Tsukasa Tanifuji
Deputy Manager of Coporate planning and support at Nagoya Grampus- Claim this Profile
Click to upgrade to our gold package
for the full feature experience.
-
English Full professional proficiency
-
Japanese Native or bilingual proficiency
Topline Score
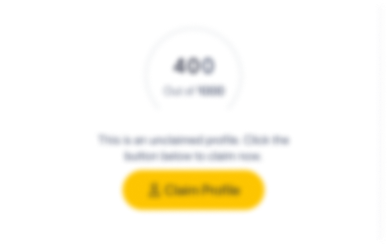
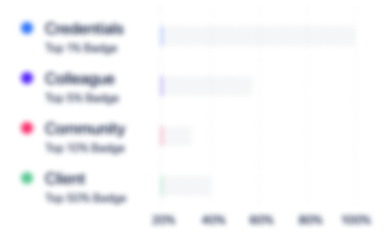
Bio


Experience
-
Nagoya Grampus
-
1 - 100 Employee
-
Deputy Manager of Coporate planning and support
-
Feb 2020 - Present
-
-
-
Roland Berger
-
Germany
-
Business Consulting and Services
-
700 & Above Employee
-
Project Manager
-
Apr 2014 - Jan 2020
-
-
-
Kearney
-
United States
-
Business Consulting and Services
-
700 & Above Employee
-
Student Consultant
-
Sep 2013 - Dec 2013
・Selected to participate in cross-functional Business School class focusing on improving the number of SKUs for actual client firm・Developed an optimization model to find an optimal set of SKUs; reducing 56% SKUs from the current situation and 1% cost reduction through reduction. ・Selected to participate in cross-functional Business School class focusing on improving the number of SKUs for actual client firm・Developed an optimization model to find an optimal set of SKUs; reducing 56% SKUs from the current situation and 1% cost reduction through reduction.
-
-
-
Waseda University
-
Higher Education
-
700 & Above Employee
-
Research Assistant
-
Apr 2011 - Mar 2012
-Operations Research applications in Home-Visit Nurse Care Scheduling・Led six undergraduate students; conducted the seminar every week for sharing knowledge; counseled the method to use AMPL application for mathematical approach.・Devised a novel Scheduling System in the Home-Visit Nurse Care industry; solving within ten minutes with the instance of 30 staffs and 100 customers by using AMPL application; first successful system in the world.・Modeled the Home-Visit Nurse Care Schedule as a Linear Programming with constraints such location of visit, transportation method, the number of visits, flexible time windows, idle time and psychological load.
-
-
Teaching Assistant
-
Apr 2010 - Mar 2012
・Evaluated 300 undergraduate students reports in the course of Operations Research; Trained 150 freshman undergraduate students the method to use Excel Solver & AMPL.
-
-
-
Mitsubishi Research Institute
-
Japan
-
Think Tanks
-
200 - 300 Employee
-
Consulting Internship
-
Aug 2009 - Aug 2009
・Presented analysis of Chinese markets in pharmaceutical industries to upper management. ・Presented analysis of Chinese markets in pharmaceutical industries to upper management.
-
-
-
NTN Bearing Corporation
-
United States
-
Machinery Manufacturing
-
700 & Above Employee
-
Manufacturing Internship
-
Aug 2008 - Sep 2008
・Analyzed optimal staff size along 4 assembly lines; reduced needed employees by 22% in car bearing facility.・Developed layout of factory to maximize efficiency of supply chain model in assembly line; reducing 30% of semi-operation and non-operation time to operation time for each worker by D-I analysis.・Presented analysis & recommendations to upper management; recommendations currently implemented ・Analyzed optimal staff size along 4 assembly lines; reduced needed employees by 22% in car bearing facility.・Developed layout of factory to maximize efficiency of supply chain model in assembly line; reducing 30% of semi-operation and non-operation time to operation time for each worker by D-I analysis.・Presented analysis & recommendations to upper management; recommendations currently implemented
-
-
-
Panasonic North America
-
United States
-
Appliances, Electrical, and Electronics Manufacturing
-
700 & Above Employee
-
Manufacturing Internship
-
Feb 2008 - Mar 2008
・Led three interns including two Thailand University Students and taught Scientific Management and D-I analysis.・Changed equipment placement along assembly lines to maximize efficiency; reduced needed employees from 30 to 27.・Designed the standardized work in the assembly lines by Scientific Management, reduced 15% of operation time.・Presented analysis & recommendations to upper management; recommendation currently implemented and created a new assembly lines for new demands by allocating employees.
-
-
-
Hitachi
-
Japan
-
Appliances, Electrical, and Electronics Manufacturing
-
700 & Above Employee
-
Manufacturing Internship
-
Jul 2007 - Aug 2007
・Analyzed standardized for optimal supply chain model in assembly lines to improve production efficiency, cost savings $25,000 year in train assembly.・Provided three new layout of factory for maximizing efficiency and making 60-80 square meter to allocate a new equipment for new demands. ・Analyzed standardized for optimal supply chain model in assembly lines to improve production efficiency, cost savings $25,000 year in train assembly.・Provided three new layout of factory for maximizing efficiency and making 60-80 square meter to allocate a new equipment for new demands.
-
-
Education
-
University of Michigan
Master of Science (MS), Industrial and Operations Engineering -
Waseda University
Master of Science (M.S.), Coursework in Industrial and Management System Engineering -
Waseda University
Bachelor of Science (B.S.), Industrial and Management System Engineering
Community
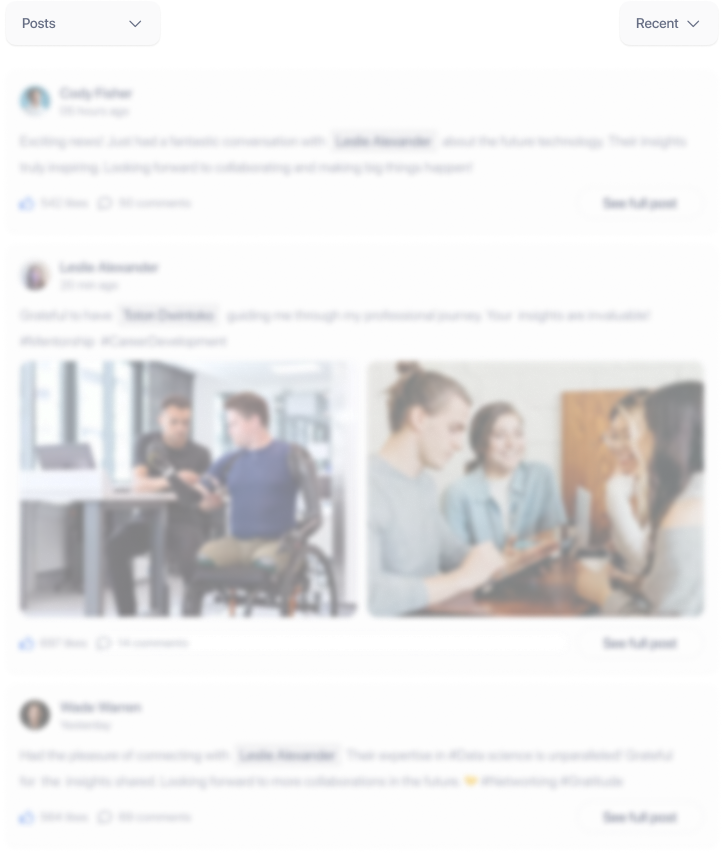