Tony Anderson
General Manager at FloTex- Claim this Profile
Click to upgrade to our gold package
for the full feature experience.
-
English Native or bilingual proficiency
-
Spanish Professional working proficiency
Topline Score
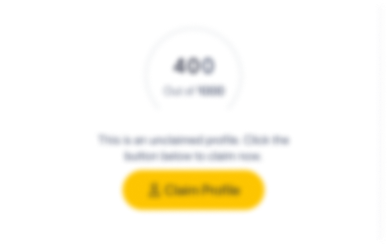
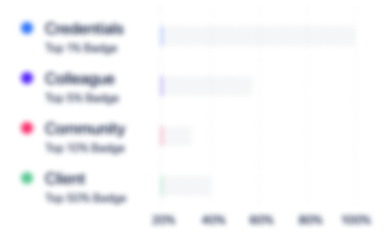
Bio


Experience
-
FloTex
-
United States
-
Textile Manufacturing
-
1 - 100 Employee
-
General Manager
-
Nov 2014 - Present
-
-
-
Carolina Narrow Fabric
-
United States
-
Textile Manufacturing
-
1 - 100 Employee
-
Operations Manager
-
Mar 2011 - Nov 2014
Plan, organize and direct the manufacturing and maintenance operations which ensure the most effective return on assets. Initiate plans and processes which minimize manufacturing costs through effective utilization of manpower, equipment, facilities, materials, and capital. Assure attainment of business objectives and productions schedules while insuring product standards that will exceed our customers’ expectations. Implement manufacturing strategies and action plans to… Show more Plan, organize and direct the manufacturing and maintenance operations which ensure the most effective return on assets. Initiate plans and processes which minimize manufacturing costs through effective utilization of manpower, equipment, facilities, materials, and capital. Assure attainment of business objectives and productions schedules while insuring product standards that will exceed our customers’ expectations. Implement manufacturing strategies and action plans to ensure that the facility supports strategic initiatives. Establish group and individual accountabilities throughout assigned departments for problem solving and cost reduction. Encourage use of new techniques and focus on fact based problem solving. Improve manpower utilization within existing departments and processes. Schedule stability that allows for maximum return on efficiencies. Work to establish management practices throughout assigned areas which include all employees’ positive involvement with opportunity for construction input and action. Continually improve safety record by addressing both physical safety issues and employee safety attitudes. Maintain and improve housekeeping in all areas. Maintain individual skills keeping up to date with latest production and production management concepts. Product development and pricing strategies. Reform current ISO 9001:2008 system and implement I3485:2003 standards. Show less Plan, organize and direct the manufacturing and maintenance operations which ensure the most effective return on assets. Initiate plans and processes which minimize manufacturing costs through effective utilization of manpower, equipment, facilities, materials, and capital. Assure attainment of business objectives and productions schedules while insuring product standards that will exceed our customers’ expectations. Implement manufacturing strategies and action plans to… Show more Plan, organize and direct the manufacturing and maintenance operations which ensure the most effective return on assets. Initiate plans and processes which minimize manufacturing costs through effective utilization of manpower, equipment, facilities, materials, and capital. Assure attainment of business objectives and productions schedules while insuring product standards that will exceed our customers’ expectations. Implement manufacturing strategies and action plans to ensure that the facility supports strategic initiatives. Establish group and individual accountabilities throughout assigned departments for problem solving and cost reduction. Encourage use of new techniques and focus on fact based problem solving. Improve manpower utilization within existing departments and processes. Schedule stability that allows for maximum return on efficiencies. Work to establish management practices throughout assigned areas which include all employees’ positive involvement with opportunity for construction input and action. Continually improve safety record by addressing both physical safety issues and employee safety attitudes. Maintain and improve housekeeping in all areas. Maintain individual skills keeping up to date with latest production and production management concepts. Product development and pricing strategies. Reform current ISO 9001:2008 system and implement I3485:2003 standards. Show less
-
-
-
Textum OPCO, LLC
-
United States
-
Textile Manufacturing
-
1 - 100 Employee
-
Process Engineer / Quality Manager
-
Sep 2005 - Dec 2010
Designated Management Representative for the company’s ISO 9001:2008 UL-DQS registration. This included representing the company during both internal and external audits with the ISO registrar. Management responsibility for the Quality Management System included maintaining documentation for all Quality Procedures (QP’s), Work Instructions (WI’s) and Quality Forms (QF’s) both physically and electronically on company server. Facilitate quality meetings to determine quality… Show more Designated Management Representative for the company’s ISO 9001:2008 UL-DQS registration. This included representing the company during both internal and external audits with the ISO registrar. Management responsibility for the Quality Management System included maintaining documentation for all Quality Procedures (QP’s), Work Instructions (WI’s) and Quality Forms (QF’s) both physically and electronically on company server. Facilitate quality meetings to determine quality objectives, progress, and effectiveness; playing a key role in keeping the organization focused on quality objectives. Meeting with department heads to perform root cause analysis on quality problems or customer returns by using Ishikawa, FMEA, DMAIC, and other forms of defect identification. Develop relationships with both customers and vendors to effectively handle customer complaints and non-conformance material issues. Create and refine internal manufacturing processes by process/ value stream mapping. Properly adjust and confirm procurement specifications provided by customers in developing new products. Manage multiple capital projects and cope with scope change. Evaluate, purchase, and oversee installation of new and used equipment used in the manufacturing process. Determine ROI and coordinate efforts with department heads. Product Development leader. Assisted V.P. of Sales and Marketing in determining product application. Show less Designated Management Representative for the company’s ISO 9001:2008 UL-DQS registration. This included representing the company during both internal and external audits with the ISO registrar. Management responsibility for the Quality Management System included maintaining documentation for all Quality Procedures (QP’s), Work Instructions (WI’s) and Quality Forms (QF’s) both physically and electronically on company server. Facilitate quality meetings to determine quality… Show more Designated Management Representative for the company’s ISO 9001:2008 UL-DQS registration. This included representing the company during both internal and external audits with the ISO registrar. Management responsibility for the Quality Management System included maintaining documentation for all Quality Procedures (QP’s), Work Instructions (WI’s) and Quality Forms (QF’s) both physically and electronically on company server. Facilitate quality meetings to determine quality objectives, progress, and effectiveness; playing a key role in keeping the organization focused on quality objectives. Meeting with department heads to perform root cause analysis on quality problems or customer returns by using Ishikawa, FMEA, DMAIC, and other forms of defect identification. Develop relationships with both customers and vendors to effectively handle customer complaints and non-conformance material issues. Create and refine internal manufacturing processes by process/ value stream mapping. Properly adjust and confirm procurement specifications provided by customers in developing new products. Manage multiple capital projects and cope with scope change. Evaluate, purchase, and oversee installation of new and used equipment used in the manufacturing process. Determine ROI and coordinate efforts with department heads. Product Development leader. Assisted V.P. of Sales and Marketing in determining product application. Show less
-
-
-
Accesorios Textiles S.A.
-
1 - 100 Employee
-
Contract Consultant / Technical Manager
-
Nov 2003 - Aug 2008
Knowledge of weaving and machinery effectively stream-lined the manufacturing process which resulted in a 35% increase in output. Addressed quality issues in manufacturing processes and raw materials that had an annual woven tape company with a capacity >1,000,000 yards per month. Project led the purchase and sale of used equipment with a total value of $900K. savings of $10,000. Created data collection system for machine efficiency and defined down time… Show more Knowledge of weaving and machinery effectively stream-lined the manufacturing process which resulted in a 35% increase in output. Addressed quality issues in manufacturing processes and raw materials that had an annual woven tape company with a capacity >1,000,000 yards per month. Project led the purchase and sale of used equipment with a total value of $900K. savings of $10,000. Created data collection system for machine efficiency and defined down time. Created and maintained an effective preventive maintenance program for all equipment involved in the manufacturing process. Developed a new technical maintenance team of 14 people. Achieved a spare parts inventory/ ordering system. Project managed various building and layout projects along with new electrical installation projects. Show less Knowledge of weaving and machinery effectively stream-lined the manufacturing process which resulted in a 35% increase in output. Addressed quality issues in manufacturing processes and raw materials that had an annual woven tape company with a capacity >1,000,000 yards per month. Project led the purchase and sale of used equipment with a total value of $900K. savings of $10,000. Created data collection system for machine efficiency and defined down time… Show more Knowledge of weaving and machinery effectively stream-lined the manufacturing process which resulted in a 35% increase in output. Addressed quality issues in manufacturing processes and raw materials that had an annual woven tape company with a capacity >1,000,000 yards per month. Project led the purchase and sale of used equipment with a total value of $900K. savings of $10,000. Created data collection system for machine efficiency and defined down time. Created and maintained an effective preventive maintenance program for all equipment involved in the manufacturing process. Developed a new technical maintenance team of 14 people. Achieved a spare parts inventory/ ordering system. Project managed various building and layout projects along with new electrical installation projects. Show less
-
-
-
Jakob Muller of America, Inc.
-
Charlotte, North Carolina Area
-
Technical Engineer / Customer Technical Support
-
Nov 1998 - Oct 2003
Factory technician based out of Charlotte that supported global effort by Jakob Muller Frick A.G., in Frick, Switzerland. Traveled the world extensively in the installation of new equipment. Trouble shot problems for customers on site and over the phone. Customer application assistance which provided adequate information and sound advice for customer making decisions. Trained customer technicians. Installation and testing of product upgrades. Factory technician based out of Charlotte that supported global effort by Jakob Muller Frick A.G., in Frick, Switzerland. Traveled the world extensively in the installation of new equipment. Trouble shot problems for customers on site and over the phone. Customer application assistance which provided adequate information and sound advice for customer making decisions. Trained customer technicians. Installation and testing of product upgrades.
-
-
-
Culp, Inc.
-
United States
-
Textile Manufacturing
-
100 - 200 Employee
-
Head Technician
-
Mar 1993 - Oct 1998
Daily duties included trouble shooting machinery problems that shift technicians could not repair. Specialized in solving electrical problems. Performed overhauling of weaving equipment. Daily duties included trouble shooting machinery problems that shift technicians could not repair. Specialized in solving electrical problems. Performed overhauling of weaving equipment.
-
-
Education
-
South Piedmont
A.A., Business -
CPCC
Six Sigma Certified Green Belt -
East Carolina University
Community
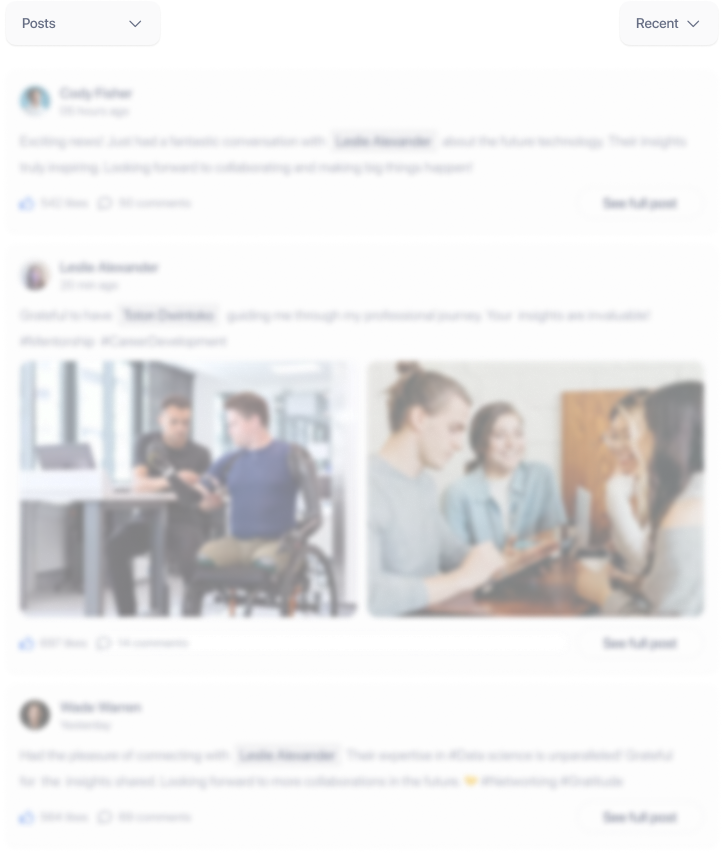