Rita Bahio-Cube
Production Engineer at DTI Group Ltd- Claim this Profile
Click to upgrade to our gold package
for the full feature experience.
Topline Score
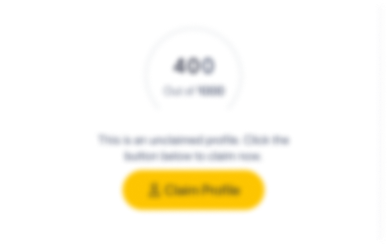
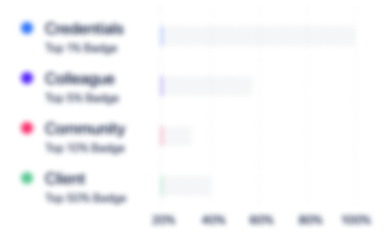
Bio


Experience
-
-
Production Engineer
-
Mar 2016 - Present
-
-
-
-
Product Engineer / Lead Product Engineer
-
Jun 2011 - Apr 2015
Supported the development and execution of strategies that attain profitability targets on Smart Power Product lines (under Automotive Product Group) through cost reduction, capacity expansion and yield enhancement projects following product specifications and industry standards. Collaborated with cross-functional teams in Italy (Designer, QA, Applications) with regards to new product introductions (NPI), customer returns and requests, quality control, and new business opportunities. Applied design for manufacturing analysis in supporting new product releases and setup or program changes Practiced SPC tools and methods in new or matured products to ensure a high process capability Provided disposition and sign off corrective actions to rectify the root cause of product’s technical issues. Repaired and troubleshoot setup equipment and PCB test jigs. Performed curve-tracing and bench testing analysis on sample devices. Developed and implemented screen tests with corresponding AQL management to improve the product quality and test coverage. Also submitted ANOVA report pertaining to the concerned test parameters. Updated documents relating to the approved and released test setup configuration, software, and processes. Cascade the information to the concerned groups. Major Achievements • Characterized and created energy stress test program on one pre-driver product • Highly-participated in securing the business deal with a new customer • Test time reduction performed on two devices ( 30% capacity and tester utilization increase) • Test Flow Elimination on four devices ( 33.33% test cost reduction on each product ) • Implemented parallel testing of two devices ( 50% productivity and utilization increase) • Qualified and supported the release of five new products and two product derivatives Show less
-
-
-
Analog Devices
-
United States
-
Semiconductor Manufacturing
-
700 & Above Employee
-
Subcon Product Engineer
-
Dec 2010 - May 2011
Led two members to carry out remote product engineering support to Carsem Malaysia Had regular correspondence and coordination with Malaysian counterpart in subcontractor area. Performing root cause analysis and corrective actions to QA failures (In-line sampling)
-
-
Test Product Engineer
-
May 2010 - Dec 2010
Responsible for the yield monitoring, sustaining, and improvement of ADI’s Amplifier Products. Had direct interface with the Product Line counterparts in USA and Ireland sites Validated customer return on AMP products through automatic test equipment and bench testing. Reviewed and sign off platform transfer or migration statistical data of my products
-
-
-
-
PRODUCT SUSTAINING ENGINEER SUPERVISORY
-
Apr 2007 - May 2010
Supervised a line support engineering force of 6-8 engineers in attaining metrics and company goals. Promoted Total Quality Management (TQM) principles and used Project Management Method in capacity enhancement Assisted in the training and development of new engineers. Submitted regular performance or progress reports Engineering representative in manufacturing’s daily coordination meeting Major Achievements• Lower down hold lots capture rate to 2% from 7%, the target was 5%• Successfully completed the Idiot’s Guide manual for new Product Sustaining Engineers• Successfully led training programs such as Product Sustaining Technician Immersion Program. • Contributed in the company recognized UPH improvement project using TQM Show less
-
-
TEST MANUFACTURING ENGINEER
-
Mar 2004 - Apr 2007
Worked in rotating shift in providing engineering support to production test floor. Performed verification and validation on encountered production and AQL rejects online or on bench test. Identify and rectify the root cause of those rejects and document them in an engineering report. Attended and gave appropriate disposition to non-conforming lots and out of control processes Closely coordinated with maintenance and system group to resolve production problems which includes but not limited to the hard-to-setup or hard-to-sustain test setups Liaise closely with product development group relating to new product releases and introduction Performed characterization, correlation, Guard Band Analysis, EOS check, and the like to qualify hardware or software changes. Developed and implemented continuous improvement in the yield and parts per million (PPM) performances, as well as in the capacity and flexibility of the existing system. Major Achievements• Resolved seven test setup issues on different devices that led to an increase of tester utilization• Platform migration offshore assignment in Carsem Malaysia • Major Initiative involved the in-line-sampling failure resolution of three devices• Successful completion of the process related projects : Test program standardization; Teradyne A360 Standard Binning Assignment; Test program revision standardization; MT93xx – MT9918 handler interchangeability project; Epson Handler interchangeability fan out Show less
-
-
Education
-
Polytechnic University of the Philippines (Taguig Branch)
Bachelor's Degree, Electrical, Electronics and Communications Engineering
Community
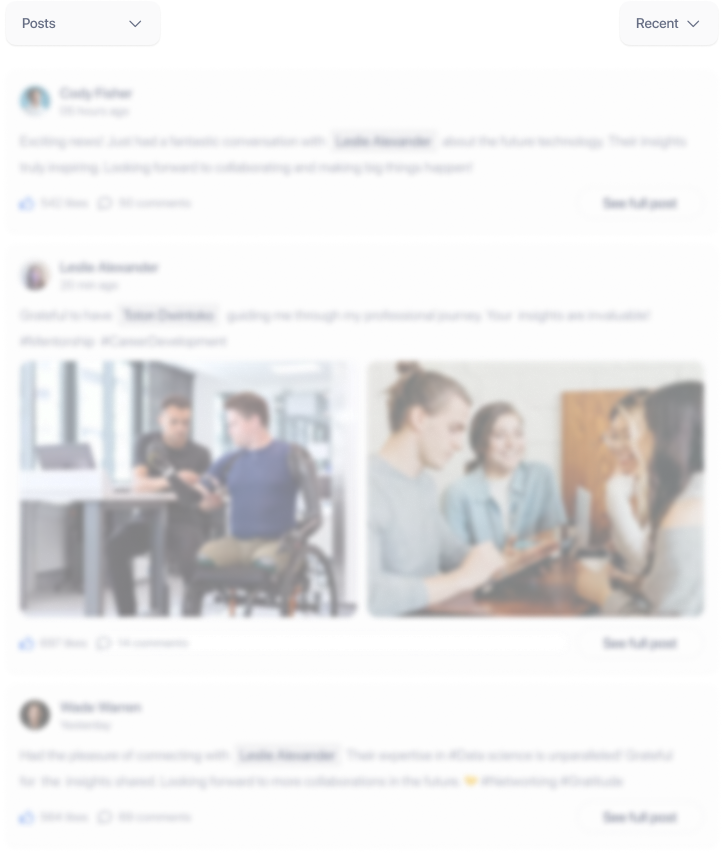