Varun Velpula
Senior Machine Learning Engineer at Third Insight- Claim this Profile
Click to upgrade to our gold package
for the full feature experience.
-
English Full professional proficiency
-
Telugu Native or bilingual proficiency
-
French Elementary proficiency
-
Hindi Elementary proficiency
Topline Score
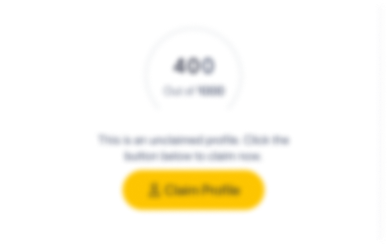
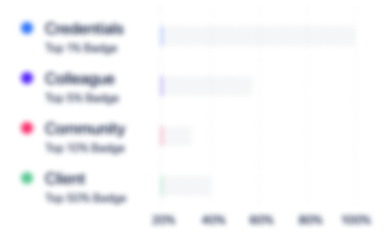
Bio


Experience
-
Third Insight
-
United States
-
Research Services
-
1 - 100 Employee
-
Senior Machine Learning Engineer
-
Jul 2021 - Present
-
-
-
University of Pennsylvania
-
United States
-
Higher Education
-
700 & Above Employee
-
Teaching Assistant
-
Jan 2021 - May 2021
Teaching Assistant for CIS 522 Deep Learning for Data ScienceI am responsible for content creation for the classes , grading and for guiding a group of 10 students during the classes every week.
-
-
Graduate Research Assistant, mLab
-
Jan 2021 - May 2021
I am currently working in mLab under Prof. Rahul Mangharam on a project on the F1tenth racing car and simulator.I am working on implementing the Model Predictive Control (MPC) stack for the autonomous F1tenth racecar. The aim is to integrate a number of MPC methodologies with the current software stack as an API which gives the user an option to choose between different MPC methods.I am currently working on implementing the Learning based MPC for the simulator. The final goal is to implement it on the actual autonomous racecar. Show less
-
-
-
-
Graduate Research Assistant, modLab
-
May 2020 - Sep 2020
Research Assistant in ModLab under Prof Mark Yim. I worked on the modular aerial robots project - ModQuad As part of research work during the summer in ModLab, I worked on a simulation based project to learn suitable trajectories for quadcopters attached with a gripper. I developed a policy search algorithm to determine these suitable trajectory waypoints and the yaw angle of quadcopter which would affect the orientation thus affecting the gripping action. I designed the four bar gripper attachment for the quadcopter on Coppelia Robotics simulator and attached it about the vertical axis of the quadcopter. The policy gradient learning script was run using python and was linked with the simulator using the Coppelia Robotics Python API library. We achieved the learning of trajectories from a point in space to the goal while minimizing the cost function, which is the distance to goal. The yaw angle was checked if the gripping action was successful at the end once the quadcopter reached the goal. Show less
-
-
-
CSD ROBOCON NITK
-
India
-
Robotics Engineering
-
1 - 100 Employee
-
Mechanical Design Engineer
-
Dec 2017 - May 2019
Part of the mechanical design, development and prototyping team for the team Part of the mechanical design, development and prototyping team for the team
-
-
-
Indian Institute of Science (IISc)
-
India
-
Research
-
700 & Above Employee
-
Summer Research Intern
-
May 2018 - Jul 2018
Worked under the guidance of Prof Ashwini Ratnoo. I worked on the control of Unmanned Aerial Vehicles (UAVs) in an indoor environment. A motion capture system set up in the lab was used to localize the UAVs. The noise from the IMU sensor (accelerometer and gyroscope) data was removed using a Kalman filter. The UAV parameters were controlled using PID tuners. Waypoint guidance law was implemented and tested this system. Worked under the guidance of Prof Ashwini Ratnoo. I worked on the control of Unmanned Aerial Vehicles (UAVs) in an indoor environment. A motion capture system set up in the lab was used to localize the UAVs. The noise from the IMU sensor (accelerometer and gyroscope) data was removed using a Kalman filter. The UAV parameters were controlled using PID tuners. Waypoint guidance law was implemented and tested this system.
-
-
-
ABB
-
Azerbaijan
-
Banking
-
700 & Above Employee
-
Summer Internship
-
May 2017 - Jul 2017
Worked on the integration of humanoid robotic arm with ABB robot IRB 1600. The finger motion of the arm was based on the principle of underactuation. Nylon string wounded onto the servo motorhead on one side and attached to the tip of the finger on the other end was used to achieve this. A hierarchical control scheme was implemented. The signals for the finger motions are received from the robot controller via an Arduino microcontroller. Worked on the integration of humanoid robotic arm with ABB robot IRB 1600. The finger motion of the arm was based on the principle of underactuation. Nylon string wounded onto the servo motorhead on one side and attached to the tip of the finger on the other end was used to achieve this. A hierarchical control scheme was implemented. The signals for the finger motions are received from the robot controller via an Arduino microcontroller.
-
-
Education
-
University of Pennsylvania
Master of Science - MS, Robotics -
National Institute of Technology Karnataka
Bachelor’s Degree, Mechanical Engineering -
Abu Dhabi Indian School
High School, Science
Community
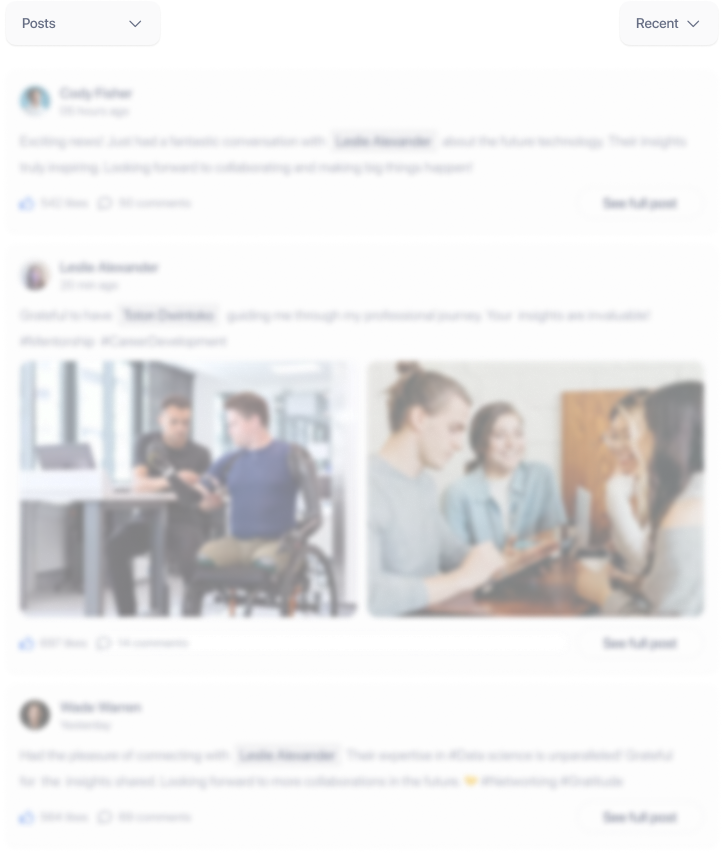