Tom McLaren
Head Of Operations at Crucial Drinks- Claim this Profile
Click to upgrade to our gold package
for the full feature experience.
Topline Score
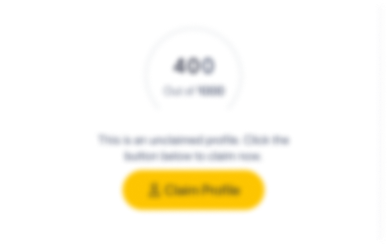
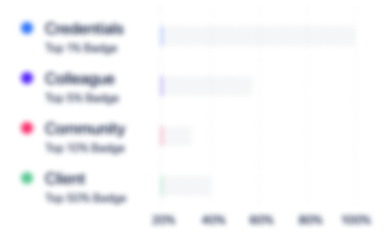
Bio


Experience
-
Crucial Drinks
-
United Kingdom
-
Wine & Spirits
-
1 - 100 Employee
-
Head Of Operations
-
Apr 2022 - Present
-
-
-
-
New Product Development Manager
-
Jan 2014 - Mar 2022
-
-
-
Bacardi
-
Glasgow, United Kingdom
-
Materials team leader
-
Dec 2008 - Dec 2013
• People management and development covering a team of up to 10 personnel covering, material planning & buying, line feed, material control, internal warehousing, external storage. Core responsibilities include monthly 1:1’s competency assessments, Performance Appraisals and all areas of Performance Management. Monitor and control expenditure against agreed budgets, LE’s and highlight in advance any anticipated risks including: overtime, temporary labour and external storage. • Recruitment and selection where applicable as required. • Compliance with ‘Sarbanes Oxley’ independent audit requirements • Implementation, and ongoing maintenance, of a training programme for all Operators within Supply Chain Process Group. • Ensure adherence to Bacardi Environmental Health & Safety continuous improvement programme. • Maintain a programme of dry goods audits at 3rd Party facilities. • Ensure that the working environment is maintained to a high standard of cleanliness, and housekeeping in accordance with Bacardi Operating System 5S principles. • Support Continuous Improvement activities, and project implementation as required. Plan the effective use of available personnel to ensure that all key operations are covered. Where necessary. • Responsibility for materials accuracy and twice yearly full physical stock reconciliation’s. • Support and drive continuous improvement initiatives to eliminate non value added activities and deliver tangible business improvement. • To Supply weekly material requirements to the supply base covering the period of next day to 18 months. • Drive supplier review meetings on a monthly and quarterly basis. • Work in parallel with the Supplier Development Officer to ensure sufficient pipeline materials to support future bottling plans. • Lead supplier performance management programs. • Preparation and distribution of critical component supply information for the monthly global plant S&OP process. Show less
-
-
-
Self employed
-
Scotland
-
director
-
Nov 2003 - Nov 2008
• Importing & exporting motor sport goods from USA, Asia & Europe that involved extensive travelling Throughout Europe, China, Taiwan & USA. • Distribute goods to both trade and retail sectors throughout the UK & Europe. • Marketing / advertising • Financial accounting • Purchasing • Manage own brand products. • Manage workshop, sales & warehouse staff • Importing & exporting motor sport goods from USA, Asia & Europe that involved extensive travelling Throughout Europe, China, Taiwan & USA. • Distribute goods to both trade and retail sectors throughout the UK & Europe. • Marketing / advertising • Financial accounting • Purchasing • Manage own brand products. • Manage workshop, sales & warehouse staff
-
-
-
Hewlett Packard Enterprise
-
United States
-
IT Services and IT Consulting
-
700 & Above Employee
-
Alliance programs manager
-
Nov 2001 - Nov 2003
In this role I managed a local alliance partner who manufactured high volume low-mid range servers on behalf of HP. The role covered a wide range of responsibilities including new product introductions to factory quality and performance. Coordinate & report new product introductions for both Server & options products. Manage new product introduction project plans & roadmap for EMEA geography.Publish project updates and liase with both internal & external clients as necessary.•Manage and report manufacturing, engineering, materials & quality process readiness. This covered all aspects of readiness including: software, component qualification. Responsible for the factory daily, weekly, monthly production, ship & quality performance. Verify and approve current quarter +1 demand signals to the alliance partner ensuring sufficient materials and capacity were in place whilst maintaining flexibility. •Report factory performance and present daily stats at both local & corporate level within HP.•Attend and represent site on WW supply chain allocation calls.•Work closely with product managers to identify opportunities within product lifecycle and end of life processes. •Coordinate and present factory quarterly quality performance & review at both local and corporate level. Maintain and publish factory scorecard and present at VP level within both organisations on a quarterly basis.•Support factory management by allocating labour, engineering & technical support as required.•Drive cost reductions whilst improving factory productivity and quality.•Manage and monitor component supplier performance (mainly Asian suppliers).•Attend and report performance metrics at WW product managers quarterly meetings.•Chair daily supply chain, logistics & quality calls with relevant functions in WW locations.•Ensure HP’s proprietary information was protected and liase with corporate security on audit procedures & results. Show less
-
-
ISSG options programs manager
-
Nov 2000 - Nov 2001
Coordinate and manage the introduction of EMEA server options & field replaceable units.• Liase with EMEA marketing & product managers to review and report product introduction progress in support of customer requirements.• Chair weekly progress meetings with procurement for OEM & alliance turnkey products. Report site readiness & progress to corporate new products engineering.• Liase with in-house manufacturing & engineering teams to ensure new product pilots & planned production ramps were achieved in support of customer requirements.• Chair bill of material reviews with procurement, product engineering & manufacturing engineering ensuring factory readiness for planned production ramp.• Support new product pilots & ramps.• Lead product life cycle management & obsolescence reviews. Show less
-
-
Weekend senior planner
-
Nov 1998 - Nov 2000
• Chair and present weekend production meetings for high volume in-house manufacturing, which included: Printed circuit boards, Laptops, desktop & servers.• Identify and report on any potential risks impacting factory weekend performance targets.• Ensure sufficient on call coverage is available for all functions and coordinate call-outs as required.• Liase with local suppliers and place purchase orders as required.• Maintain and change build schedules based on customer priorities and or constraints ensuring seamless production to protect productivity & factory capacity. • Publish and report factory weekend performance metrics ensuring a seamless transition and handover to the relevant functions. Show less
-
-
Senior planner
-
Oct 1995 - Nov 1998
• Coordinate options sub planning group of 3 planners & 1 placement student.• Report daily, weekly & monthly performance metrics• New product introduction• Analyse and confirm MRP / MPS output on a weekly basis.• Liase with procurement on potential issues and coordinate recovery.• Implementation of JIT• Turnkey forecast commit monitoring.• 8 step discipline process implementation.• Responsible for: two day look ahead plan & ship to first commit performance.• Fast implementation (new factory scheduling and performance program). • Lead SAP implementation for the options planning group.• Report & manage product life cycle management & obsolescence. • Engineering change management.• Ensure standard work operation procedures were up to date and amended as required.• Plan holiday cover ensuring sufficient resources were available at all times. Show less
-
-
-
Sun Microsystems
-
United States
-
IT Services and IT Consulting
-
700 & Above Employee
-
Senior planner - Master scheduler
-
Jan 1992 - Jan 1995
• Interpret customer demand and forecast information to create master schedule for printed circuit boards and server manufacturing.• Establish capacity and material constraints.• Verify MRP output.• Chair weekly & daily build plan meetings.• Produce current quarter +1 build schedules and load into MRP schedule.• New product introduction readiness.• Chair capacity planning meeting with relevant manufacturing and support functions.• Publish weekly performance report.• Supervise and assist 2 production planners. Show less
-
-
2nd Shift planner
-
Jan 1991 - Jan 1992
• Ensure seamless transitions between shifts. • Responsible for all materials & procurement related issues. • Supervise the stores and kitting areas including 8 materials handlers and receiving area in support of daily build schedule.• Chair & attend shift handover meetings.• Coordinate & supervise cycle counting of both raw and finished goods.• Control & coordinate purges, stop ships & stop builds.
-
-
-
Unisys
-
United States
-
IT Services and IT Consulting
-
700 & Above Employee
-
Purchasing expeditor
-
Jan 1989 - May 1991
• Schedule and plan logistics of all inbound electrical components from a worldwide vendor base in support of manufacturing requirements.• Liase with logistics partners ensuring both schedules and cost targets were met.• Report and chair quarterly performance review with logistics partners.• Establish material constraints.• Verify MRP output v’s actual supply• Assist buyers and provide holiday cover.
-
-
Technician
-
Jun 1984 - Jun 1989
Elctrical & Electronic debug of document processing equipment
-
-
Community
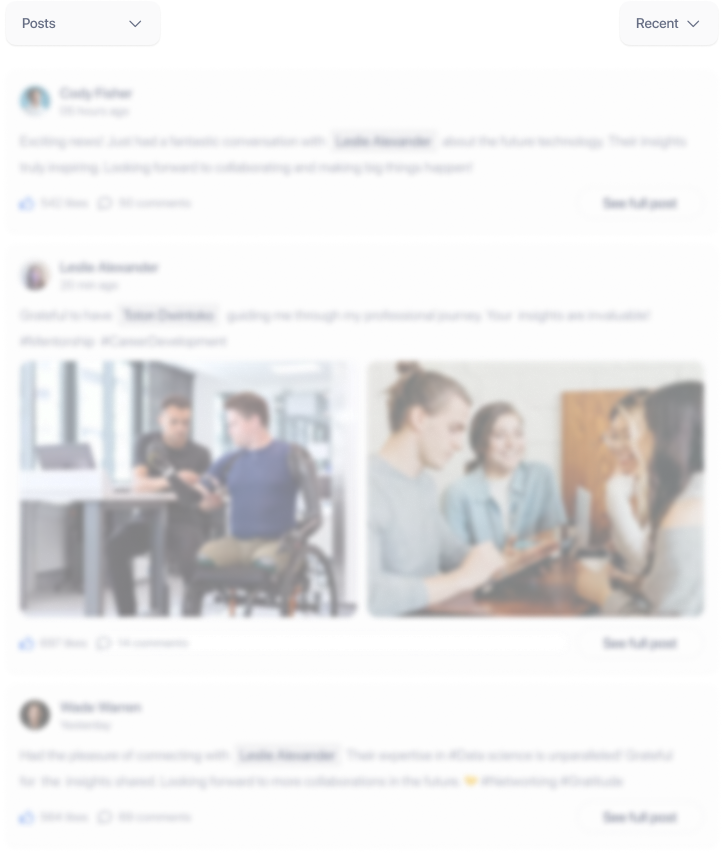