Umesh Nevgi
Director & Principal Designer - Product Design at Trimiti Moebius Design- Claim this Profile
Click to upgrade to our gold package
for the full feature experience.
-
English Full professional proficiency
-
Marathi Native or bilingual proficiency
-
German Limited working proficiency
-
Hindi Native or bilingual proficiency
Topline Score
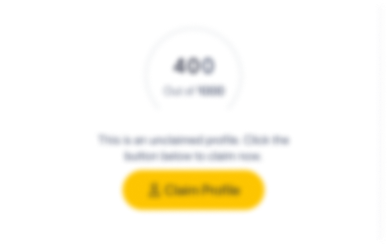
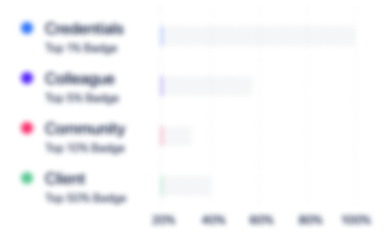
Bio


Experience
-
Trimiti Moebius Design
-
Australia
-
Design Services
-
1 - 100 Employee
-
Director & Principal Designer - Product Design
-
Jul 2013 - Present
* Working as Lead Designer in this young Australian industrial design and product engineering studio-consultancy to exploit the knowledge/competence gained through working over 3+ decades in multinational companies in the automotive, medical & consumer products engineering industries * Working on development of an array of products * Conceived, invented and developed an innovative-creative toys family to stimulate creative-cognitive-spatial skills amongst children worldwide. This range, XS Family Of Toys (Patents Pending), awarded many industry-coveted product design awards [IF DESIGN AWARD 2017 by International Forum Design (Germany), GOOD DESIGN AWARD 2017 by The Chicago Athenaeum Museum Of Architecture/Design (USA), EUROPEAN PRODUCT DESIGN AWARD 2018 by International Awards Inc. (Hungary/USA), RED DOT AWARD 2019: Honourable Mention by Design Zentrum (Germany), GERMAN DESIGN AWARD 2020 & GERMAN INNOVATION AWARD 2021 - both by German Design Council (Germany)] as seals of design excellence, with three of these six awards considered, within the global product design community, as the world's topmost three product design awards * Competent in hands-on designing of worldclass state-of-art products. Starting with Specs Definition, the work involves all interim stages: Market Analysis, Product Positioning, Concepts Generation, Materials & Manufacturing Processes Selection, Production-level 3D Models & 2D Drawings Preparation, Design Verification, Design for Manufacture, Mockups/Prototypes Trials, Customer Approvals, Toolmakers-Suppliers Liaison, Part Approvals, Design Validation Tests Support till Pilot Series Production Overview * Worked out key technical aspects (concepts development, materials selection, safety evaluation, proof of concept, feasibility assessment with toolmakers/suppliers, customer study) and commercial aspects (manufacturing costs, gross margins, selling prices) of these toys * Filed Patent Applications as a part of IP Protection strategy Show less
-
-
-
Robert Bosch Tool Corporation NA
-
Manufacturing
-
700 & Above Employee
-
Senior Technical Specialist (Product Design)
-
Sep 1995 - Apr 2013
* Executed an array of electromechanical Product Design projects through various development stages for a multitude of global OEM customers within the automotive industry (including Mercedes-Benz, Daimler-Chrysler, BMW, Toyota, Mazda, Porsche, Audi, VW, Volvo, Peugeot, Ford, General Motors, Opel, Scania and Iveco) * Designed various products within a 3D/2D CAD (Unigraphics/NX, ProEngineer/Creo & Catia) environment and developed further using rapid prototyping (including stereolithography, selective laser sintering and silicone tooling for vacuum-casting) / FMEA / DFMA / FEA / digital simulation & analysis tools (for moldflow, thermal, bending strain loads, vibration, etcetera) / design reviews / quality audit techniques so as to achieve shorter development cycles & to meet pre-defined delivery targets for quality, costs & timeframes * Successfully developed substantial intellectual property leading to 6x international patents (4x granted, 2x applied for) for the organisation * Designed, for example, an interesting engineering product - a re-designed Body Computer Module - for two European car manufacturers, with high-precision requirements and tightest-ever cost/space/weight/development-time constraints. The design concept involved a novel concept (patent granted) for a particular set of componentry and its corresponding assembly to aid achieving target constraints, resulting in 26% cost savings, 28% space savings & 18% weight savings * Designed, for example, a high-volume Body Computer Module for a major Japanese car manufacturer, meeting a design target to achieve 22% cost reduction without compromising the quality target * Designed, for example, a low-cost platform Body Computer Module for the emerging Asia-Pacific markets, with a target of a modular & cost-effective mechanical design which can be offered as a singular common high-reliability solution to meet varying requirements of multiple OEM customers in the region Show less
-
-
-
Yazaki North America
-
United States
-
Motor Vehicle Manufacturing
-
700 & Above Employee
-
Senior Product Design Engineer
-
Sep 1993 - Sep 1995
* Worked on design projects for vehicle security system / keyreader-illumination bezel / body computer systems for the future models of two major car manufacturer clients in Australia * Worked on a finely-detailed interior trim light assembly for the Commodore VT model of General Motors-Holden’s Automotive Limited. The work involved studying the behaviour of light & applying the laws of refraction in order to work out a simple & cost-effective solution to achieve the desired function of uniform illumination * These high-volume product systems were mainly plastics-based (using Nylon 6 & ABS blend, Crastin - low warpage PBT, Ultradur - general-purpose PBT, Corton - talc-filled Polypropylene, Ultramid - Nylon 6 & Nylon 66, Cycoloy - ABS & Polycarbonate alloy, Cycolac - ABS, Lexan - Polycarbonate, Delrin - Acetal, Liquid Silicone Rubber - Thermoplastic Elastomer, Rubber-modified polypropylene and Propathene - Polypropylene) and assembled in a semi-automated production line * These product systems utilise special production/assembly processes like plastic overmoulding, automated ultrasonic welding on carousel workstations, reflow soldering and robotic placement of surface-mount components, in addition to regular processes like injection moulding, snap-fit assembly and wave soldering * Prepared 3D CAD models, using Unigraphics & AutoCAD, during design stage for easier visualisation and customer approval and for later use in making faster, cheaper and more accurate prototypes using laser-sintering/stereolithography processes instead of conventional prototype tooling * Liaised and followed-up with customers, suppliers, moulder, tool-designers and tool-makers to ensure adherence to specifications / deadlines & maintenance of tooling / production programmes as per schedule Show less
-
-
-
MEISTER DESIGNS
-
Sydney, Australia
-
Product Design Consultant
-
Jul 1992 - Sep 1993
* Worked on a successfully completed short-term contract for the design & development of a hot beverages dispensing machine for office use - from initial concepts to series production * This product is plastic- (Cycolac T - ABS, Lexan - Polycarbonate, Delrin - Acetal and Zytel - Polysulfone) and metal- (stainless steel, copper alloy and die-cast zinc) based, electronically controlled and is being produced even today in Malaysia in high volumes primarily for international markets * Worked out finer and final features / assembly details, using AutoCAD Release 12, for various production processes - including injection moulding, blow moulding, rotational moulding, blanking, forming, coining and die-casting * Provided new features - tea-bags dispenser, user-adjustable ‘spoon size’ & membrane keypad control - to offer a highly market-competitive and cost-effective dispensing machine Show less
-
-
-
Siemens
-
Germany
-
Automation Machinery Manufacturing
-
700 & Above Employee
-
Senior Executive (Product Design)
-
Jul 1985 - Apr 1992
* Worked independently, in a team & later as a project leader of a team, assuming responsibility for successful execution of design projects from the concepts stage through the materials-selection/sourcing/detailing/prototyping/validation-testing/costing stages to the series production stage * Worked out precise design details for plastic/sheetmetal components-assemblies with various processes like injection-moulding, insert-moulding, blow-moulding, punching, blanking, forming, brazing, welding, powder-coating & also special processes like vacuum metallisation, metallic painting on plastics, electroless plating, laser-cutting * Designed X-ray diagnostic equipment units & systems for routine/special diagnosis, comprising of technologically advanced components: patient examination tables with manual/automatic spotfilm devices, X-ray generators of all power classes (featuring microprocessor control, programmed operation, multi-pulse technique & high-rating X-ray tube units), mobile & stationary high-res X-ray image intensifier systems for diagnostic/surgical use, electronic image evaluation & digital image processing, angiography attachments, tomography equipment & paediatric attachments for all fields of X-ray diagnosis applications * Specifically, for example, conceived & developed a novel motorised shifting table-top attachment, with a travel of 1500 mm, the highest produced then on an patient examination table by any manufacturer, enabling the use of standard examination tables (designed for routine diagnostic tests) also for special procedures like cerebral/abdominal/peripheral angiography * Successfully engineered new products using high-technology areas like advanced materials, micromechanics, microprocessor-controlled logic circuits, surface-mount components, flexible PCBs & membrane keypads * Conducted value engineering exercises, refined existing products range and trained service engineers/technicians on new products * Co-ordinated mockups & prototypes Show less
-
-
-
Larsen & Toubro
-
India
-
Construction
-
700 & Above Employee
-
Graduate Engineer Trainee (Product Design)
-
Jul 1982 - Jun 1983
* Designed sheetmetal-based process equipment (in stainless steel and high-tensile carbon steel) as per ASME Code, to suit customer’s specifications * Designed, for example, a shrunk-fit multi-wall heat-exchanger for a fertiliser-processing plant * Conducted design analysis, prepared engineering drawings, design reports & other technical documents and liaised with inspection agencies for their approval * Designed sheetmetal-based process equipment (in stainless steel and high-tensile carbon steel) as per ASME Code, to suit customer’s specifications * Designed, for example, a shrunk-fit multi-wall heat-exchanger for a fertiliser-processing plant * Conducted design analysis, prepared engineering drawings, design reports & other technical documents and liaised with inspection agencies for their approval
-
-
Education
-
Industrial Design Centre, Indian Institute of Technology, Mumbai, India
Master of Design (Industrial Design), Industrial Design / Product Design -
Government College of Engineering, Marathwada University, Aurangabad, India
Bachelor of Engineering (Mechanical), Mechanical Engineering
Community
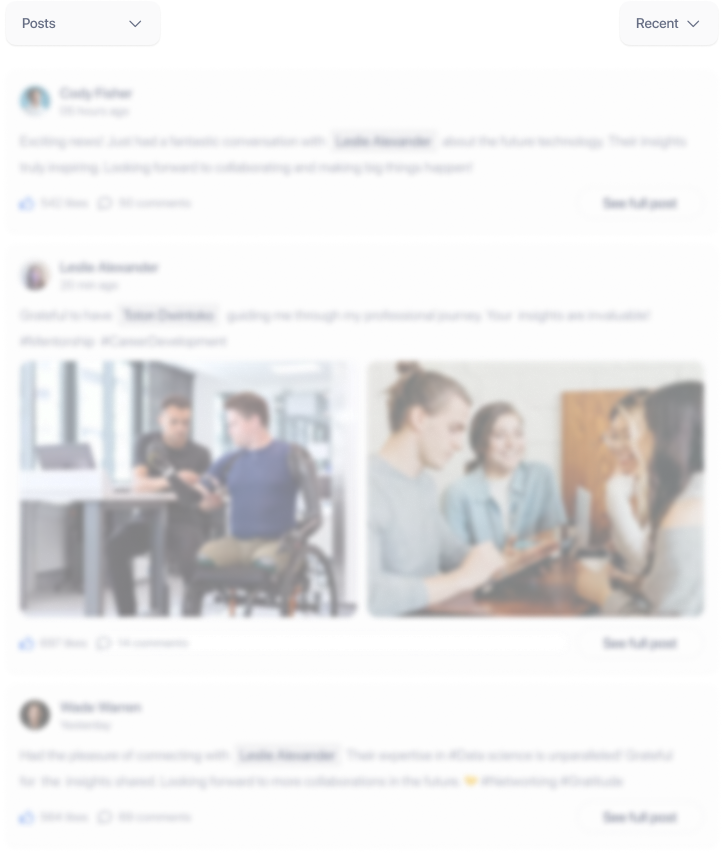