Tom Urban
Mechanical Engineer at XStream Trucking- Claim this Profile
Click to upgrade to our gold package
for the full feature experience.
Topline Score
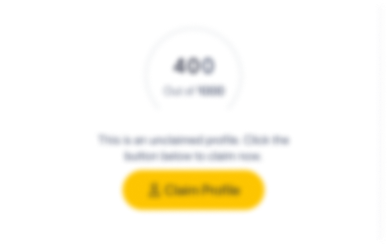
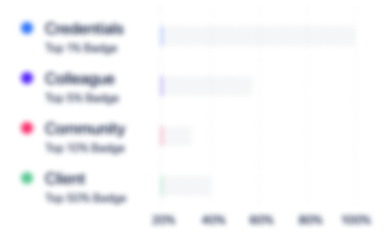
Bio


Credentials
-
Certified SolidWorks Professional (CSWP)
Dassault SystèmesJun, 2019- Nov, 2024
Experience
-
TruckLabs
-
United States
-
Truck Transportation
-
1 - 100 Employee
-
Mechanical Engineer
-
Jul 2019 - Present
I moved back to AZ, but this time to the Phoenix area to join a startup company in the transportation sector. XStream Trucking makes aerodynamic systems for 18-wheelers to help improve fuel efficiency. I'm focused on engineering systems & design documentation development, meaning I'm working on updating their existing engineering drawings and implementing systems to help standardize how they document their designs. In addition, when necessary, I participate in more traditional engineering & design tasks. Show less
-
-
-
Xtreme Manufacturing, LLC
-
United States
-
Construction
-
1 - 100 Employee
-
Engineering Contractor
-
Sep 2018 - Jul 2019
I relocated from Tucson to Henderson after learning about an opportunity from a long time acquaintance who is also in the engineering & design sector. • Assisted in the design and documentation of scissor lifts, boom lifts and telehandlers used in the construction and building maintenance industries. • Designed and documented components and sub-systems with hydraulics and electronic controls systems into top level equipment assemblies. • Designed and documented option packages for equipment such as generators. • Part of a design team working to generate concepts for a new style of chassis to improve the stability and performance of the next generation of extended reach equipment, including providing a platform for potentially adding either manual or automatic leveling of equipment by utilizing 4 independently controlled legs, allowing for platform leveling on uneven ground or grades. • CAD System used: SolidWorks, using PDM. Show less
-
-
-
Ventana Medical Systems
-
Tucson, Arizona Area
-
Engineering Contractor
-
Oct 2017 - Aug 2018
I finally found an opportunity that would allow me to relocate from New England to the SouthWest, and just in time to escape another New England winter! • Worked as an advisor/mentor to small engineering teams tasked with correcting errors found during testing and validation of a new cancer screening instrument. The role was to ensure that the team could effectively evaluate and communicate the problem(s) to other functional groups within the company and to advise the larger product launch team on technical aspects of the proposed solutions. • Member of an advisory team assembled to investigate the causes of poor engineering design output and assess its impact on product quality. Began compiling a list of recommendations to be presented to Engineering management to correct the causes of the poor engineering output. • Perform tolerance analysis to ensure fit and function of parts made from different manufacturing processes, such as molding and machining. • Revised models and drawings of machined parts, injection molded parts and thermoformed parts based on evaluation of errors found during testing and validation. Also designed new machined and thermoformed parts for new sub-systems added to improve performance and robustness. • Worked with tooling vendors to revise plastic part designs, balancing functional requirements of the part with tooling construction requirements. • CAD System used: SolidWorks, using PDM. Show less
-
-
-
Banski MotorSports LLC
-
Manchester NH
-
Self Employed
-
Sep 2014 - Jun 2017
I worked to try to expand an existing, part-time business into a full time effort. The company grew out of a hobby that I used to have which was competing in autocrosses and time trials with my 93 Corvette. The business centered around designed, made and sold suspension upgrades for sports cars & enthusiasts. After I had rebuilt (and upgraded) the rear suspension of my car I took a chance and began selling it online in 2008. Word of mouth grew as did the business. Slowly at first but as time progressed I was surprised at how much it grew considering I was just one guy working part-time out of my basement. Eventually I developed a full website and online store. I have sold products all over the US and abroad to Europe, Scandinavia & Australia. In 2016 I formed an expansion plan in which the first step was to purchase some IP from a company with complimentary products so I could greatly expand my product line and generate cash flow while working on the next generation of suspension upgrades. Ultimately the IP purchase did not happen and I decided to abandon the full time effort, return to my career as an engineer and relocate to the southwest. Show less
-
-
-
GT Advanced Technologies
-
United States
-
Semiconductor Manufacturing
-
200 - 300 Employee
-
Mechanical Engineering Contractor
-
Dec 2013 - Sep 2014
• Designed multiple material handling systems and retrofits for moving and handling sapphire boules during and after manufacturing. • Designed machine vision or laser based inspection systems for sapphire boules and the bricks made from those boules. • Duties included conceptual and detailed design work, including component and assembly drawings, design documentation and BOM generation. • CAD System used: SolidWorks, using PDM. • Designed multiple material handling systems and retrofits for moving and handling sapphire boules during and after manufacturing. • Designed machine vision or laser based inspection systems for sapphire boules and the bricks made from those boules. • Duties included conceptual and detailed design work, including component and assembly drawings, design documentation and BOM generation. • CAD System used: SolidWorks, using PDM.
-
-
-
L3 Technologies
-
United States
-
Defense and Space Manufacturing
-
700 & Above Employee
-
Senior Mechanical Engineer
-
Jul 2013 - Oct 2013
I was supposed to lead a design team working to miniaturize the next generation of weapons mounted aiming lasers for the military. Unfortunately the project was cancelled after they lost the contract bid. I was one of 64 people who were laid off that day. I was supposed to lead a design team working to miniaturize the next generation of weapons mounted aiming lasers for the military. Unfortunately the project was cancelled after they lost the contract bid. I was one of 64 people who were laid off that day.
-
-
-
BAE Systems
-
United Kingdom
-
Defense and Space Manufacturing
-
700 & Above Employee
-
Senior Mechanical Engineer
-
Oct 2010 - Jun 2013
• Managed project plans and budgets for new products, compiled costs, schedules and wrote proposals for new projects presented to customers.• Designed imaging system for internal customer’s airborne thermal imager. In addition to project management duties, developed initial conceptual design from an optical prescription, then completed the detailed design. Components were either custom machined or purchased parts.• Designed mechanical platform that two external partners could use to assemble demonstrator units displaying the capabilities of their product(s) and how they could be integrated into a “plug and play” thermal vision system. Components were either custom machined or purchased parts.• Continued working with other Sr. Mechanical Engineers to review and revise component and system designs based on their FEA.• CAD System used: SolidWorks, using PDM. Show less
-
-
Design Engineer
-
Feb 2008 - Jun 2013
• Designed new electro-mechanical optical systems for land and air based military platforms. Designs were continuous zoom or multiple fixed field of view, typically actuated by stepper motors and gear boxes paired with rotary cams or linear motion. Some had positional feedback and others did not.• Designed a static, a-thermalized vision system for vehicle mounted threat detection, using a 190º fisheye lens to detect small arms fire.• Designed an optical alignment tool for gimbal mounted vision systems. The tool was man portable and ruggedized for runway/hangar use “in theater”.• Designed an electro-mechanical, wireless, helmet mounted video simulation system for the USAF. Design utilized wireless data transmission technology and miniature hi-def video display to create a personal, clip on video simulation system for training pilots. Program sponsored by SBIR grant.• Worked with senior engineers to update designs based on their FEA analysis. Typically this was done to optimize strength and ensure systems could meet the necessary shock and vibration requirements while also being light enough to meet the required weight budget.• Duties included conceptual and detailed design work, including component and assembly drawings, design documentation and BOM generation.• In most instances built the first prototypes of above listed systems to evaluate fit, function and manufacturability. Worked with Manufacturing and Quality to determine the necessary performance and reliability testing. Continued to support products as they moved through testing and ultimately into production.• CAD System used: SolidWorks, using PDM. Show less
-
-
-
Thermo Fisher Scientific
-
United States
-
Biotechnology Research
-
700 & Above Employee
-
Product Development Engineer
-
Jan 2005 - Feb 2008
• Led cross-functional teams, including QC, Manufacturing, Marketing, and Procurement in product development projects and product introductions.• Composed capital requests, project plans and budgets for product development projects. Executed, managed and reported on progress of project plans to management.• Designed a variety of injection molded consumable products, such as large and small volume storage tubes with screw on caps.• Designed electromechanical accessories and sub-systems for various platforms of an automated pipetting product line. Designs included machined parts, sheet metal parts and off the shelf purchased components.• Designed electromechanical hand held instruments as accessories to both the consumable and automated pipetting product lines. Instruments consisted of cast urethane housings, injection molded parts, machined parts and off the shelf purchased components.• Worked with in-house tool room as well as external tooling and injection molding vendors to optimize part designs for both function and manufacturability.• Duties included conceptual and detailed design work, including component and assembly drawings, design documentation and BOM generation.• In many instances built the first prototypes to evaluate fit, function and manufacturability. Worked with Manufacturing and Quality to determine the necessary performance and reliability testing. Continued to support products as they moved through testing and ultimately into production.• CAD System used: SolidWorks. Show less
-
-
Manufacturing Engineer
-
May 2003 - Dec 2004
• Member of cross-functional team executing capital equipment and process development projects for a high production injection molding facility.• Designed components and sub-systems for a 3-axis, position driven robotic system that retrieved parts from high cavitation injection molds and assembled them directly into their final packaging.• Designed components and sub-systems for a multi-axis robot that used machine vision to identify and assemble parts into its final packaging while discarding the sprue and runner system of parts molded in an 8 cavity tool.• Designed a proof of concept system that used machine vision to inspect the quality of injection molded parts. Show less
-
-
-
Madison CMP
-
Salem, NH
-
Development Engineer
-
Jun 1998 - Dec 2002
• Lead designer on in-house design and build capital equipment projects. Developed concepts and drawings and supervised construction. • Designed a pneumatic-over-hydraulically actuated fixture that was a collapsible mandrel for machining the OD of large urethane belts on a 43” Vertical Turret Lathe. • Designed a pneumatically actuated press that disassembled (allowing for “demolding” of the part) then re-assembled large cast urethane molds. • Designed the machining process as well as the tooling for adding a grooved, tire tread like pattern, to the OD of large, thin wall urethane belts. Show less
-
-
-
Springfield Mold Works
-
Westfield, MA
-
Mold Designer
-
Dec 1991 - Sep 1995
• Responsible for the engineering, design layout and component specification of various injection, structural foam, blow, and thermoforming molds that utilized mechanically, hydraulically and pneumatically actuated sub-systems and components. • Generated machine code and documentation for programs for CNC machining centers. • Responsible for the engineering, design layout and component specification of various injection, structural foam, blow, and thermoforming molds that utilized mechanically, hydraulically and pneumatically actuated sub-systems and components. • Generated machine code and documentation for programs for CNC machining centers.
-
-
-
Tell Tool
-
Westfield MA
-
Engineering Aide
-
Dec 1990 - Nov 1991
• Made process sheets for CNC machining, manual machining, EDM and assembly processes. • Designed and detailed tooling and fixturing for both CNC and manual machining processes. • Made process sheets for CNC machining, manual machining, EDM and assembly processes. • Designed and detailed tooling and fixturing for both CNC and manual machining processes.
-
-
Education
-
University of Massachusetts, Amherst
Bachelor's degree, Mechanical Engineering -
Springfield Technical Community College
Associate's degree, Drafting & Design
Community
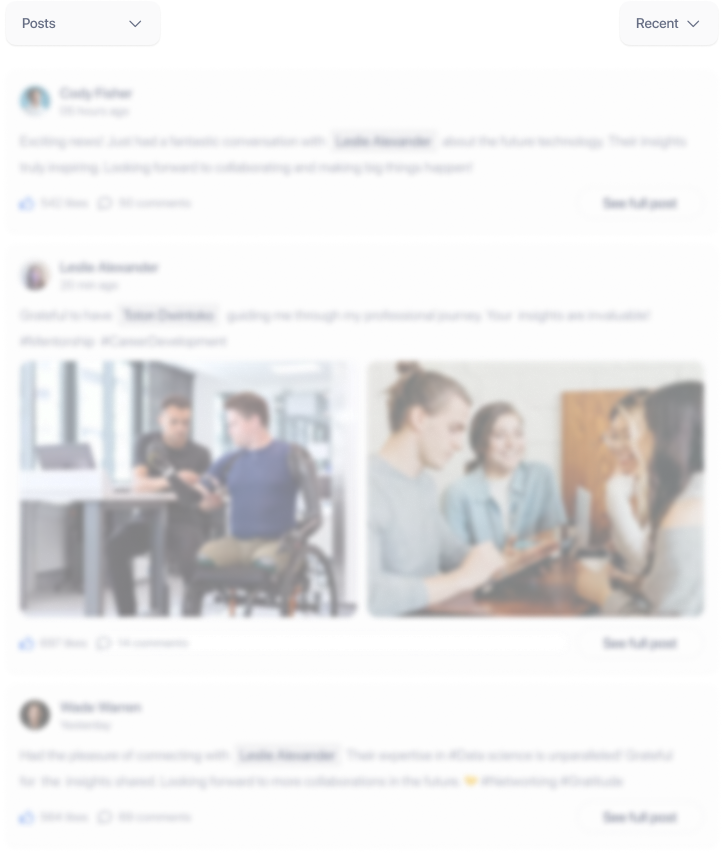