Troy Buckle
Superintendent of Maintenance at Freeman Lumber Co- Claim this Profile
Click to upgrade to our gold package
for the full feature experience.
-
English Native or bilingual proficiency
Topline Score
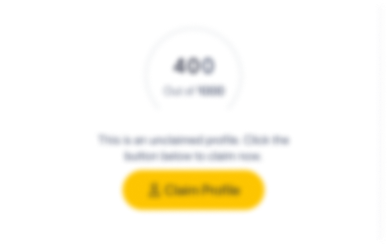
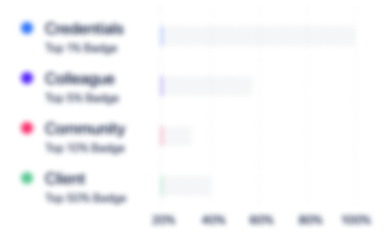
Bio

Eddy Periz
A great team leader, always there for the company anytime and any day. Troy has great energy and ability to pin point the critical improvements while motivating those around him.

Eddy Periz
Troy and I worked successfully for many months on operational improvement projects aimed on efficiency, reliability and delivery. It was a pleasure to have someone as dedicated and resilient as he in our team. When implementing improvements we seek sustainability, so when you have someone on the team who understands people dynamics and is hands on you can root quickly the best work practices.

Eddy Periz
A great team leader, always there for the company anytime and any day. Troy has great energy and ability to pin point the critical improvements while motivating those around him.

Eddy Periz
Troy and I worked successfully for many months on operational improvement projects aimed on efficiency, reliability and delivery. It was a pleasure to have someone as dedicated and resilient as he in our team. When implementing improvements we seek sustainability, so when you have someone on the team who understands people dynamics and is hands on you can root quickly the best work practices.

Eddy Periz
A great team leader, always there for the company anytime and any day. Troy has great energy and ability to pin point the critical improvements while motivating those around him.

Eddy Periz
Troy and I worked successfully for many months on operational improvement projects aimed on efficiency, reliability and delivery. It was a pleasure to have someone as dedicated and resilient as he in our team. When implementing improvements we seek sustainability, so when you have someone on the team who understands people dynamics and is hands on you can root quickly the best work practices.

Eddy Periz
A great team leader, always there for the company anytime and any day. Troy has great energy and ability to pin point the critical improvements while motivating those around him.

Eddy Periz
Troy and I worked successfully for many months on operational improvement projects aimed on efficiency, reliability and delivery. It was a pleasure to have someone as dedicated and resilient as he in our team. When implementing improvements we seek sustainability, so when you have someone on the team who understands people dynamics and is hands on you can root quickly the best work practices.

Credentials
-
CWB Welding Supervisor
-Jun, 2005- Oct, 2024
Experience
-
Freeman Lumber Co
-
Nova Scotia, Canada
-
Superintendent of Maintenance
-
Jun 2023 - Present
-
-
-
Chaleur Forest Products
-
Bathurst, New Brunswick, Canada
-
Maintenance Superintendent
-
May 2020 - Oct 2023
-
-
-
Produits Forestiers Arbec Inc
-
Miramichi, New Brunswick, Canada
-
Superintendent of Maintenance
-
May 2018 - Feb 2022
-
-
-
-
Superintendent- Processing Operations
-
Feb 2017 - May 2018
I am responsible for the safe operations of three processing plants and a dryer facility, managing both company and contractor work forces of forty-five plus employees. My day to day duties include and but are not limited to the following. Responsibility and accountability for all employee’s health and safety while ensuring to maximize production numbers on all four assets, working on both days and nights depending on the business needs. I am also responsible to work with other divisions of the business to understand the needs of train and ship loading, product quality requirements and provide the required material(s) for sales. At times when plants were having quality or low thru put issues, I’ve taken it upon myself to work with the required teams to meet the needs, implementing hourly tracking documents that have since been adopted as normal operating procedures. Show less
-
-
-
Rio Tinto
-
United Kingdom
-
Mining
-
700 & Above Employee
-
Supervisor of Parallel Ore Delivery System Maintenance & Operations
-
Mar 2016 - Dec 2016
Responsible for: - 40+ employees daily including maintenance, operations, and troubleshooting activities.- Any and all contractors at PODS location.- All employees health and safety- For all maintenance and operations on the PODS system.- All daily/ weekly inspections - Ensuring the safe operations of crusher 3, overland conveyor and ore storage.- For work direction, holding employees accountable to meet maintenance requirements, operational requirements, and production targets.- Manage day to day housekeeping requirements of various areas.- Payroll entry for various employees.- Leading and mentoring various tradespersons to meet daily business plans and requirements.*In 2016 the business changed their management model, at which time I volunteered to help the business by moving into a supervisory role.* Show less
-
-
Superintendent of Ore Delivery System Maintenance & Ore Car Shop
-
Jun 2015 - Feb 2016
Responsible for: - Over 90 employees, that worked with PODS (OLC/ crusher 3) crushers 1 and 2, loading pockets 2 and 3, ore car/ locomotive shop, and ATO/ rail.- Established the LMF (locomotive facility) to be a functioning maintenance shop.- Mentor supervisors on the day to day maintenance requirements to meet the business daily production needs.- Health and safety housekeeping in multiple areas.- HR requirements.- Government inspector tours and providing updates to government inspectors.- Cost and budgeting of the department.- Work to reduce cost and safely increase production.- Work with reliability teams to prioritize, manage, and implement DE projects.- Worked PDI teams for departmental improvements.- Implement hourly workforce to manage PODS maintenance and troubleshooting activities.- Reduce the cost of monthly and yearly contractor expenses. Show less
-
-
Ore Delivery Systems Shutdown Coordinator
-
Dec 2014 - May 2015
Direct duties:- Work in conjunction with shutdown planner and areas supervisors and planner.- Identify required shutdown work on the areas operating assets.- Responsible to assist with the populating the shutdown gantt chart.- Review and approve final schedules.- Execute monthly and annual shutdown activities for all of ODS, including: ATO (Automatic Train Operation), rail, PODS (Parallel Ore Delivery System), three crushers, and ore storage facility.- Facilitate daily update meetings to all the assets stakeholders.- Daily report to upper management on the progress status and health and safety updates of the shutdown.This role required me to work with, the hourly workforce in conjunction with various contracting companies, being accountable to manage both. Show less
-
-
Superintendent of Main Service Shops& Warehousing
-
May 2012 - Nov 2014
Responsible for:- Mentoring and coaching the senior supervisor in their leadership role.Direct duties:- Departmental yearly planning.- Budgeting.- Meeting health and safety requirements.- Meeting shop housekeeping expectations, implementing lean initiatives.- Implementing 5 S initiatives.- Facilitating weekly health and safety meetings, monthly cost meetings.- Attending weekly managers safety meeting.- Implementing, supporting, continuous improving program.- Managing apprenticeship program for multiple trades.- Facilitate grievance process, providing updates to human resources.- Assisting, approving, and managing staff and hourly annual vacation schedules, within the CA. Show less
-
-
Senior Supervisor of Main Service Shops/ Central Services.
-
Jan 2011 - Apr 2012
Responsible for:- Day to day work execution and operations of the following shops.1. Carpenter 2. Automotive/ HME 3. Cranes and Elevator4. Fabrication5. Machine6. Component7. Pallet8. Ore Car/ Locomotive- Mentor, lead, and direct shop supervisors in the day to day requirements of the various areas.- Mentoring supervisors in all health and safety rules and regulations.- Understanding and executing in collective agreements meeting HR requirements.- Coaching supervisors on executing daily work plans and holing employees accountable for work progress.- Mentor supervisor to manage and understand their monthly and annual budget.- Coach supervisors to promote health and safety, pristine housekeeping, and meeting industry standards wrench-times.Direct duties:- Accountable and manage a $45 million budget.- Provide, implement, and update on departmental government directives.- Meet with crane and elevator government inspectors to ensure all equipment met codes and regulations, in the event of any directives on set equipment provide government officials with action plans and completed updates in order to maintain annual certifications. I was accountable for ore car and loco availability, pallet fleet and HME equipment availability. Show less
-
-
Supervisor of Fabrication Machine, Component and Pallet Shop
-
Jan 2010 - Dec 2010
Responsible for:- Executing daily work plans for 30+ employees in various trades.- Employees health and safety.- Various shops housekeeping.- Providing a safe and healthy workplace.- Providing leadership and mentoring of various tradespersons.- Managing any daily break-ins for the entire project, prioritizing and meeting production requirements.Daily and monthly reports highlighting:- Health and safety -Cost and budgets-Shops performance that were reported on in monthly managers meeting. Show less
-
-
Planner of Fabrication Machine, Component and Pallet Shop
-
Jan 2009 - Dec 2009
- Weekly and monthly planning.- Long term planning.- Securing parts and materials for all work.- Providing all safety requirements to complete the jobs.- Provide detailed schedule to supervisor, utilizing all required workers to meet the business requirements.- Meet daily with the supervisor to discuss daily activities and upcoming work.- Provide detail job packages with safe work procedures and all relative documents.
-
-
Supervisor of Mobile Maintenance
-
Jan 2008 - Jan 2009
- Executing planned maintenance for the heavy mining equipment fleet (over 70 pieces of various equipment).- Prioritize and manage any daily break-ins in order to meet daily production requirements.Responsible for the following:- Employee health and safety.- Multiple maintenance bay's housekeeping (13 bays).- Payroll entry (approximately 40-45 workers per shift).- Provide detail shift reports for upper management and oncoming shifts.- Asset management compliance.- Accountable for haul truck availability. Show less
-
-
Team Leader/ Planner of Component and Pallet Shop
-
Oct 2005 - Dec 2007
- Planning and executing maintenance activities for the indurating pallet fleet.- Managed repairs of various components for the entire company (pumps, gearboxes, fluid drives, etc...) Responsible for the following: - Housekeeping requirements - Providing a safe and healthy workplace, meeting the health and safety requirements. - Payroll Entry. - Meeting and being below monthly and annual budgets.Providing daily reports and monthly summaries of: - Health and Safety. - Pallet fleet availability. - Asset management compliance. - Employee productivity. - Cost updates.- Accountable to manage any daily break-ins, ensuring to meet demands of the business needs and production requirements. Show less
-
-
-
Bowringer
-
Newfoundland And Labrador, Canada
-
Supervisor
-
Jun 2005 - Oct 2005
- Manage workers You with various trades and crews to perform required maintenance on equipment and infrastructure. - Responsible for employees health and safety - Meeting customers timelines while meeting health and safety needs. -Providing daily reports to upper management. - Manage workers You with various trades and crews to perform required maintenance on equipment and infrastructure. - Responsible for employees health and safety - Meeting customers timelines while meeting health and safety needs. -Providing daily reports to upper management.
-
-
-
Elite Trade Painting
-
New Brunswick, Canada
-
General Foreman
-
May 2003 - Sep 2003
Resposible for: - Employees health and safety. - Provide a safe and healthy workplace. - Cost estimating. - Managing multiple crews and projects. - Securing parts and equipment for multiple jobs. - Planning and scheduling of multiple jobs. - Executing and meeting deadlines of multiple jobs. - Providing payroll data and daily and weekly updates to company owners. - Mentoring, coaching lead hands and employees. Resposible for: - Employees health and safety. - Provide a safe and healthy workplace. - Cost estimating. - Managing multiple crews and projects. - Securing parts and equipment for multiple jobs. - Planning and scheduling of multiple jobs. - Executing and meeting deadlines of multiple jobs. - Providing payroll data and daily and weekly updates to company owners. - Mentoring, coaching lead hands and employees.
-
-
Education
-
NBCC (New Brunswick Community College)
Diploma, Welding Engineering Technology/Technician -
NBCC (New Brunswick Community College)
Civil Engineering Technology/Technician, 3.0 GPA -
Labrador City Community College
Trades Program, Carpentry/Carpenter -
Avalon Community College
Trades Program, Welding -
Menihek Integrated High School
High School
Community
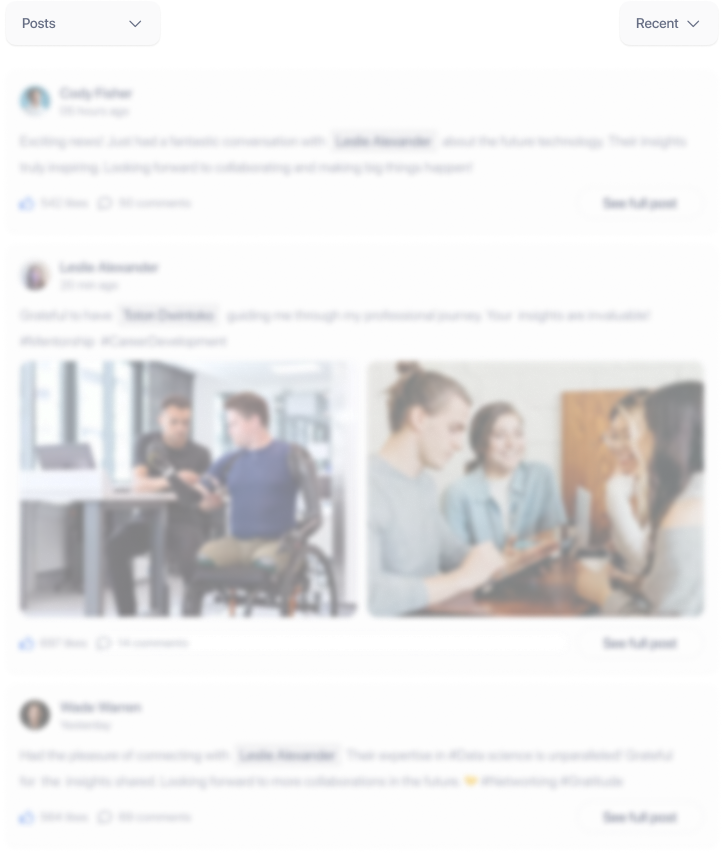