Tyler Leach
Engineering Consultant at Endeavor Consulting Group, LLC- Claim this Profile
Click to upgrade to our gold package
for the full feature experience.
-
English Native or bilingual proficiency
-
Spanish Limited working proficiency
Topline Score
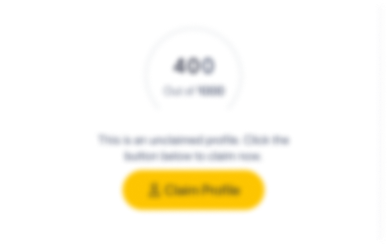
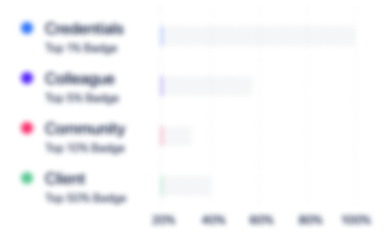
Bio


Experience
-
Endeavor Consulting Group, LLC
-
United States
-
Business Consulting and Services
-
1 - 100 Employee
-
Engineering Consultant
-
Oct 2023 - Present
-
-
-
NorthStar Medical Radioisotopes, LLC
-
United States
-
Pharmaceutical Manufacturing
-
200 - 300 Employee
-
Senior Chemical Process Engineer
-
Sep 2022 - Aug 2023
As a Sr Chemical Process Engineer, I was the process technical lead for the Actinium-225 program, which aims to produce the scarce radioisotope used in targeted alpha therapy for cancer treatment. In this role I coordinated sub-teams, including process chemistry, mechanical systems, production process, radiation containment (Hot Cells), material/ equipment life testing, and various process equipment engineering teams. Integration and organization was maintained through detailed project documentation, regular sub-team meetings, and close communication with main stakeholders. I oversaw and assisted with generation of requirements documentation, risk analyses, process flow diagrams, equipment lists, and detailed schedules. In addition to leading several recurring team meetings, I also drove critical decision making by assembling key stakeholders, developing detailed meeting agendas to drive discussion, generating comprehensive meeting notes, and logging the resulting key decisions and actions. The project required regular coordination with our hot cell vendor to ensure our process would integrate seamlessly with their enclosures. It also required coordination with a Vaporized Hydrogen Peroxide system vendor to ensure appropriate microbiological control could be achieved within the enclosures. I maintained regular communication with Leadership to implement customer and business needs as they evolved. The impacts of these needs were assessed for impact to process and relayed to project teams for implementation. Many unique constraints resulted due to the extremely high price of the starting material, the radioactive nature of the product, the radioactive gas produced during decay, and the acidic solutions in which it is processed in. Many unique and custom solutions were needed. Regular input was given to build out detailed project flow and schedule. I assisted in project budgeting by providing Capital Expenditure estimates and requests. Show less
-
-
Chemical Process Engineer II
-
Apr 2020 - Sep 2022
As a Chemical Process Engineer II, I was in a leadership role on the process development team for development of the molybdenum dissolution process. I acted as system SME and coordinated cross departmental efforts to ready the system for Qualification. To help achieve this, I drafted User and Functional Requirements, Software Detailed Design Specifications, FMEAs, system risk assessments, procurement specs, receiving inspection documentation, Master Component Lists, Impact Assessments, parameter definition documents, and both production and cleaning recipes. I worked to optimize process reliability and performance by defining Critical Process Parameters (CPPs) and Critical Material Attributes (CMAs). Further control was achieved by implementation of Critical Aspects (CAs), Critical Design Elements (CDEs), and RI tests. I also interfaced extensively with our system integrator to define modular process automation phases that can be organized into different recipes with editable parameters. I attended a Factory Acceptance Test (FAT) for a skidded Water for Injection (WFI) system and another FAT for a Clean in Place (CIP) skid. Over my time at NorthStar I have learned how to effectively work in an FDA regulated, cGMP quality environment as we produce a parenteral drug product. I have had the opportunity to perform several site acceptance tests (SATs), installation/operational qualifications (IOQs) and commissioning activities. This role has required me to interface with QC, QA, Validation, Project Management, Manufacturing Engineering, Operations, Sourcing, Automation, Science and Maintenance on a regular basis. I have utilized Master Control (eQMS), Microsoft Excel, Microsoft Word, Microsoft Project, Microsoft Outlook, and Wonderware frequently. Show less
-
-
Chemical Process Engineer
-
Aug 2018 - Apr 2020
As a chemical process engineer at NorthStar, I was responsible for development testing of a pilot system used to dissolve radioactive molybdenum target material for extraction of the medically useful isotope Mo-99, which decays into the diagnostic imaging molecule Tc-99m. My responsibilities included designing experiments to characterize unit operations, developing clean in place (CIP) parameters, troubleshooting design issues for implementation on the production system, and working with the automation group to achieve the desired chemical/mechanical outcome during operation. While at NorthStar I also implemented a hydrophilic polymer production process which required equipment sourcing, material sourcing, development of a validated test method for lot release, and overseeing the transfer to the manufacturing group for sustained operation. In more minor roles, I had assisted in guidance document research for critical process parameter (CPP) and critical material attribute (CMA) determination to meet the defined critical quality attributes (CQAs). I attended two water for injection (WFI) courses put on by the International Society for Pharmaceutical Engineering (ISPE), which included Pharmaceutical Water Generation as well as Storage, Delivery and Qualification of Pharmaceutical Waters. Show less
-
-
-
Alliant Energy
-
United States
-
Utilities
-
700 & Above Employee
-
Generation Engineering/ Resource Planning Intern
-
May 2017 - Aug 2017
At Alliant Energy, I spent half of the time in Resource Development and the other half in emission controls within power generation engineering. While in resource planning, I researched and presented different grid scale energy storage systems for integration with renewable power generation. I also coded a Visual Basic macro to convert large scale data inputs to Fortran based flat files. While in generation engineering, I worked on a spreadsheet that would take large amounts of plant data from a server, and process it automatically to generate a monthly report. At a coal plant, I helped tune the ammonia injection grid of the Selective Catalytic Reducer (SCR) by taking NOx concentration measurements and creating a 3D emission profile across the reactor. Show less
-
-
-
Bemis Company, Inc.
-
Switzerland
-
Packaging and Containers Manufacturing
-
700 & Above Employee
-
Process Engineering Intern
-
May 2016 - Dec 2016
At Bemis, I worked on a blown film process engineering team, where I was given both long and short term projects. I studied pressure fluctuations in an extruder as a result of resin demixing throughout the resin distribution system. I also studied nylon film shrink effects in order to minimize trim waste depending on the specification ran by creating a Visual Basic program that would calculate the ideal equipment settings for the least waste. I also had the chance to perform a range of lab work, including tensile strength tests, heat seal tests, Davinor film analysis, and film shrinkage tracking. During my time at Bemis, I used lots of Excel, summarized and reported my findings for others, and worked with a range of departments outside of engineering. Show less
-
-
Education
-
University of Wisconsin-Madison
Bachelor’s Degree, Chemical Engineering
Community
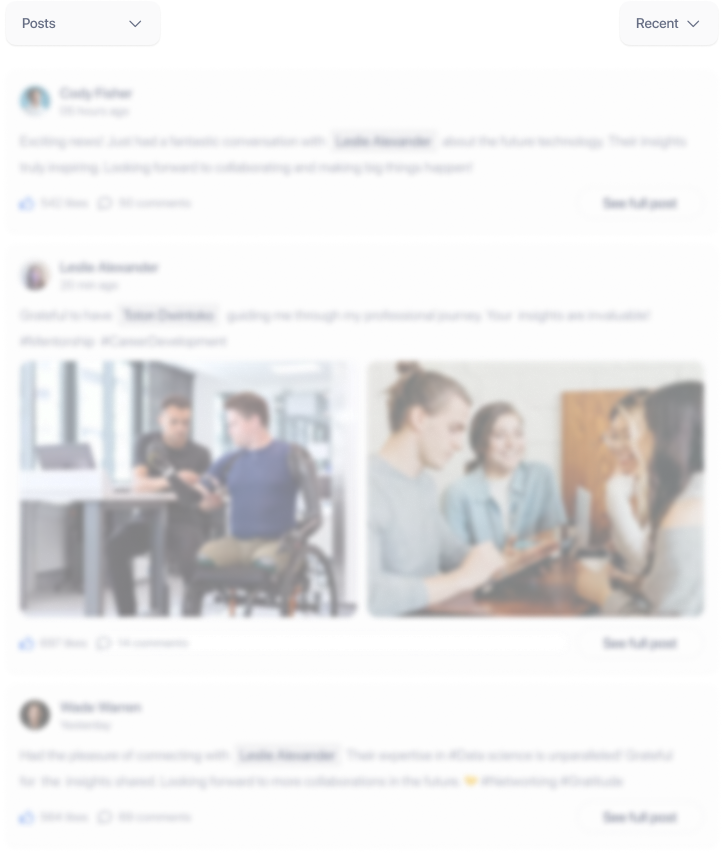