Varathan Thuraisinkam B. Eng., MBA, CQE, CSSBB
Corporate Quality Assurance Manager at Iroquois Industries Inc.- Claim this Profile
Click to upgrade to our gold package
for the full feature experience.
-
English -
Topline Score
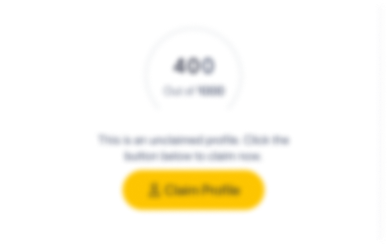
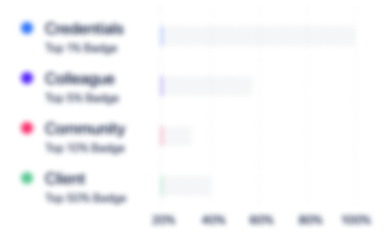
Bio

Anna Pachut
I have had the opportunity to work with Varathan in the capacity of a parts supplier to the organization he was employed in previously. Varathan is extremely technical and has the ability to communicate - complies ideas with any level within an organization. Varathan is one of those rare individuals that take technical knowledge, communication and analytical skills and get the job done in an extremely efficient manor. Varathan is extremely fair and bases his decisions on facts and treats people with the respect they require. I personally consider Varathan as one of the best Quality Professional, Program Manager, etc. that I have ever had the pleasure to be associated with. Any organization that would have the opportunity to hire Varathan would be getting a GREAT asset. September 12, 2009

Bill Pollack
Varathan is a very dedicated professional and did contribute to the sucessful launch of many complex programs. His positive attitude and work ethic make Varathan a truly valuable asset.

Anna Pachut
I have had the opportunity to work with Varathan in the capacity of a parts supplier to the organization he was employed in previously. Varathan is extremely technical and has the ability to communicate - complies ideas with any level within an organization. Varathan is one of those rare individuals that take technical knowledge, communication and analytical skills and get the job done in an extremely efficient manor. Varathan is extremely fair and bases his decisions on facts and treats people with the respect they require. I personally consider Varathan as one of the best Quality Professional, Program Manager, etc. that I have ever had the pleasure to be associated with. Any organization that would have the opportunity to hire Varathan would be getting a GREAT asset. September 12, 2009

Bill Pollack
Varathan is a very dedicated professional and did contribute to the sucessful launch of many complex programs. His positive attitude and work ethic make Varathan a truly valuable asset.

Anna Pachut
I have had the opportunity to work with Varathan in the capacity of a parts supplier to the organization he was employed in previously. Varathan is extremely technical and has the ability to communicate - complies ideas with any level within an organization. Varathan is one of those rare individuals that take technical knowledge, communication and analytical skills and get the job done in an extremely efficient manor. Varathan is extremely fair and bases his decisions on facts and treats people with the respect they require. I personally consider Varathan as one of the best Quality Professional, Program Manager, etc. that I have ever had the pleasure to be associated with. Any organization that would have the opportunity to hire Varathan would be getting a GREAT asset. September 12, 2009

Bill Pollack
Varathan is a very dedicated professional and did contribute to the sucessful launch of many complex programs. His positive attitude and work ethic make Varathan a truly valuable asset.

Anna Pachut
I have had the opportunity to work with Varathan in the capacity of a parts supplier to the organization he was employed in previously. Varathan is extremely technical and has the ability to communicate - complies ideas with any level within an organization. Varathan is one of those rare individuals that take technical knowledge, communication and analytical skills and get the job done in an extremely efficient manor. Varathan is extremely fair and bases his decisions on facts and treats people with the respect they require. I personally consider Varathan as one of the best Quality Professional, Program Manager, etc. that I have ever had the pleasure to be associated with. Any organization that would have the opportunity to hire Varathan would be getting a GREAT asset. September 12, 2009

Bill Pollack
Varathan is a very dedicated professional and did contribute to the sucessful launch of many complex programs. His positive attitude and work ethic make Varathan a truly valuable asset.

Credentials
-
Certified Six Sigma Black Belt (CSSBB)
American Society For Quality (ASQ)Dec, 2012- Oct, 2024 -
ASQ Certified Quality Engineer
ASQ - World HeadquartersJun, 1992- Oct, 2024 -
ASQ Certified Six Sigma Black Belt
ASQ - World HeadquartersOct, 2009- Oct, 2024 -
Certified Quality Engineer (CQE)
American Society For Quality (ASQ)Jun, 2010- Oct, 2024
Experience
-
Iroquois Industries Inc.
-
Motor Vehicle Manufacturing
-
1 - 100 Employee
-
Corporate Quality Assurance Manager
-
Nov 2017 - Present
Corporate Quality Assurance Manager, USA Division, Managing 8 Plants in Quality Assurance, and Quality Systems. Corporate Quality Assurance Manager, USA Division, Managing 8 Plants in Quality Assurance, and Quality Systems.
-
-
-
-
Program Manager
-
Jan 1998 - Jan 2021
Program Manager and Instructor for Certificate in Quality Assurance Program. Subjects: • Quality Concepts • Statistical Process Control ( SPC ) • Management of Quality Assurance • Reliability of Quality Assurance • Quality Auditing • Advanced Statistical Methods • Inspection, Test, Metrology, and Blue Print Reading • Problem Solving Techniques • Quality Engineering Program Manager and Instructor for Certificate in Quality Assurance Program. Subjects: • Quality Concepts • Statistical Process Control ( SPC ) • Management of Quality Assurance • Reliability of Quality Assurance • Quality Auditing • Advanced Statistical Methods • Inspection, Test, Metrology, and Blue Print Reading • Problem Solving Techniques • Quality Engineering
-
-
-
ZF
-
Canada
-
Technology, Information and Internet
-
Customer Quality Manager
-
Feb 2016 - Oct 2017
Customer: FCA (Stellantis). Program Launch, and Quality Assurance - Plants in North America, Mexico, China, and Europe. Customer: FCA (Stellantis). Program Launch, and Quality Assurance - Plants in North America, Mexico, China, and Europe.
-
-
-
Chrysler
-
United States
-
PSO / AQP Manager/ Quality Manager
-
Aug 2011 - Feb 2016
Lead Program Launch at Warren Stamping Plant. Lead Program Launch at Warren Stamping Plant.
-
-
-
Adavanced Assembly Products Inc.
-
United States
-
Motor Vehicle Manufacturing
-
1 - 100 Employee
-
Quality Manager
-
Mar 2011 - Aug 2011
Managing Quality Dept. at Plant 1 & 2. Managing Quality Dept. at Plant 1 & 2.
-
-
-
-
Senior Quality Engineer/ Quality Supervisor
-
Dec 2009 - Mar 2011
Responsibilities included developing quality systems, performing process capability studies, Control plans, APQP, PFMEA, PPAP submissions, quality training, quality audit, preparing Process and quality instructions, continuous improvement, dealing with customers and Suppliers on quality issues and working on new launches with advanced engineering in Body Systems. In-charge of Quality Laboratory. Responsibilities included developing quality systems, performing process capability studies, Control plans, APQP, PFMEA, PPAP submissions, quality training, quality audit, preparing Process and quality instructions, continuous improvement, dealing with customers and Suppliers on quality issues and working on new launches with advanced engineering in Body Systems. In-charge of Quality Laboratory.
-
-
-
-
Supplier / Quality Engineer
-
Nov 2008 - Feb 2009
Responsibilities included developing quality systems, performing process capability studies, Control plans, APQP, PFMEA, PPAP submissions, quality training, quality audit, preparing Process and quality instructions, continuous improvement, dealing with customers and Suppliers on quality issues and working on new launches with advanced engineering in Injection Moulding, and Assembly of polybond headliners. Responsibilities included developing quality systems, performing process capability studies, Control plans, APQP, PFMEA, PPAP submissions, quality training, quality audit, preparing Process and quality instructions, continuous improvement, dealing with customers and Suppliers on quality issues and working on new launches with advanced engineering in Injection Moulding, and Assembly of polybond headliners.
-
-
-
Metaldyne Corporation
-
Airlines and Aviation
-
Corporate Supplier Quality Engineer
-
Jan 2006 - Aug 2008
Working for Corporate Global Purchasing Group. Responsibilities include managing suppliers for Power train / NVH plants. Involved in supplier selection, risk assessment, Quality System audits, PSO, APQP, PPAP submissions, Program / Product launches at suppliers, quality issues, and Continuous Improvement activities at Suppliers. Managed Suppliers for Six (6) including Plants in Mexico, and China. Working for Corporate Global Purchasing Group. Responsibilities include managing suppliers for Power train / NVH plants. Involved in supplier selection, risk assessment, Quality System audits, PSO, APQP, PPAP submissions, Program / Product launches at suppliers, quality issues, and Continuous Improvement activities at Suppliers. Managed Suppliers for Six (6) including Plants in Mexico, and China.
-
-
-
-
Quality Engineer
-
May 2003 - Dec 2005
Responsibilities included developing quality systems, performing process capability studies, control plans, APQP, PFMEA, PPAP submissions, quality training, quality audit, preparing process and quality instructions, continuous improvement, dealing with customers and suppliers on quality issues and working on new launches with advanced engineering in machining, cold and warm forming. Responsibilities included developing quality systems, performing process capability studies, control plans, APQP, PFMEA, PPAP submissions, quality training, quality audit, preparing process and quality instructions, continuous improvement, dealing with customers and suppliers on quality issues and working on new launches with advanced engineering in machining, cold and warm forming.
-
-
-
Ford Motor Company
-
United States
-
Motor Vehicle Manufacturing
-
700 & Above Employee
-
Supplier Tech. Assistance / Warranty Engineer
-
Jan 2001 - Mar 2003
Responsibilities included launching of Warranty Reduction Program at suppliers, and performing as a liaison to interface with suppliers / dealers and Ford management, tear down analysis, serve as a technical expert on evaluation of warranty parts for charging back dealers, interface with Supplier Technical Assistance Engineers on service / production parts' warranty issues, supported Quality Systems ( Q1 / QS9000 / ISO9000 ) effort within PS&L, performed facility reviews at potential new… Show more Responsibilities included launching of Warranty Reduction Program at suppliers, and performing as a liaison to interface with suppliers / dealers and Ford management, tear down analysis, serve as a technical expert on evaluation of warranty parts for charging back dealers, interface with Supplier Technical Assistance Engineers on service / production parts' warranty issues, supported Quality Systems ( Q1 / QS9000 / ISO9000 ) effort within PS&L, performed facility reviews at potential new program suppliers, followed-up corrective actions ( 8-D ) with suppliers, and provided technical support to engineering, sales / marketing,& purchasing. • Reduced Warranty cost by 1.0 million every year for two (2) years on Engines / Transmissions by launching Warranty Reduction Program at Suppliers. Show less Responsibilities included launching of Warranty Reduction Program at suppliers, and performing as a liaison to interface with suppliers / dealers and Ford management, tear down analysis, serve as a technical expert on evaluation of warranty parts for charging back dealers, interface with Supplier Technical Assistance Engineers on service / production parts' warranty issues, supported Quality Systems ( Q1 / QS9000 / ISO9000 ) effort within PS&L, performed facility reviews at potential new… Show more Responsibilities included launching of Warranty Reduction Program at suppliers, and performing as a liaison to interface with suppliers / dealers and Ford management, tear down analysis, serve as a technical expert on evaluation of warranty parts for charging back dealers, interface with Supplier Technical Assistance Engineers on service / production parts' warranty issues, supported Quality Systems ( Q1 / QS9000 / ISO9000 ) effort within PS&L, performed facility reviews at potential new program suppliers, followed-up corrective actions ( 8-D ) with suppliers, and provided technical support to engineering, sales / marketing,& purchasing. • Reduced Warranty cost by 1.0 million every year for two (2) years on Engines / Transmissions by launching Warranty Reduction Program at Suppliers. Show less
-
-
-
-
Quality Engineer
-
Sep 1999 - Nov 2000
Responsibilities included developing quality systems, PPAP submissions, performing process capability studies, control plans, PFMEA, quality training, quality audit, preparing process and quality instructions, continuous improvement, dealing with customers and suppliers on quality issues and work on new launches with advanced engineering. • Maintained zero PPM on Toyota program. • Successful launch of two Toyota programs. • Passed QS 9000 audit every six months. • Implemented… Show more Responsibilities included developing quality systems, PPAP submissions, performing process capability studies, control plans, PFMEA, quality training, quality audit, preparing process and quality instructions, continuous improvement, dealing with customers and suppliers on quality issues and work on new launches with advanced engineering. • Maintained zero PPM on Toyota program. • Successful launch of two Toyota programs. • Passed QS 9000 audit every six months. • Implemented effective training program for operators to reduce scrap by 30%. Show less Responsibilities included developing quality systems, PPAP submissions, performing process capability studies, control plans, PFMEA, quality training, quality audit, preparing process and quality instructions, continuous improvement, dealing with customers and suppliers on quality issues and work on new launches with advanced engineering. • Maintained zero PPM on Toyota program. • Successful launch of two Toyota programs. • Passed QS 9000 audit every six months. • Implemented… Show more Responsibilities included developing quality systems, PPAP submissions, performing process capability studies, control plans, PFMEA, quality training, quality audit, preparing process and quality instructions, continuous improvement, dealing with customers and suppliers on quality issues and work on new launches with advanced engineering. • Maintained zero PPM on Toyota program. • Successful launch of two Toyota programs. • Passed QS 9000 audit every six months. • Implemented effective training program for operators to reduce scrap by 30%. Show less
-
-
-
-
Quality Engineer
-
May 1998 - Jul 1999
Responsibilities included performing process capability studies, PFMEA, PPAP submissions, process control plans, G R & R studies, APQP, quality training, quality audit, continuous improvement and working with customers and suppliers on quality issues. • Reduced scrap by 30% through problem solving activities and training programs. Responsibilities included performing process capability studies, PFMEA, PPAP submissions, process control plans, G R & R studies, APQP, quality training, quality audit, continuous improvement and working with customers and suppliers on quality issues. • Reduced scrap by 30% through problem solving activities and training programs.
-
-
Education
-
American Society for Quality (ASQ)
Certified Six Sigma Black Belt, and Certified Quality Engineer -
University of Michigan
MBA, Business Administration -
American Society for Quality (ASQ)
Certified Quality Engineer -
Ryerson University
Quality Assurance -
Ahmadu Bello University
B. Eng.( Hons), Mechanical Engineering -
Colombo Hindu College
N.C.G.E. / G.C.E.(A/L)., Science / Engineering
Community
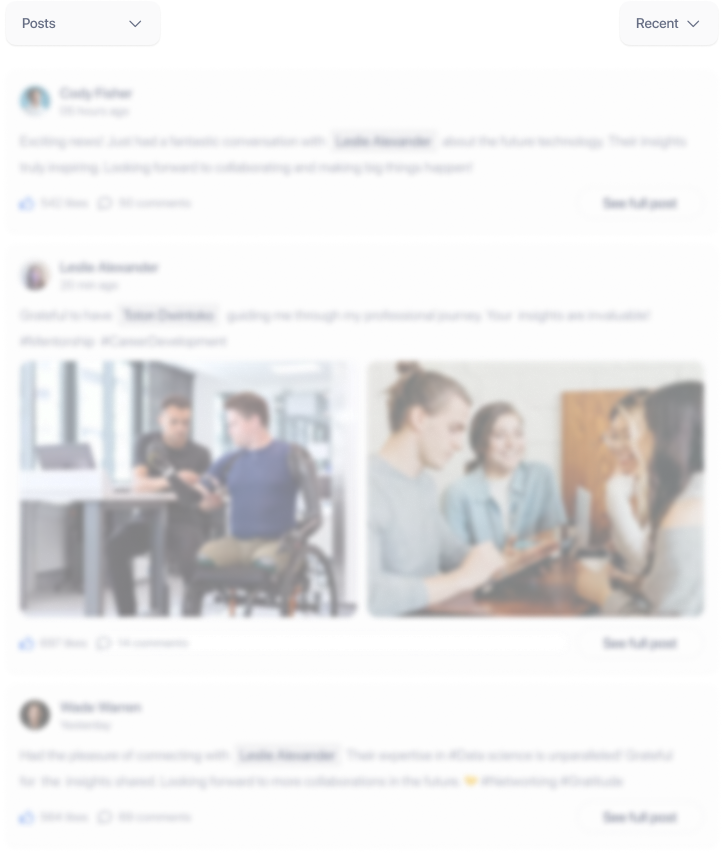