Tracy Clark
Quality / Process Improvement Specialist at Blend Supply- Claim this Profile
Click to upgrade to our gold package
for the full feature experience.
Topline Score
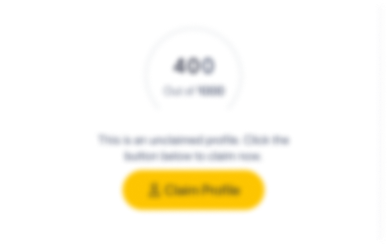
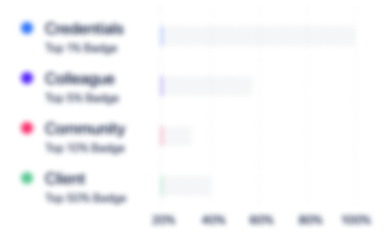
Bio


Experience
-
Blend Supply
-
United States
-
Paint, Coating, and Adhesive Manufacturing
-
1 - 100 Employee
-
Quality / Process Improvement Specialist
-
Jan 2023 - Present
-
-
-
King Aerospace
-
United States
-
Aviation and Aerospace Component Manufacturing
-
1 - 100 Employee
-
Supply Technician
-
Sep 2021 - Sep 2022
Receives, stores and issues equipment, material, supplies, merchandise, tooling, and compiles stock record in support of the aircraft. Orders, distributes and maintains an inventory of adequate parts, supplies and equipment, to be available for distribution to all team members in support of mission requirements, keeping detailed records of each item received and issued. Ensures the efficient and effective repair of aircraft components, assemblies and other mission-support equipment and tools by utilizing repair orders or other acceptable repair procedures. Generates reports and updates Management Information System for Aviation on use of stock handling equipment, adjustments of inventory counts and stock records, spoilage or damaged stock, location changes, and refusal of shipments.
-
-
-
US Navy
-
United States
-
Armed Forces
-
700 & Above Employee
-
Senior Enlisted Leader
-
Jul 2017 - Apr 2020
Direct liaison between Commanding Officer and 171 junior enlisted personnel in achieving commandtasking, mobilization readiness, and training requirements. Processed over 350 travel orders that provided 5,775 days of Fleet Support with cost exceeding $3.3M. Manages command security clearance program processing 276 re-investigations/visit requests. Managed triennial inspection of 72 command programs, receiving high marks and accolades from regional leadership with multiple programs identified as "best-practice".
-
-
Production Control Chief
-
Jan 2015 - Jul 2017
Responsible for production efforts of 363 USN, USMC, and 5 Civilians across 54 workcenters inscheduled and unscheduled maintenance of F/A 18, C-130 & P-3 aircraft components. Orchestrated the largest joint maintenance department across Command Naval Forces Reserves into one cohesive production team who spearheaded a 12% reduction in backlog, eight percent reduction in BCM's and $750,000 in savings while safely executing 13,336 mishap-free maintenance actions. Screened electronic Work Orders, maintenance reports, and aircraft log books for accuracy of data. Responsible for administration of safety management system (SMS), including: safety cultures, safety risk management, human and organizational factors, methods of facilitation, documentation, risk management strategies, hazard identification, and risk analysis. Plans and implements safety instruction and inspection programs; prepares periodic or recurring reports; supervises; plans, directs, organizes, schedules, and evaluates training programs for personnel. Reviews and coordinates work schedules; evaluates status and impact of department work.
-
-
Aviation Life Support Systems Division Chief
-
Dec 2013 - Jan 2015
Hand selected by senior management to lead and redirect a division of 35 personnel to meet production goals, decrease maintenance mishaps, address quality issues and improve moral. Received a grade of “On-Track” for all division managed maintenance quality programs during an external audit performed by Commander Naval Air Forces Aviation Maintenance Management Team inspectors. Verified Technical Directive incorporation and aircraft configuration were properly documented in aircraft log books utilizing Naval Air Technical and Engineering Service Command (NATEC) websites. Collaborated with the Navy Advancement Center’s “Aircrew Survival Equipmentman” Advancement Exam Readiness Review, validating 2,952 E4-E7 examination questions, verified 41 publications/references and authored 253questions impacting 1,522 Fleet Sailors.
-
-
Aviation Life Support Systems Intermediate Maintenance Technician / Quality Assurance
-
Sep 2012 - Dec 2013
Managed six aircraft quality assurance programs, 45 monitored programs, four quality assurance specialists, and 50 quality assurance inspectors in the completion of aircraft component inspections, maintenance monitoring and program support for six Divisions supporting multiple squadrons executing world-wide operations. Performed engineering/mishap investigations utilizing trend analysis methods to determine deficiencies and corrective actions for failures in equipment, systems, processes, inspection procedures and workmanship. Promoted sound preventative maintenance practices, teamwork, and fostered a safe working environment in accordance with the Maintenance Safety Program.
-
-
Maintenance Monitoring Team Lead
-
May 2007 - Sep 2012
Directly responsible for the training and supervision of eight Sailors and 18 civilian contractors in support of the Navy’s $15M C-20G CLS contract for three aircraft. Hand selected to manage multiple CENTCOM detachments resulting in a 98% mission readiness rate, encompassing 150 sorties, 800 mishap free flight hours, transportation of 2K passengers and 27K pounds of cargo. Maintenance Monitoring Team Quality Assurance Lead responsible for CMP.net monitors, Performance Assessment Reports and Maintenance Performance Audits. Collateral Duty Inspector responsible for ordering, inventory and inspection of 1,500 pieces of Chemical, Biological and Radiological items supporting 100 command personnel.
-
-
Aircrew Survival Equipmentman Technician Organizational Level
-
Aug 2003 - May 2007
Performed scheduled and unscheduled Aviation Life Support Systems maintenance on four C-130 aircraft.
-
-
Aircrew Survival Equipmentman Technician Organizational Level
-
Jul 1999 - Aug 2003
Performed scheduled and unscheduled Aviation Life Support Systems maintenance on five P-3 aircraft.
-
-
Community
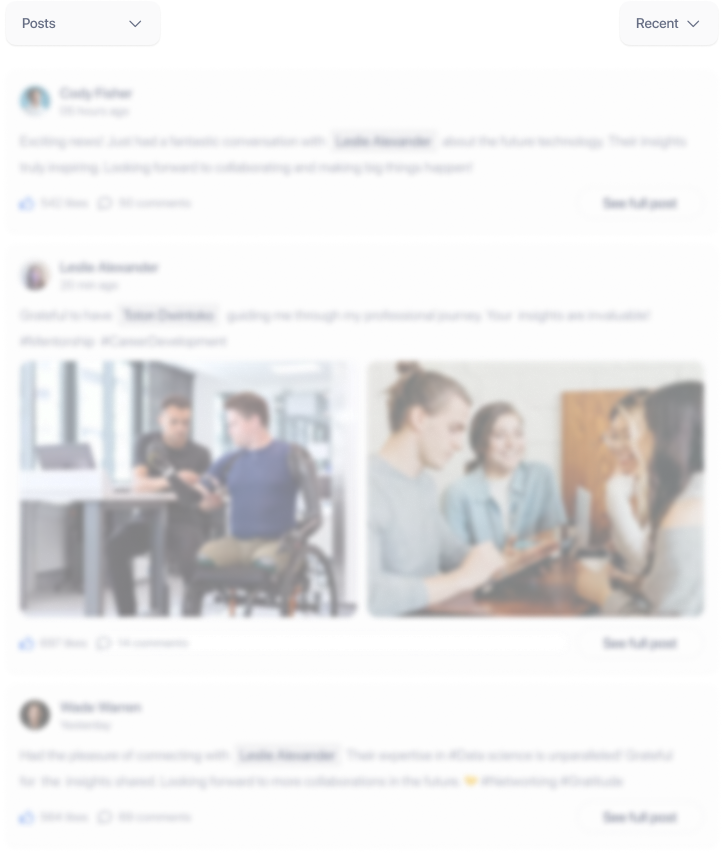