Mike Vinson
Warehouse And Distribution Manager at Blue Bird Corporation- Claim this Profile
Click to upgrade to our gold package
for the full feature experience.
-
English -
Topline Score
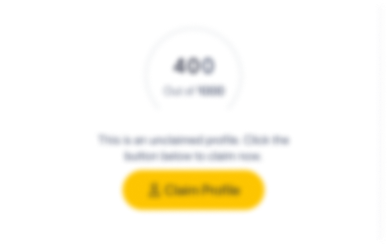
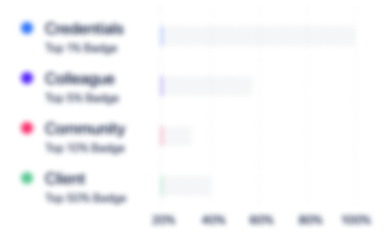
Bio


Credentials
-
ISO 9001:2000 Internal Quality Systems Auditor
BSIApr, 2008- Nov, 2024
Experience
-
Blue Bird Corporation
-
United States
-
Motor Vehicle Manufacturing
-
400 - 500 Employee
-
Warehouse And Distribution Manager
-
Jun 2020 - Present
Blue Bird, located in Fort Valley, Georgia, is a world leader in the manufacturing of school buses, security buses, and activity buses. These are offered in a variety of power solutions, including Propane, CNG, Gasoline, and Electric Bus options with annual production ranging from 8,000 to 10,000 units. -Lead a team of 50+ hourly associates and 2 Shift Supervisors in 300K SF facility operating three shifts on a 24/5 schedule. Peak Season operate up to 24/7 basis. -Manage daily shipping and receiving operations to include processing up to 35 inbound and 24 outbound truckloads to Fort Valley facilities, scheduling of Express shipment outbounds, and servicing other company facilities to include Part Sales, Blue Bird Fabrication, and Blue Bird West operations. -Work with outside suppliers to ensure timely M&R of Plant equipment. This includes 25 mobile equipment units, auto-tie stretch wrap machine, and company owned Class A trucks. -Oversee picking, kitting, and put-away aspects of operations to ensure manpower and budgetary metrics are met in a monthly and annual cost-effective manner, ensure safe and proper storage of over 12K inventory components valued up to $39M, and work with Supply Chain Materials Department to coordinate timely delivery of supplier shipments. -Responsible for HR functions including payroll, disciplinary actions, and termination processes. Handle escalation of issues to the Director of Supply Chain that affect cost, quality, customer service, or safety of operations. -Work with Corporate Finance & Purchasing to ensure proper receipt of purchased parts, disposal and storage of obsolete materials, Purchase Order requisitions, and verification of monthly inventory levels. -Responsible for site EHS requirements, orientation/training of new associates, Continuous Process Improvements, and review/implementation of both Work Instructions & SOP’s in order to improve operational efficiency. Show less
-
-
-
Dixie Pulp & Paper, Inc.
-
United States
-
Paper & Forest Products
-
1 - 100 Employee
-
Plant Manager
-
Jul 2019 - Mar 2020
Dixie Pulp & Paper provides solutions for off-grade paper, board, tissue, pulp, and secondary fiber customers and suppliers. They market these products across the U.S. and abroad from four recycling and processing plants. – Led a team of 12+ hourly and temporary associates in a 43K SF facility operating three shifts on a 24/5 schedule. – Managed daily shipping and receiving operations including processing up to 10 inbound / outbound truckloads, scheduling railcar outbounds, and servicing company tractor-trailer accounts. Plant equipment includes auto-tie baler, WEIMA shredder, roll guillotine, EXCEL closed door baler, and mobile equipment. – Oversaw all aspects of operations including ensuring budgetary metrics were met in a monthly and annual cost-effective manner, working with customer service group to verify all incoming and outgoing shipments, managing the handling and disposition of materials, and maintaining monthly inventory. – In charge of HR functions including payroll, disciplinary actions, and termination processes. Handled escalation of issues to the Senior Director of Operations that affected cost, quality, customer service, or safety of operations. – Managed the budget for processing and handling 2400 inbound and 2600 outbound tons per month. Managed annual operating expense budget of $1.3M and revenue budget of $1.375M. – Coordinated with sales team to ensure both supplier and customer issues were resolved in a timely manner. Show less
-
-
-
GEODIS (Loss of Account)
-
McDonough, Georgia, United States
-
Operations Manager » First Shift Monday – Thursday
-
Aug 2018 - Jul 2019
GEODIS is a 3PL supply chain operator and part of the SNFC Group, the number one transport and logistics operator in France. In the U.S., GEODIS has 160+ warehousing sites with over 37M SF servicing a wide range of industry sectors. – Led a team of 45+ FT hourly and temporary associates in 360K SF facility. Maintained consistent communication and a high level of customer satisfaction. Led cultural change within facility. – Managed three supervisors and four lead personnel covering operational areas including receiving, cross-dock, picking, replenishment, auditing, and shipping operations. – Oversaw all aspects of operational activities including ensuring customer and location Key Performance Indicators (KPI) metrics were met in a timely and cost-effective manner. Ensured incoming and outgoing shipments were executed flawlessly, materials were handled and disposed of properly, and inventory was maintained well. – Ensured compliance with Environmental Health and Safety (EHS), Customs Trade Partnership Against Terrorism (CTPAT), ISO, AIB, and other regulatory certifications. – Managed site P&L and HR functions including payroll, discipline, and termination processes. Handled escalation of issues to the Senior Operations Manager that affected cost, quality, customer service, or safety of operations. – In charge of daily shipping and receiving operations including processing over 15 inbound and 25 outbound truckloads a day, and monitoring LTL and customer pick-ups. – Ensured work orders for repair and/or replacement of equipment were submitted to management for all necessary approvals. Show less
-
-
-
Capstone Logistics, LLC
-
United States
-
Transportation, Logistics, Supply Chain and Storage
-
700 & Above Employee
-
Warehouse Site Manager
-
Dec 2017 - Aug 2018
Capstone is the leading 3PL in the U.S. with over 400 locations. Manufacturing and distribution operational support services include full service unloading warehouse support, production project support, and value-add services. – Led a team of 60 hourly associates responsible for providing unloading services for both dry dock and cold dock operations in food and beverage industry. – Oversaw all aspects of operational activities including ensuring customer and location KPI metrics were met; customer value-added services including site scheduling of inbound loads were flawlessly executed; oversight of security, delivery, and removal of excess pallets in facility was maintained; spotting trailers for loading and unloading was managed; and clerical office support was provided. – Responsible for all EHS compliance; site P&L; HR functions including interviewing, hiring, and termination processes; and handled escalation of issues to the Regional Director that affected cost, quality, customer service, or safety of operations. – Responsible for daily operations including processing an average of 100+ truckloads per day. Inventory product mix consisted of 70% cold and 30% dry truckload breakdown. – Served as Project Site Manager for a 12-week customer assistance program with 25 road crew team members; assisted customer with daily picking operations on their second shift. – Achieved Year to Date (YTD) actual revenue 10.60% over YTD budget. – Managed two supervisors with seven support personnel to provide administrative and value-added services. – Ensured daily site check and cash closeout transactions were properly entered, and payments were correct prior to transfer to bank and system entry; ensured payroll and system truck transactions were entered and uploaded for end of day closeout. – Oversaw weekly site closeout to ensure truck receipts had been verified and transferred on a daily basis, and payroll, and customer billing and invoicing had been completed correctly. Show less
-
-
-
1888 Mills
-
United States
-
Textile Manufacturing
-
100 - 200 Employee
-
Distribution Center Manager
-
Nov 2014 - Dec 2017
1888 Mills is a leading global manufacturer of home and commercial textiles catering to the retail, hospitality, and healthcare markets worldwide. The company also operates the largest remaining towel mill in the United States. – Led a team of 45 employees and up to 15 temps. Supervised multi-site (three) operations with 650K total SF. Provided 24/5 or 24/7 support to manufacturing for retail, e-commerce, and hospitality business units. – Oversaw all Logistics Center (LC) operations including ensuring customer and location KPI metrics were met; all customer value-added services were flawlessly executed, inventory control including ABCD analysis was performed, and pick-pack and storage and delivery requirements were executed through initiation of process improvement and root cause analysis. – Ensured compliance with EHS, CTPAT, DOT, OSHA, and other regulatory certifications. – Managed site P&L and HR functions and handled escalation of issues to the VP of Supply Chain that affected cost, quality, customer service, or safety of operations. – In February 2015, managed relocation and start-up of new distribution center (DC) facility located 35 miles away from Griffin, in Thomaston, Georgia; continued simultaneous operations with no interruptions in customer service. Was $400K under budget for capital assets Request for Proposal (RFPs) associated with start-up and relocation. Transferred all associates, with no turnover, to new location. – Managed two direct reports with five administrative reports, supporting retail and hospitality businesses. – Inventory Product mix consisted of 70% imported and 30% domestic mill production. Show less
-
-
-
SYNCREON (FACILITY CLOSURE)
-
Greater Atlanta Area
-
Senior Logistics Center Manager
-
Apr 2010 - Jun 2014
Syncreon is a multi-national 3PL company headquartered in Detroit that is ISO 9001 certified and designs and operates supply chain solutions for leading Fortune 500 companies. – Supervised all LC operations including ensuring customer and location KPI metrics were met; all customer value-added services were flawlessly executed; inventory, kitting, pick-pack, storage, and delivery requirements were maintained through initiation of process improvement and root cause analysis. Also, ensured site P&L was managed; and, when needed, issues were escalated to the General Manager if they affected cost, quality, or safety of the operations. – Ensured all EHS, CTPAT, DOT, and OSHA requirements were met, and compliance with ISO 9001 Quality Management System program was maintained. – Became the first LC to exceed company ISO internal audit objective score of 92%; received score of 93%. – Achieved 63% return on Lowes Retail Project versus target return of 35%; resulted in $100K additional revenue. – Maintained highest warehouse inventory accuracy in network with YTD totals at 100% versus goal of 99.5%. – Achieved zero OSHA recordable or lost time accidents or incidents during tenure. – Indirect billable hours were 4% YTD versus LC objective of 17%; LC had 0% YTD claims attributed to handling. – Oversaw business process improvements resulting in over $1000 per month savings beginning in 2011. – Served as project start-up team member for two new locations in Grapevine, Texas and Dayton, New Jersey. Show less
-
-
-
Hoshizaki America
-
United States
-
Industrial Machinery Manufacturing
-
300 - 400 Employee
-
Materials Department Manager
-
Dec 2008 - Apr 2010
Hoshizaki America is one of the world’s largest manufacturers of commercial ice equipment and refrigerated food service equipment. Hoshizaki is ISO-9001/ISO 14000 certified and employs over 10,000 people worldwide. – Led a four-member team. Ensured 300+ monthly orders were picked and administered correctly in the following areas: production lines (seven), engineering, service parts, quality control, scrap, and line requisition items. – In charge of inventory control for 1,100+ pick-to-stock parts valued at over $1.2M. Handled all galvanized and stainless-steel sheets for processing, and finished sheet metal components for storage. Handled all order delivery to production lines. – Ensured correct data entry into AS400 system for all orders picked and delivered; performed monthly cycle counts and semi-annual physical inventory count. – Served as Kaizen team member for Reach-In production cell which reduced unit assembly times by 50%. – Managed inbound receiving department operation from inter-company transfers and outside 3PL transportation services. Ensured accuracy of item labeling, stocking of items, and purchase order entry into the computer. – Managed Quality Control (QC) inbound first part item inspection process. Ensured all parts were sampled and met vendor engineering drawing specifications. Reported nonconformities to buyers and purchasing department; held items from production until issues were resolved. Tracked all engineering design and deviation changes in manufacturing processes and reported to management on a weekly basis. – Ensured Lean, 5S, ISO 9001, Kaizen, Kanban, Six Sigma, and other Continuous Improvement (CI) procedures were implemented and followed. Show less
-
-
Education
-
Georgia Institute of Technology
Bachelor of Science (BS), Management -
MIddle Georgia College
Associate of Science (AS), Industrial Management -
Professional Development
Community
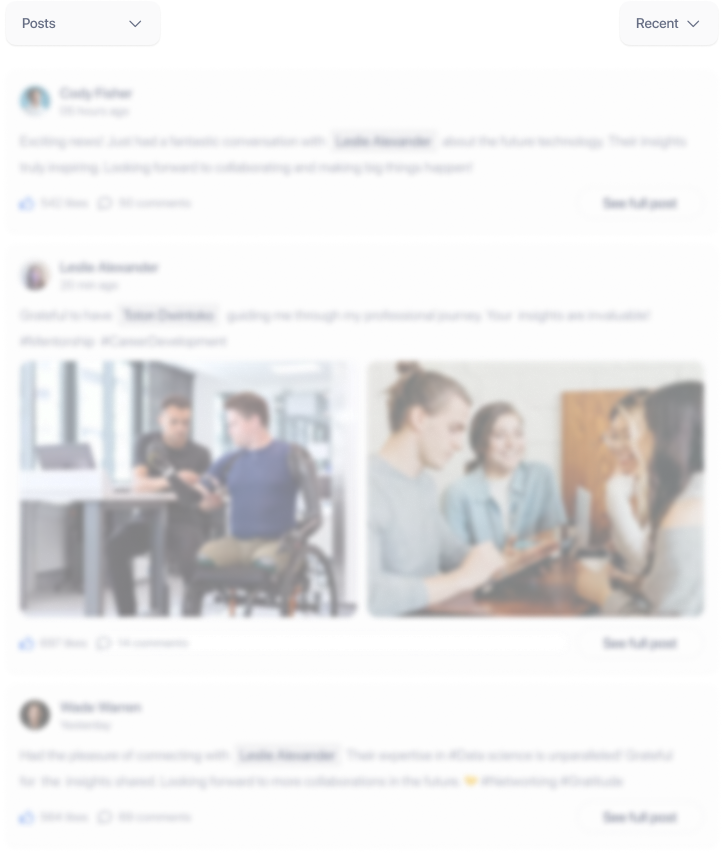