Troy Brewster
Operations Manager at Capsigen- Claim this Profile
Click to upgrade to our gold package
for the full feature experience.
Topline Score
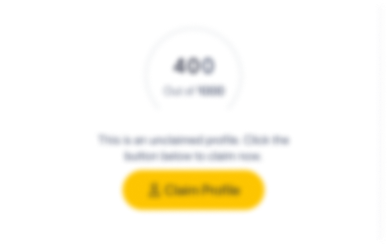
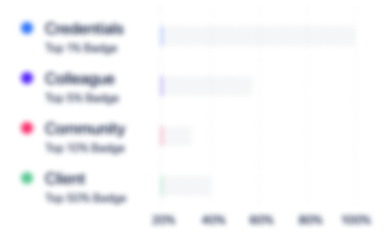
Bio


Experience
-
Capsigen
-
United States
-
Biotechnology Research
-
1 - 100 Employee
-
Operations Manager
-
May 2021 - Present
•Active day-to-day managing of Facilities, Purchasing, Supplier Management, Receiving, and Accounts Payable functions. •Manage Preventive Maintenance (PM) and Calibration programs. •Provide on-site IT support, escalate issues to IT contractor as necessary. •Manage company safety program. •Coordinate new employee training as part of onboarding process. •Working with all business functions to document and improve processes. •Provide subject-matter guidance and support to ensure appropriate quality system design and regulatory compliance. Show less
-
-
-
Freelance
-
Egypt
-
Human Resources
-
1 - 100 Employee
-
Freelancer/Independent Contractor
-
Oct 2020 - May 2021
•Working with a Vancouver, Washington gene therapy startup in establishing a nimble and flexible Quality Management System following cGMP and cGLP guidelines. •Working with a Vancouver, Washington gene therapy startup in establishing a nimble and flexible Quality Management System following cGMP and cGLP guidelines.
-
-
-
Freelancer/Independent Contractor
-
Software Development
-
1 - 100 Employee
-
-
Jun 2019 - Oct 2020
•Working with a Denton, Texas Specification Developer in performing document review, revision, remote audits and audit response corrective actions for ISO 13485:2016 and MDSAP certification and compliance.
-
-
-
Mar 2019 - Oct 2019
Working with a Portland, Oregon area startup Medical Device Specification Developer to build a FDA complaint Quality Management System per the applicable requirements within 21 CFR Part 820.
-
-
-
High Speed Interconnects, LLC
-
United States
-
Appliances, Electrical, and Electronics Manufacturing
-
1 - 100 Employee
-
Quality Systems Engineer
-
Nov 2019 - Jul 2020
Manufacturer of cable and cable assemblies for the Aerospace, Defense and Medical Device industries. Quality Engineer, 2019-Present •Managed and maintained all aspects of the Quality Management System to maintain AS9100 certification. •Upgraded and improved the Quality System to achieve ISO 13485 certification. •Identified gaps and executed improvements across the Quality System affecting three sites. •Hands-On management of Document Control, Corrective and Preventive Action (CAPA), Customer Complaints, Non-Conforming Materials, Calibration and Training programs. •Coordinated and led CAPA, Material Review Board (MRB) and Customer Complaint meetings. •Appointed as the Management Representative by executive leadership. Performed Management Review for organization. •Led external audits (Customer/ISO), representing and speaking on the Quality Management System. Coordinating or directly follow-up with auditors with written responses. •Created and maintain KPI’s for organization (Operations and Quality). •Validated NetSuite ERP and Box software programs, verifying functionality. Show less
-
-
-
TE Connectivity
-
Switzerland
-
Appliances, Electrical, and Electronics Manufacturing
-
700 & Above Employee
-
-
Jun 2018 - Feb 2019
Senior Quality Systems Analyst (Cross-Site), June 2018-2019Maintained compliance to applicable regulatory requirements while continuously improving the Quality Management System (QMS).•Worked closely with the Site Head of Quality at two site locations ensuring that the Quality Management System is maintained to 21 CFR Part 820 and ISO 13485.•Responsible for the Quality Management System at both locations.•Identified gaps and executed improvements across multiple site Quality Systems.•Managed Corrective Action/Preventive Action (CAPA) program across sites.•Led internal audit program to maintain compliance to ISO 13485 and FDA (21 CFR Part 820) requirements across sites.•Co-led external audits (Customer/ISO/FDA), representing and speaking on the QMS aspects. Coordinated or directly followed-up with auditors written responses.•Coordinated Management Review across sites including providing information for Global/Corporate Management Reviews.•Assisted Training Manager with implementation of sites' Training Programs.•Managed annual FDA registration and listing process.•Maintained data and publishing regular reports for the Quality Department. Show less
-
-
-
Feb 2015 - Jun 2018
Quality Analyst (November 2016 to June 2018)Lead site Quality Management System activities.•Administer CAPA program globally.•Coordinate and lead CAPA review board meetings.•Track and maintain CAPA metrics for quality review for site and globally.•Train new users in CAPA system.•Lead site internal audit program to maintain compliance to ISO 13485 and 21 CFR Part 820.•Participate in customer, third party and regulatory audits.•Administer records program.•Create and revise site and global level Quality System procedures.•Process engineering change orders (ECO's) supporting product, process, document and system changes using QP3 product lifecycle management (PLM) system.Engineering Support Specialist (February 2015 to November 2016)Providing support functions for all aspects of site document control department.•Process engineering change orders (ECO's) supporting product, process, document and system changes using QP3 product lifecycle management (PLM) system.•Prepare and assemble manufacturing lot packets.•Complete requests for documents.•Manage electronic and hard copy files and records.•Create or revise documentation in support of system, product or process changes.•Provide training for employees using the QP3 PLM software. Show less
-
-
-
-
Quality Management Consultant
-
Jan 2017 - Apr 2018
Created quality system procedures, work instructions and manufacturing batch records to implement a Quality Management System compliant to OLCC statutes 845-025-3230 and 845-025-3240 for Portland area company extracting oil from cannabis. Created quality system procedures, work instructions and manufacturing batch records to implement a Quality Management System compliant to OLCC statutes 845-025-3230 and 845-025-3240 for Portland area company extracting oil from cannabis.
-
-
-
Cascade Composites
-
United States
-
Aviation and Aerospace Component Manufacturing
-
1 - 100 Employee
-
Quality Systems Director
-
Sep 2013 - Feb 2015
Manufacturer of composite panels and structural fittings for military aircraft. Quality Systems Director (September 2013 to February 2015) Tasked with implementing and maintaining a quality management system to achieve and maintain Nadcap accreditation. •Implemented a quality management compliant to Nadcap AC7004 (QMS) and AC7118 (Composite Manufacturing) standards. •Achieved Nadcap accreditation May 2014, eight months after date of hire. •Created document control, internal audit, CAPA, equipment calibration, employee training and supplier management processes. •Perform Thermo Uniformity Surveys (TUS) and System Accuracy Test validation activities on industrial oven and autoclave. •Author standard operating procedures and work instructions for all aspects of manufacturing and quality. Show less
-
-
-
-
Technical Writer
-
Dec 2013 - May 2014
Authored Standard Operating Procedures (SOP), Work Instructions (WI), Test Methods (TM) and Batch Records (BR) for Oregon Biotech company that manufactures plant based cell culture products for use in nutraceutical and nutrition industries. Authored Standard Operating Procedures (SOP), Work Instructions (WI), Test Methods (TM) and Batch Records (BR) for Oregon Biotech company that manufactures plant based cell culture products for use in nutraceutical and nutrition industries.
-
-
-
Life Technologies
-
United States
-
Biotechnology Research
-
700 & Above Employee
-
-
Jun 2009 - Feb 2013
Managed all aspects of quality for the primary and stem cell systems business unit, with annual revenue of $2M. Appointed as the functional leader of the business unit, tasked with updating senior leadership in the health of the quality system and overall operation.•Managed a quality system based on the requirements of 21 CFR Part 820, 210, 211 and ISO 13485 for primary and stem cell system business unit.•Coached and developed employees by serving as a mentor.•Responded to customer inquiries regarding product issues and complaints by telephone and email.•Led staff, quality review, material review and operational metric review meetings.•Assisted Cellular Analysis Unit in receiving ISO 13485 certification September 2012.•Conducted individual and group training sessions on procedures, processes and best practices.•Completed supplier surveys, origin documentation and other correspondence documents for customers and leadership.•Coordinated calibration activities for all lab equipment by managing equipment databases.•Authored, revised and approved SOP’s, test methods, batch records and data forms.•Appointed as quality leader for new product introductions for business unit.•Performed weekly analysis of technical and non-technical complaints. Tracked and trended technical complaints by lot number and issue.•Reviewed final product and intermediate product batch records.•Approved finished goods for sale including certificate of analysis generation and publication.•Managed TrackWise CAPA, Agile eDMS document and KaplanWire training systems. Show less
-
-
-
Apr 2007 - May 2009
Coordinated and managed the day to day quality assurance support functions for the manufacturing groups on-site. •Maintained a Quality System Program to follow the requirements of 21 CFR Part 820, 210 and 211.•Reviewed final product and intermediate product batch records.•Authored version 2.0 of a component medical device master file for the FDA.•Approved finished goods for sale including certificate of analysis/origin generation and publication.•Reviewed and released raw material and supply specification packets.•Conducted individual and group training sessions on procedures, processes and best practices.•Performed analysis of technical and non-technical complaints. Tracked and trended technical complaints by lot number and issue.•Authored, revised and approved SOP’s, test methods, batch records and data forms. Show less
-
-
-
Jan 2003 - Mar 2007
Member of four person team that implemented a cGMP compliant quality system so that cell culture media and supplements could be used for further manufacturing in regulated medical device manufacturers. Coordinated and managed the day to day quality assurance support functions for the manufacturing groups on-site.•Assisted in the implementation and maintenance of a Quality System Program to follow the requirements of 21 CFR Part 820, 210 and 211.•Assisted in the development of a component medical device master file for the FDA.•Reviewed final product and intermediate product batch records.•Approved finished goods for sale including certificate of analysis/origin generation.•Reviewed and released raw material and supply specification packets.•Authored over 300 controlled documents including batch records, specifications, and SOP’s.•Performed receiving functions for all incoming goods to the facility. Show less
-
-
-
Feb 2002 - Jan 2003
Performed the packaging and processing of cell, media, supplements and reagent orders. Ensured the customer received their orders accurately and on-time.•Processed an average of 30 shipments a day consisting of cryopreserved primary cells, refrigerated liquid media and frozen supplements and reagents using FedEx systems.•Performed receiving functions for all incoming goods to the facility.
-
-
-
-
Owner
-
Jun 1995 - Jan 2002
Mail order company specializing in the acquisition of rare and import CD’s and records from Europe and Japan for distribution within the United States. •Worked with international distributors to provide music CD’s for customers that were not available in the US. •Performed audio transfer to compact disc from various audio and video sources (Cassette, LP Records, VHS, Minidisc, DAT and Video CD). •Performed video transfer to Video CD (precursor to DVD) and DVD from VHS sources. Mail order company specializing in the acquisition of rare and import CD’s and records from Europe and Japan for distribution within the United States. •Worked with international distributors to provide music CD’s for customers that were not available in the US. •Performed audio transfer to compact disc from various audio and video sources (Cassette, LP Records, VHS, Minidisc, DAT and Video CD). •Performed video transfer to Video CD (precursor to DVD) and DVD from VHS sources.
-
-
-
GTS Services
-
United States
-
Software Development
-
1 - 100 Employee
-
-
Jan 2000 - Oct 2000
Managed purchasing functions for a multi-million dollar software company. Mandated to reduce costs while still providing the same quality of goods customers expected.•Purchased all items for internal and external use including computer workstations, servers, hardware, software and accessories using ACCPAC database.•Supervised temporary employees hired to perform warehouse and facilities tasks.•Assisted IT department in building and configuring Windows NT servers and workstations. Repaired and upgraded systems as requested.•Picked up locally purchased goods from vendors using company vehicle. Show less
-
-
-
Apr 1999 - Jan 2000
Performed the packaging and processing of hardware and software orders. Ensured the customer received their orders accurately and on-time.•Processed an average of 50 shipments a day consisting of computer workstations, servers and software orders using UPS systems.•Maintained auto and flat glass software inventory. Assembled new software packages as inventory levels dictated.•Picked up locally purchased goods from vendors using company vehicle.
-
-
-
Rite Aid
-
Retail
-
700 & Above Employee
-
Supervisor and Sales Associate
-
Sep 1994 - Mar 1999
•Served as interim resident supervisor performing store closing procedures. •Served as freight crew lead, which included restocking of product shelves, configuring merchandise displays, and using planograms to rebuild merchandise aisles. •Developed and printed photos including conducting calibration tests, general maintenance, troubleshooting, and repair of the Noritsu QSS Micro photo processing machine. •Traveled to other stores within Portland Metro area prepping for annual inventories. •Provided customer service in both the pharmacy and the store. •Processed Western Union money transfers per customer requests. •Processed hunting and fishing license orders per customer requests. Show less
-
-
Education
-
Oregon Bioscience Association
-
Portland Community College
Community
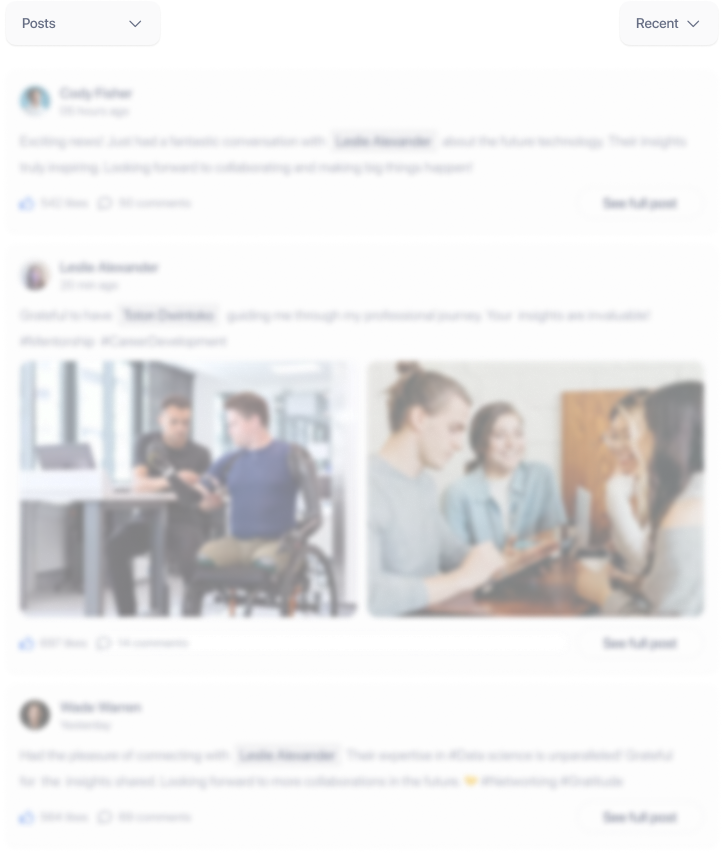