Tracy Canipe
Chief of Engineering & Design at 80 Acres Farms- Claim this Profile
Click to upgrade to our gold package
for the full feature experience.
-
English -
Topline Score
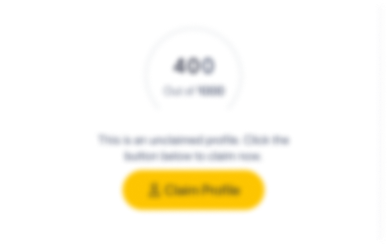
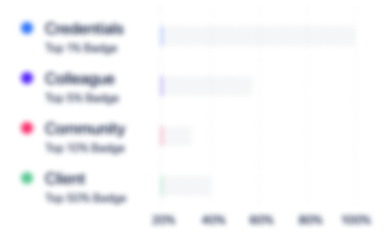
Bio

Terry Walker, MSHR, SPHR, SHRM-SCP
I had the opportunity to work with Tracy for three years. During that time, I saw many instances of Tracy's dedication. He is the type of person who always goes above and beyond for his employer. Tracy was responsible for every facet of the Maintenance department at our facility and frequently assisted other facilities in our company with projects and strategic planning. He is very passionate about doing things the right way, the smart way. Anyone who has Tracy on their team is assured of an exemplary professional.

Terry Walker, MSHR, SPHR, SHRM-SCP
I had the opportunity to work with Tracy for three years. During that time, I saw many instances of Tracy's dedication. He is the type of person who always goes above and beyond for his employer. Tracy was responsible for every facet of the Maintenance department at our facility and frequently assisted other facilities in our company with projects and strategic planning. He is very passionate about doing things the right way, the smart way. Anyone who has Tracy on their team is assured of an exemplary professional.

Terry Walker, MSHR, SPHR, SHRM-SCP
I had the opportunity to work with Tracy for three years. During that time, I saw many instances of Tracy's dedication. He is the type of person who always goes above and beyond for his employer. Tracy was responsible for every facet of the Maintenance department at our facility and frequently assisted other facilities in our company with projects and strategic planning. He is very passionate about doing things the right way, the smart way. Anyone who has Tracy on their team is assured of an exemplary professional.

Terry Walker, MSHR, SPHR, SHRM-SCP
I had the opportunity to work with Tracy for three years. During that time, I saw many instances of Tracy's dedication. He is the type of person who always goes above and beyond for his employer. Tracy was responsible for every facet of the Maintenance department at our facility and frequently assisted other facilities in our company with projects and strategic planning. He is very passionate about doing things the right way, the smart way. Anyone who has Tracy on their team is assured of an exemplary professional.

Credentials
-
Lean Six Sigma Green Belt (ICGB)
ExpertRating Inc.Aug, 2019- Nov, 2024 -
SQF "Implementing SQF Systems" (Post-Farm Gate)
SQF InstituteMar, 2014- Nov, 2024 -
Lean Six Sigma Yellow Belt
AdvancePierre FoodsMay, 2013- Nov, 2024
Experience
-
80 Acres Farms
-
United States
-
Farming
-
100 - 200 Employee
-
Chief of Engineering & Design
-
Jan 2016 - Present
•Designed, built and deployed proprietary grow systems, driving over 4 million dollars in confirmed savings versus outsourced installations in 2016-2018 •Patent Holder for method for high-density indoor farming apparatus •Reported directly to President and CEO, responsible for ensuring all strategic and financial goals were met for the manufacturing design/build/deployment/installation/commissioning process •Provided metric driven reports and ensured Six Sigma Lean principles were applied throughout the manufacturing process •Led the value engineering process to evaluate ways to drive down cost, eliminate waste and increase effectiveness •Negotiated with vendors to achieve the best price; reduced cost of next generation builds by 15-40% •Accelerated new product development to exceed domestic and international growth targets by providing "first to market" vertical farming equipment solutions and components •Condensed next generation build time by 20% •Increased automation features to eliminate user errors •Implemented work order system to track repairs and identify trends; utilized exceptional communication skills and persuasion to convey its benefits to team members and overcome resistance •Managed the installation of the equipment and the manufacturing process of a proprietary grow zone product •Directed quality control checks, ensuring the safety and effectiveness or reliability of the system •Partnered with Organizational Development to deploy TPM to reduce production downtime by over 40% •Established the short and long-term engineering goals of a multi-location enterprise •Devised plans for each phase of engineering projects; identifying and procuring the resources needed •Recruited engineering team of HVAC, Electrical, Plumbing, Fabrication and Construction professionals to build, deploy and maintain proprietary grow systems •Implemented morning production meetings and maintenance log, resulted in increased productivity and team cohesion Show less
-
-
-
Del Monte Foods, Inc.
-
United States
-
Food and Beverage Services
-
700 & Above Employee
-
Plant Engineer
-
2015 - 2016
• Managed capital and repair projects totaling over $6.5M- employing sound financial analysis to ensure all capital projects were approved with an ROI of 18 months or less • Analyzed process and personnel capabilities and directed and advised the team in designing and implementing new concepts, strategies, and personal behaviors to improve performance • Utilized Lean concepts and critical reasoning to reduce a $2.2 M repair parts inventory by $439,000; a 21% reduction; exceeded annual cost reduction goals by $39K • Directed overall day to day management and coordination of major plant and facilities construction, installation, upgrades and expansion in various manufacturing and production areas with a focus on safety, quality, maintenance, production and security, captured documented savings of over 2 million dollars by reducing downtime by over 50% • Established asset based Preventative Maintenance program • Developed and managed a maintenance action plan to prioritize complex operations which allowed projects to complete on schedule and under budget • Managed each phase of the engineering/facilities/maintenance projects process—from engineering analysis during the conception phase, to Capital Appropriation Request, to Vendor solicitation and selection, to implementation to project completion • Directed the reactive, routine and cyclical maintenance work activities for a team of 41 manufacturing maintenance, engineering and facilities associates (3 direct and 38 indirect reports) Show less
-
-
-
Tyson Foods
-
United States
-
Food and Beverage Manufacturing
-
700 & Above Employee
-
Facilities/Engineering/Maintenance Manager
-
Aug 2002 - Jun 2015
(Formerly AdvancePierre Foods) • Managed each phase of the engineering/facilities/maintenance projects process—from engineering analysis during the conception phase, to Capital Appropriation Request, to vendor solicitation and selection, to implementation to project completion • Re-designed the production floor process flow which increased daily output from 600 K to 1.4 M units a day • Launched “Pay for Skill” initiative; partnered with training to lay out a road map of the performance measures/training support required, resulting in a 50% increase in the work performed, while generating an in-house saving in excess of $125K • Orchestrated the implementation of TPM, 5S and a plant-wide computerized maintenance management system (MP2), as well as an inventory control program o These efforts led to personnel savings of over $500,000 annually, improved plant output by over 15%, improved equipment up-time by 30%, and reduced over production (give away) by 83% • Designed and built 18 MFW flow wrappers which provided a customized packaging solution for APF o These wrappers produce over 300 million sandwiches annually while maintaining an uptime rate in excess of 98% o Cutting edge design resulted in MUV savings of over $990,000 annually • Executed the total roof replacement of the Claremont manufacturing facility while continuing production at normal output and as a result productivity, employee safety, inventory levels, and market share was maintained as well as customer satisfaction and profitability o Increased efficiency by streamlining the troubleshooting process • Directed the reactive, routine and cyclical maintenance work activities for a team of 40 manufacturing maintenance, engineering and facilities associates in the Claremont facilities (5 direct and 35 indirect reports) • Provided leadership guidance to the engineering teams in the Easley and Amherst plants Show less
-
-
-
Dean Foods
-
United States
-
Dairy Product Manufacturing
-
700 & Above Employee
-
Plant Superintendent
-
1987 - 2001
•Managed a team of 10 direct reports and 637 indirect reports in an ice cream plant that generated over $140 M in revenues annually, responsible for full P&L, increasing sales and profitability, implementing cost management principles and best practice manufacturing across all facilities, ensuring innovation and accelerating new product development to achieve expanded market growth •Tapped for Management Development Program; rotated through Quality, Production Planning, Sanitation, Materials Management, Maintenance and Engineering •Selected for Plant Turn-Around Team, traveled throughout the system to provide assessment regarding long-term viability of the facility •Re-engineered the plant process controls and process flow to improve overall facility performance •Reduced labor costs by $2 M, decreased change-over time by 15% and increased MUV savings by $6 M •Acted as the procurement agent; successfully negotiated advantageous pricing contracts for uniforms, chemicals, commodities and facility lease-Negotiations resulted in annual company savings of over $5.4 M •Maintained EMS system for Ammonia; ensured proper documentation/inspections to remain in compliance •Implemented facility-wide maintenance programs (predictive maintenance for oil, infrared, and vibration analysis as well as preventative maintenance on boilers, chillers, cooling towers, water treatment, HVAC, and backflow preventer testing) to increase uptime and reduce downtime •Actively drove success on the following committees: o Safety Committee-increased use of PPE from 63% to 99%, which in turn reduced injury rates by 22% o EMS Committee-increased process/practice compliance from 88% to 98% o Employee Steering Committee-reduced employee turnover by 32% Show less
-
-
Education
-
University of the People
Bachelors of Science, Business Administration and Management, General -
University of Alabama at Birmingham
Certificate, Electrical and Mechanical Engineering
Community
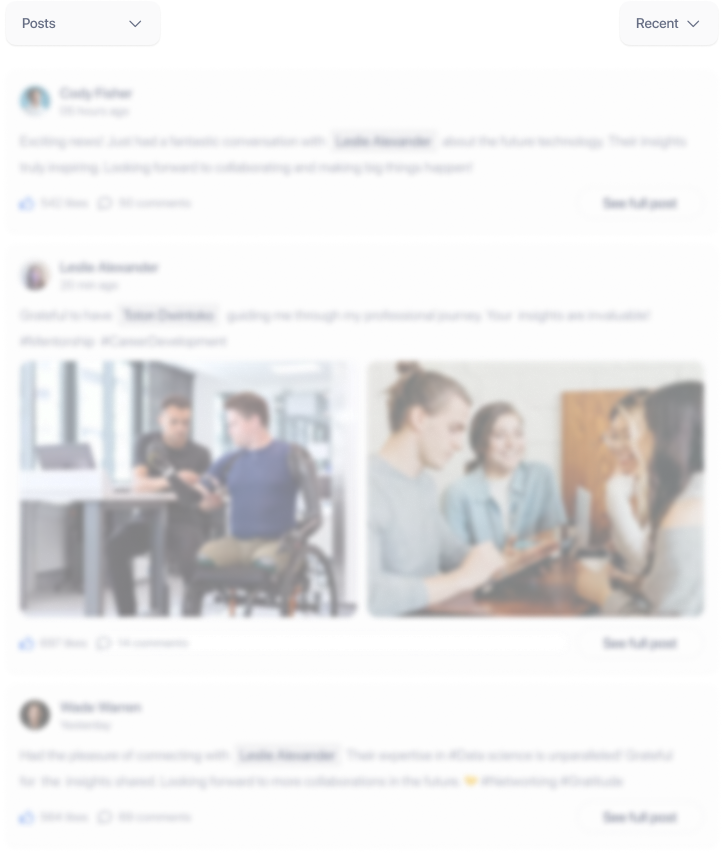