Travis Lansdown
Production Planner at Mercedes Packaging Pty Ltd- Claim this Profile
Click to upgrade to our gold package
for the full feature experience.
Topline Score
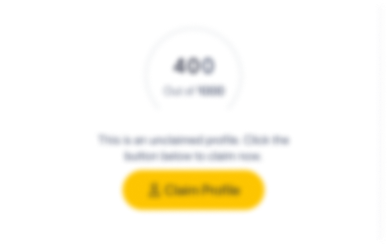
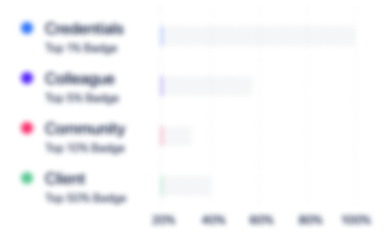
Bio
0
/5.0 / Based on 0 ratingsFilter reviews by:
Experience
-
Mercedes Packaging Pty Ltd
-
Australia
-
Plastics Manufacturing
-
1 - 100 Employee
-
Production Planner
-
Jun 2022 - Present
-
-
-
Amcor
-
Switzerland
-
Packaging and Containers Manufacturing
-
700 & Above Employee
-
Operations Analyst
-
Nov 2017 - May 2022
• Project Coordination of a SMED (Single Minute Exchange of Die) campaign, based on shrinking the length of setup time needed for each print run. • Waste reporting which reviews the reasoning of production waste between raw material input and finished-goods output. • Capacity planning which reviews how labour resources could/should be used compared to a rolling 13-week demand forecast. • Ad-hoc analyses which scrutinise operational occurrences and behaviours. • Job costing variance analysis, to ensure the accurate closure of job lots. • Fill in production planner, ensuring raw materials and WIP is transformed into Finished Goods to meet customer lead times.
-
-
-
Samsung Australia
-
Australia
-
Computers and Electronics Manufacturing
-
300 - 400 Employee
-
Collaborative Planning, Forecasting & Replenishment Specialist
-
Aug 2016 - Aug 2017
(Maternity Leave Coverage role). - Australian Samsung DC to JB Hi Fi fulfilment focus (4 to 16 week horizon). - 120 Collaborative SKU's across Tablet / TV&AV / Home Appliances / Accessories. - Provision of analytical insight for meetings with National Account Managers & JB Hi Fi Buyer. - Ensure Orders from JB HiFi match the agreed plans and take corrective actions if otherwise. (Maternity Leave Coverage role). - Australian Samsung DC to JB Hi Fi fulfilment focus (4 to 16 week horizon). - 120 Collaborative SKU's across Tablet / TV&AV / Home Appliances / Accessories. - Provision of analytical insight for meetings with National Account Managers & JB Hi Fi Buyer. - Ensure Orders from JB HiFi match the agreed plans and take corrective actions if otherwise.
-
-
-
-
Demand Planner
-
Jan 2016 - Aug 2016
(Maternity Leave Coverage role) - German Manufacturing to Australian Distribution Centre focus. - 180 SKU's across Kitchen / Laundry / Refridgeration / Vacuum categories. - Attendance to Monthly review meetings with Product Managers and Logistics Planning Manager. - Submit rolling 12 month manufacturing plans in SAP APO post monthly Demand Reviews. (Maternity Leave Coverage role) - German Manufacturing to Australian Distribution Centre focus. - 180 SKU's across Kitchen / Laundry / Refridgeration / Vacuum categories. - Attendance to Monthly review meetings with Product Managers and Logistics Planning Manager. - Submit rolling 12 month manufacturing plans in SAP APO post monthly Demand Reviews.
-
-
-
-
Assets Analyst
-
Feb 2014 - Nov 2015
As the Assets Analyst at Viscount Logistics Services (VLS), I was the analytical, reporting and administrative intermediary between VLS and key customer Coles Supermarkets. Completed Ad-hoc analyses: • Expensed an additional $80k labour, allowing VLS to issue over 1.3 million crates in the week prior to Christmas 2014. This volume was a 10-year record at the time and prevented lost revenue if the crates were not available to issue. • Experienced an 8.4% increase to the profitability of one Resource Recovery Unit by servicing a high volume low value customer from a different state. Budget vs. Actual tracking: • Identified VLS were favourable by 3 to 10% on actual transport expenditure compared to budgeted expenditure throughout 9 Coles reporting periods throughout 2014/15. • Populated a daily estimate tool that reviewed revenue and operating expenses to identify the likelihood of meeting weekly budget figures. Reporting Template Implementation and Revision: • Revised MS Excel templates used by the VLS Equipment Control Team to report their proactive and pre-emptive efforts. These efforts more often then not added close to $40k towards a weekly financial result. Prior to this revision, their contributions were not made so clear to Coles throughout the reporting week and left the perception the value-add of VLS was not being delivered. • Implemented a web-based portal (Quickbase) that captured the trading activity of each Resource Recovery Unit that washed and issued crates. This portal removed 6 MS Access Databases containing multiple spellings of customer names, as well as sped up the daily reporting requirements back to Coles. • Keyed the formulae and conditional formatting into a RRU Operational Analysis, which based on heat mapping ideology highlights KPI measures that show excellence and those needing improvement. These measures include Machine run time, use of personnel, as well as crates washed as a comparison to the same week last year.
-
-
-
Coca-Cola Amatil
-
New Zealand
-
Retail
-
1 - 100 Employee
-
Transport Load Coordinator
-
Aug 2010 - Feb 2014
Route Planning (Sept 2012 - February 2014): Using SAP and scheduling software, Sales orders from smaller transactional customers were transitioned into Transport Routes. Per day close to 800 orders spread across 14 transportation zones in regional QLD were routed. Depending on the transportation zone, these orders were diversified between 48, 72 & 96 hour lead times & adherent to different carrier requirements. Bulk Load Planning (August 2010 - Sept 2012): Orders sent from the larger Grocery (Woolworths/Coles), Alcohol (ALM) and Petroleum (Caltex/BP/Coles Express) customers reviewed each day to ensure the stock they required could be provided in the timeframes requested. Stock On Hand was compared to the daily demand from all customers, and if need be timeslots with retailers were re-negotiated when production plans did not meet. For transport efficiency, out of stock lines were replaced by consulting re-buyers before orders became transport loads, In just over the two year tenure, I looked after WA (approx. 60,000 cases per day), NSW & QLD (approx 100,000 cases per day each).
-
-
-
Toll Holdings Limited
-
United Kingdom
-
1 - 100 Employee
-
Logistics Coordinator
-
Jul 2004 - May 2010
Operations Planner (January 2006 - May 2010): Utilising scheduling software orders sent from Arnotts Biscuits Ltd. were scheduled into transportation routes. The planning logic was to balance the warehouse efficiencies against those gained in transportation. Most of the orders contained 35-45 cartons per drop and delivered to the rear dock of supermarkets. B2B Customer Service Representative (July 2005 - January 2006): Provision of on-call assistance to Toll Fashion clients who used Toll Lite to print consignment notes. Logistics Controller (February 2005 - July 2005): Clerical duties for the receiving function within the Nike contract. Planning and Development Officer (July 2004 - February 2005): Preparation of RFQ / RFT documentation utilising cost models which project the warehousing activity of upcoming warehousing contracts. Controlled a $20m reverse logistic project involving the unsold DVD Discs from Coles Supermarkets back to Suppliers.
-
-
Education
-
La Trobe University
Graduate Certificate, Business Analytics -
Deakin University
Graduate Diploma, Information Systems -
RMIT University
Bachelor of Business, Transport and Logistics Management -
RMIT University
Advanced Diploma, International Trade
Community
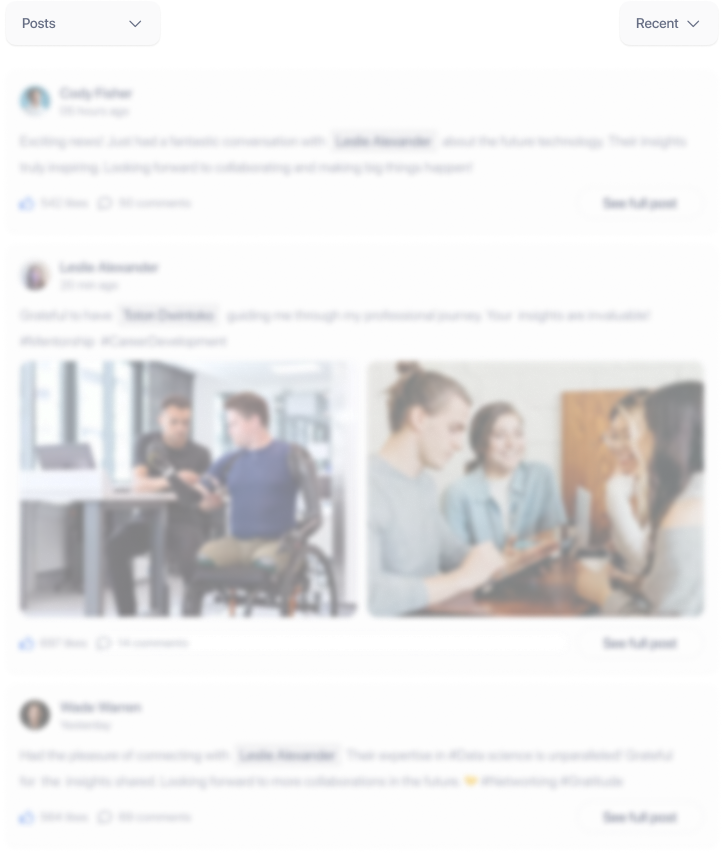