Vern Holden
Business Adviser at HTK Group Community- Claim this Profile
Click to upgrade to our gold package
for the full feature experience.
Topline Score
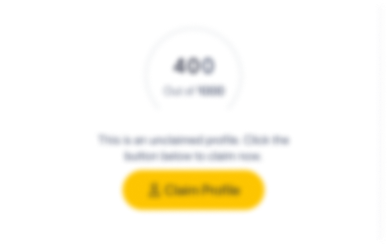
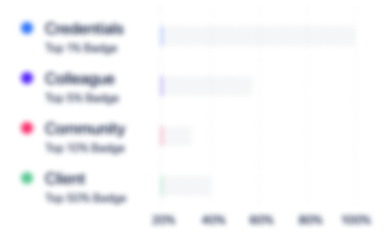
Bio
0
/5.0 / Based on 0 ratingsFilter reviews by:
Experience
-
-
Business Adviser
-
Nov 2020 - Present
HTK Group specialises in working with Māori and indigenous groups to build better futures. HTK Group works along-side whānau, businesses, corporates, hapū/iwi, institutions and not-for-profits creating tailor-made, innovative and dynamic solutions for their business. HTK Group specialises in working with Māori and indigenous groups to build better futures. HTK Group works along-side whānau, businesses, corporates, hapū/iwi, institutions and not-for-profits creating tailor-made, innovative and dynamic solutions for their business.
-
-
-
SKOPE Industries Limited
-
United Kingdom
-
Manufacturing
-
Manufacturing Improvement Leader
-
Dec 2017 - May 2020
Oversee all aspects of production management, continuous improvement, quality management, and health and safety while leading a team of nine process leaders and 90 members across nine departments, two of which operated 24/7.Key Achievements• Established new rules in the manufacturing process to maximise a stable flow of finished products by at least 15%• Championed the implementation of manufacturing improvement projects and the continued development of TOC throughout the manufacturing department• Improved the manufacturing and supply of components to the assembly process• Enhanced operational efficiency and reducing the overall waste in the production department• Coordinated with the Design Team to integrate the assembling of new products• Liaised with the Purchase Department for negotiating with and determining the most effective manufacturers and suppliers of materials, parts and equipment• Monitored direct labour and expenses of all consumables• Deployed a standardised flowchart for the quality check of parts and products• Motivated and implemented a performance-driven culture for increasing the team’s productivity• Collaborated with the IT Team for introducing, updating, and improving work reports• Documented and improved the efficiency of the standard operating practices across the factory• Deployed enhanced quality and accountability systems for capturing and analysing production issues and increasing quality• Oversaw daily work requirements of production schedule, team members, delegating and prioritising teams for maximising production flow• Coordinated with all support functions to ensure the supply of parts, quality of finish goods and health and safety regulations are all meet while achieving the desired productivity levels• Motivated and trained staff to enhance team and individual productivity• Investigated incidences and developed safety objectives to create a safer work environment Show less
-
-
Special Project Manager
-
Jan 2014 - Dec 2017
Executing several engineering/manufacturing projects at a time, led various teams for successfully commissioning improvements across the manufacturing facility.Key Achievements• Improved the accuracy of the BOM construction and manufacturing process by timing the assemblies throughout the factory, updating the routing times in JDE• Organised and executed health and safety training programs for all staff members• Led a team in the Customs Department for creating a project plan for designing, manufacturing, and introducing new products into the market• Liaised with customers for creating contract prices• Sold residual heating stock in the retail market, generating an additional income of $30,000• Organised and trained the design team on project planning and management• Assisted the sales and marketing team in carrying out market research studies, in addition to supporting the production team in manufacturing new products• Designed and implement a parts ordering system for smoothing production demand• Streamlined the ordering rework process, allowing data collection and analysis• Initiated a project for improving the collaboration between the Production and Design teams, creating better information flow and introduction of new productsKey Responsibilities• Managed a wide range of special projects aimed at streamlining the design, production, and HR processes across the factory• Defined the project scope, and planned schedules for executing them, on time• Partnered with the senior leadership to analyse bottlenecks and complexity of operations for suggesting improvements• Established project milestones, costs and overall objectives while managing resources to achieve business results• Identified and mitigated project risks, in addition to tracking and reporting project progress to the senior leadership• As the single point of contact analysed and recommended solutions to resolve technical problems Show less
-
-
Spare Parts Manager
-
Jan 2013 - Dec 2013
Led a team of three customer service representatives and three dispatchers for managing spare parts, including controlling inventory to dispatching and delivering customer service.Key Achievements• Streamlined the inventory controlling processes, reducing the overall inventory levels by over 40% while improving availability of parts needed for customers’ orders• Reduced order-to-dispatch times by over 20%• Increased the on-time dispatch of orders from 70% to over 90%• Created and implemented standards for enhancing customer service and satisfactionKey Responsibilities• Analysed the current replenishment process and spare parts inventory levels for creating, implementing, and ensuring the timely availability of replenishment stock• Carried out monthly audits of the physical inventory and reconciled details in the inventory management software• Planned and delegated tasks to dispatchers/customer service representatives• Worked closely with and visited key customers for improving relationships and sales Show less
-
-
Heating Sales Manager
-
Jun 2010 - Dec 2012
Working closely with the Sales Manager of ANZ revitalised the sales of the heating products.Key Achievements• Increased sales of the heating division by over 20% over one-and-a-half years• Created an innovative remuneration scheme for improving the sales team’s focus and productivity• Improved customer satisfaction by maintaining healthy relationships with clients and gaining a deeper understanding of their businessKey Responsibilities• Created call cycles and defined Key Performance Indicators (KPIs) for the sales team• Championed a long-term strategy for selling heating products and closing high-value deals by developing productive relationships with critical business partners• Resolved customer issues, delivery problems and shipment concerns• Mentored and monitored the performance of all team members• Maintained a client database and presented revenue/sales performance reports to the senior management/board representatives Show less
-
-
Manager – Throughput Projects
-
Jun 2008 - Jun 2010
Collaborated with multiple teams on a wide range of sales and costing projects.Key Achievements• Created an innovative pricing model for selling SKOPE’s spare parts• Presented and trained critical stakeholders on the Make-to-Availability (MTA) concept• Implemented MTA for spare parts, increasing sales to critical accounts by 50%• Created bespoke pricing models for customised refrigeration cabinets for enhancing revenues
-
-
Process Leader
-
Jul 2006 - Jun 2008
As the leader of two assembly lines, managed the manufacturing process of the Ladder Towel Rails (LTR) and Heaters.Key Achievements• Introduced TOC and Lean manufacturing techniques for improving productivity by 100%, from 40 LTRs to 80 LTRs with the existing team• Implemented a dashboard to provide a bird’s eye view of production while enhancing communication with the senior leadership• Defined and deployed daily productive goals, capturing the details in the dashboard• Built self-driven teams for independently/collectively achieving production targets• Delivered parts from the store, as per a predefined schedule, ensuring their on-time availability at the production floor, every time Show less
-
-
Education
-
Massey University
Bachelor of Technology (BTech) Hons., Manufacturing and Industrial Technology -
PNBHS
Community
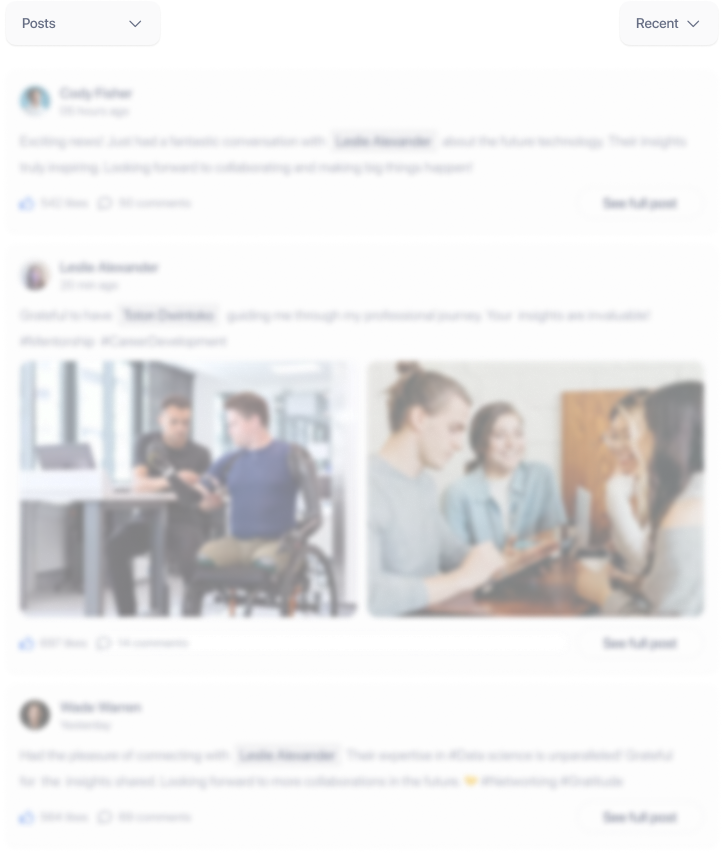