Troy McNeil
Quality Manager at ICON Injection Molding, Inc.- Claim this Profile
Click to upgrade to our gold package
for the full feature experience.
-
English -
Topline Score
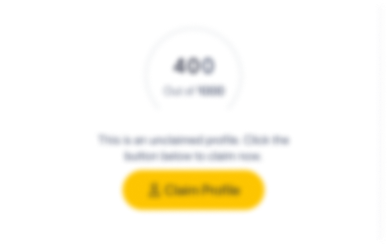
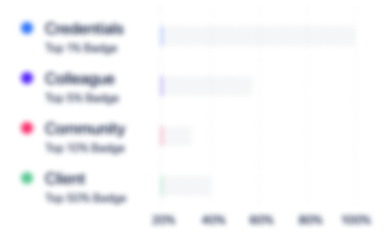
Bio


Credentials
-
Lean Six Sigma Black Belt
Six Sigma Global InstituteOct, 2020- Nov, 2024 -
White Belt Certification
Six Sigma Global InstituteSep, 2020- Nov, 2024 -
Management Certificate
Management BLC,Sep, 2009- Nov, 2024 -
BAC5578 & BAC5713 certification, NADCAP certification
- -
CPR First Aid & BBP
- -
Current FAA Part 121 / 145, DOT Repairman Certificate
Commercial Aircraft Interiors -
JCAB Certified
JCAB -
Senior Management
Boeing Leadership Center
Experience
-
ICON Injection Molding, Inc.
-
United States
-
Plastics Manufacturing
-
1 - 100 Employee
-
Quality Manager
-
Mar 2022 - Present
-
-
-
-
Quality Manager
-
Feb 2015 - Present
FAA Part 145, Part 121 Quality Manager FAA Part 145, Part 121 Quality Manager
-
-
-
-
Repair Station Quality Manager
-
Apr 2018 - Present
Serving as a key stakeholder and displaying ownership of the department’s ability to demonstrate compliance with the AS9100 Quality Manual, Repair Station & Quality Control Manual, Training Program Manual, Production Approval Manual and NADCAP requirements, as applicable. Understands the relationship between the SAE Aerospace Standard and supplementary documents. Actively participates in monitoring, auditing, development and implementation of measures designed to provide objective evidence of conformity.• Directs plans and disseminates the details of inspection standards, methods and procedures to be used to comply with Federal Aviation Regulations.• Serves as the final authority to release to service, components and parts, thereof, to include the relevant certifications.• Properly executes various FAA (Federal Aviation Administration) forms, reports and disclosures, as applicable.• Maintains quality records in accordance with applicable regulations.• Ensures segregation of all non-conforming products.• Chairs MRB (Material Review Board) proceedings and activities.• Participates in the Sales, Planning and RFQ (request for Quote) process by providing information related to certification approach, as well as anticipated risk and mitigation strategies.• Executes departmental work plans in conformance with company policies, procedures, regulations, best practices, management objectives, priorities and financial impact to the business. Supports interdepartmental cooperation.• Designs and implements effective workgroups and systems and proactively drives the progress of work. • Drives On-Time-Delivery (OTD) and Quality metric targets; seeks opportunities to increase productivity and eliminate waste.• Recruits, hires, mentors, manage, and trains employees and assist them in performance improvement and accomplishment of business objectives. Ensures department personnel receive job relevant training.
-
-
-
VARTAN.AERO
-
Germany
-
Aviation and Aerospace Component Manufacturing
-
100 - 200 Employee
-
Quality Manager
-
May 2017 - Apr 2018
• Established and started new FAA 145 Repair Station for company, from application to writing of all manuals and processes & procedures. Building a solid QMS system to attain AS9100 certification. • Coordinated with FAA personnel and auditors to achieve Repair Station Certificate. • Established and started new FAA 145 Repair Station for company, from application to writing of all manuals and processes & procedures. Building a solid QMS system to attain AS9100 certification. • Coordinated with FAA personnel and auditors to achieve Repair Station Certificate.
-
-
-
-
Repair Station Manager
-
Jan 2016 - Apr 2017
Oversight of all production modifications and quality related to repair station aircraft interiors Part.145. Providing leadership and supervision to supporting production in order to meet production-planning and on time delivery goals.. Oversight of all production modifications and quality related to repair station aircraft interiors Part.145. Providing leadership and supervision to supporting production in order to meet production-planning and on time delivery goals..
-
-
-
Universal Aerospace Co., Inc
-
United States
-
Aviation and Aerospace Component Manufacturing
-
1 - 100 Employee
-
Quality Assurance Manager
-
Jan 2015 - Jun 2015
1. Met and exceeded the quality system standards on inspection of all aerospace machined & assembled parts while maintaining a robust QMS. 2. Solved internal and customer issues and provided corrective action plans.3. Managed budget for quality department as needed. 4. Proactively responded to customer on quality related issues in timely manner5. Monitored quality and productivity of the team, and mentored and trained members as needed.6. Conducted Internal Quality Audits, and generated the audit reports, reviewed the report with applicable management and ensure that non-conformance is processed within the Internal Quality Audit system.
-
-
-
-
Production Supervisor
-
2014 - 2015
1. Supervised the everyday to day assembly of aircraft interior parts. Fabricate and assemble aircraft interior panels, stowage bins, sidewalls, closets, and other assemblies manufactured from honeycomb core, fiberglass, aluminum, and other materials.2. Achieved daily production schedule of parts flow. Forecast parts costing and flow.3. Acquired appropriate work order, engineering drawing(s) and plan for assigned job. Located parts on assembly tools, mating parts and/or assemblies per drawing.
-
-
-
Janicki Industries
-
United States
-
Aviation and Aerospace Component Manufacturing
-
1 - 100 Employee
-
Operations / Cell Manager
-
2012 - 2014
1. Managed the production of carbon fiber tooling and aerospace parts to ISO Class 8 cleanroom standards. Developed layup schedules and processes for complex pre-preg parts.2. Led Internal Quality Audits, and generate the audit reports, review the report with applicable management and ensure that non-conformance is processed within the Internal Quality Audit system.Key Accomplishment:1. Achieved BAC5578, BAC5713 certification, and NADCAP certification. Manager Autoclave Operations1. Achieved and coordinated autoclave operation processes and procedures along with activities for all production schedules.2. Accomplished Boeing BAC5578 qualification for aerospace parts fabrication with autoclave. Full over-site new building construction and maintenance for autoclave and stage area. 3. Coordinated with contractors and teams for best locations for cameras and safety devices in building for safe operation for employees. 4. Developed PM’s for new building and autoclave and monitored and maintained them as well as trained all employees SABA and other safety regulations required in the area.Manager Gerber Ply Cutter1. Achieved operation and maintenance of Gerber & Eastman Ply Cutters, Kitting all materials for factory operations.
-
-
-
Boeing
-
United States
-
Aviation & Aerospace
-
700 & Above Employee
-
EDC Quality Assurance Manager
-
1986 - 2012
1) Quality Manager responsible for the production of all aspects of completing aircraft for delivery to customers, to include, interiors, galley, lavatories, seating, exterior structure and all flight control and engine installations and troubleshooting, blueprint reading. Sign off release for flight.2) Coordinated the manufacturing of delivery aircraft to airline customers.3) Everett Delivery Center EHS and safety focal manager 5 yrs. 4) Implementing quality planning, control plan, inspection methodology, and root cause analysis 5) Coordinated Boeing Puget Sound with quality inspections for emergent issues within manufacturing production lines.6) Significantly reduced and controlled expenses by strategic manpower placement. 7) Led cross-functional initiative to achieve implementation of new QMS, and Lean acceptance provisions. 8) Was the leader in creating mechanisms for flow of information between customers, suppliers and operations.9) Proactively suggested operational improvements to enhance quality, improve production times and reduce costs. 10) Created and fostered planning for multiple sites and manufacturing facilities.11) Coordinate problem-solving activities; analyze inputs and develop course of action to ensure timely problem resolution. 12) Accomplished and participated in the support of terms and conditions, as well as pricing negotiations with customers, and communicated requirements.13) Initiated pro-active correspondence to communicate program status, on-going financial viability, and identification of key issues to Senior Management staff on a regular basis. 14) Directed and developed supervisory personnel to ensure efficient and safe operation of the new site. Ensured compliance with company policies and procedures; makes final determinations on hiring and firing decisions; establishes and maintains positive communication with employees and customers.
-
-
Education
-
La Conner High School
High School Diploma, All
Community
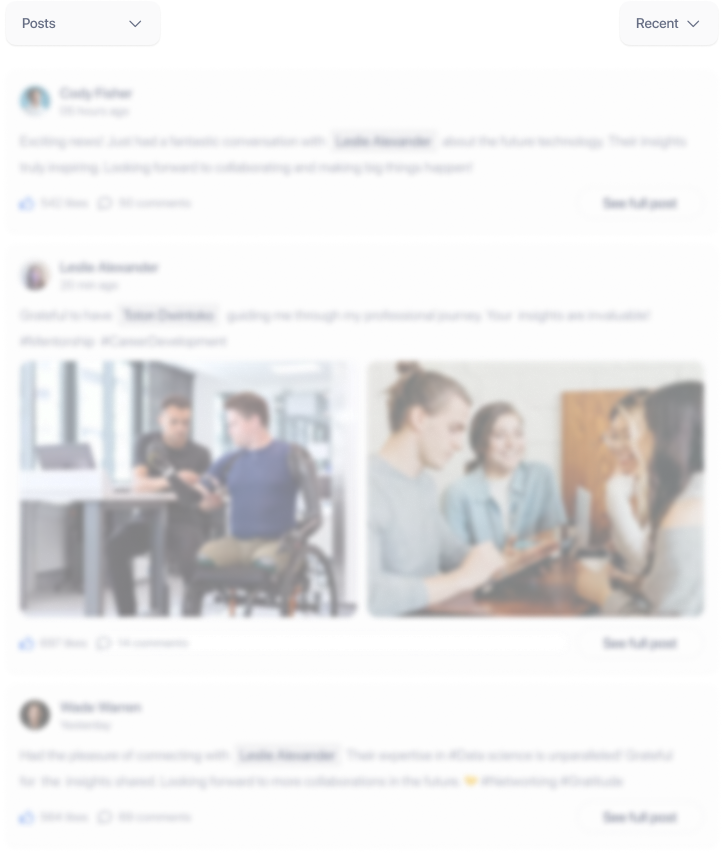