Travis Horak
Supply Chain Director at Kanto Corporation- Claim this Profile
Click to upgrade to our gold package
for the full feature experience.
Topline Score
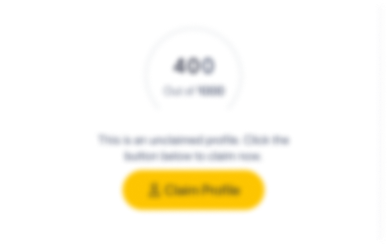
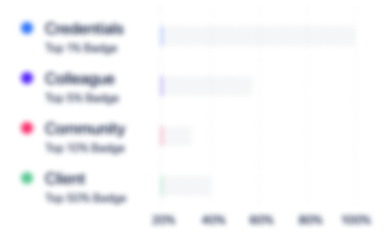
Bio

Jen Boardman
Travis is one of the most impressive systems analysts I have ever worked with. He was very successful in the role of Materials Manager at DCI, but I feel his greatest strengths are around planning, analysis and strategy. I was always confident that he would analyze data accurately, no matter how complicated, to give the rest of the management team the most detailed picture in the moment so we could make smart decisions. He is regularly thinking several steps ahead of everyone else and uses that skill to make tactical moves and well thought out suggestions. He's incredibly well rounded in his knowledge and experience with many facets of manufacturing, not only the purchasing side of the business. Travis was an integral part of the management team, helping us to achieve incredible production and sales growth year over year and influencing many important corporate decisions. He is fantastic to work with, collaborative in team environments and gives 100% every day. He's one of the few people I've worked with who have earned my complete trust and confidence in his skills and abilities. I have truly amazing memories of our years working together and would be thrilled to work with him again in any capacity.

James Priester
I knew Travis as the Quality Assurance Manager at Pioneer Pump. It was always a pleasure to work with Travis because he was always a "straight shooter". His methodical and accurate exchange of information was effective in not only solving quality problems that were uncovered in the field, but also in helping me provide a fair and informed action for our customers.Responsiveness and completeness are his hallmarks. Anyone could esteem Travis as a valuable employee and colleague.

Jen Boardman
Travis is one of the most impressive systems analysts I have ever worked with. He was very successful in the role of Materials Manager at DCI, but I feel his greatest strengths are around planning, analysis and strategy. I was always confident that he would analyze data accurately, no matter how complicated, to give the rest of the management team the most detailed picture in the moment so we could make smart decisions. He is regularly thinking several steps ahead of everyone else and uses that skill to make tactical moves and well thought out suggestions. He's incredibly well rounded in his knowledge and experience with many facets of manufacturing, not only the purchasing side of the business. Travis was an integral part of the management team, helping us to achieve incredible production and sales growth year over year and influencing many important corporate decisions. He is fantastic to work with, collaborative in team environments and gives 100% every day. He's one of the few people I've worked with who have earned my complete trust and confidence in his skills and abilities. I have truly amazing memories of our years working together and would be thrilled to work with him again in any capacity.

James Priester
I knew Travis as the Quality Assurance Manager at Pioneer Pump. It was always a pleasure to work with Travis because he was always a "straight shooter". His methodical and accurate exchange of information was effective in not only solving quality problems that were uncovered in the field, but also in helping me provide a fair and informed action for our customers.Responsiveness and completeness are his hallmarks. Anyone could esteem Travis as a valuable employee and colleague.

Jen Boardman
Travis is one of the most impressive systems analysts I have ever worked with. He was very successful in the role of Materials Manager at DCI, but I feel his greatest strengths are around planning, analysis and strategy. I was always confident that he would analyze data accurately, no matter how complicated, to give the rest of the management team the most detailed picture in the moment so we could make smart decisions. He is regularly thinking several steps ahead of everyone else and uses that skill to make tactical moves and well thought out suggestions. He's incredibly well rounded in his knowledge and experience with many facets of manufacturing, not only the purchasing side of the business. Travis was an integral part of the management team, helping us to achieve incredible production and sales growth year over year and influencing many important corporate decisions. He is fantastic to work with, collaborative in team environments and gives 100% every day. He's one of the few people I've worked with who have earned my complete trust and confidence in his skills and abilities. I have truly amazing memories of our years working together and would be thrilled to work with him again in any capacity.

James Priester
I knew Travis as the Quality Assurance Manager at Pioneer Pump. It was always a pleasure to work with Travis because he was always a "straight shooter". His methodical and accurate exchange of information was effective in not only solving quality problems that were uncovered in the field, but also in helping me provide a fair and informed action for our customers.Responsiveness and completeness are his hallmarks. Anyone could esteem Travis as a valuable employee and colleague.

Jen Boardman
Travis is one of the most impressive systems analysts I have ever worked with. He was very successful in the role of Materials Manager at DCI, but I feel his greatest strengths are around planning, analysis and strategy. I was always confident that he would analyze data accurately, no matter how complicated, to give the rest of the management team the most detailed picture in the moment so we could make smart decisions. He is regularly thinking several steps ahead of everyone else and uses that skill to make tactical moves and well thought out suggestions. He's incredibly well rounded in his knowledge and experience with many facets of manufacturing, not only the purchasing side of the business. Travis was an integral part of the management team, helping us to achieve incredible production and sales growth year over year and influencing many important corporate decisions. He is fantastic to work with, collaborative in team environments and gives 100% every day. He's one of the few people I've worked with who have earned my complete trust and confidence in his skills and abilities. I have truly amazing memories of our years working together and would be thrilled to work with him again in any capacity.

James Priester
I knew Travis as the Quality Assurance Manager at Pioneer Pump. It was always a pleasure to work with Travis because he was always a "straight shooter". His methodical and accurate exchange of information was effective in not only solving quality problems that were uncovered in the field, but also in helping me provide a fair and informed action for our customers.Responsiveness and completeness are his hallmarks. Anyone could esteem Travis as a valuable employee and colleague.

Experience
-
Kanto Corporation
-
United States
-
Chemical Manufacturing
-
1 - 100 Employee
-
Supply Chain Director
-
Jul 2022 - Present
-
-
-
DCI International | DCI Edge
-
United States
-
Medical Equipment Manufacturing
-
1 - 100 Employee
-
Materials Manager
-
Sep 2017 - Jul 2022
• Implemented Intuitive ERP buying process to improve flexibility - Created reporting to respond proactively to projected shortages - Supported average YoY growth of 28% for 2017 through 2021 54% in 2021 alone, 77% growth in equipment business • For parts business developed stocking level algorithm to allow for a 20% inventory reduction with 98% on time delivery(pre-covid), most shipments same day • Reset Harmonized Tariff Codes to save company over $3.5 million • Managed international supply chain through Covid chaos and major growth - Adjusted to ocean transit times increasing by up to 700% - Booking dropped by 80% initially only to increase by 148% over 2019 rate - Reacted to many domestic and international supplier quarantines - Company was able to maintain industry leading growth, OTD, and lead time - Added new suppliers and worked with existing suppliers on their capacity and yield to increase component availability • Developed sophisticated reporting tools for forecasting business growth, product mix, material lead times, and outgoing product lead times - Reviewed with ownership weekly and they are a leading resource for decision making and strategic initiatives Show less
-
-
-
Cascade Controls Inc.
-
Portland, Oregon Area
-
Materials Manager
-
Jan 2016 - Sep 2017
• Created Planning Department to increase efficiency of production and provide better lead times and expediting to our customers • Reorganized warehouse and developed picking procedures that reduced picking errors by 90% and increased efficiency by 25% • Renegotiated prices and terms with multiple suppliers, saved over $200K annually • Reduce inventory by 20%, freeing up $1 million of capital • Created Planning Department to increase efficiency of production and provide better lead times and expediting to our customers • Reorganized warehouse and developed picking procedures that reduced picking errors by 90% and increased efficiency by 25% • Renegotiated prices and terms with multiple suppliers, saved over $200K annually • Reduce inventory by 20%, freeing up $1 million of capital
-
-
-
Pioneer Pump
-
United States
-
Machinery Manufacturing
-
1 - 100 Employee
-
Planning/Procurement Manager
-
Jan 2015 - Nov 2015
• Implemented metric driven process to increase multi-sourcing activities leading to improvements in cost, quality, and lead time• Posted 8 of 9 periods with favorable purchase price variance, resulting in hundreds of thousands of savings for company• Reduced inventory by 8 million dollars over 6 month period• Percentage of reimbursement credits received for defective material increased from 15% to 74% of material and time loss value
-
-
Planning Manager
-
Feb 2014 - Jan 2015
• Turned around a planning department that was ineffective and inefficient- Improved 90 day trailing on time delivery for equipment from 66% to 88% within 5 months- Increased throughput in terms of revenue by 42% from Q4 to Q2- Reduced idle manufacturing time due to material shortages to near zero- Exceeded revenue budget in first full quarter by 56%• Modified ERP system demand prioritization to more effectively use components to satisfy both equipment and parts orders• Developed cross functional material forecast based on reliable historic data and input from sales and marketing- Average lead time of stainless pumps reduced from 11 weeks to 6 weeks Show less
-
-
Quality Manager
-
Jan 2013 - Jun 2014
• Management representative for successful ISO 9001:2008 surveillance and re-registration audits- First audit passed with only one month to prepare after 11 months of neglect by prior quality manager- Second audit passed while holding both Planning Manager and Quality Manager positions• Built and implemented process for tracking of defective materials - Developed method for returning Non-Conforming Materials (NCM) to vendors for credit or rework- Over $300,000 in credits received in first 6 months- Created process for detailed and timely reports to support supplier corrective actions• Setup Quality area and defined inspection procedures- Wrote standards for inspection and documentation of first articles and NCM - Created process for scraping of low cost defect parts that reduced the NCM handling time by 1 hour and allowed for trace-ability Show less
-
-
Manufacturing Engineer
-
Jul 2010 - Jan 2013
• Developed one piece flow assembly line - Reduced lead time from 8 weeks to 3 weeks on average - Designed process to schedule production slots for sale to customers • Took an aged and obsolete ERP System and greatly improved functionality - Created multiple new reports to express data in actionable ways- Changed process and tools to begin using the MRP module to replace a very poor process for material sourcing and planning• Key player on SyteLine implementation team, provided the bulk of the practical and procedural direction Show less
-
-
-
PPM
-
United States
-
Machinery Manufacturing
-
1 - 100 Employee
-
Manufacturing Engineer
-
Aug 2006 - Jul 2010
• Lead multiple projects to improve lead time, reduce cost and minimize errors - Consolidated multiple schedules to an MRP driven schedule - Evaluated and revised Safety Stock levels - Reduced data entry time for shop personnel • Coordinated outsourcing both locally and internationally - Key player in establishing a manufacturing presence in Mexico - Helped balance manufacturing resources with global demand • Reduced cost and improved function of manufactured equipment • Managed MRP system and created work instructions • Modified forms and procedures to reduce non-value added activities • Streamlined advance purchasing process and implemented in foreign site Show less
-
-
-
-
Quality Assurance Inspector
-
Aug 2003 - Sep 2005
• Worked unsupervised as the sole swing shift inspector for over one year • Interpreted technical prints and verified dimensions to insure quality • Confirmed accuracy of materials from lasers industrial machines • Participated in successful ISO 9001 registration • Worked unsupervised as the sole swing shift inspector for over one year • Interpreted technical prints and verified dimensions to insure quality • Confirmed accuracy of materials from lasers industrial machines • Participated in successful ISO 9001 registration
-
-
-
-
Installer
-
Jun 2002 - Sep 2002
• Assembled multiple types and styles of office furniture • Attention to detail required for professional installation • Assembled multiple types and styles of office furniture • Attention to detail required for professional installation
-
-
Education
-
Oregon State University
BS, Manufacturing Engineering
Community
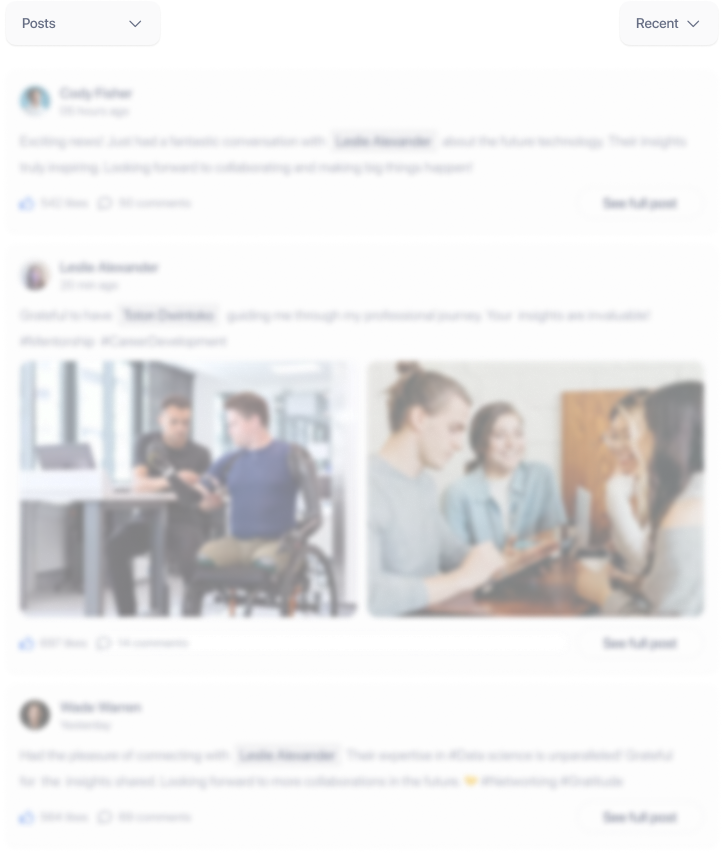