Víctor Jerónimo Núñez López
Operations Manager at GMD Stamping (Groupe GMD)- Claim this Profile
Click to upgrade to our gold package
for the full feature experience.
-
Inglés Full professional proficiency
Topline Score
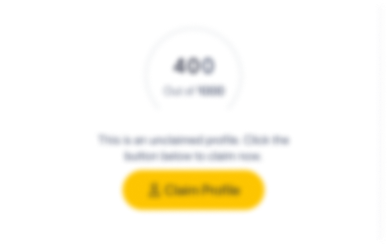
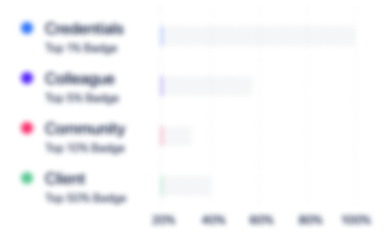
Bio

Edgar Padrón
Cuando trabajé con él, demostró ser un jefe excepcional, con un alto sentido de responsabilidad en todas sus actividades, siempre con la visión de negocio que se requiere en un puesto gerencial, sin olvidar el aspecto humano de sus colaboradores, siempre fomentando el crecimiento profesional y personal de la gente que lo rodea, creando un ambiente de trabajo excelente y por consecuencia el logro de los objetivos de todos principalmente los de la empresa.

LinkedIn User
Victor is a very competitive leader committed and responsible always focuses on results and with high human sense, one of the most developed skills I believe he has is rapid problem solving in order to achieve all the objectives of the company.

Edgar Padrón
Cuando trabajé con él, demostró ser un jefe excepcional, con un alto sentido de responsabilidad en todas sus actividades, siempre con la visión de negocio que se requiere en un puesto gerencial, sin olvidar el aspecto humano de sus colaboradores, siempre fomentando el crecimiento profesional y personal de la gente que lo rodea, creando un ambiente de trabajo excelente y por consecuencia el logro de los objetivos de todos principalmente los de la empresa.

LinkedIn User
Victor is a very competitive leader committed and responsible always focuses on results and with high human sense, one of the most developed skills I believe he has is rapid problem solving in order to achieve all the objectives of the company.

Edgar Padrón
Cuando trabajé con él, demostró ser un jefe excepcional, con un alto sentido de responsabilidad en todas sus actividades, siempre con la visión de negocio que se requiere en un puesto gerencial, sin olvidar el aspecto humano de sus colaboradores, siempre fomentando el crecimiento profesional y personal de la gente que lo rodea, creando un ambiente de trabajo excelente y por consecuencia el logro de los objetivos de todos principalmente los de la empresa.

LinkedIn User
Victor is a very competitive leader committed and responsible always focuses on results and with high human sense, one of the most developed skills I believe he has is rapid problem solving in order to achieve all the objectives of the company.

Edgar Padrón
Cuando trabajé con él, demostró ser un jefe excepcional, con un alto sentido de responsabilidad en todas sus actividades, siempre con la visión de negocio que se requiere en un puesto gerencial, sin olvidar el aspecto humano de sus colaboradores, siempre fomentando el crecimiento profesional y personal de la gente que lo rodea, creando un ambiente de trabajo excelente y por consecuencia el logro de los objetivos de todos principalmente los de la empresa.

LinkedIn User
Victor is a very competitive leader committed and responsible always focuses on results and with high human sense, one of the most developed skills I believe he has is rapid problem solving in order to achieve all the objectives of the company.

Experience
-
GMD Stamping (Groupe GMD)
-
France
-
Motor Vehicle Manufacturing
-
1 - 100 Employee
-
Operations Manager
-
Sep 2022 - Present
• Stablish a strong health, safety and environmental site performance every day. Applying micro management in critical operations, validating, designing and approving procedures and formats. • Design and Drive work processes and standards to ensure the highest production quality and productivity, including daily walk tours reviewing 100% critical stations. • Work collaboratively with cross functional leaders to balance team's capacity with prioritized activities. Implementing LPA program involving key departments. Show less
-
-
-
TAXAN MEXICO
-
Mexico
-
Consumer Electronics
-
1 - 100 Employee
-
Operations Manager
-
May 2017 - Jun 2022
• Deliver on strong site health, safety and environmental performance every day • Drive work processes and standards to ensure the highest production quality and productivity • Work collaboratively with cross functional leaders to balance your team's capacity with prioritized activities. • Budget Control and Managment • Development of Managers • Lead Productivity Improvement projects • Strategy Plan development • Drive culture of safety and continuous improvement • Collaborate with customers and cross functional teams • Ensure practices and processes are robust • Talent management • Resource management in a dynamic environment • Strategy development • Ensure plant maintenance program execution Show less
-
-
-
Faurecia
-
France
-
Motor Vehicle Manufacturing
-
700 & Above Employee
-
APU Manager
-
Jul 2016 - Dec 2016
Responsible for managing an Autonomous Production Unit. Assure coordination of product scheduling, success in launch new projects, plant functions, responsibilities, estimates and prepares budget and operate with budgetary performance, maintaining a safe and secure work environment, evaluate feasibility of each engineering change request, making sure successful in new launches accomplishing standards established by corporate´s engineering, ensure control of M & R and tooling, optimizing manpower utilization and skills. Support and promote company’s plans, programs, projects and activities which contribute to the company’s continuous improvement, creating culture of best practices in each team member. Direct head in Production, Safety and Quality indicators such as: Efficiency, Internal Defects, Overhead, Customer Defects, Safety, Scrap and OPR. Show less
-
-
-
Nidec Global Appliance
-
Brazil
-
Industrial Machinery Manufacturing
-
700 & Above Employee
-
Production Manager
-
Sep 2012 - Jun 2016
Responsible for managing a fractional horsepower AC/DC electric motor production area. Maintain close surveillance and control over production operations through perusal reports, meetings, observation and personal contact. Assure coordination of product scheduling, plan functions, responsabilities, budgetary performance, manpower utilization and skills. Bring forward new ideas, concepts and perceptions. Keep top management apprised of major concerns and issues. Promote an atmosphere that will motivate all production employees, encouraging optimum quality and productivity. Develop, train, assist and advise supervisors. Support and promote company's plans, programs and activities wich contribute to the company's continuous improvement. Maintain professionalism and stay abreast of new developments. Direct head in Production, Safety and Quality indicators such as: Efficiency, Internal defects, Customer Defects, Safety and Scrap. Show less
-
-
-
Groschopp, Inc.
-
Automation Machinery Manufacturing
-
1 - 100 Employee
-
Operations Manager
-
Jul 2008 - Aug 2012
Responsible for managing a fractional HP AC/DC electric motor manufacturing facility for an established American company transferring existing product manufacturing operations to Mexico. Responsible for effectively planning, directing, and coordinating all plant production. Through delegation of responsibilities and assignment of duties to coordinators and supervisors, achieve efficient and economical operation of the plant, conforming to the established goals and objectives to accomplish corporate profit, growth, and investment return. Manage the start up of a facility and production as it relates to building, equipment, quality and control of the manufacturing process. Assist in the evaluation of all capital equipment. Maintain detailed operation work instructions and control plans for all processes. Contribute to management areas responsible for quality assurance, problem recognition/resolution resulting in cost reductions, work simplifications, method improvements and work aids. Bring forward new ideas, concepts, and perceptions. Oversee the maintenance of all equipment, technical repairs, installations and a preventative maintenance system. Encourage employee communication. Maintain on-going and scheduled employee appraisal processes including wage considerations, promotions, and job transfers. Insure building, assuring a safe working environment for employees and secure necessary training to meet needs and regulations. Keep supervisors informed on matters of new policy, procedures, corporate philosophy, and decisions. Authorize payments of local expenses for the plant to a pre-determined maximum. Support and promote company’s plans, programs, and activities which contribute to the company’s continuous improvement. Maintain professionalism and stay abreast of new developments through various publications. Direct head in Manufacturing, Safety, Quality & Production with indicators such as: Productivity, Internal Defects, Customer Defects, Overhead Spending Show less
-
-
-
Remy International
-
Motor Vehicle Manufacturing
-
200 - 300 Employee
-
Operations Superintendent
-
Sep 2004 - Jun 2008
Operations Superintendent Head at Heavy-Duty area, direct head in Manufacturing, Safety, Quality & Production issues. Management indicators such as: Security and Safety: Reducing number of incidents in the area from 7 to 1 incident (Annual), as well as near misses identification. Scrap: Reducing from 3.5 to 2.1 KUSD in different projects into area reduction in 40% (Daily). FTQ (First Time Quality): Reducing from 3,626 to 1,412 ppm’s in Sub-assy area reduction in 60% (Annual). Warranties Costs: Reducing from 32,677 to 24,111 USD reductions in 26% (Monthly). UPLH: Increasing from 1.42 to 2.05 UPLH increasing 44% weekly. Overtime: Reducing from 3.4 % to 2.3 % weekly, reduction in 32%. Overhead Spending: Trend from 141 KUSD to 114 KUSD (Monthly), this mean reduction in 20%. Show less
-
-
-
Valeo
-
France
-
Motor Vehicle Parts Manufacturing
-
700 & Above Employee
-
Manufacturing Engineer
-
Jun 2002 - Sep 2004
-
-
-
Mabe Global
-
Mexico
-
Appliances, Electrical, and Electronics Manufacturing
-
700 & Above Employee
-
Operations Engineer
-
Aug 1998 - Aug 2001
-
-
Education
-
Universidad Tecmilenio
Master of Business Administration (MBA), Calidad y Productividad -
The University of Winnipeg
5o. Grado, English Language and Literature, General -
Instituto Tecnológico de San Luis Potosí
Ingeniero Industrial, Productividad y Calidad
Community
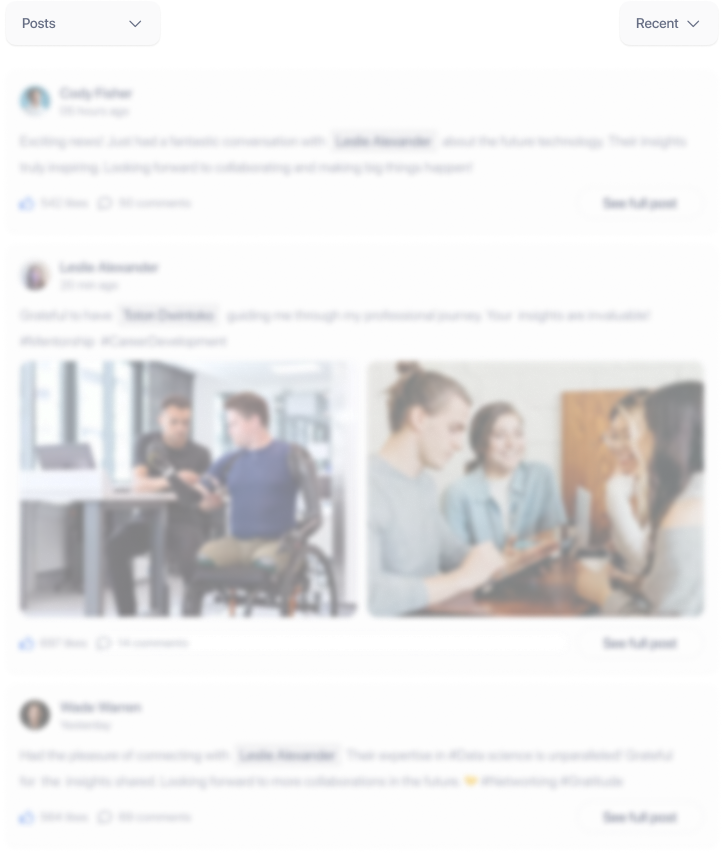