Todd Baum
Plant Manager Plant 3 at Genesis Products- Claim this Profile
Click to upgrade to our gold package
for the full feature experience.
Topline Score
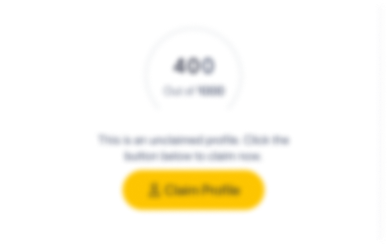
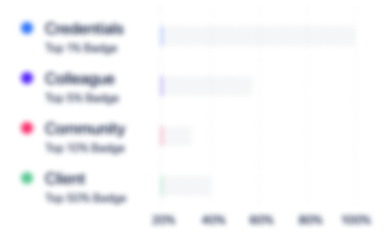
Bio


Credentials
-
Microsoft Excel- Advanced
Pryor Learning | Fred Pryor Seminars | CareerTrackJan, 2020- Nov, 2024 -
Pro Ex 1 Extrusion- Gold Level Achievement
Paulson Plastics AcademyFeb, 2019- Nov, 2024
Experience
-
Genesis Products
-
United States
-
Wholesale Building Materials
-
200 - 300 Employee
-
Plant Manager Plant 3
-
Sep 2022 - Present
-
-
Production Supervisor
-
Aug 2020 - Sep 2022
-
-
-
Pregis
-
United States
-
Packaging and Containers Manufacturing
-
700 & Above Employee
-
Production Supervisor
-
Feb 2019 - Jun 2020
Reduction in Recordable injuries and first aids yearly by holding weekly Safety meetings, discussing company safety events and by having employees turn in weekly safety observations that identify risks and hazards at their work center or throughout the plant. Continual reduction in customer complaints from implementing a Layered Process Audit (LPA) procedure where Shift Leads, Quality, and Supervisor performed end of line audits. Scrap reduction from 29% to 13% on major work center from collecting data and analyzing biggest losses then diving into the causes and assigning action items to Shift leads to resolve the issues. Delivered 95%+ on OTIF through hands-on and working with Shift leads to dictate and execute orders to meet Customer demands.
-
-
-
KIK Consumer Products
-
United States
-
Manufacturing
-
700 & Above Employee
-
Production Supervisor
-
Jul 2013 - Feb 2019
-Through a team effort we demonstrated a safe work environment keeping record-able injuries down. -Worked abreast with logistics, Supply Chain, Maintenance, and Quality to ensure on-time delivery of products. -Developed and implemented SOP's and visual Work Instructions. - Analyzed processes and implemented changes to increase production to 75% for all high speed production lines. -Created Shadow boards at all machines to reduce unscheduled downtime by having tools in place and training Machine Operators to resolve minor issues. -Supported leadership in review, approval, and tracking of corrective actions. -Delivered performance evaluations, scheduled vacation, and coordinated new hire training.
-
-
-
Lippert Components
-
Goshen, Indiana, United States
-
Quality Engineer
-
Apr 2011 - Jun 2013
-Worked with Quality and R & D teams on new projects and set up of the new production lines. - Responsible for some incoming inspections and developing quality checks during the manufacturing process. -Developed hourly check sheets for live time production and data collection spreadsheets to track production parts to ensure that specifications were being met. -Developed checks sheets for both incoming assembled parts and raw materials to ensure that our suppliers were being held to our quality standards. -Work Instructions and visual standards were also made to ensure that these checks were performed correctly. -Responsible for the training of the line inspectors.
-
-
-
Toefco Engineered Coatings
-
Niles, Michigan, United States
-
Plant Manager
-
Jan 2002 - Jul 2010
-Created new process flows, controlling processes better thru work instructions and better organization throughout the Plant. -Reduced turnaround time from a targeted 7-10 days to 3-7 days at all Job shop work centers. -Reduced our Return Material Authorizations (RMA} from an average of 3% to 1%. These two measurables in turn saved the company money and increased profits. -Throughout the Plant I created Work Instructions and Visual Standards for machinery and for jobs that were being processed. These Work Instructions were posted at the machines and production lines for reference. -Shadow boards were designed for cleaning supplies, a daily checklist for cleaning duties were posted and were to be signed off by their respective team leader. -Organized and 5S was implemented throughout the entire Plant. -Project Lead on John Deere JD-223 audit and the Special Paint process audit. With these being passed we were awarded there Approved Supplier Certificate. Passing both of these audits took a lot of hard work and dedication from myself, the Quality Manager and the rest of the team. This was done by working hand in hand with John Deere engineers on a weekly basis.
-
-
-
-
Group Leader Shipping & Receiving
-
May 1998 - Jan 2002
-
-
3rd Shift Supervisor of Operations
-
Mar 1994 - May 1998
-
-
Production Team Leader Sub-Assembly Lines
-
Mar 1993 - Feb 1994
-
-
Education
-
Richland Community College
Community
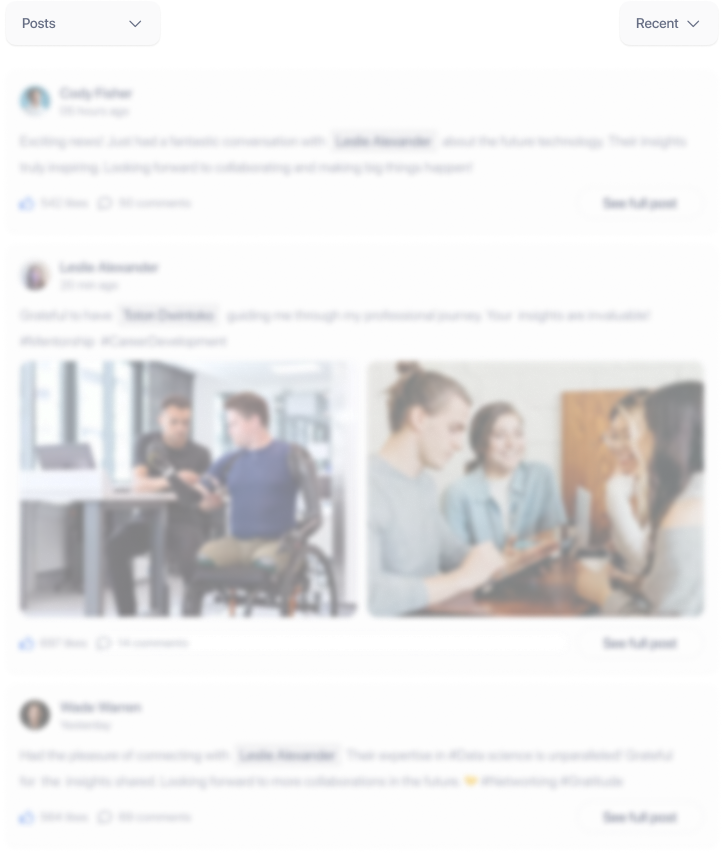