Tom Moritz
Global Leader - Purchasing, Supply Chain & Logistics at Perrone Performance Leathers & Textiles- Claim this Profile
Click to upgrade to our gold package
for the full feature experience.
Topline Score
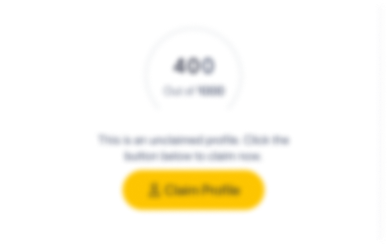
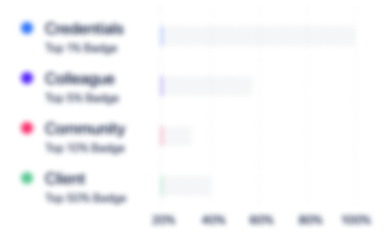
Bio


Experience
-
Perrone Performance Leathers & Textiles
-
United States
-
Textile Manufacturing
-
1 - 100 Employee
-
Global Leader - Purchasing, Supply Chain & Logistics
-
Sep 2021 - Present
Lead site Teams in Purchasing, Planning, and Transportation related functions, build supplier relationships, and support the introductions of new product lines. Lead site Teams in Purchasing, Planning, and Transportation related functions, build supplier relationships, and support the introductions of new product lines.
-
-
-
Greenfield Industries, Inc.
-
United States
-
Machinery Manufacturing
-
100 - 200 Employee
-
Planning and Forecasting Manager
-
Dec 2017 - Sep 2021
Lead the Planning and Forecasting Team to develop an effective production schedule that meets Customer needs and minimizes obsolete inventory. Lead the Planning and Forecasting Team to develop an effective production schedule that meets Customer needs and minimizes obsolete inventory.
-
-
-
Arconic
-
United States
-
Manufacturing
-
700 & Above Employee
-
Supply Chain Manager
-
Dec 2016 - Nov 2017
Manage the Planning, Material Flow, and Shipping functions for the Midway, GA site. Drive the S&OP process and improvements to Customer Service. Ensure the maximization of all resources, especially capacity bottlenecks. Manage the Planning, Material Flow, and Shipping functions for the Midway, GA site. Drive the S&OP process and improvements to Customer Service. Ensure the maximization of all resources, especially capacity bottlenecks.
-
-
-
-
Corporate Planning Manager
-
Mar 2010 - Dec 2016
Responsible for the Supply Chain, Planning, and Service levels for the Wellsboro, McElhattan, and Coudersport PA Manufacturing Facilities. Manage the Planning Teams at each site and be a liaison with other departments to coordinate improvement activities across the company.
-
-
Supply Chain Manager
-
Jan 2012 - Aug 2013
Temporary assignment supporting the deployment of new ERP software and Supply Chain improvement opportunities across the European facilities.
-
-
-
L'Oréal
-
France
-
Personal Care Product Manufacturing
-
700 & Above Employee
-
Cell Manager
-
Jan 2009 - Apr 2010
Managed a packaging cell of 9 lines operating on a 24/7 schedule. On site trainer for the Packaging Department for Go-Live of SAP/Flexnet production control ERP software. Implemented waste reduction and Total Productivity Maintenance programs. Managed a packaging cell of 9 lines operating on a 24/7 schedule. On site trainer for the Packaging Department for Go-Live of SAP/Flexnet production control ERP software. Implemented waste reduction and Total Productivity Maintenance programs.
-
-
-
Reckitt
-
United Kingdom
-
Manufacturing
-
700 & Above Employee
-
Operations Manager
-
2007 - Oct 2008
Manage 24/7 plant operations and personnel including 2 Processing Areas and 13 Packaging Lines in the production of Lysol Brand liquid and aerosol products.
-
-
Materials Manager
-
2005 - 2007
Managed the Shipping, Receiving, and Scheduling functions within the site. Forecasted and managed site financial accounts for labor, materials, indirect supplies, shipping, and other discretionary spending. Delivered high service levels to final customers through improved supply chain management.
-
-
-
Baldwin Richardson Foods
-
United States
-
Food and Beverage Manufacturing
-
100 - 200 Employee
-
Assistant Production Manager
-
2004 - 2005
Managed all manufacturing, including preparation, cooking, and packaging of syrups, dips, sauces, and fillings across 10 production lines and 3 shifts with a work force consisting of 3 Supervisors and 90 Technicians. Managed all manufacturing, including preparation, cooking, and packaging of syrups, dips, sauces, and fillings across 10 production lines and 3 shifts with a work force consisting of 3 Supervisors and 90 Technicians.
-
-
-
PepsiCo
-
United States
-
Food and Beverage Services
-
700 & Above Employee
-
Materials Manager
-
1994 - 2004
Over the 10+ years with Frito Lay, I worked my way up from a Front Line Resource covering weekend operations to being a Quality Resource, Packaging Resource, Processing Department Manager, Maintenance Senior Resource, and Plant Materials Manager. I worked at 3 different manufacturing sites, and became proficient in Team Development and instituting Continuous Improvement principles to drive results. I executed several large capital projects, including a $1.5 million PC Fryer/Line refurbishment. I also instituted systems in materials management that reduced on hand inventory by a monthly average of $800,000 while increasing plant productivity and customer service levels. Show less
-
-
-
-
Manufacturing Engineer Intern
-
1993 - 1994
-
-
Education
-
Virginia Tech
Bachelor of Science, Industrial Engineering
Community
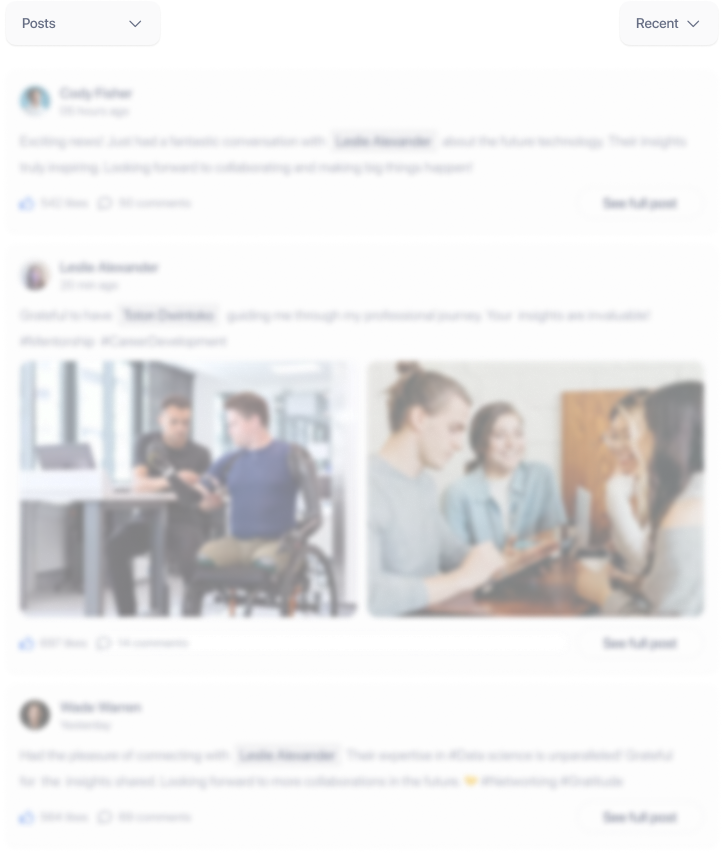