Vanessa Carolina Prieto Parra
Demand and Supply Planner at Essence Group Sydney- Claim this Profile
Click to upgrade to our gold package
for the full feature experience.
-
Spanish Native or bilingual proficiency
-
English Full professional proficiency
Topline Score
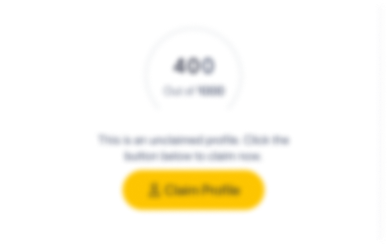
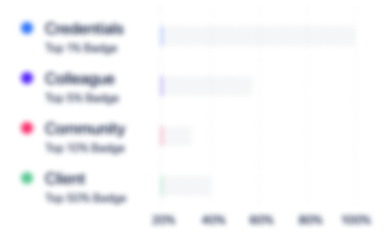
Bio
0
/5.0 / Based on 0 ratingsFilter reviews by:
Experience
-
Essence Group Sydney
-
Australia
-
Health, Wellness & Fitness
-
1 - 100 Employee
-
Demand and Supply Planner
-
Feb 2023 - Present
-
-
-
Alsea
-
Mexico
-
Restaurants
-
700 & Above Employee
-
Planning and Replanishment Manager (Argentina - Uruguay)
-
Feb 2020 - Dec 2022
-
-
S&OP Sr Analyst
-
Sep 2019 - Feb 2020
-
-
Analista Sr. Supply Chain Performance
-
Apr 2019 - Aug 2019
-
-
-
Positivo BGH
-
Argentina
-
Computer Hardware Manufacturing
-
1 - 100 Employee
-
Analista Supply Chain
-
Jan 2018 - Dec 2018
• Leader of the S&OP (Sales and operations planning) process, ensuring the fulfillment of task by the involved areas as product development, finance and after sales. • Provide the updated forecast through the analysis of current stocks and history sales reports that leads with the production plan, inventory plan, customer lead time plan, new product development plan, and resulting financial plan. • Analyzing the stock of aging products at non-available deposit developing a re-work plan to include them in the sales forecast as obsolete products, establishing a procedure of inventory rotation to avoid the increase of aging products in future. • Establishing a purchase plan according to the forecast for Latin America region, through the analysis of the levels of stock, the transit purchases and the lead time of suppliers. • Responsible for the direction, coordination, implementation and completion of projects related with the supply of technological equipment to educational institutions in LAR region, mainly in ARG & UY while remaining aligned with strategy, procedures and goals of the organization. • Identifying opportunely the risks associated with the fulfillment of the project aim • Presenting to the direction a report with the different alternatives to achieve the projects goals • Developing with the suppliers the shipping plans according to the Gantt Diagram that result in the correct execution of the logistic that meet with the budget requirements, considering the client needs. Show less
-
-
-
Colgate-Palmolive
-
1 - 100 Employee
-
Production Planner, Detergents Plant
-
Sep 2015 - Nov 2017
Plans, schedules and monitors the movement of materials through the production cycle to determine required material purchases Ensure the material availability required to execute the production plan according to the timeline. Develop a production plan according with demand requirements Prepare for and communicate shutdowns, maintenance, schedule changes and supply problems Close follow up with production and procurement team to resolve labor and material shortages, backlogs and other potential schedule interruptions. Manage a fit Inventory level according with the company goals Leader of the sulfonic acid export project in the production plant Manage purchase orders in SAP system and evaluate monthly requirements Show less
-
-
Team Leader, Toliet Soap Bar Plant
-
Sep 2014 - Sep 2015
-Ensure compliance of production process and plans according to plant strategies through the asset utilization balance, reaching production records in the soaps plant- Lead and manages the team to drive them to reach production goals based in quality and productivity guidelines- Responsible to manage daily personnel issues related with organization of work shifts, attendance and vacations.-Use of Shop Floor Reporting as tool for improve the plant performance and report productivity kpis monthly- Leader of the “5S and Visual Work place” standard of the FP&R (Floor Performance & Reliability) program in the soap bar plant focus on improve area conditions- In charge of the step 1 certification to one line in the Soaps plant according to Autonomous Maintenance Standard, leading the root cause analysis meetings and the maintenance interventions- Leader of the “Production Planning” standard of the FP&R (Floor Performance & Reliability) program Total Plant focus on develop a 100% system planning strategy- Coordination and management of team work to assure plant operations- Responsible of the timely close of safety findings according to internal and external standards- Participation and execution of continuous improvement projects and autonomous maintenances in the productive lines and making areas Show less
-
-
Home Care Productivity Engineer
-
Feb 2013 - Aug 2014
- Responsible of the efficiency optimization in productive process through performance analysis and monitoring- Leader of the “Productivity and Continuous Improvement” standard of the FP&R(Floor Performance & Reliability) program in the Home Care plant- Capacity analysis and simulation of equipments utilization scenarios according to the business needs- Identification and calculation of savings projects for the focus factories- Management of productivity, quality and efficiency indicators- Monitoring of material losses and participation in the losses reduction projects during the productive process- Creation of rate routings and work centers in SAP system for the active sku’s in the Home care plantProductivity Show less
-
-
Productivity Engineer, Manufacturing Strategy Department
-
Sep 2011 - Jan 2013
-In Charge of the Material Master: Extend and maintain codes of finished goods and packing materials in SAP system, monitor and resolve daily system interface errors- Support in the monthly report of productivity indicators.- Participation in the implementation of MDGM (Master Data Governance Materials) system in the subsidiary.- Daily report of the products availability in all the warehouses.
-
-
Education
-
Universidad de Carabobo
Engineer's Degree, Industrial Engineering
Community
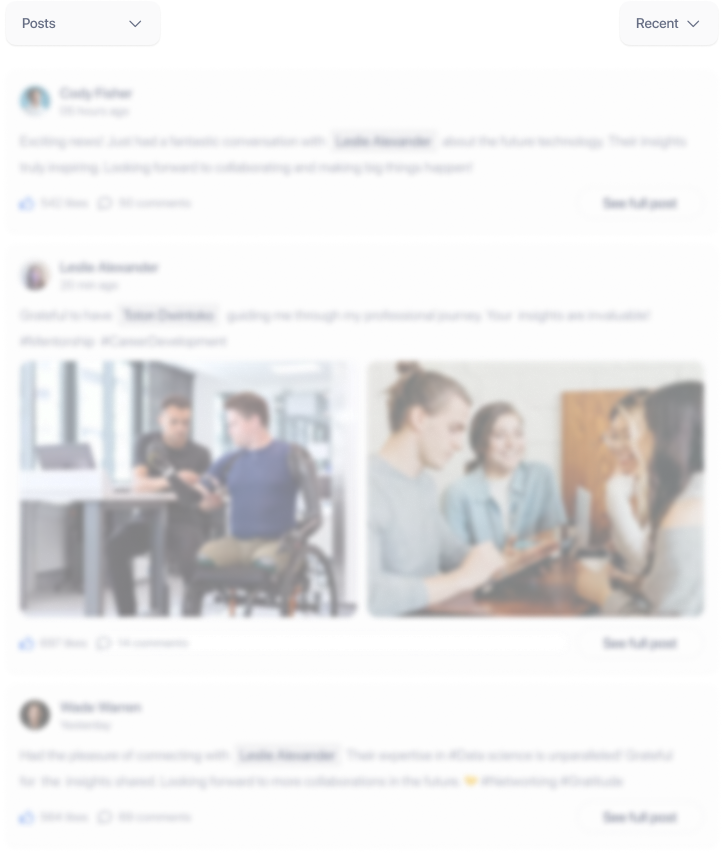