaluate opportunities and gaps in the Supply base - Assess schedules, create policies for execution of procurement activities
-
-
-
Ansell
-
United States
-
Consumer Goods
-
700 & Above Employee
-
Supply Chain Specialist
-
Apr 2017 - Oct 2017
Chatsworth, California, USA - Drive operational efficiencies, strategic supply chain initiatives and process optimization through order fulfillment including logistics coordination for the Healthcare Safety Solutions (HSS) business division - Demand Forecasting for Ansell Sandel product line, Production scheduling & prioritization to support customer order priorities and fluctuating sales trends in North American markets - Support strategic sourcing efforts, procurement of raw materials and finished goods… Show more - Drive operational efficiencies, strategic supply chain initiatives and process optimization through order fulfillment including logistics coordination for the Healthcare Safety Solutions (HSS) business division - Demand Forecasting for Ansell Sandel product line, Production scheduling & prioritization to support customer order priorities and fluctuating sales trends in North American markets - Support strategic sourcing efforts, procurement of raw materials and finished goods from a global supply base of 20+ suppliers and contract manufacturers spanning over United States , Mexico, China and Japan to meet business requirements at competitive costs and expected quality - Cross functional team collaboration to streamline and improve production, shipping, receiving and inspection processes - Periodic monitoring & reporting of back ordered finished products to Ansell’s executive leadership, optimize demand forecasts and production schedules thereby successfully helped reduce back ordered dollar value by 80% in four months for Ansell Sandel product line. - Plan and facilitate inter-company inventory transfers to support global demand for Ansell Sandel product line by collaborating with Ansell EMEA (Europe, Middle East & Africa) , ANZ (Australia & New Zealand), APAC (Asia-Pacific) and Americas. - Working with distribution centers, global and regional partners in executing strategic cross functional projects in accordance with deadlines and budgets, maintaining strong collaborative relationships with suppliers - Establishing and maintaining supplier quality working closely with suppliers, Quality Assurance and other functional partners; Optimizing supply chain performance against key performance indicators Show less
-
-
-
Avcorp Industries
-
Canada
-
Aviation and Aerospace Component Manufacturing
-
1 - 100 Employee
-
Supply Chain Management Systems Intern
-
May 2016 - Apr 2017
Gardena, California, USA *Avcorp Industries acquired by Latcoere in November 2022 - Client & Supplier Liaison- Coordinating with end customers like Boeing, Fuji Heavy Industries (FHI) and multiple suppliers to improve handling, movement and packaging of Boeing 787-9 Carbon Composite beams - Product Quality Improvement: Participate in weekly Quality Improvement Projects (QIP) and apply principles of Quality Control (QC) and Total Quality Management (TQM) to analyze and reduce rework in shop floor… Show more *Avcorp Industries acquired by Latcoere in November 2022 - Client & Supplier Liaison- Coordinating with end customers like Boeing, Fuji Heavy Industries (FHI) and multiple suppliers to improve handling, movement and packaging of Boeing 787-9 Carbon Composite beams - Product Quality Improvement: Participate in weekly Quality Improvement Projects (QIP) and apply principles of Quality Control (QC) and Total Quality Management (TQM) to analyze and reduce rework in shop floor processes - Manufacturing Process Improvement : Optimizing workflows in work centers, conducting time/motion studies, value stream mapping and improving process throughput through application of Lean and Six Sigma tools - Delivery Process Improvement- Collaborating with Quality Document Control & Shipping/Receiving departments to refine traceability of work orders and upgrade the delivery process to increase efficiency - Material Requirements Planning & Master Production Scheduling- Optimizing inventory levels, capacity planning capabilities and shop floor control to reduce work in progress (WIP) inventory - Procurement Control- Connecting with new and existing suppliers to acquire required materials and aircraft structures for business units; Monitoring ERP systems to keep track of purchase orders, inventory levels and organizational resources Show less
-
-
-
Dodsal E & C Pte Ltd
-
United Arab Emirates
-
Oil and Gas
-
700 & Above Employee
-
Project Management Intern
-
Aug 2014 - Jan 2015
Dubai, United Arab Emirates - Project Management- Gained vast knowledge and valuable experience in the field of project management through creation and management of cross-functional sub-team work breakdown structures, gantt charts, project networks and schedules. I understood the essence of teamwork, task prioritization, planning and coordination with multi-disciplinary technical and commercial teams working on the Kuwait Oil Company GC-31 project - Business Process Modeling-Strategically analyzed and devised… Show more - Project Management- Gained vast knowledge and valuable experience in the field of project management through creation and management of cross-functional sub-team work breakdown structures, gantt charts, project networks and schedules. I understood the essence of teamwork, task prioritization, planning and coordination with multi-disciplinary technical and commercial teams working on the Kuwait Oil Company GC-31 project - Business Process Modeling-Strategically analyzed and devised action plans to ensure optimal utilization of finances and resources by collaborating with estimation, finance, supply chain, business development and procurement teams - Prepared project proposals, technical specification reports, client queries, engineering change notices, cost and budget evaluations for monthly client meetings - Database Control-Upgraded project equipment database(on MS Access) by collecting and evaluating data from multiple engineering departments to revise data sheets and material requisitions as per client standards Show less
-
-
-
HOERBIGER
-
Switzerland
-
Machinery Manufacturing
-
700 & Above Employee
-
Process Improvement Intern
-
Jan 2014 - Jan 2014
Dubai, United Arab Emirates - Root Cause Analysis & Process Improvement- Analyzed defects and improved maintenance processes of reciprocating compressors using root cause analysis - Process Data Analysis- Examined and optimized servicing its ancillary like valves, piston rod and stuffing box by collecting and evaluating process data - Lean & Six Sigma Tools, Quality Control- Applied Statistical Quality Control, 5S Methodology and Total Quality Management Techniques (TQM) to facilitate customer focused… Show more - Root Cause Analysis & Process Improvement- Analyzed defects and improved maintenance processes of reciprocating compressors using root cause analysis - Process Data Analysis- Examined and optimized servicing its ancillary like valves, piston rod and stuffing box by collecting and evaluating process data - Lean & Six Sigma Tools, Quality Control- Applied Statistical Quality Control, 5S Methodology and Total Quality Management Techniques (TQM) to facilitate customer focused quality improvements initiatives Show less
-
-
-
-
Manufacturing & Inventory Intern
-
Jun 2013 - Aug 2013
Dubai, United Arab Emirates - Production Planning & Process Mapping- Successfully implemented & planned manufacturing processes using fundamentals of value stream mapping - Inventory Control & Kaizen Events- Estimated economic order quantity and engaged in Kaizen events to optimize throughput time, inventory levels and assembly time - Market Entry & Customer Trend Analysis- Assisted Product Development team in market entry and customer trend analysis of newly designed precision press tools, turnkey… Show more - Production Planning & Process Mapping- Successfully implemented & planned manufacturing processes using fundamentals of value stream mapping - Inventory Control & Kaizen Events- Estimated economic order quantity and engaged in Kaizen events to optimize throughput time, inventory levels and assembly time - Market Entry & Customer Trend Analysis- Assisted Product Development team in market entry and customer trend analysis of newly designed precision press tools, turnkey projects, LPG systems and CNC job parts - Product Management- Assessed Product Lifecycle of above mentioned products during the course of the Internship - Prepared a detailed reference manual on Compter Aided Design/Manufacturing (CAD / CAM) systems being used in the production line. Show less
-
-
-
Rane Group
-
India
-
Motor Vehicle Manufacturing
-
700 & Above Employee
-
Supply Chain & Manufacturing Intern
-
Jul 2012 - Aug 2012
Chennai,India -Operations Control - Planned production operations for valves and cam shafts to meet client demand - Supply Chain Improvements- Reduced transportation lead time between supply nodes to reduce procurement lead time, improve inventory turn over ratio and productivity - Productivity Enhancements-Assessed manufacturing processes of valves and helped in cycle time reduction through time/motion studies thereby facilitating improvement in operational efficiency and productivity -… Show more -Operations Control - Planned production operations for valves and cam shafts to meet client demand - Supply Chain Improvements- Reduced transportation lead time between supply nodes to reduce procurement lead time, improve inventory turn over ratio and productivity - Productivity Enhancements-Assessed manufacturing processes of valves and helped in cycle time reduction through time/motion studies thereby facilitating improvement in operational efficiency and productivity - Change Management-Examined and upgraded team collaboration, operating rhythms and communication networks among various engineering sectors to enhance productivity and efficiency - Market Sizing Analysis- Assisted the business development and product design teams in Market Sizing Analysis of newly designed valve tappets and cam shafts Show less
-
-
Education
-
University of Southern California
Master of Science - MS, Industrial and Systems Engineering -
University of Southern California - Marshall School of Business
Graduate Certificate, Optimization and Supply Chain Management -
Birla Institute Of Technology and Science, Pilani Dubai
Bachelor of Engineering - BE, Mechanical Engineering -
Cornell University
Certificate, Project Management -
University of California, San Diego - Rady School of Management
Engineerin Edge Certificate Program - Aerospace and Defense Focus, ENGINEERING -
Abu Dhabi Indian School
High School Diploma, Physics, Chemistry, Computer Science and Mathematics
Community
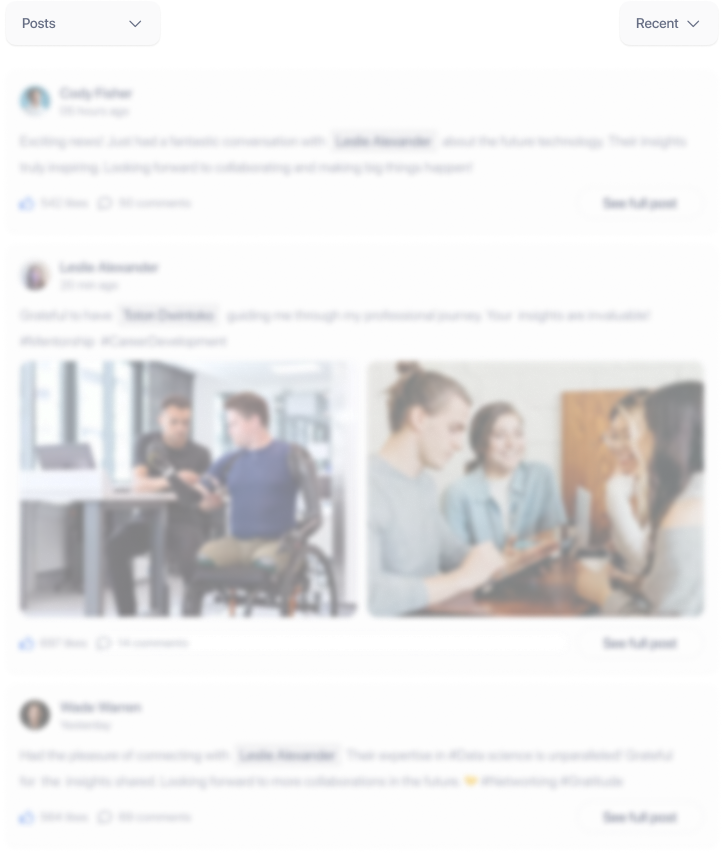