Vicki Koo
Lead Auditor at DAS Certification Singapore Pte Ltd- Claim this Profile
Click to upgrade to our gold package
for the full feature experience.
-
English, Chinese, Malay -
Topline Score
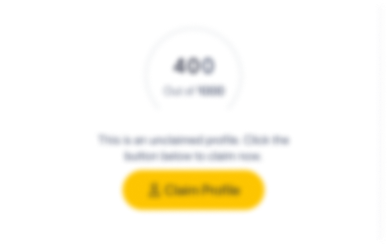
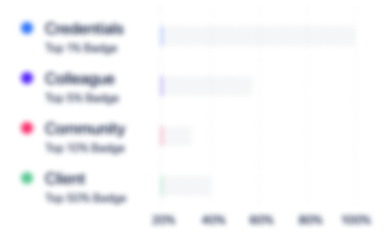
Bio
0
/5.0 / Based on 0 ratingsFilter reviews by:
Credentials
-
ISO 45001 Lead Auditor
SGS -
ISO 9001 Lead Auditor - Quality Certification
BSI Neville Clarke – A BSI Professional Services Company -
Iso 14001 Lead Auditor
BSI Neville Clarke – A BSI Professional Services Company
Experience
-
DAS Certification Singapore Pte Ltd
-
Singapore
-
Business Consulting and Services
-
1 - 100 Employee
-
Lead Auditor
-
May 2012 - Present
- Conduct certification and surveillance audits for ISO 9001, ISO 14001 & ISO 45001 in Singapore, Malaysia, Myanmar and Laos. Industry audited included construction, shipyard / marine, trading, manufacturing, training, engineering, social activities, etc - Perform Audit Planning, Document and Records Review, Site Visit Audit, Evaluation of conformance to International and local standards, Report Preparation, maintain audit log, draw up competency report for industry audited - Involved in marketing matters, handle sales enquiry and quotation issuance - Involved in training related matters - Assist to review audit reports - Assist in technical- related matters and other business assignments (such as development of training and company procedures) - Initiate the business development for Malaysia market - Assist to setup, oversee and manage Malaysia branch operation and audit Show less
-
-
-
-
QA Engineer
-
Oct 2010 - Mar 2012
~HOD in overall operation of QA Department. ~Interface with internal and external customer for quality issue, quality improvement and technical requirement. ~Ensure compliance of Quality Management System in accordance to the ISO 9001:2008 and internal procedure requirement. ~Interface with internal and external QMS audit. ~Lead and manage a team of QA/QC. ~HOD in overall operation of QA Department. ~Interface with internal and external customer for quality issue, quality improvement and technical requirement. ~Ensure compliance of Quality Management System in accordance to the ISO 9001:2008 and internal procedure requirement. ~Interface with internal and external QMS audit. ~Lead and manage a team of QA/QC.
-
-
-
-
QA Engineer
-
Dec 2008 - Oct 2009
~ Lead and manage a team of Foreman, Technician and inspector in Incoming, In process and outgoing quality control. ~ Responsible for products' quality improvement, monitor, data analysis, review and drive for corrective action plan. ~ Interface with internal & external customer/ vendor for all quality issue. Perform quality data analysis and drive for quality improvement. ~ Ensure compliance of Quality Management Systems in accordance to the ISO/TS16949:2002 and internal procedure requirements. ~ Responsible for ISO system audit and provide corrective action for audit finding. ~ Responsible for Equipments’ Inspection calibration and verifications. Show less
-
-
-
-
QA Executive
-
Jul 2006 - Nov 2008
~ Manage, plan, control and ensure that the quality aspects are in conformance with specified requirements for incoming, in-process and finished products to be in alignment with the company Main Thing that is to achieve 100% IN-FULL-ON-TIME (IFOT) of Consistent Quality MDF. ~ Function as a Deputy Management Representative of the company Quality Management System in areas. Also act as an ISO Coordinator to coordinate the ISO 9001 (QMS) document. ~ Plan and organize the Internal Quality Audit for ISO 9001 (QMS), also involve in ISO 14001 & OHSAS 18000 (EMS & OHSAS) Internal Audit. To upkeep and improve on the ISO 9001 quality system to ensure conformance to the standard requirement at all times. Follow-up on all non-compliances/discrepancies raised, initiate and execute corrective action plans to remedy these non-compliances. ~ Manage the laboratory testing, R&D work, involved in production on trial project, process and quality improvement. ~ To investigate the root cause for any nonconformance related to product quality. ~ Act as a technical service for customer new requirements; handle any customer complaint related to technical issue, provide information and solution to customer which related to their product. Show less
-
-
Education
-
Universiti Putra Malaysia
Bachelor's degree, Forestry Science -
University Putra Malaysia
Bachelor's degree, Forestry Science -
University of Putra Malaysia
Diploma, Foresty Science
Community
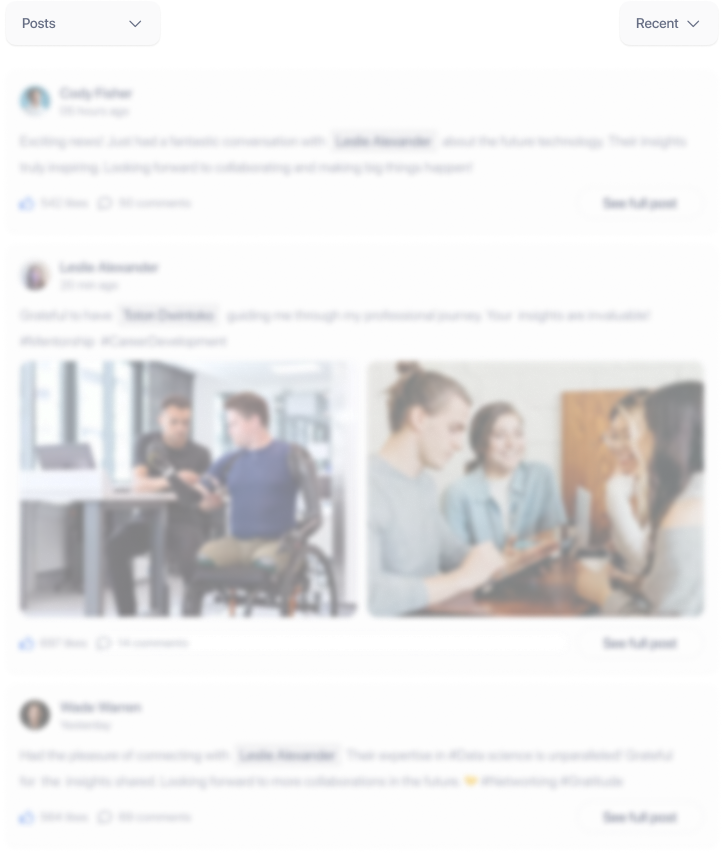