Todd Ballou
Director of Quality and Operational Excellence at MIC Group- Claim this Profile
Click to upgrade to our gold package
for the full feature experience.
Topline Score
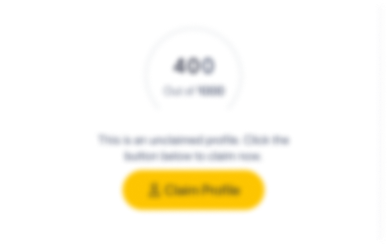
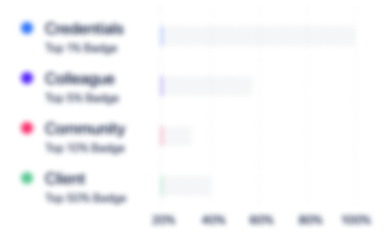
Bio

Luis Antillon
Simply said, an extraordinarily versatile leader. An executive possessing a solid and balanced background in manufacturing operations, continuous improvement process design and deployment, with a unique ability to work with people from all levels across the organization and who has exceptional communication skills. In summary, a rare commodity, that’s Todd. I met Todd several years ago, at Caterpillar, where he took on the challenge to train a group of people as Six Sigma Black Belts. In the course of 4 weeks, I witnessed how the group widely benefited not only from Todd’s extensive knowledge on Six Sigma, but most importantly, from Todd’s incredibly useful realistic examples gained from experience in running manufacturing operations with an engrained continuous improvement culture. Later, Todd joined our ranks in the Operational Excellence Central Office as Master Black Belt. In a short time, Todd became instrumental to the success of the program while engaging and contributing in key areas such as program strategy, content design, instructional processes, all while coaching and supporting business leaders working on complex projects. It has been impressive to see Todd create value in different companies hence industries, facing complex challenges, solving critical problems. Todd is someone that will always earn people’s trust by fully delivering on his commitments. As a leader or as a colleague, Todd has my highest recommendation.

Craig McGaughy
Every so often during your working career you run into an individual who has ‘it’. Todd is that person. His background is heavily influenced as a Continuous Improvement practitioner coupled with training that has taken him all the way to a Master Black Belt. While at CEMEX, I have had the luxury of working with Todd on several of my projects seeking his counsel on areas that I was not familiar with. His knowledge of concepts and practices is amazing and his way of delivering them in a fashion you would understand first pass is something we should all aspire to do. Working alongside and watching him win the hearts and minds of the employees through his coaching and advocacy is truly a joy and is something I try to emulate every day I am out in the field working on a project. Finally, having Todd here at CEMEX has raised our collective bar by bringing vast knowledge and experience to bear that we could not have achieved on our own.

Luis Antillon
Simply said, an extraordinarily versatile leader. An executive possessing a solid and balanced background in manufacturing operations, continuous improvement process design and deployment, with a unique ability to work with people from all levels across the organization and who has exceptional communication skills. In summary, a rare commodity, that’s Todd. I met Todd several years ago, at Caterpillar, where he took on the challenge to train a group of people as Six Sigma Black Belts. In the course of 4 weeks, I witnessed how the group widely benefited not only from Todd’s extensive knowledge on Six Sigma, but most importantly, from Todd’s incredibly useful realistic examples gained from experience in running manufacturing operations with an engrained continuous improvement culture. Later, Todd joined our ranks in the Operational Excellence Central Office as Master Black Belt. In a short time, Todd became instrumental to the success of the program while engaging and contributing in key areas such as program strategy, content design, instructional processes, all while coaching and supporting business leaders working on complex projects. It has been impressive to see Todd create value in different companies hence industries, facing complex challenges, solving critical problems. Todd is someone that will always earn people’s trust by fully delivering on his commitments. As a leader or as a colleague, Todd has my highest recommendation.

Craig McGaughy
Every so often during your working career you run into an individual who has ‘it’. Todd is that person. His background is heavily influenced as a Continuous Improvement practitioner coupled with training that has taken him all the way to a Master Black Belt. While at CEMEX, I have had the luxury of working with Todd on several of my projects seeking his counsel on areas that I was not familiar with. His knowledge of concepts and practices is amazing and his way of delivering them in a fashion you would understand first pass is something we should all aspire to do. Working alongside and watching him win the hearts and minds of the employees through his coaching and advocacy is truly a joy and is something I try to emulate every day I am out in the field working on a project. Finally, having Todd here at CEMEX has raised our collective bar by bringing vast knowledge and experience to bear that we could not have achieved on our own.

Luis Antillon
Simply said, an extraordinarily versatile leader. An executive possessing a solid and balanced background in manufacturing operations, continuous improvement process design and deployment, with a unique ability to work with people from all levels across the organization and who has exceptional communication skills. In summary, a rare commodity, that’s Todd. I met Todd several years ago, at Caterpillar, where he took on the challenge to train a group of people as Six Sigma Black Belts. In the course of 4 weeks, I witnessed how the group widely benefited not only from Todd’s extensive knowledge on Six Sigma, but most importantly, from Todd’s incredibly useful realistic examples gained from experience in running manufacturing operations with an engrained continuous improvement culture. Later, Todd joined our ranks in the Operational Excellence Central Office as Master Black Belt. In a short time, Todd became instrumental to the success of the program while engaging and contributing in key areas such as program strategy, content design, instructional processes, all while coaching and supporting business leaders working on complex projects. It has been impressive to see Todd create value in different companies hence industries, facing complex challenges, solving critical problems. Todd is someone that will always earn people’s trust by fully delivering on his commitments. As a leader or as a colleague, Todd has my highest recommendation.

Craig McGaughy
Every so often during your working career you run into an individual who has ‘it’. Todd is that person. His background is heavily influenced as a Continuous Improvement practitioner coupled with training that has taken him all the way to a Master Black Belt. While at CEMEX, I have had the luxury of working with Todd on several of my projects seeking his counsel on areas that I was not familiar with. His knowledge of concepts and practices is amazing and his way of delivering them in a fashion you would understand first pass is something we should all aspire to do. Working alongside and watching him win the hearts and minds of the employees through his coaching and advocacy is truly a joy and is something I try to emulate every day I am out in the field working on a project. Finally, having Todd here at CEMEX has raised our collective bar by bringing vast knowledge and experience to bear that we could not have achieved on our own.

Luis Antillon
Simply said, an extraordinarily versatile leader. An executive possessing a solid and balanced background in manufacturing operations, continuous improvement process design and deployment, with a unique ability to work with people from all levels across the organization and who has exceptional communication skills. In summary, a rare commodity, that’s Todd. I met Todd several years ago, at Caterpillar, where he took on the challenge to train a group of people as Six Sigma Black Belts. In the course of 4 weeks, I witnessed how the group widely benefited not only from Todd’s extensive knowledge on Six Sigma, but most importantly, from Todd’s incredibly useful realistic examples gained from experience in running manufacturing operations with an engrained continuous improvement culture. Later, Todd joined our ranks in the Operational Excellence Central Office as Master Black Belt. In a short time, Todd became instrumental to the success of the program while engaging and contributing in key areas such as program strategy, content design, instructional processes, all while coaching and supporting business leaders working on complex projects. It has been impressive to see Todd create value in different companies hence industries, facing complex challenges, solving critical problems. Todd is someone that will always earn people’s trust by fully delivering on his commitments. As a leader or as a colleague, Todd has my highest recommendation.

Craig McGaughy
Every so often during your working career you run into an individual who has ‘it’. Todd is that person. His background is heavily influenced as a Continuous Improvement practitioner coupled with training that has taken him all the way to a Master Black Belt. While at CEMEX, I have had the luxury of working with Todd on several of my projects seeking his counsel on areas that I was not familiar with. His knowledge of concepts and practices is amazing and his way of delivering them in a fashion you would understand first pass is something we should all aspire to do. Working alongside and watching him win the hearts and minds of the employees through his coaching and advocacy is truly a joy and is something I try to emulate every day I am out in the field working on a project. Finally, having Todd here at CEMEX has raised our collective bar by bringing vast knowledge and experience to bear that we could not have achieved on our own.

Credentials
-
Caterpillar 6 Sigma Black Belt
Caterpillar Inc.Aug, 2006- Oct, 2024
Experience
-
MIC Group
-
United States
-
Machinery Manufacturing
-
100 - 200 Employee
-
Director of Quality and Operational Excellence
-
May 2019 - Present
-
-
-
CEMEX
-
Mexico
-
Wholesale Building Materials
-
700 & Above Employee
-
Master Black Belt
-
May 2016 - Apr 2019
One of three CEMEX USA Master Black Belts (MBB) responsible for development and deployment of the country’s Operational Excellence Program. Personally accountable for CEMEX USA belting certification program, raising capability through delivering Green Belt and Black Belt training, and coaching Black Belts to achieve project success and financial benefits.▪ Implement technology-enabled processes to support training and certification program▪ Coach and Mentor Black Belts to achieve $64M target in 2018 project benefits.▪ Drive cultural change at CEMEX USA to embed Operational Excellence across all business lines
-
-
-
Caterpillar Inc.
-
United States
-
Machinery Manufacturing
-
700 & Above Employee
-
Master Black Belt
-
Dec 2014 - May 2016
Joined Corporate 6 Sigma and Caterpillar Production System Deployment group to develop and deliver both Black Belt (BB) and Master Black Belt (MBB) 6 Sigma and CPS training, and coach BBs to ensure project success. ▪ Caterpillar Corporate Process Owner for Root Cause Corrective Action methodology and training. ▪ Effectively deliver 6 Sigma and CPS training to Caterpillar, Suppliers, Dealers and Customers in 2015: 87 BBs and 20 MBBs.▪ Leading Strategy development and governance for CPS Division driving focus, alignment and governance to ensure achievement of aggressive business objectives. ▪ Redesigned and implemented simplified Corporate CPS Deployment website making available the training materials, templates, and CPS communications to Global Caterpillar 6 Sigma and CPS practitioners.▪ Strong contributor to key Executive Director-sponsored Division-wide efforts including Culture of Values and Innovation teams.
-
-
Strategy Manager
-
Mar 2009 - Dec 2014
Promoted to head strategy development, governance, and execution for $6B Component Division, which included oversight, tracking, planning, and support for 10 key projects, each with different sponsors and teams. Engaged to transition into specific segment of the division based on changing needs, currently acting as a facilitator for other major initiatives. Partner with high-level leaders, such as VPs and General Manager. ▪ Instrumental in division’s cost reduction methodology and initiative, providing guidance and training that helped generate ~$15M in cost savings for 2014. ▪ Proved vital to defining Vertical Integration Methodology, Low-Cost Producer (LCP) Approach, and Multi-Level Product Strategy; improved transparency in communicating with Executive Office and gaining R&D funding. ▪ Rolled out training seminars for topics that included Normal Plant Cost and Art of Deal Negotiation. ▪ Facilitate annual Divisional Strategy Sessions and Executive Office Reviews (EORs) for senior-level audience.
-
-
-
Caterpillar Inc.
-
United States
-
Machinery Manufacturing
-
700 & Above Employee
-
Value Stream Manager / 6 Sigma Champion
-
2006 - 2009
Provided oversight for $800M Bolted Cylinder business and key metrics for safety, quality, on-time delivery, and cost. Supervised team of ~90 management and unionized employees, including Master Black Belts, Black Belts, and Process Engineers. Ensured appropriate cylinder supply throughout Caterpillar based on demands. ▪ Led consolidation of two facilities while maintaining component shipping performance, meeting increasing demand of 50%+, and creating new rod welding process.▪ Headed deployment of Caterpillar Production System (CPS) and drove key changes to improve supply chain, supplier on-boarding, and team talent, which supported Caterpillar in reaching record sales of $51B for 2008.▪ Revamped 6 Sigma approach for delivery of key projects that tied to facility’s strategy, reducing average number of open days for key projects 25%.▪ Volunteered as mentor and have continued mentoring up to three employees concurrently since 2007.
-
-
-
-
Operations Manager / Value Stream Manager
-
2005 - 2006
Directed machining operations for wholly owned subsidiary manufacturing low and medium pressure hydraulic hose couplings. Supervised 125-person staff spanning 37 machines running 24/7. Held accountability for department safety, engagement, quality, delivery, and budget/cost targets. ▪ Boosted overall machine output 25% by maintaining top-talent team to meet quality and process partner needs. ▪ Initiated key changes that took operation from 8.51 Recordable Injury Frequency (RIF) in 2005 to world-class safety performance and 0 RIF by 2014; drove collaborative approach to action planning to shift safety culture.
-
-
-
Caterpillar Inc.
-
United States
-
Machinery Manufacturing
-
700 & Above Employee
-
Master Black Belt
-
2002 - 2005
Appointed to drive continuous improvement and deployment of 6 Sigma curriculum, leading team of Instructional Designers for creation, refinement, and delivery of training to Black Belts and Master Black Belts. ▪ Coordinated and delivered training to ~100 Master Black Belts as well as facilitated 6 Sigma Project Sponsor training at Peterson and Thompson Caterpillar dealers.▪ Created process management curriculum to address gap in process ownership and sustainability; also held key role in defining process ownership tool to track and transfer responsibility as employees progressed.
-
-
6 Sigma Black Belt
-
2001 - 2002
Engaged for and completed Caterpillar DMAIC Black Belt training program in its first wave of deployment, providing leadership for planning, change management, and execution of key projects. ▪ Appointed as project lead for CEO-sponsored Enterprise Strategic Improvement 6 Sigma Project (SIP) to define and implement Caterpillar’s current Continuous Product Improvement (CPI) process. o Drove eight-month project with upper-level, cross-functional managers, gaining approval from CEO for execution, forming project team, and creating project plan. o Facilitated Sponsor and Gate Reviews with Chairman/CEO and delivered presentations to Administrative Council comprised of Group Presidents and VPs. o Proved vital to successful completion that resulted in $150M cost reduction associated with resolving product problems while improving speed of resolution 50%+ within the first two years of deployment.
-
-
Sr. Manufacturing Engineer
-
2001 - 2002
Provided CNC programming for five-axis machining centers using Pro-E associativity to apply machining processes to engineering 3D models. Optimized programs to minimize cycle time, boost quality, and maximize too life. ▪ Cut machining program development time 95% from five days to two hours by retraining engineers on new approach to modifying features and engineering drawings.
-
-
-
Caterpillar Inc.
-
United States
-
Machinery Manufacturing
-
700 & Above Employee
-
Management Development Supervisor
-
1998 - 2000
Created and rolled out CareerQuest, a competency-based technical career development process and system for base of ~2,400 engineers; process adopted as corporate standard and still in use today. ▪ Gained buy-in from company’s Specialty Products Business Unit for adoption of CareerQuest into its ~500-person technical community and supported deployment. ▪ Built Engineering Career Progression Planning Tool that was customized for corporate-level use across HR, global purchasing, treasury, finance, accounting, legal/support services, and IT.
-
-
Technical Training Consultant
-
1997 - 1998
Determined and addressed training/development needs for engineering community at Caterpillar’s R&D facility. Coordinated development and delivery of technical courses that included Digital Signal Processing, Mine Safety, and Basic through Advanced Hydraulics.▪ Defined objectives and co-developed Electro-hydraulics curriculum with Milwaukee School of Engineering.▪ Increased use of resources by improving access via intranet and better communications.
-
-
-
EY
-
United Kingdom
-
IT Services and IT Consulting
-
700 & Above Employee
-
Senior Consultant
-
1994 - 1997
Created and delivered in-house and client training programs in support of firm’s key consulting engagement methodologies, including Business Process Re-engineering, Knowledge Management, and Activity-Based Costing. Created and delivered in-house and client training programs in support of firm’s key consulting engagement methodologies, including Business Process Re-engineering, Knowledge Management, and Activity-Based Costing.
-
-
-
PAL Health Technologies
-
United States
-
Medical Device
-
1 - 100 Employee
-
Design Engineer
-
1991 - 1992
Designed and developed new and improved custom, prescription orthodics utilizing thermoplastic materials and engineered plastics. Developed the capability for physical material testing. Designed and developed new and improved custom, prescription orthodics utilizing thermoplastic materials and engineered plastics. Developed the capability for physical material testing.
-
-
Education
-
Illinois State University
Master's degree, Industrial Technical Training -
Illinois State University
Bachelor of Applied Science (BASc), Industrial Technology/Technician
Community
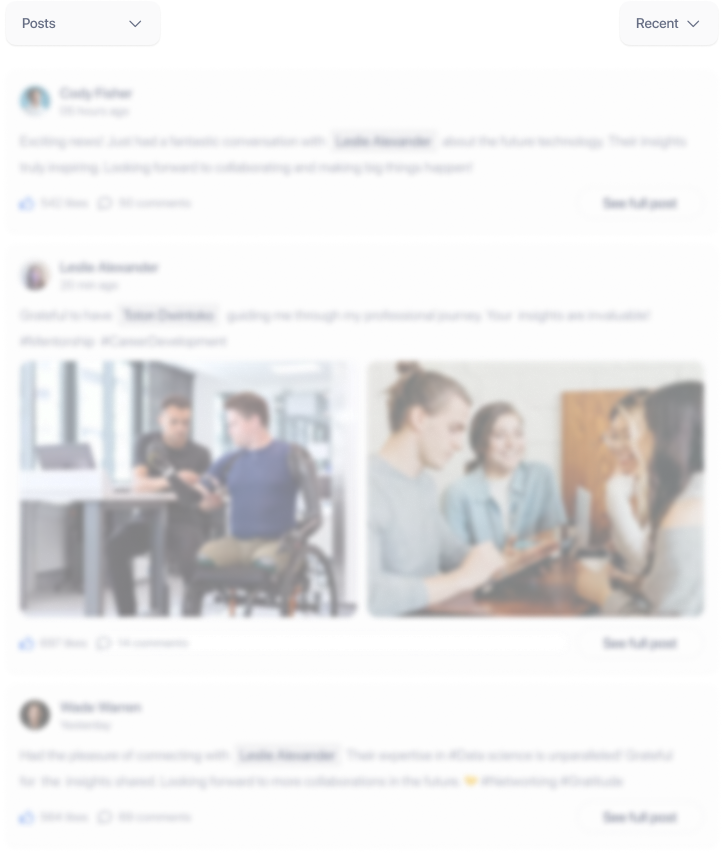