Tomas Meza
Manager of Operations at Sensient Natural Ingredients LLC- Claim this Profile
Click to upgrade to our gold package
for the full feature experience.
-
Español Native or bilingual proficiency
-
ingles Full professional proficiency
Topline Score
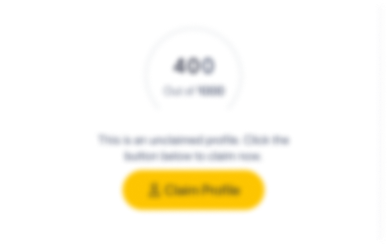
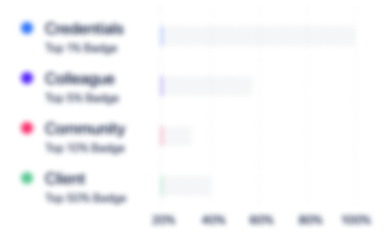
Bio


Credentials
-
PLC Allen Bradley Programming and Trouble shotting
Rockwell Automation MXJan, 2008- Nov, 2024
Experience
-
Sensient Natural Ingredients LLC
-
United States
-
Food and Beverage Manufacturing
-
1 - 100 Employee
-
Manager of Operations
-
Mar 2023 - Present
Deploy Management plans to accomplish with the quality assurance policies, BRC’s and others GMP’s that may apply to food safety and production. Deploy Management plans to accomplish with the quality assurance policies, BRC’s and others GMP’s that may apply to food safety and production.
-
-
-
ofi
-
Singapore
-
Food and Beverage Services
-
700 & Above Employee
-
Manufacturing Supervisor
-
Aug 2021 - Mar 2023
•Fast pace cannery and bottling of processed peppers (4 Oz, 7oz, 10,z etc) •Lead and promote solid actions to ensure the alignment of operations to Continuous Improvement, lean manufacturing and sustainability policies •Deploy Project Management plans to accomplish with the quality assurance policies, BRC’s GMP’s, GOP’s and others that apply to food safety and production •Coordinate Maintenance,QA, and stellital teamsto reach KPIs •Operations Budgetary control and Operations planning and deployment. Food defense applied to all processes and equipment, being accountable for all activities and improvements in Operations. •Develop solid actions to control, improve WIP materials and reduce the waste, loses over Raw materials management in Peppers processing. •Productivity increases 10% this past season
-
-
-
W. Silver, INC.
-
United States
-
Wholesale
-
1 - 100 Employee
-
Maintenance Supervisor
-
Feb 2020 - Jul 2021
Rolling Mill Maintenance coordinator, •Create and Develop a Maintenance Matrix and PM's routines to improve maintenance deployment. •Develop and Assign PM’s, Duties and task assignment, •SPC implemented in operations to create evidence for analytical studies for CI projects, •Metal stamping Operations projects developed to reduce downtimes, •Gages and measuring equipment designed and implemented to know process control and improve stability, •TPM launch and implementation as strategy to increase productivity and reduce downtimes, material waste and increase equipment availability. •Lean manufacturing implemented to reduce repetitive fails and to increase production output, (Production Registered when start in company 350 Steel tons/wk, after Maintenance Matrix and PM's were implemented 600 Stel Tons/wk, after TPM and Lean manufacturing implemented 900 ton/wk. When CI was developed 1200 tons/wk Supervisor), •SMED applied to Change overs and set up with great improvements, Painless start up as results. •Automation applied in too many areas that reduced material waste and improve operational deployment. •CAPEX used for new equipment and automation upgrades for existing processes. •Fabrication of equipment using in home technicians •Facilities maintenance developed for sustainability projects such as cost reduction over electricity (Illumination projects), Gas power usage reduction, water usage, including low maintenance flooring and walls to reduce A/C usage. •Coaching Fresh Engineers over parts and equipment design as well as engineering processes improvements. Coaching production personnel to know CI concepts and involve them on Lean Manufacturing philosophy. •
-
-
-
Mission Foods
-
United States
-
Food Production
-
700 & Above Employee
-
Maintenance Manager
-
Dec 2017 - Jul 2019
•CI applied in Tortilla factory Fast pace environment thru Maintenance and engineering solid actions implemented •Lead and promote solid actions to ensure the alignment of operations to Continuous Improvement, lean manufacturing and sustainability policies. •LSS projects implemented to ensure product quality and improve production outcome. •Several projects developed to improve processes and WIP reduce waste •Deploy Project Management plans to accomplish with the quality assurance policies, BRC’s GMP’s, GOP’s and others that apply to food safety per maintenance activities •Partner with all site leaders from executive, middle, and associate level teams. •Ensure a consistent site project pipeline at each site • Identify and work to remove barriers that slow or prevent the successful attainment to company policies and Good manufacturing practices across productive areas. processes •Develop Technical Information research & data to development work Instruction and procedures • Operations Budgetary control applied to New incoming projects and to improve existing processes (CAPEX) •Lean manufacturing applied in tortilla production processes to reduce Food quality and production increase. •Food defense SPC studies applied to all processes and equipment for tortilla production to implement new technology and sanitation techniques, •Deploy of technical research and investigate about new technology introduction to improve equipment and processes. •Storm-water and water inspection projects applied to improve waste management. Facility equipment projects to improve water usage and implement water softeners to reduce Minerals/solids in production lines. •Flour Silos and injection flour pipping projects to reduce cleaning and repairs over filtration/filler systems. •LSS training to employees to focus in waste reduction/ productivity increase/ cost reduction projects, Improvement teams created to focus in processes and quality improvement projects. •Sustainability projects
-
-
-
Mizkan America
-
United States
-
Food and Beverage Manufacturing
-
400 - 500 Employee
-
Manufacturing Supervisor
-
Jun 2016 - Dec 2017
•Peppers and Sauces fast cannery and bottling Manufacture •Lead and promote solid actions to ensure the alignment of operations to Continuous Improvement, lean manufacturing and sustainability policies •Deploy Project Management plans to accomplish with the quality assurance policies, BRC’s and others GMP’s that may apply to food safety and production •Partner with all site leaders from executive, middle, and associate level teams. •Ensure a consistent site project pipeline at each site • Identify and work to remove barriers that slow or prevent the successful attainment to company policies and Good manufacturing practices across productive areas. •Lean manufacturing applied over final drums packaging and Shipment deliveries to reduce late/short deliveries penalties, eliminate late fees and operations cost reduction ( Late fees were avoid and 500k yearly savings, Short/late deliveries were eliminated, Savings by avoid O/T savings 300k yearly, emergency material request eliminated 250k yearly savings). •Processes improvement due re-engineering applied to productive processes in drums packaging and warehouse shipment operations. Introduction to 7 waste elimination and kaizen events realized to improve in every step of packaging •Training and mentoring employees to implement TPM technique over packaging drums, prepping final labeling and planning. (Multiple cost reductions were developed, Process time change from push to pull system, Movement and transportation reduced to reduce times in process, VSM developed to get actual and future processes states, Labor and Over time reduced in more that 40%) •8 D's developed to investigate customer complains and get real cause on problems such as Jalapeño Pouches Leaks, 40# bags of green peppers leaks and 440# bags of red puree leakers and mold found. •Delivery processes changed and improve to reduce pallets damage while trucks transportation to customer.
-
-
-
Kelly services (@ Lear Corporation Electrical)
-
El Paso y alrededores, Texas, Estados Unidos
-
Regional CI Coordinator
-
Mar 2015 - Oct 2015
•Develop consistent Value Stream Maps (VSMs) at assigned site (LATAM plants were managed for LSS way). •Partner with all site leaders from executive, middle, and associate level teams. •Ensure a consistent site project pipeline at each site •Work closely with the CI global team to ensure Lean, Six Sigma and Best Practices (LSS & BP) compliance and implementation. •Identify and work to remove barriers that slow or prevent the successful attainment of LSS, BP & Sustainability across the site enterprise. •Deploy LSS, BP & Sustainability strategy across the site enterprise, ensuring common company training compliance and understanding at all levels of the organization •the Global Executive team for LSS, BP & Sustainability ensuring constant feedback and coaching to ensuring team objectives are met and exceeded. •Lead and Promote Sustainability projects and actions to ensure Lear Sustainability program and alignment with their social responsibility. Database and SPC developed to register all projects, results from 9 plants combined in saving projects were 1.5 USD millions registered by accounting department. +500 SS and lean manufacturing projects were lead and impulse thru all 9 LATAM plants. +200 new LSS Green belts and +50 LSS Black Belts plus 1000 Yellow belt certified. +100 sustainability projects implemented and paperless initiative produces the synergy to create a digital suggestion mailbox as equal as the use of technology such as tablets to reduce 50% of white paper used in offices to internal communication (1 USD Million). •Solar panels installed in two biggest plants reducing Electricity bills and A/C usage (results were over 30% in savings) •Residual treated water used for gardens and green areas such football fields. •Coaching and training multiple level workers to get Continuous improvement implemented
-
-
-
Federal-Mogul Powertrain
-
United States
-
Motor Vehicle Manufacturing
-
700 & Above Employee
-
Manufacturing Engineer
-
Apr 2012 - Jan 2015
•Establish and develop consistent VSM over fabrics manufacturing process and special products manufacturing • Design and improve floor use by modifying Lay out and start up for new productive areas (Improve floor usage by installing 22 looms machines in a 14000 Sq-Ft to increase from 350 K feet to 1.3 Million feet • Partner with all site leaders from executive, middle, and associate level teams. •Ensure a consistent site project pipeline at productive areas •Design and customize all fixtures, tools and equipment modification to ensure the proper • Identify and work to remove barriers that slow or prevent the successful attainment to company policies and lean manufacturing practices across productive processes •Develop Technical Information research & data to development work Instruction and procedures •Work closely with customer and product design team to design and develop new products • Establish and design all proper conditions to establish New product introduction •Deploy of technical research and investigate about new technology introduction. •Lead and promote solid actions to ensure the alignment of operations to Continuous Improvement, lean manufacturing and sustainability policies •Deploy Project Management plans to accomplish with the quality assurance policies such as ISO 9000, TS 16900 and other related to quality reinforce •750k savings during the LM projects developed in last year • +10 products designed and develop of High quality improvement in our active products •Review machinery and tools needs to design parts and fabricate fixtures, dies or equipment modifications to ensure all quality aspects on the products •Investigate and implement +20 projects focused to improve safety while handling, transporting and processes fibers and cores. •Create and design new aeronautical products to be use in military and commercial use •Implement TPM and training maintenance technician's for better practices and New PM's routines
-
-
-
Regal Beloit Corporation
-
United States
-
Appliances, Electrical, and Electronics Manufacturing
-
700 & Above Employee
-
Sr. Manufacturing Engineer
-
Dec 2009 - Oct 2011
•Process control and special products manufacturing such as aluminum rotor cast •Lay out design and start up for production areas •Manufacturing process transfer •Procedures creation and operational manuals elaboration •Equipment and accessories designer (End rings, Punches, Knives, cutters, other die parts for metal stamping) •Technical Information data development •Interdepartmental coordination to metal stamping process (High Energy Team Leader) •Goals reached Production increase and becomes regular •Down times reduction and control •Accessories and auxiliary machines buyer
-
-
-
Flex
-
United States
-
Appliances, Electrical, and Electronics Manufacturing
-
700 & Above Employee
-
Process Engineer
-
Aug 2007 - May 2009
•Process control and special products manufacturing •Lay out design and start up for production areas •Manufacturing process transfer •Procedures creation and operational manuals elaboration •Equipment and accessories designer (Punches, Knives, cutters, scrap shuts, other die parts for metal stamping) •Technical Information data development •Interdepartmental coordination to start up metal stamping process •ISO 9000 documentation control & preparation •Down times reduction and control •Accessories and auxiliary machines buyer
-
-
-
Jerzeez de Jimenez
-
Jimenez Mexico
-
Maintenance Manager & EHS Manager
-
Feb 2001 - Jan 2007
•Maintenance planning and execution •Down times reduction and control (lower than 60 %) •Maintenance expenses control & reduction (lower than 60%) •Tool crib materials management •Maintenance Technicians management •SPC to maintenance management •TPM Implementation and follow up •Facilities maintenance & supplier coordination •Water recycling systems Maintenance & operation •Air compressors maintenance •Electrical Distribution & control •Health & Sanity Control and Governmental registers as Environmental and labor regulations & others •Lay out drawer & modifier
-
-
-
BAPSA
-
Chihuahua Mexico
-
Maintenance Supervisor
-
Aug 1998 - Jan 2001
•NPS design and start up •Equipment and accessories design •Harness Matrix development •Continuity test programmer •Maintenance technician coordination •Assembly boards Fabrication & electrical test board elaboration •Conveyors maintenance •Wire cutting & crimper machines maintenance (automatics y manual operation) •Facilities maintenance •NPS design and start up •Equipment and accessories design •Harness Matrix development •Continuity test programmer •Maintenance technician coordination •Assembly boards Fabrication & electrical test board elaboration •Conveyors maintenance •Wire cutting & crimper machines maintenance (automatics y manual operation) •Facilities maintenance
-
-
-
La buena Meza
-
Chihuahua Mexico
-
Manager half time
-
Apr 1994 - Aug 1998
•Business chief •Sales chief •Sales trainer •Duties designation. •Business chief •Sales chief •Sales trainer •Duties designation.
-
-
Education
-
Instituto Tecnologico de Chihuahua
Bachelor of Engineering (B.Eng.), Electromechanical Engineering -
Instituto Tecnologico de Chihuahua
Grado en Ingeniería, Ingeniería electromecánica
Community
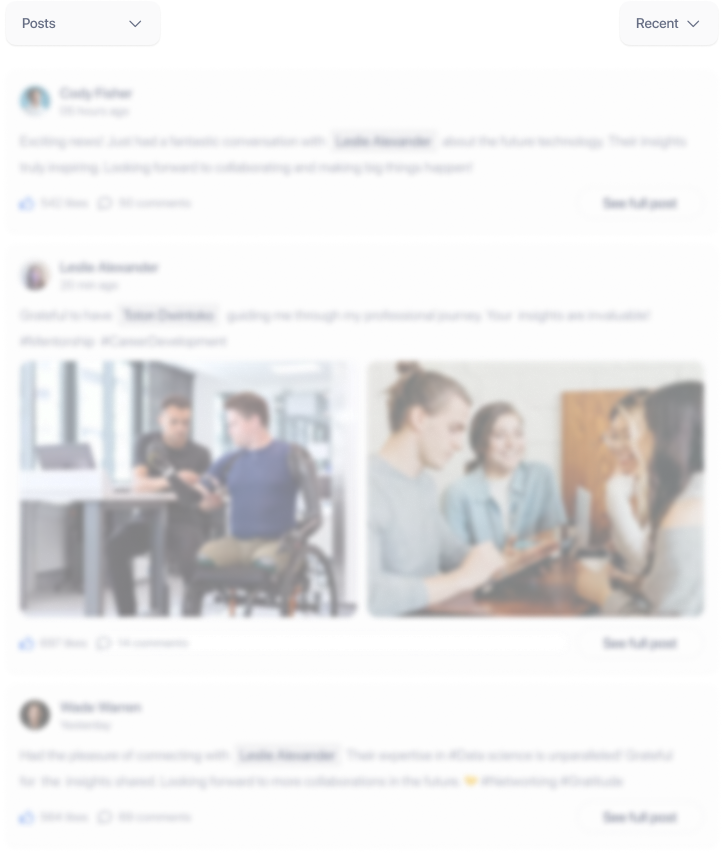