Thomas Briggs
Operations Manager at Michigan Language Assessment- Claim this Profile
Click to upgrade to our gold package
for the full feature experience.
Topline Score
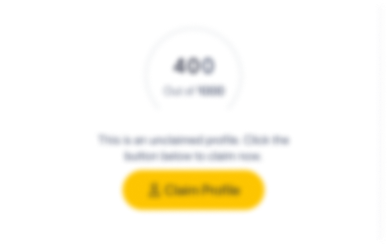
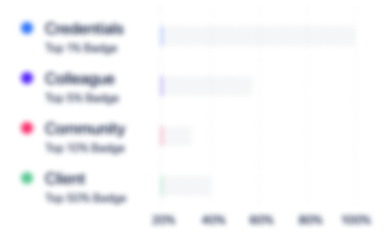
Bio

Preston Steele
Thomas is an authentic leader with a focus on process improvement. During his time at Ohio University he was selflessly devoted to teaching and mentoring those around him while promoting efficency as a key component to effective leadership . From our days as Cadets to his time as a Army Infantry Officer and now as a business professional Thomas has, without exception, demonstrated his abilities to successfully and efficiently, lead teams and organizations.

Preston Steele
Thomas is an authentic leader with a focus on process improvement. During his time at Ohio University he was selflessly devoted to teaching and mentoring those around him while promoting efficency as a key component to effective leadership . From our days as Cadets to his time as a Army Infantry Officer and now as a business professional Thomas has, without exception, demonstrated his abilities to successfully and efficiently, lead teams and organizations.

Preston Steele
Thomas is an authentic leader with a focus on process improvement. During his time at Ohio University he was selflessly devoted to teaching and mentoring those around him while promoting efficency as a key component to effective leadership . From our days as Cadets to his time as a Army Infantry Officer and now as a business professional Thomas has, without exception, demonstrated his abilities to successfully and efficiently, lead teams and organizations.

Preston Steele
Thomas is an authentic leader with a focus on process improvement. During his time at Ohio University he was selflessly devoted to teaching and mentoring those around him while promoting efficency as a key component to effective leadership . From our days as Cadets to his time as a Army Infantry Officer and now as a business professional Thomas has, without exception, demonstrated his abilities to successfully and efficiently, lead teams and organizations.

Experience
-
Michigan Language Assessment
-
United States
-
Book and Periodical Publishing
-
1 - 100 Employee
-
Operations Manager
-
Apr 2022 - Present
-
-
-
Domino's
-
Canada
-
Internet Publishing
-
1 - 100 Employee
-
Production Manager
-
Sep 2017 - Dec 2021
●Manage all aspects of production operations serving 454 franchise stores, including a direct staff of 26 employees ●Responsible for all aspects of Quality Management System; first dough producing facility to achieve FSSC 22000●Manage sanitation program for production areas, warehouse, and office area● Facility point-person for all internal, external, and third party auditing - achieved 4 years with zero critical findings●Responsible for Corrective Actions Preventative Actions as a part of QMS system●Respond to customer requests and works collaboratively to resolve customer complaints● Invest in consistent employee training, support and retention to improve productivity and drive down turnover, achieving 18 months with zero voluntary departures● Implement processes and practices to ensure exceptional safety controls; Achieved over 1,100 days without an OSHA incident in Production● Maximize yield and minimize waste through rigorous planning, controls, quality assurance and cost engineering● Led successful technology transformation and implementation of workforce management software● Achieve industry-leading food safety management certification● Co-Head of innovative pilot program to automate production with robotics; through creative financing with partner automation company, this effort required zero capital cost to Domino’s and drove process efficiencies
-
-
-
Oldcastle BuildingEnvelope
-
IT Services and IT Consulting
-
1 - 100 Employee
-
Production Manager
-
Apr 2014 - Aug 2017
Oldcastle BuildingEnvelope is a leading manufacturer of building materials, and is a U.S. subsidiary of CRH plc., one of the top five international building products companies. With operations in 35 countries and revenues of $31.8B (€27.1B), CRH employs approximately 75,000 people.• Promoted to Plant Manager for a large industrial facility that generated $60 million in revenue producing customized Architectural Glass and Aluminum extrusion fabrication.• Responsible for 100+ Employees over 2 shifts with 6 direct reports. The 100+ total reports represented well over half of the entire operation.• Oversaw and actively managed the logistics and the processing of 600-800 custom orders per week, as well as an In House fleet of drivers that service 22 states.• KEY ACCOMPLISHMENTS:o Made safety a key priority for all workers and delivered an entire year without a single OSHA incident. o Served as the Project Manager for the planning and installation of a $1M key infrastructure system, which automated certain processes, improved safety and decreased machine wait time by 80%.
-
-
Production Shift Manager
-
Oct 2011 - Apr 2014
Responsible for 55 employees over 4 departments in production of 1/3 of total product produced for $50 Million in Sales annually.-Reduced internal rejects from a heavy glass tempering furnace from 10% to 3%, resulting in an estimated savings of over $600,000 Annually-Received a Six Sigma Green Belt-Implemented cross training and metrics review to increase output from 2 tempering furnaces by 30%.-Reduced Optimization and Cutting Lead Time by 40 hours.-Graduated from Lean Managers Certification Program (LMAC) from The Ohio State University's Fisher School of Business.
-
-
-
Oldcastle Building Envelope
-
IT Services and IT Consulting
-
1 - 100 Employee
-
Production Supervisor
-
Oct 2011 - Jun 2012
Led a 13 man team to packageand ship 500,000lbs. of product a week valued at over $50 million annually. Managed maintenance andemployment of 5 crane systems and 4 forklifts. Determined day-to-day production schedule based on needs.· Identified lack of procedural guidelines and created Standard Operating Procedures for 3 main tasks.· Trained and mentored employees to increase the efficiency of their forklifts, thereby reducing overtime.· Continuously stressed process improvement and performance review, which resulted in a 50% decrease in the cost of replacements from boxing department.· Identified waste and established procedures that recycled wood for boxes, saving $25,000 annually.
-
-
-
US Army
-
United States
-
Law Enforcement
-
1 - 100 Employee
-
Captain, Infantry
-
Mar 2010 - Aug 2011
Second-in-command of 130-person heavy weapons company. Led 11-person headquarters platoon. Managed maintenance and employment of $64 million of equipment. Planned/forecasted/executed logistical, maintenance, and supply support for combat/training operations.· Deployed to Afghanistan in advance of unit to plan and lead inventory and accountability of over $52 million of property; executed in 8 days with zero defects and 100% accountability during change of command.· Planned/led logistical support and maintenance for remote outpost in Afghanistan; accurately forecasted resources for 300+ personnel/61 vehicles/72 buildings/complex communication networks/dining facility.· Analyzed/developed supply and equipment needs 3 months in advance of training; directed logistics to move $12 million of equipment from HI to CA with no losses; greatly increased team's combat readiness.· Identified lack of maintenance on 24 vehicles; implemented program that increased mission readiness 25%.· Planned and led deployment of company and all equipment from Island of Oahu to the Big Island of Hawaii, providing necessary support for over 20 days of field training that increased combat readiness.· Developed and implemented company-wide process improvement in accounting for over 800 sensitive equipment items; resulted in zero losses of equipment and 100% accountability for 13 months.· Successfully worked cross-functionally across company and sister companies to complete risk mitigation for all training events; resulted in zero incidents, no loss of equipment, and no disruptions in training.
-
-
Platoon Leader
-
Mar 2009 - Mar 2010
Led 18-person heavy weapons platoon in Iraq executing counter-insurgency operations. Maintained and accounted for over $5 million of equipment, 5 up-armored vehicles, and 8 crew- served weapons. Planned/executed unit training. Forecasted/directed logistics as unit movement officer.· Planned, resourced, and led 150+ combat patrols in northern Iraq with zero injuries or loss of equipment; increased security/stability for 50,000 citizens; built 5 water supply pumps, 2 schools, and 1 health clinic.· Developed 12 key relationships with Iraqi Security Force leaders, city officials, and village sheiks; improved attendance at meetings, enabling 8 infrastructure improvement projects and increasing joint patrols 30%.· Researched/initiated/developed 7 essential services projects; restored water supply system for 50,000+ Iraqis.· Worked cross-functionally with 4 agencies over 5 months to build new health clinic for over 6,000 Iraqis.· Assessed platoon maintenance program; revamped processes, developed training, and established in-depth daily and weekly maintenance cycle; led team to achieve operational readiness above 95% while deployed.· Planned/led training for 200+ Iraqi soldiers in live-fire exercises; set standard in company for joint training.· Earned Bronze Star Medal for meritorious service while deployed in support of Operation Iraqi Freedom.
-
-
Intelligence Supervisor and Assistant Operations Officer
-
Jun 2007 - Mar 2009
Led 3-person intelligence synchronization team in Iraq collecting, vetting, analyzing, and reporting battlefield intelligence to support 80-person company. Assisted in developing and tracking civil-military projects from inception to completion. Assisted company commander in planning, resourcing, and forecasting training.· Worked cross-functionally with 6 agencies to develop deep understanding of complex enemy networks in area of responsibility; improved cross-agency communication to quickly become top rated team out of 6.· Created debriefing/analyzing/reporting templates; quickly adopted as standard for ~4,000-person Brigade.· Attended 3-month Leaders Course and 4-month Infantry Basic Course; spent 3 months as ROTC Advisor.
-
-
Education
-
Ohio University
Bachelor of Science (B.S.), Communication, General -
The Ohio State University Fisher College of Business
Lean Managers Certification
Community
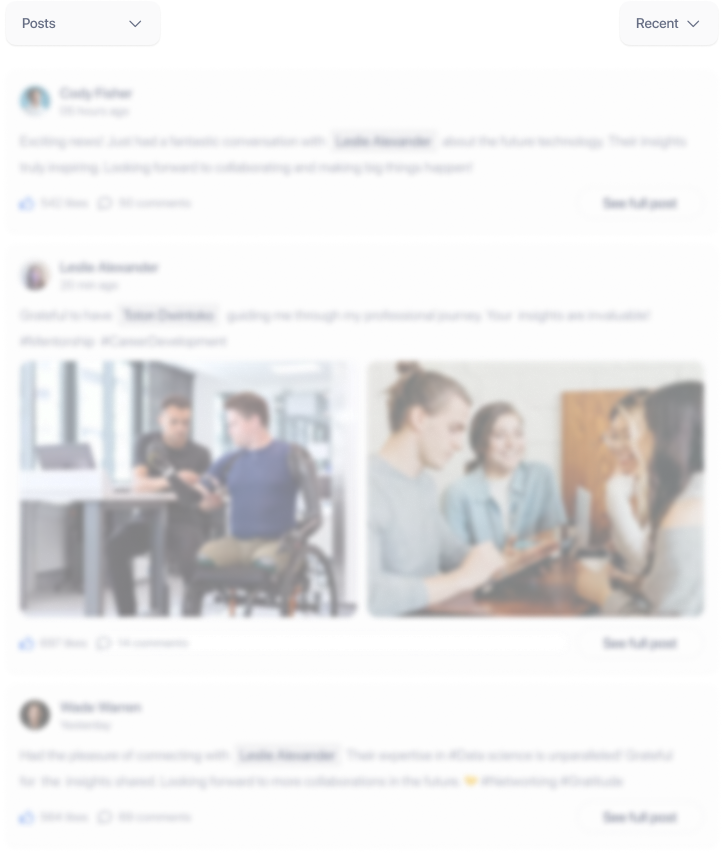