Tina NGUYEN
Production Operator at HBC Trading Australia P/L- Claim this Profile
Click to upgrade to our gold package
for the full feature experience.
Topline Score
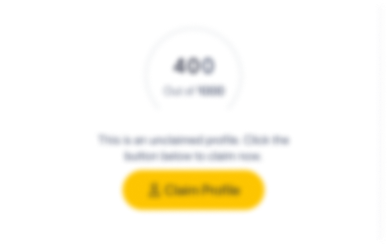
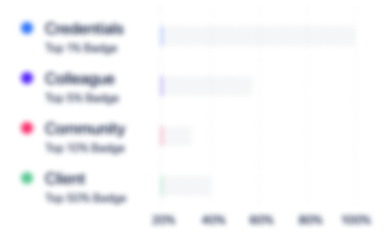
Bio


Credentials
-
Global Quality Audit Certificate of Sanofi
Sanofi
Experience
-
HBC Trading Australia P/L
-
Australia
-
Food and Beverage Services
-
1 - 100 Employee
-
Production Operator
-
Apr 2017 - Present
-
-
Production Operator
-
Apr 2017 - Present
-
-
-
Sanofi
-
France
-
Pharmaceutical Manufacturing
-
700 & Above Employee
-
Quality Assurance Officer
-
Apr 2012 - Sep 2014
• Managing Computerized system: - Compiling validation protocol for new equipment with computerized system, validating, assessing and reporting the validation results, following up proposals stemmed from validation outcomes. - Working with Technical Department to set up access rights and parameters as approved. - Planning and performing Back-up data of equipment with computerized system. • Managing quality of suppliers/ third parties: - Auditing sites of material manufactures and suppliers. - Identifying materials with mono-source status, assessing the related risk and working with Purchasing Department to propose the back-up solution. - Identifying and updating the basic audit frequency for each manufacturer/ supplier. - Evaluating and updating the yearly audit frequency. - Making plan of auditing manufacturers of APIs, excipients, primary packaging materials and warehouses of traders. Ensuring audit performed as planned. - Managing Quality Third Party (QTP) program of company - Collecting, analyzing information regarding quality and safety of materials (QSMP). - Compiling and monitoring quality agreements between Sanofi and Third parties. • Monitoring operations of Production and Warehouse. • Managing change control system: - Training new users - Updating data into system - Monitoring, processing changes and informing the relevant Departments about changes. • Managing complaint system: Working with other Departments to solve customer complaints and work with suppliers to follow up complaints of Sanofi about materials. • Working with other Departments to assure the current internal procedures of Thu Duc site in compliance with requirements of Sanofi directives, and to update as needed.
-
-
-
-
GMP Team Leader
-
Mar 2011 - Mar 2012
Key Responsibilities: • Developing and following up: - suppliers’ profiles, Change Control • Take part in investigation of Deviation cases; Complaint from Customers, then keeping track and completing these cases • Developing Standard Operating Procedures (SOPs) • Training staffs in SOPs • Checking change of packing compared to Drug Registration Dossiers,… and the others related to packing products Key achievements: • Trained site staff in SOPs • Completed all tasks assigned in good quality and before targeted dates • Positive feedback from both managers and colleagues
-
-
-
-
Production Supervisor
-
Sep 2006 - Sep 2008
Key Responsibilities: • Organized production schedules • Assigned tasks to workers in order to accomplish optimal productivity • Supervised production and cleaning processes • Developed Standard Operation Procedures in production (SOPs) • Trained and retrained workers according to SOPs • Worked directly with warehouse manager and other Departments in order to assure production as plan. • Reported on productivity and production status. Key achievements: • Achieved the high productivity of production batch (over 95%) • Solved conflicts between two workers and helped them to cooperate to work efficiently • Completed all tasks assigned in good quality and before targeted dates • Positive feedback from both managers and colleagues
-
-
Education
-
Curtin University
Master's degree, Project Management -
Western Sydney University
Master of Business Administration (MBA), Business and Commerce -
University of Medicine and Pharmacy, Ho Chi Minh City
Bachelor of Pharmacy (BPharm), Pharmacy
Community
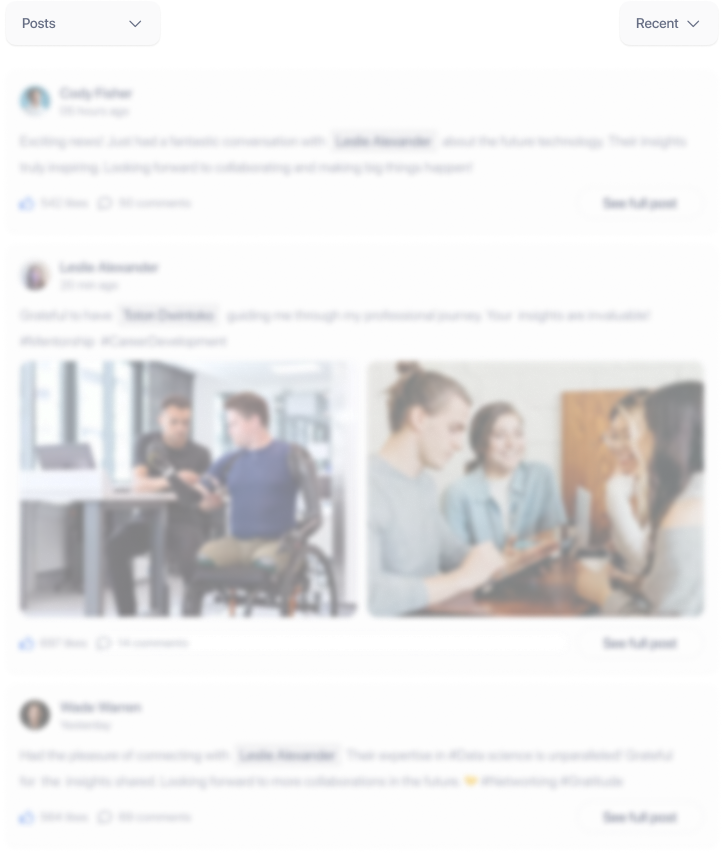