Brian Videtich, EIT, CP1
Production Engineer - ND (Bakken & ThreeForks) at Slawson Companies- Claim this Profile
Click to upgrade to our gold package
for the full feature experience.
-
Spanish Elementary proficiency
Topline Score
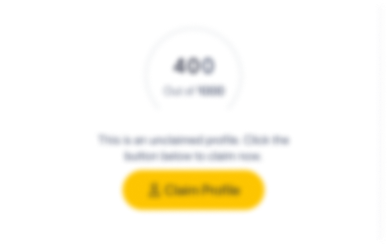
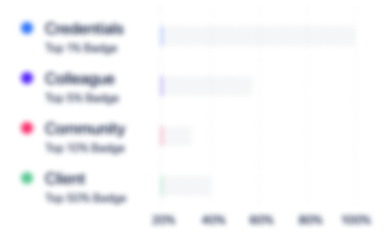
Bio


Experience
-
Slawson Companies
-
Oil and Gas
-
1 - 100 Employee
-
Production Engineer - ND (Bakken & ThreeForks)
-
Jul 2018 - Present
-
-
-
Caliber Midstream
-
Oil and Gas
-
1 - 100 Employee
-
Project & Facilities/Operations Engineer - ND (Bakken & ThreeForks)
-
May 2014 - Jul 2018
◆ Handle day-to-day operations of a multi-directional produced water gathering and disposal system with a down-hole capacity of 34,000 BWPD. Organize flowback coordination and logistics, chemical injection programs and facility improvements/troubleshooting.◆ Successfully planned, coordinated and executed 4 acid jobs on wells in the Dakota disposal system to improve down-hole capacity ahead of major operations. Arranged workover operations to investigate, mitigate and repair damages to a SWD. Conducted and passed MIT examinations on 5 disposal wells. ◆ Assist in the day-to-day operations of a Refrigeration Plant capable of processing 10.5 MMSCF of Bakken gas per day. Troubleshoot and commission a 2 MMSCFD VRU capable of collecting tank vapors from a central stabilizing facility. ◆ Support daily operations of an oil stabilization facility capable of processing 40,000 BOPD and monitor nominations to a large transmission pipeline.◆ Troubleshoot, design, support and optimize wellsite transfer units including LACTs, water transfer skids and gas metering buildings. Discuss interaction between clients automation to optimize safety and efficiency of the units.◆ Managing SCADA implementation (ClearSCADA, Profile & Kepware) including design architecture, interface, alarming scheme, networking, software and hardware, and information optimization. Managing meter data utilizing FlowCal in a unique allocation scheme revolving around the capture of entrained gases from "live" oil. Successfully designed the ability to automatically upload truck offloading batches directly into FlowCal in real-time. ◆ Hierarchy design and implementation of maintenance coordination and work order software for utilization in facility, grounds, PHMSA, mechanical and electrical maintenance and regulatory schedules.
-
-
-
Continued...
-
United States
-
E-Learning Providers
-
1 - 100 Employee
-
Project & Facilities/Operations Engineer - ND (Bakken & ThreeForks)
-
May 2014 - Jul 2018
◆ Manage 3 deep well impressed current cathodic protection systems for 100 miles of pipeline including 2 PHMSA regulated breakout tanks. Organize and manage all foreign encroachment and line crossings for the isolation of influential and interfering currents. Review annual pipe-to-soil surveys and CIS data to conform to 49 CFR 192/195 and O & M manual requirements.◆ Planned, organized and participated in 49 CFR 192 and 49 CFR 195 audits. ◆ Manage 3 deep well impressed current cathodic protection systems for 100 miles of pipeline including 2 PHMSA regulated breakout tanks. Organize and manage all foreign encroachment and line crossings for the isolation of influential and interfering currents. Review annual pipe-to-soil surveys and CIS data to conform to 49 CFR 192/195 and O & M manual requirements.◆ Planned, organized and participated in 49 CFR 192 and 49 CFR 195 audits.
-
-
-
-
Facilities/Midsteam Engineer - ND (Bakken & ThreeForks) / WY (Sussex, Shannon & Muddy)
-
Aug 2012 - May 2014
◆ Created a company-wide standard on tank vapor control management which included a sizing, piping design and equipment standard for the control of atmospheric tank vapor emissions for multiple North American basins. The standard provided operations and maintenance procedures as well as environmental reporting of tank vapor destruction. ◆ Responsible for the the design and project engineering for production and operations support in Wyoming and North Dakota basins. I have maintained a heavy travel schedule (60%) consisting of field visits, contractor/bid meetings, project kick-off meetings, equipment acceptance, construction approvals, commissionings and project haz-ops.◆ Acting project manager accountable in 2013 for $19MM worth of projects in North Dakota.These projects included:▪ 12-well off-site central tank battery with (2) VRUs and (2) LACTs able to handle 5000bopd & 7MMSCFD of production.▪ Stationary and mobile jet pump operations which included the design of skid mounted injection, power cycle fluids processing, prime tanks and wellhead modules.▪ High-volume ESP artificial lift on a facility with considerable produced water volumes and a high concentration of hydrogen sulfide.▪ Implementation of a 10" HDPE SDR9 produced water gathering system which connects 68 wells.▪ Installation and project management of electrical and automation installs for 68 wells.▪ Erection of a 100ft. communications tower which involved county meetings and public discussions.▪ Implemented several LACTs, VRUs, VCDs and pump skids on multiple wellsites.Projects spanned from conception to commissioning and included performing regulatory and standards research, generating P&IDs, C&E matrices and EI&C diagrams, producing bid documents, sizing and ordering equipment, coordinating hazops and commissioning and troubleshooting equipment.
-
-
Facilities/Midstream Engineer - ND (Bakken & ThreeForks) / WY (Sussex, Shannon & Muddy)
-
2012 - 2014
◆ Directly managed (5) on-site construction/automation managers and multiple third-party contractors exceeding 35 individuals. Scope of projects required multidisciplinary communication between every department in the company. Worked very closely with operations to compile, produce and instruct operational procedures in the field.◆ Worked with a team of engineers and operators to provide solutions for the accurate measurement of oil, water and gas for allocation purposes on (10+) central tank batteries. Setup a reporting structure for allocation and calibration tests and produced a workflow diagram for the proper reporting of regulatory mandated forms. ◆ Prepared freezing protection alternatives for equipment and piping infrastructure during harsh North Dakota winters. Provided accident investigation support and analysis to multiple departments within the company.◆ Worked closely with a third-party company on the implementation of an oil gathering system which required the commingling of several facilities to significantly reduce wellsite equipment and capital costs. Commingled production of 54+ wells in order to connect directly to the oil gathering system.
-
-
-
-
Project Manager - Sustaining Engineering
-
Jun 2012 - Aug 2012
◆ Worked to troubleshoot and mitigate systematic errors on master meter calibration stands utilized for the QAQC of new Coriolis meters. ◆ Worked to troubleshoot and mitigate systematic errors on master meter calibration stands utilized for the QAQC of new Coriolis meters.
-
-
-
CoorsTek
-
Glass, Ceramics and Concrete Manufacturing
-
700 & Above Employee
-
Design/Mechanical Engineering Intern
-
May 2011 - Dec 2011
◆ Supported a group of engineers in the development of a commercial electrolysis system for the on-site production of a catalyst used in the bio-diesel industry. ◆ Troubleshooted problems and performed system maintenance on the on-site prototype skid. Utilized special training in handling and cleaning dangerous chemicals. ◆ Designed and CAD modeled a dynamic platform for the system which utilized commercially available products and custom parts to create an efficient and uncomplicated way to perform system maintenance. ◆ Contracted out materials for the above system with an allocation of $75,000, but completed the design 50% under budget. ◆ Developed testing processes and conducted reliability and quality assurance tests on individual cartridges as well as performed overall equipment maintenance.
-
-
-
Cordillera Energy Partners LLC
-
United States
-
Oil and Gas
-
Drilling/Completion Engineering Intern - TX/OK (Granite Wash, Tonkawa, Cleveland & Marmaton)
-
May 2008 - Aug 2010
Cordillera Energy Partners is an independent oil and gas company comprised of professionals from each respected area of the E&P industry working in a fast paced and professional environment in order to achieve the highest level of production and efficiency. While working at Cordillera, some of my job duties included:◆ Supported engineering management in daily system operations, attended interoffice and vendor meetings and provided feedback for the drilling & completion departments.◆ Researching and compiling an assessment on horizontal down-hole sidetracks based on economics, performance, days lost and vendor performance. Created an extensive step by step report for each well which had difficulties sidetracking and compiled a list of vendors, bits used vs. performance, and provided improvements for future wells in a final presentation to engineering management. ◆ Visited drilling operations in Pampa, Texas and interacted with rig personnel and the drilling supervisor. Oversaw drilling, bit change and tripping pipe operations while out in the field and viewed the rigging up of a slickwater frac job.◆ Visited completion operations in Elk City, Oklahoma for a CO2 frac job. Was on-site for two days supervising the frac job, assisting the controllers in the trucks as well as personnel working the sand dumpers, pumps and ball frac plugs. Monitored the dropping of the balls to assure management that each fracing zone was properly plugged off.◆ Compiled correspondence and reviewed documents for litigation and provided the engineering department with a preliminary failure assessment of a separated section of casing based on crack propagation and visual tension marks. I was responsible for providing litigation with a history of drilling the well and other supporting documents and researched possible reasons for the casing to separate.
-
-
-
-
Drilling/Completions Engineering Intern - TX/OK (Granite Wash, Tonkawa, Cleveland & Marmaton)
-
May 2008 - Aug 2010
◆ I was accountable for filling out, filing and compiling state regulatory forms for a number of completed and operating wells drilled during an accelerated time of operation. I was liable for the accuracy of these forms and spent an extensive time researching and reviewing supporting documents for correctness. Through doing this, I learned that making multiple copies, both physically and electronically is good practice within the industry.◆ I prepared drilling procedures for each new well and created templates for future wells. I interacted with drilling supervisors and foremen regarding any difficulties understanding the procedural documents.◆ Created well-bore diagrams for existing wells and used them to assist the completions manager with workover procedures. I sat in on live frac jobs, took notes and shared them with the completions manager. He taught me how to pick the zones for which each well would be fraced using gamma ray and density logs. I sat in on a vendor meeting about radiation tracing within each zone and was able to see the tracing pellets go down the wellbore while on the CO2 frac.◆ I reviewed and corrected each morning report that was filed from the drilling rigs and contacted foremen in order to obtain the correct readings for the incomplete forms. ◆ I cross-checked vendor invoices with contracts and past invoices to assure that the company was being charged correctly. I brought forth discrepancies to the upper management so that they may pursue further action. I retained expenditures of $100,000 from vendor invoices as a result of this cross-checking.
-
-
Education
-
University of Colorado Boulder
B.S., Mechanical Engineering -
Mountain Vista High School
Community
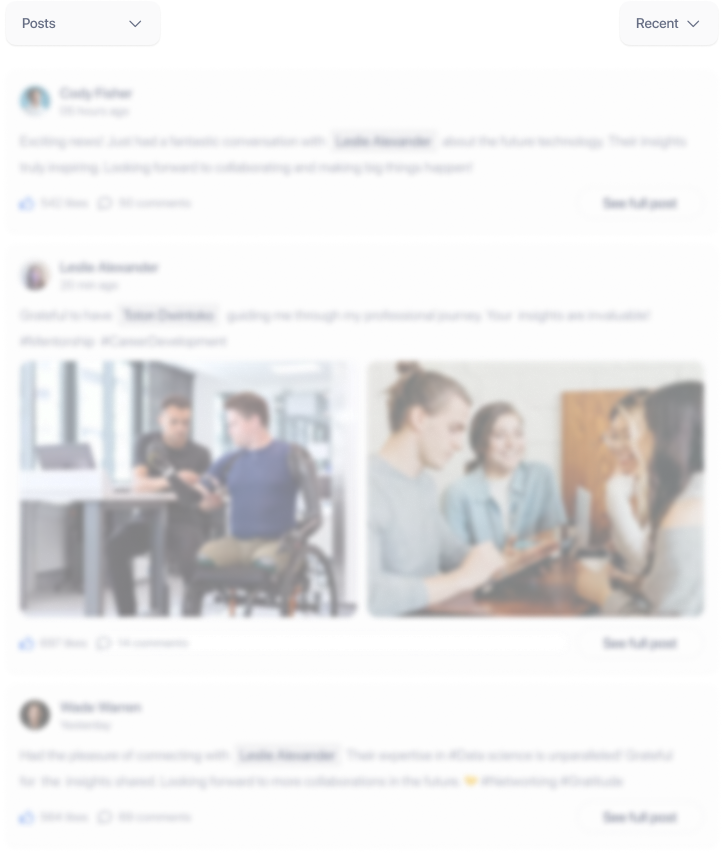