Troy Rock
Project Manager at Griesenbeck Architectural Products, Inc.- Claim this Profile
Click to upgrade to our gold package
for the full feature experience.
-
English -
Topline Score
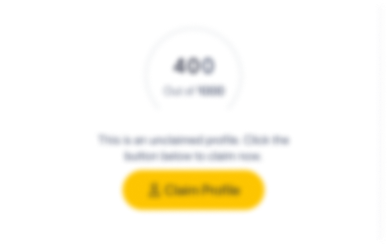
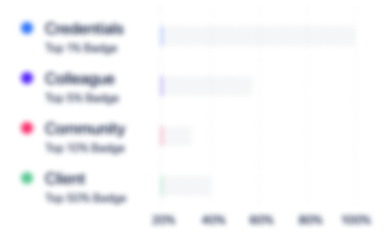
Bio
0
/5.0 / Based on 0 ratingsFilter reviews by:
Credentials
-
Construction Project Management
Coursera Course CertificatesFeb, 2022- Sep, 2024 -
EIT
Florida Board of Professional EngineersMay, 2007- Sep, 2024 -
CQM
US Army Corps of EngineersSep, 2017- Sep, 2024
Experience
-
Griesenbeck Architectural Products, Inc.
-
United States
-
Construction
-
1 - 100 Employee
-
Project Manager
-
May 2022 - Present
-
-
-
Advon Corporation
-
United States
-
Construction
-
1 - 100 Employee
-
Quality Control Manager
-
Mar 2019 - Jan 2022
• Responsible for implementation and management of the Quality Management System of the project, and to work with the PM to ensure timely completion, quality, and implementation of continuous process improvements for all contractual deliverables. • Interfaced and collaborated with designers and management of all trades (HVAC, MEP, concrete-works, architectural, landscaping, fire protection, fire detection & alarm, etc.) to resolve any issues in a timely manner. • Develop, implement and manage the Construction Inspection and Test Plans (ITP) for Definable Features of Work (DFOW), in partnership with the responsible design engineers and construction team members. • Issue Nonconformity Reports (NCRs) for any unapproved work or process. Then manage the NCR to ensure it is resolved in a timely manner. • Conduct regular project status meetings and communicating regularly to keep all project stakeholders up to date on the status of the project and other critical or contractual items. • Monitor Client feedback on construction progress and ensuring high levels of client satisfaction. • Negotiate, manage, and document change orders with the Client and subcontractors. • Manage the documentation and execution of claims from initiation through resolution. • Review and verify subcontractor invoices for materials installed or work completed. • Created and implemented subcontractor quantity tracking procedures, processes, and work tools to manage quantities, unit rates, and expenditures. • Responsible for managing materials, logistics, and vendors as the primary point of contact. • Responsible for prompt recognition, documentation, and communication of scope and design changes and for client authorization prior to scope changes. • Tracked and reported on project budgets, progress, productivity. • Facilitated cross-functional collaboration amongst design leads to process RFIs to address potential conflicts that could have significant cost and schedule impact. Show less
-
-
-
Jacobs
-
Netherlands
-
Retail Office Equipment
-
1 - 100 Employee
-
Project Engineer/ Deputy Quality Control Manager
-
Dec 2015 - Mar 2019
• Administered the Quality Assurance/Quality Control program to ensure compliance of with design specifications and standards. • Analyzed and reported on vendor and subcontractor performance to project managers. • Evaluated material procurement lead-times during project design phases and assessed the impact on production progress, and found alternative sources at lower cost with faster lead times. • Recommended and implement continuous process improvements and action plans to continually reduce waste and save cost. • Reviewed and approve subcontractor & vendor monthly pay applications. • Determines project schedule by studying project plan and specifications, calculating time requirements, and sequencing project elements. • Collaborated with Lead Procurement Manager in the sourcing of materials, including the preparation and issuance of RFPs, gathering submittals for bid analysis, and monitoring vendor and subcontractor performance metrics to ensure suppliers have the capabilities and capacity to align with project demands. • Reviewed sourcing decisions and negotiate contracts to reach budgetary objectives. • Performed site visits to vendors’ facilities to audit and improve their fabrication processes. • Coordinated the proper assembly of all documentation required for project close-out such as shop drawing, as-builts, punch-list, inspection logs, and compliance certificates. • Led preconstruction meetings with the subcontractors or in-house crew before any new activity start to ensure all aspects of the work can be performed successfully Show less
-
-
-
CH2M
-
France
-
Railroad Equipment Manufacturing
-
Project Engineer
-
Jun 2007 - Dec 2015
• Project Engineer assigned to design, constructability & value engineering reviews, schedule preparation, and preparation of MOT plans on various DB and EPC transportation (TxDOT & FDOT), water resources, and commercial projects with contracted values ranging from $400MM to $2B. • Served as the Owner’s Representative and led construction meetings with major subcontractors regarding potential change orders, deviations from scope and schedule concerns. • Created workplans to determine manpower, equipment, cost, and schedule for various features of work. • Monitored subcontractor progress during the construction phase and provided technical oversight of all aspects of the project development. • Ensured subcontractor adherence to all quality, budgetary, scheduling, safety, and material procurement guidelines per their contracts. • Involved in constructability reviews to identify any circumstances that may lead to delays, and cost overruns. • Reviewed submittals to ensure that contractors provided appropriate documentation and record-keeping in conformance with construction requirements. • Provided cost-saving construction method alternatives and giving input on safety improvement policies. • Created monthly progress reports which included Key Performance Indicators (KPI) for measuring vendor and internal performances. • Tracked the progress of construction operations such as the arrival and utilization of materials, supplies, tools, machinery, equipment, and vehicles. • Conducted daily collaboration meetings with subcontractors and in-house labor to set daily targets. • Inputs take-offs and prices into bidding software. • Determined equipment and material needs based on forecasted activities and negotiated terms of contracts with vendors. • Presented formal cost volume reviews and cost reports to senior leadership Show less
-
-
Education
-
Florida Institute of Technology
Master of Science (M.Sc.), Supply Chain Management -
Florida Institute of Technology
Bachelor of Science (BSc), Civil Engineering
Community
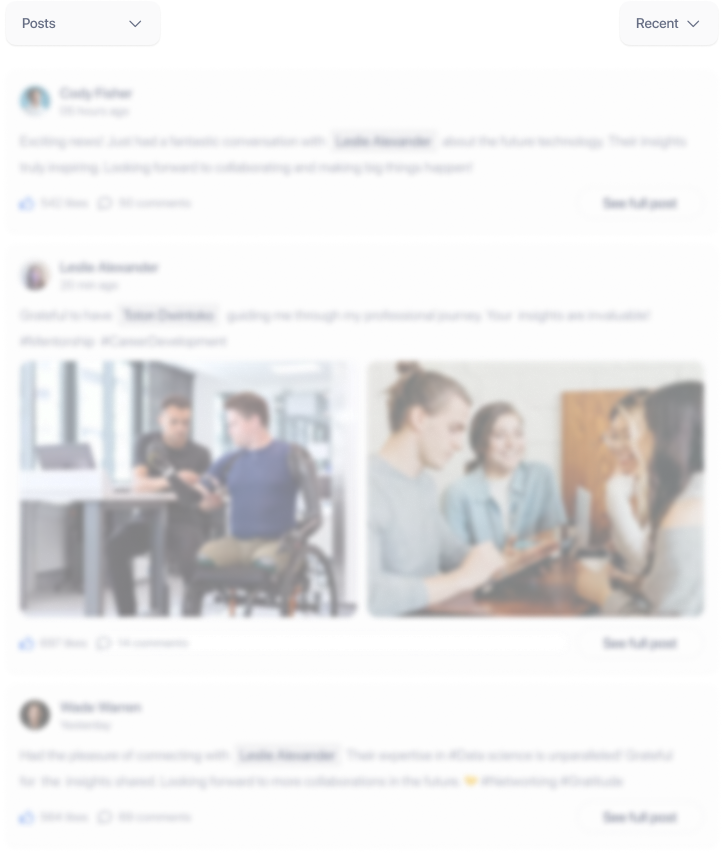