Troy Alvarez
Senior Cost Accounting Manager at Standard Fiber- Claim this Profile
Click to upgrade to our gold package
for the full feature experience.
Topline Score
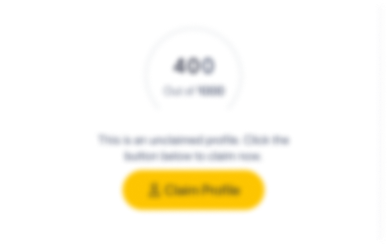
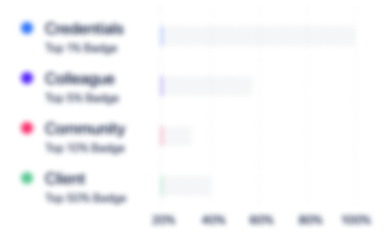
Bio


Experience
-
Standard Fiber
-
United States
-
Textile Manufacturing
-
1 - 100 Employee
-
Senior Cost Accounting Manager
-
Dec 2022 - Present
-
-
-
Aruze Gaming
-
United States
-
Gambling Facilities and Casinos
-
100 - 200 Employee
-
Cost Accounting Manager
-
Dec 2015 - Dec 2022
¥ Wrote inventory control procedures for a 45 million inventory ¥ Implement a cycle count program; 98%-dollar inventory accuracy ¥ Mapped 50,000 square feet of warehouse space to scale and subdivided it into stocking locations ¥ Facilitated the implementation of a bar code system ¥ Prepared labor, material, and overhead reports for senior management ¥ Facilitate weekly meetings with team members with purpose of continuous improvement ¥ Prepared a 260day (1yr) plan to achieve specific measurable goals with regard cost, inventory transaction discipline, and culture ¥ Organized time studies of the labor and overhead time consumed in the assembly of finished goods. The results of the studies were used to establish standard cost of finished goods. ¥ Worked closely with Operations in all areas including training, reporting, labor managment, and inventory control Show less
-
-
-
Menlo Energy Florida, LLC
-
Dade City, Florida
-
Senior Cost Accountant
-
Apr 2013 - Dec 2015
• Create, manage, and edit bill of materials for products. Bills of materials include raw material, direct labor, indirect manufacturing costs, and freight in. Bills of material were created using historical refining data and time studies. • Produce a daily production report for management. The report depicts refining yield , an inventory reconciliation, rate of output, and manufacturing variances • Oversee the manufacturing and financial accounting for the glycerin refinery. This includes review of monthly financial statements, adjusting journal entries, accruals, and account reconciliation • Daily calculation of manufacturing variances including inventory variances, direct labor variances, overhead variances, purchase price variances, and overhead variances • Conduct detailed studies of historical yield and analysis of factors impacting manufacturing efficiency. Factors include: ambient temperature, overtime, regular preventive maintenance, the availability of spare parts, raw material specifications Show less
-
-
-
Biodiesel of Las Vegas
-
North Las Vegas Nevada
-
Cost Accounting Manager
-
Oct 2011 - Aug 2012
• Reviewed daily production batches of biodiesel and compared actual consumption of material, labor, and time to the bill of material. Variances were analyzed and used to measure and improve efficiency • Established inventory control procedures for spare parts, raw material, and finished good inventory • Worked with Purchasing, Production, and Sales in order to create a 12 month profit and loss statement and Balance Sheet projection for a new biodiesel plant. This included establishing needs for raw material, labor, overhead and all operating necessities of the plant • Created bills of materials for biodiesel fuel by working with production management, production personnel and conducting independent research of currently operating biodiesel plants • Adjusted budgets according to actual usage of time, materials, and market changes • Compiled a fixed assets and cost segregation schedule for the fixed assets of the facility • Analyzed overall efficiency of the plant by inserting actual labor, material, overhead , and other operating expenses into the projected 12 month financial statements for viability analysis of multiple scenarios • Ongoing analysis of all aspects of production and their impact on projected profit margins Show less
-
-
-
GENESIS Pharma
-
Greece
-
Pharmaceutical Manufacturing
-
100 - 200 Employee
-
-
Jun 2006 - Sep 2007
In this position I was accountable for the ongoing analysis of process constraints, target costing projects, margin analysis, and tracing costs back to underlying activities. Constructed and monitored those cost-effective data accumulation systems needed to provide an appropriate level of costing information to management.• Collected and analyzed data to determine standard and actual cost of pharmaceutical products used for annual standard cost update, including raw material, direct labor, overhead, and Quality Control• Trained Warehouse, Production, Purchasing, and Scheduling personnel in inventory control, work order processing, cost analysis, and interpretation of bills of material• Collaborated with IT, Warehouse, and Production personnel in establishing internal inventory controls including cycle counting• Assisted in overseeing the relocation of manufacturing from Michigan to Nevada Show less
-
-
-
2006 - 2007
-
-
-
-
-
2003 - 2006
-
-
-
2003 - 2006
-
-
-
2003 - 2006
-
-
-
Aristocrat
-
Australia
-
Gambling Facilities and Casinos
-
700 & Above Employee
-
-
2002 - 2003
-
-
-
2002 - 2003
-
-
Education
-
New Mexico State University
Bachelor's degree, Accounting and Finance
Community
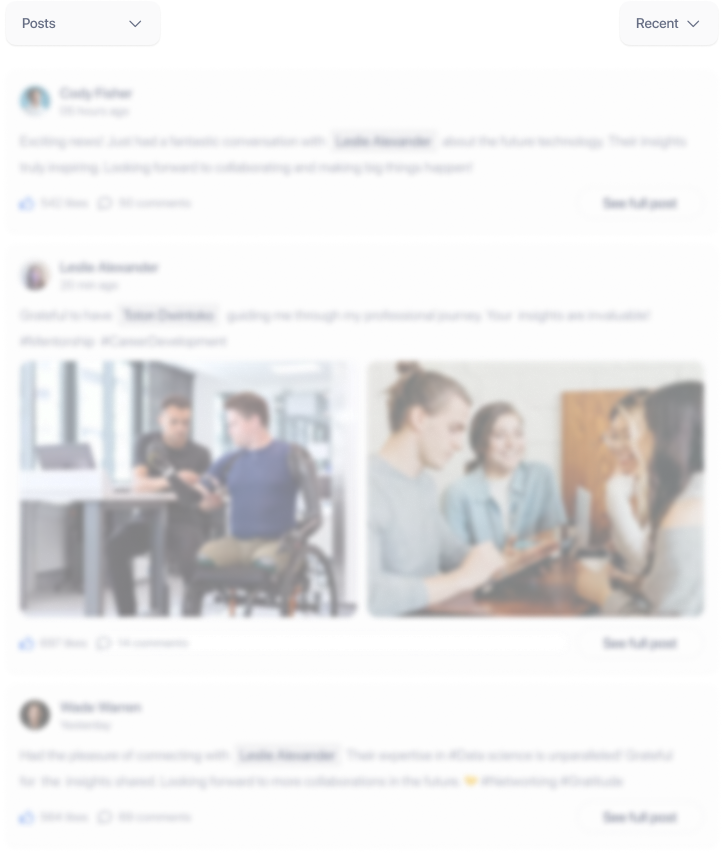